In the world of CNC machines, two popular contenders stand out: CNC routers and CNC mills. These advanced tools have revolutionized the manufacturing industry, enabling precise and automated production processes. However, despite their similarities in functionality, it is crucial to grasp the distinctions between these two machines. By understanding their unique characteristics, businesses and individuals can make informed decisions when selecting the online CNC machining services.
What is CNC Routers
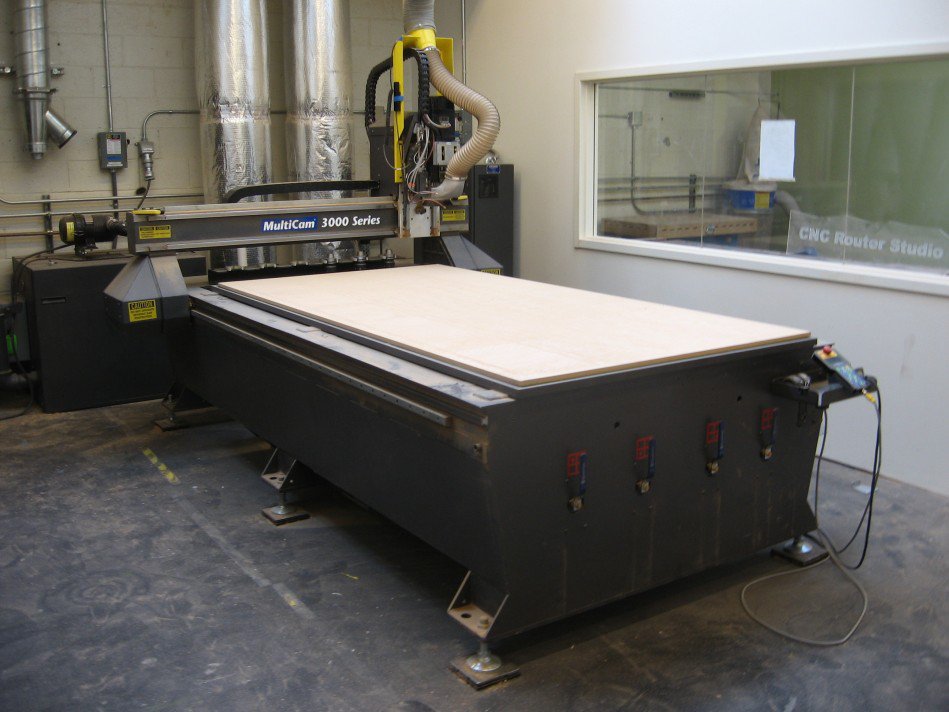
CNC routers are versatile machines designed for cutting, shaping, and hollowing out various materials, including wood, plastic, and metal. They employ computer-controlled movements to precisely execute intricate designs and patterns. With their high precision and efficiency, CNC routers have become indispensable in industries such as woodworking, sign-making, and prototyping.
What is CNC Mills
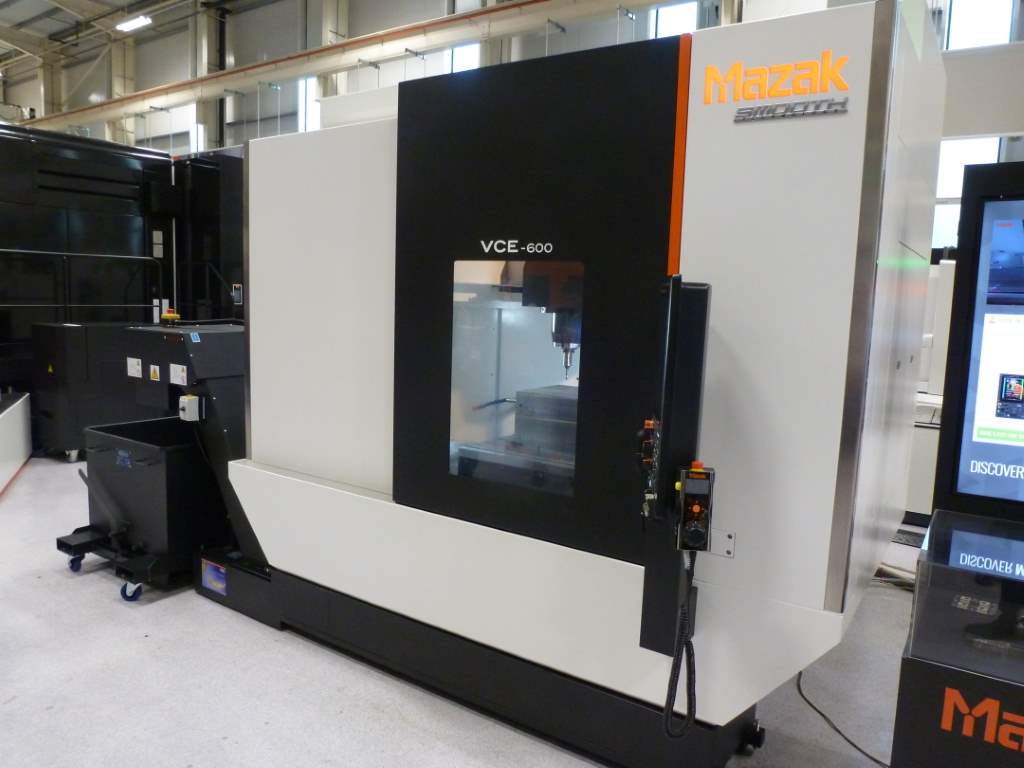
On the other hand, CNC mills are specifically engineered for precision machining operations, such as drilling, milling, and cutting. These machines excel in fabricating complex three-dimensional shapes and parts with exceptional accuracy. CNC mills are widely used in industries such as aerospace, automotive, and medical manufacturing, where intricate components demand utmost precision and repeatability.
The Main Differences
While CNC routers and CNC mills share certain functionalities, discerning their differences is of paramount importance. Each machine has its unique strengths, limitations, and applications. By gaining a comprehensive understanding of their distinctions, manufacturers, hobbyists, and entrepreneurs can make well-informed decisions about which machine aligns best with their production goals, budgetary constraints, and material requirements.
#1 Tooling & Cutting Mechanism
CNC routers employ a diverse range of cutting tools to accommodate various materials and cutting applications. These tools typically include end mills, ball nose cutters, V-groove bits, and router bits with different profiles. The selection of the tool depends on factors such as the desired cutting depth, material hardness, and desired finish. CNC routers are good at producing intricate designs and smooth contours due to the versatility of their cutting tools.
CNC mills primarily utilize end mills, which feature a cutting edge on the cylindrical end and sometimes on the sides. End mills are available in various sizes, flute configurations, and materials, allowing for precise machining operations. Additionally, specialized tooling like drills, taps, and reamers can be used in CNC mills for specific tasks such as hole-making and threading. CNC mills are widely used for high-precision machining because they are capable of achieving tight tolerances and exceptional surface finishes.
#2 Material Compatibility
CNC routers are commonly used for working with softer materials such as wood, plastics, foam, and composites. These machines are well-suited for applications like cabinetry, signage, and artistic creations. CNC routers offer versatility and excellent cutting performance when it comes to these materials, delivering intricate details and smooth finishes.
In contrast, CNC mills are designed to handle a broader range of materials, including metals like aluminum, steel, and titanium, as well as harder materials like ceramics and certain composites. Their robust construction and higher cutting forces enable CNC mills to tackle tougher materials and achieve precise results in demanding industries such as aerospace and automotive manufacturing.
#3 Rigidity
Rigidity refers to the machine’s ability to maintain stability and resist deflection during cutting operations. In the case of CNC mills, rigidity is a critical characteristic due to the high cutting forces involved in machining harder materials. CNC mills are built with heavy-duty structures, rigid frames, and robust components to withstand these forces and maintain stability. The focus on rigidity in CNC mills ensures consistent and accurate machining, even under demanding conditions.
On the other hand, CNC routers prioritize versatility and adaptability over rigidity. Since routers often work with softer materials like wood and plastic, they typically feature lighter frames and structures. While this lighter construction may lead to slightly more flexibility, it allows CNC routers to be more agile and versatile in their applications. The emphasis on versatility and maneuverability in CNC routers suits the requirements of industries that focus on intricate designs and creative applications.
Rigidity plays a crucial role in the accuracy and tolerances achieved by CNC mills and CNC routers. In CNC mills, the high rigidity ensures minimal vibrations and deflection during cutting, resulting in precise and repeatable machining. This attribute allows for tighter tolerances and the ability to achieve complex geometries with exceptional accuracy. The rigidity of CNC mills contributes to maintaining consistent performance over extended periods, ensuring the reliability of the machined components.
While CNC routers may have relatively less rigidity compared to CNC mills, it is important to note that their applications often do not require the same level of precision as machining harder materials. The impact of rigidity on accuracy and tolerances in CNC routers is more pronounced when working with softer materials. The inherent flexibility of CNC routers may result in slight variations in cuts and contours. However, this flexibility can also contribute to the artistic freedom and versatility of CNC routers in creative and design-focused industries.
#4 Speed & Spindle Power
CNC routers are known for their higher spindle speeds compared to CNC mills. The higher spindle speeds in routers allow for faster material removal rates. This increased cutting speed enables CNC routers to efficiently work on softer materials, where high-speed cutting can be advantageous. The faster material removal rates of CNC routers make them suitable for applications such as rapid prototyping, sign making, and general woodworking. The ability to work at higher speeds contributes to the overall productivity and time efficiency of CNC routers.
In contrast, CNC mills generally operate at lower spindle speeds but compensate for this with more powerful spindles. The lower speeds in mills are necessary to handle the demands of machining harder materials like metals and composites. These materials often require slower cutting speeds to maintain optimal cutting conditions and avoid excessive heat generation or tool wear. The more powerful spindles in CNC mills provide the necessary torque and cutting force to efficiently remove material from tougher workpieces. This combination of lower spindle speeds and increased power enables CNC mills to achieve precise cuts and high-quality finishes on challenging materials.
#5 Workpiece Size
CNC routers offer distinct advantages when it comes to processing large workpieces and sheet materials. The open design and larger work area of CNC routers allow for the handling of sizable workpieces with ease. Whether it’s cutting large wooden panels, machining oversized signs, or carving intricate designs on large sheets of plastic or foam, CNC routers excel in accommodating substantial workpiece sizes. The ability to process large workpieces in a single setup increases efficiency and reduces the need for additional manual intervention or repositioning.
Furthermore, CNC routers are particularly suitable for working with sheet materials. The flat table surface of a router provides excellent support for thin sheets, ensuring accurate and consistent cutting throughout the material. This makes CNC routers ideal for industries such as cabinetry, furniture manufacturing, and architectural millwork, where large sheet materials are commonly used.
Other Articles You Might Enjoy
- Differences Between CNC Lathes and CNC Mills
In the world of manufacturing, two machines play pivotal roles: CNC lathes and CNC mills. These machines share the purpose of material removal using cutting tools, yet they possess unique…
- Understanding CNC Routers: Top Question Asked
Imagine a single machine capable of transforming raw materials into intricate designs with unparalleled precision. It's like having a skilled craftsman with a technological edge, working tirelessly to bring your…
- 10 Key Features of CNC Mills You Should Know
The significance of CNC mills in the modern manufacturing industry cannot be overstated. These cutting-edge machines are instrumental in the precise shaping and cutting of materials, ensuring impeccable accuracy. By…