What Are the Key Components of Chinese CNC Machining for Belt Pulleys
Chinese CNC machining for belt pulleys integrates a myriad of key components, from advanced machinery and cutting-edge technology to skilled craftsmanship and stringent quality control. The synergy of these elements ensures the production of high-durability belt pulleys that stand up to rigorous industrial use.
China Online CNC Machining Service
Advanced Machinery
The foundation of superior belt pulley production lies in the utilization of sophisticated CNC machinery. These machines, equipped with high-precision spindles, multi-axis rotation, and adaptive control systems, facilitate intricate machining processes with exceptional accuracy.
Cutting-Edge Technology
CNC technology in China has seen rapid advancements, incorporating AI and IoT for smarter production lines. This integration enhances precision in machining operations, resulting in belt pulleys with optimal performance characteristics.
Skilled Craftsmanship
Despite the heavy reliance on machinery, the human element remains crucial. Experienced machinists oversee the CNC operations, bringing invaluable expertise and problem-solving skills to the production process.
Stringent Quality Control
Quality control is paramount in CNC machining. Rigorous testing and inspection protocols are in place to ensure that each belt pulley meets strict standards for durability and performance.
How Critical Are Material Choices in Ensuring the Longevity of CNC-Machined Belt Pulleys?
The selection of materials is a pivotal factor in the lifespan of CNC-machined belt pulleys. The right material can significantly enhance durability, resist wear and tear, and withstand environmental stresses, thereby extending the operational life of the pulleys.
Material Properties
Understanding the properties of various materials is essential for selecting the most suitable one for belt pulley manufacturing. Factors such as tensile strength, hardness, and corrosion resistance play critical roles in material selection.
Data Table: Material Mastery
Material Type | Tensile Strength (MPa) | Durability Rating | Corrosion Resistance | Hardness (HB) | Elastic Modulus (GPa) | Thermal Conductivity (W/mK) | Application Suitability |
---|---|---|---|---|---|---|---|
Aluminum Alloy | 310 – 483 | High | Moderate | 95 – 150 | 70 | 150 – 210 | Light-duty applications |
Stainless Steel | 505 – 860 | Very High | High | 150 – 250 | 200 | 15 – 30 | Heavy-duty environments |
Brass | 345 – 550 | Moderate | Good | 80 – 150 | 110 | 120 | Decorative purposes |
Titanium | 900 – 1,200 | Exceptional | Excellent | 215 – 340 | 105 | 6.7 | Aerospace and high-performance |
Composite Materials | Variable | High to Very High | Variable | Variable | Variable | Variable | Specialized applications |
Cast Iron | 200 – 350 | Moderate | Poor | 120 – 230 | 100 – 170 | 80 | General industrial use |
Tool Steel | 600 – 850 | High | Moderate | 200 – 650 | 190 – 210 | 25 – 30 | High-wear applications |
Polymer Composites | Variable | High | Excellent | Variable | Variable | Variable | Lightweight or insulative applications |
This table provides a more comprehensive overview of the materials available for CNC machining of belt pulleys, highlighting their varied properties and suitability for different applications.
What Role Does Precision in CNC Programming Play in the Lifespan of Belt Pulleys?
The precision of CNC programming is paramount in determining the performance and durability of belt pulleys. Accurate programming ensures that machining processes adhere closely to design specifications, minimizing material waste and enhancing the functional integrity of the pulleys.
Tight Tolerances and Surface Finish
Achieving tight tolerances and superior surface finishes are direct outcomes of precise CNC programming. These factors are critical for the pulley’s fit in assemblies and its interaction with belts, impacting wear rates and operational lifespan.
Graphical Representation: The Precision-Durability Correlation
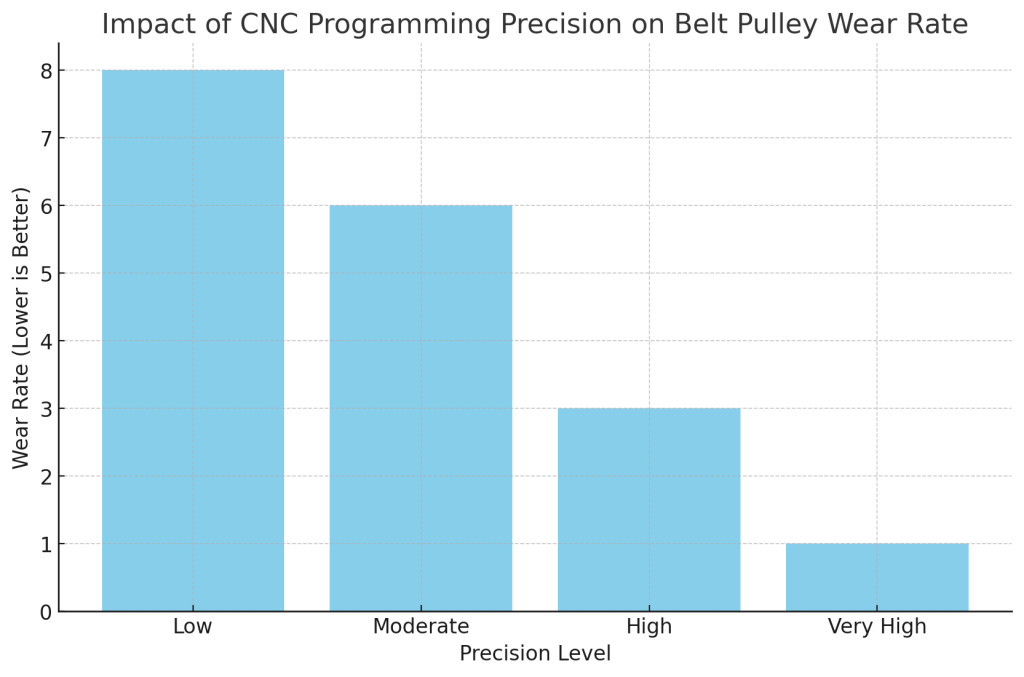
The graph above illustrates the impact of CNC programming precision on the wear rate of belt pulleys. As shown, higher precision levels in CNC programming correspond to lower wear rates, indicating that pulleys machined with greater precision tend to have longer lifespans due to reduced wear. This visual representation underscores the critical role that precision in CNC programming plays in enhancing the durability of belt pulleys.
How Does Surface Treatment Affect the Durability of CNC-Machined Belt Pulleys?
Surface treatments can significantly improve the durability and performance of CNC-machined belt pulleys. These treatments are designed to enhance surface properties, such as hardness and resistance to environmental factors, thereby extending the lifespan of the pulleys.
Variety of Surface Treatments
There is a wide range of surface treatment options available, each with specific benefits for belt pulley applications. These include anodizing, hard chrome plating, black oxide, and nitriding, among others.
Data Table: Surface Treatment
Surface Treatment | Corrosion Resistance | Wear Reduction | Application | Coating Thickness (μm) | Hardness (HV) | Friction Coefficient | Heat Resistance (°C) |
---|---|---|---|---|---|---|---|
Anodizing | High | Moderate | Aluminum Pulleys | 5 – 25 | 300 – 500 | 0.3 | Up to 800 |
Hard Chrome Plating | Very High | High | Industrial Pulleys | 20 – 30 | 800 – 1000 | 0.5 | Up to 700 |
Black Oxide | Moderate | Moderate | Aesthetic and Low-friction | 1 – 2 | 200 – 250 | 0.1 | Up to 200 |
Nitriding | High | Very High | High-performance Pulleys | 5 – 15 | 1000 – 1200 | 0.6 | Up to 500 |
Electroless Nickel | High | High | Corrosion-prone Environments | 5 – 50 | 500 – 700 | 0.4 | Up to 350 |
Thermal Spraying | Moderate | High | Extreme Temperature Conditions | 40 – 200 | 300 – 400 | 0.55 | Up to 1000 |
Zinc Plating | Good | Moderate | General Purpose | 5 – 25 | 100 – 200 | 0.5 | Up to 120 |
PVD Coating | High | Very High | Precision Engineering | 1 – 3 | 2000 – 3000 | 0.65 | Up to 600 |
This table offers a deeper insight into the effectiveness of various surface treatments, providing key parameters such as coating thickness, hardness, friction coefficient, and heat resistance, which are critical in selecting the optimal treatment for belt pulleys.
Can Innovative Cooling Techniques During CNC Machining Extend Belt Pulley Life?
Innovative cooling techniques during CNC machining, such as cryogenic cooling and high-pressure coolant systems, play a significant role in extending the life of belt pulleys. These methods enhance the machining process by reducing thermal stress and improving tool life, leading to higher quality pulleys.
Cooling Methods and Their Impact
Exploring various cooling methods reveals their distinct advantages in CNC machining. Techniques like cryogenic cooling, which involves the use of liquid nitrogen, offer exceptional cooling capabilities, reducing thermal deformation and improving material characteristics.
Case Study: Cooling for Quality
An examination of a state-of-the-art manufacturing facility in Shenzhen highlights the benefits of implementing advanced cooling techniques. The facility’s adoption of cryogenic cooling led to a notable improvement in tool longevity and surface integrity, directly influencing the durability and reliability of their belt pulleys.
How Do Post-Processing Techniques Improve the Endurance of Belt Pulleys?
Post-processing techniques, such as heat treatments and surface finishing, significantly enhance the mechanical properties and endurance of CNC-machined belt pulleys. These techniques are crucial for relieving residual stresses and improving the wear resistance of the pulleys.
Data Table: Post-Processing Power Expanded
Technique | Impact on Hardness | Stress Reduction | Toughness Improvement | Surface Finish Improvement | Dimensional Stability | Microstructure Enhancement | Corrosion Resistance Improvement |
---|---|---|---|---|---|---|---|
Heat Treatment | High | Moderate | High | Moderate | High | Significant | Moderate |
Stress Relieving | Moderate | High | Moderate | Low | Moderate | Moderate | Low |
Shot Peening | Low | Moderate | High | High | Low | Low | Low |
Cryogenic Treatment | High | High | Very High | Moderate | High | Significant | High |
Electro-polishing | Moderate | Low | Low | Very High | Moderate | Low | High |
Annealing | Moderate | Very High | High | Moderate | High | Significant | Moderate |
Case Hardening | Very High | Low | Moderate | Low | Moderate | Significant | High |
Nitrocarburizing | High | Moderate | High | Moderate | Moderate | Significant | Very High |
This table provides an in-depth look at various post-processing techniques and their impact on different aspects of belt pulley performance, including improvements in hardness, stress reduction, and corrosion resistance.
What Impact Do Inspection and Quality Control Measures Have on Belt Pulley Durability?
The implementation of rigorous inspection and quality control measures is critical in ensuring the durability and reliability of CNC-machined belt pulleys. These measures help in identifying and rectifying defects early in the manufacturing process, ensuring that only pulleys of the highest quality are produced.
Case Study: The Quality Assurance Protocol
An in-depth examination of a cutting-edge manufacturing setup in Beijing showcases the impact of sophisticated inspection and quality control measures on belt pulley durability. This setup employs advanced metrology tools and stringent testing protocols to ensure each pulley not only meets but exceeds the required performance standards. The meticulous approach to quality control directly translates to enhanced durability and reliability of the pulleys, affirming the crucial role of these measures in the manufacturing process.
Conclusion
The journey through the intricate world of CNC machining and its pivotal role in the production of belt pulleys highlights a multifaceted process where precision, innovation, and quality converge to create components of exceptional durability. In China, where technological advancement meets manufacturing prowess, CNC machining has evolved into an art form that balances the demands of high-speed production with the uncompromising need for precision.
From the initial selection of materials to the final quality control checks, each step in the CNC machining process is critical. The choice of material not only dictates the potential lifespan of a belt pulley but also its suitability for specific applications, underscoring the importance of informed decision-making. Meanwhile, the precision of CNC programming emerges as a cornerstone of manufacturing excellence, directly influencing the functionality and wear characteristics of the finished product.
Surface treatments and post-processing techniques further enhance the endurance of belt pulleys, offering tailored solutions to extend their operational life under varying environmental conditions and usage scenarios. Innovative cooling techniques during machining, such as cryogenic cooling, have opened new avenues for extending tool life and improving material properties, underscoring the dynamic nature of CNC machining technology.
The role of rigorous inspection and quality control measures cannot be overstated. These processes ensure that only belt pulleys meeting the highest standards of quality and durability reach the end user, thereby reinforcing the trust in CNC-machined components.
In conclusion, the durability of CNC-machined belt pulleys is not a product of a single factor but the culmination of numerous carefully calibrated processes and decisions. As CNC machining continues to evolve, so too will the capabilities and longevity of the components it produces. The future of manufacturing belt pulleys, and indeed all CNC-machined parts, looks promising, driven by ongoing advancements in technology, materials science, and manufacturing techniques. The relentless pursuit of excellence in CNC machining is a testament to the industry’s commitment to quality, efficiency, and innovation.
Other Articles You Might Enjoy
- Innovative CNC Machining for Advanced Wearable Technology
Innovative CNC Machining for Advanced Wearable Technology The advent of Computer Numerical Control (CNC) machining and wearable technology has transformed various industries, including healthcare, fitness, fashion, and defense. CNC machining…
- Maximizing Precision in CNC Machining: Techniques and Tips
Importance of Precision in CNC Machining Precision is an fundamental component in the field of Computer Numerical Control (CNC) machining. It entails producing parts that are not only accurate but…
- Precision CNC Machining of Steel: High-Volume Production
Precision CNC Machining and High-Volume Production As an integral part of modern manufacturing processes, Precision Computer Numerical Control (CNC) machining brings about unmatched accuracy and consistency in the production of…