CAM, which stands for Computer-Aided Manufacturing, is a special kind of software that helps bridge the gap between design and the actual production of physical objects. It works hand in hand with CNC machines, which are automated tools capable of carving, cutting, and shaping various materials with exceptional accuracy.
CAM software serves as the brains behind CNC machines. It takes the digital design of a part or object, created using CAD (Computer-Aided Design) software, and converts it into a set of instructions that the CNC machine can understand and execute. These instructions guide the machine’s movements, tool paths, and other parameters necessary to transform a raw material into a finished product.
The primary role of CAM software is to optimize the machining process. It determines the most efficient tool paths, minimizes waste material, calculates precise cutting speeds and feeds, and considers factors like tool changes and tool wear. By automating these complex calculations and generating precise instructions, CAM software enables CNC machines to produce parts with exceptional accuracy, consistency, and speed.
4 Must-Know CAM Software for CNC Machining
Now that we grasp the significance of CAM software in CNC machining, it’s time to delve into the world of four essential CAM software programs that every aspiring CNC machinist should know about. These software solutions offer a wide range of features and capabilities that can greatly enhance the CNC machining process.
#4 EnRoute
EnRoute is a specialized CAM software solution designed specifically for CNC routing and engraving applications. It offers a range of unique features that make it a go-to choice for sign makers, woodworking professionals, and CNC routing enthusiasts.
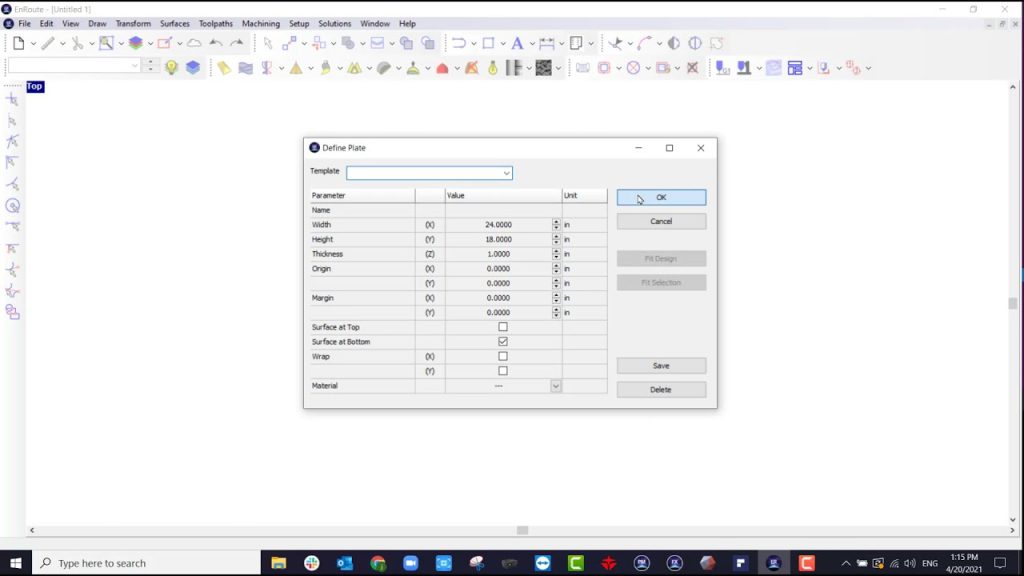
One standout feature of EnRoute is its advanced 3D surface mapping capabilities. This allows users to precisely map intricate designs onto complex three-dimensional surfaces, opening up a world of creative possibilities. Whether it’s engraving intricate patterns on curved surfaces or creating detailed textures on sculpted objects, EnRoute’s 3D surface mapping feature ensures stunning results.
Nesting optimization is another key feature of EnRoute. It enables users to maximize material usage and minimize waste by efficiently arranging multiple parts on a single sheet of material. This feature is particularly beneficial for sign makers and woodworking professionals who often work with expensive materials and strive for optimal material utilization.
Recommended Read: The 5-Step Guide to Mastering CAM in CNC Machining
EnRoute also offers parametric texture toolpaths, which allow users to generate intricate and visually appealing textures with ease. By adjusting parameters such as density, randomness, and depth, users can create unique surface finishes that add depth and character to their CNC-routed projects. This feature is especially useful for achieving decorative effects on woodworking projects and sign-making applications.
#3 SOLIDWORKS
When it comes to CAD/CAM software solutions, SOLIDWORKS stands out as one of the most popular and widely used choices among engineers and designers. Not only does SOLIDWORKS offer robust CAD capabilities, but it also provides powerful CAM features that streamline the CNC machining process.
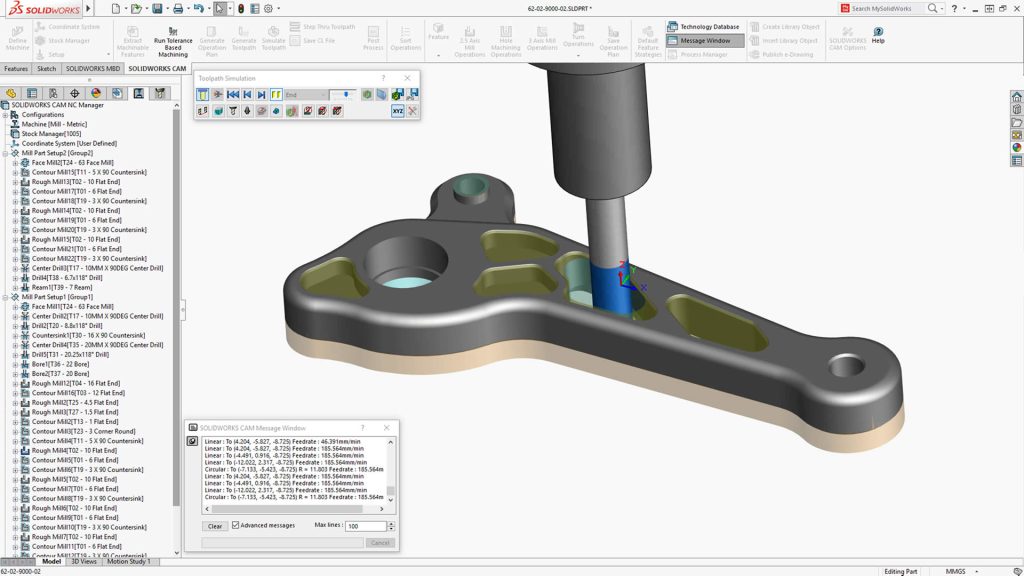
SOLIDWORKS CAM offers a range of functionalities that enhance efficiency and productivity in CNC machining. One notable feature is automatic feature recognition, which automatically identifies geometric features, such as holes, pockets, and slots, in the CAD model. This saves valuable time by eliminating the need for manual feature identification, allowing users to quickly generate toolpaths.
Toolpath optimization is another key feature of SOLIDWORKS CAM. It analyzes the part geometry, cutting conditions, and tooling parameters to generate the most efficient toolpaths. This optimization process ensures optimal cutting speeds, feeds, and tool movements, resulting in reduced machining time and improved surface finish.
SOLIDWORKS CAM also provides multi-axis machining capabilities, allowing users to create toolpaths for complex parts that require simultaneous movement in multiple axes. This feature is particularly beneficial for machining intricate and sculpted surfaces, enabling users to achieve high-quality results with ease.
One of the significant advantages of SOLIDWORKS is its seamless integration with other SOLIDWORKS modules, such as SOLIDWORKS CAD. This integration enables a smooth transition from design to manufacturing by eliminating the need for file conversions and ensuring data consistency throughout the entire workflow. Changes made to the design are automatically updated in the CAM environment, reducing errors and streamlining the manufacturing process.
SOLIDWORKS has been instrumental in numerous CNC machining success stories across various industries. For example, in the aerospace industry, SOLIDWORKS CAM has been utilized to manufacture intricate components with tight tolerances, resulting in improved efficiency and reduced costs. In the automotive industry, SOLIDWORKS CAM has enabled the production of complex molds and dies with exceptional precision and accuracy.
These case studies and success stories highlight the reliability and effectiveness of SOLIDWORKS as a CAD/CAM software solution for CNC machining applications. Its comprehensive feature set, integration capabilities, and proven track record make it a trusted choice for engineers and manufacturers worldwide.
#2 FreeCAD
FreeCAD is an open-source parametric 3D modeling software that also offers CAM capabilities, making it a versatile tool for CNC machining.
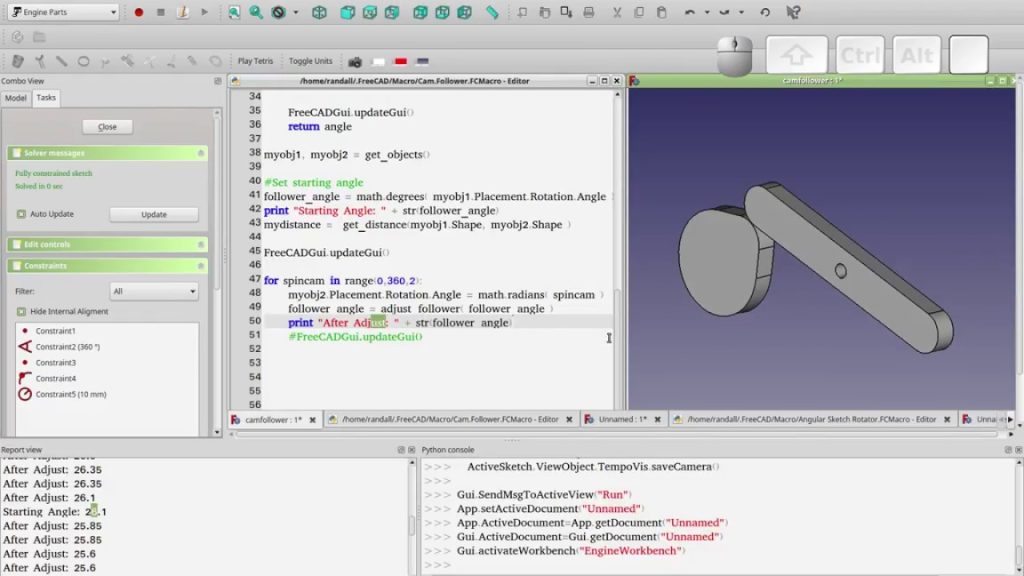
One of the key advantages of FreeCAD is its extensive set of features and capabilities. It provides a comprehensive range of tools for creating and modifying 3D models, allowing users to design intricate parts and assemblies. When it comes to CAM functionality, FreeCAD offers features such as toolpath generation, simulation, and post-processing, enabling users to generate G-code for CNC machines.
FreeCAD is designed to support a wide range of file formats, ensuring compatibility and ease of integration with other software and machining equipment. It can import and export common file formats such as STEP, IGES, STL, and DXF, allowing users to work with existing designs and collaborate with others seamlessly. This flexibility makes FreeCAD a versatile solution for CNC machining, accommodating different design requirements and workflows.
One notable aspect of FreeCAD is its user-friendly interface, which caters to users of all skill levels. Beginners can quickly grasp the basics of 3D modeling and CAM operations through intuitive tools and a straightforward workflow. Experienced users, on the other hand, can take advantage of advanced features and customization options to enhance their productivity and achieve more complex machining tasks.
However, it is important to note that FreeCAD may have some limitations compared to more advanced and commercially available CAM software options. While it offers a solid set of features, it may not have the same level of advanced functionalities and optimization capabilities as some commercial software. Users might experience limitations in terms of specialized toolpath strategies, advanced simulation features, or automated machining processes. Additionally, support and documentation for FreeCAD may not be as extensive as with commercial software, which could affect the availability of resources for troubleshooting and learning.
Nonetheless, for those seeking a cost-effective solution for CNC machining, FreeCAD provides a valuable option. Its extensive feature set, support for various file formats, and user-friendly interface make it accessible to users of different skill levels. While it may have some trade-offs compared to more advanced CAM software, FreeCAD remains a capable tool for creating toolpaths and generating G-code for CNC machines.
#1 Fusion 360
Developed by Autodesk, Fusion 360 offers a wide range of features and functionalities that cater to the needs of designers, engineers, and manufacturers.
One of the key strengths of Fusion 360 is its versatility in both 2D and 3D modeling. Users can create intricate designs using parametric modeling techniques, enabling them to modify and iterate their designs with ease. Whether it’s designing complex parts or assembling multiple components, Fusion 360 provides robust tools to bring ideas to life.

When it comes to CAM functionality, Fusion 360 excels in its toolpath generation capabilities. It offers a variety of toolpath strategies, allowing users to optimize machining operations for different scenarios. With Fusion 360, users can simulate and visualize toolpaths, ensuring that their machining processes are efficient and error-free. The software also includes simulation features to detect potential collisions and ensure safe operations.
Another innovative aspect of Fusion 360 is its cloud-based collaboration and data management capabilities. Users can easily share their designs, collaborate with team members, and access their projects from anywhere with an internet connection. This cloud-based approach ensures that everyone involved in the manufacturing process can stay up to date with the latest design changes and collaborate effectively.
Additionally, Fusion 360 offers a wide range of add-ons and extensions, allowing users to customize their workflows and access specialized tools. These extensions cover various aspects, such as generative design, simulation, and advanced machining strategies, further enhancing the capabilities of Fusion 360.
Other Articles You Might Enjoy
- Top 8 Features to Look for in CAM Software for CNC Machining
In today's fast-paced manufacturing industry, Computer-Aided Manufacturing (CAM) acts as a bridge between design and production, enabling manufacturers to translate their digital designs into precise and efficient machine instructions. One…
- Precision CNC Machining of Steel: High-Volume Production
Precision CNC Machining and High-Volume Production As an integral part of modern manufacturing processes, Precision Computer Numerical Control (CNC) machining brings about unmatched accuracy and consistency in the production of…
- Revolutionizing CNC Machining for the Future of Smart Wearables
Introduction: CNC Machining and Smart Wearables CNC (Computer Numerical Control) machining is a manufacturing process that utilizes computerized controls to operate and manipulate machine tools, converting raw materials into finished…