In machining, controlling precision is a crucial aspect that directly affects the quality and performance of the final product. This chapter details the factors influencing machining errors, geometric errors of the process system, deformation due to forces, thermal deformation, and ways to improve machining precision.
Overview of Machining Precision
Machining precision refers to the degree of conformity between the actual geometric parameters of the machined part and the ideal geometric parameters (such as dimensions, shapes, and surface positions). Conversely, machining error is the deviation between the actual geometric parameters of the part and the ideal geometric parameters. Generally, higher machining precision leads to higher machining costs and lower production efficiency. Therefore, designers need to set machining precision reasonably based on the part’s requirements, and process engineers must choose appropriate methods to ensure that machining errors remain within acceptable limits while maximizing productivity and minimizing costs.
Dimensional Accuracy, Shape Accuracy, and Positional Accuracy
These three types of accuracy are closely related. Typically, shape errors are constrained within positional tolerances, and positional errors are constrained within dimensional tolerances. When high dimensional accuracy is required, corresponding high positional and shape accuracy is also necessary. However, high shape or positional accuracy does not always demand high dimensional accuracy, depending on the functional requirements of the part.
Factors Affecting Machining Precision
Geometric Errors of the Process System
The process system includes the machine tool, cutting tool, fixture, and workpiece. Geometric errors in the process system refer to errors caused by inconsistencies between the geometric parameters of the process system and their ideal values, which are often the root cause of machining errors.
- Spindle Rotation Error: This is the deviation of the actual spindle rotation axis from the ideal rotation axis. It can be decomposed into three basic forms: radial runout, axial runout, and angular oscillation. Radial runout significantly affects the accuracy of machining external cylindrical surfaces.
- Guideway Directional Error: This is the deviation of the actual motion direction of the guideway components from the ideal direction. It includes straightness errors in the horizontal and vertical planes, and guideway twist errors. These errors significantly affect machining precision.
Deformation of the Process System Due to Forces
During machining, the process system undergoes deformation due to cutting forces, leading to machining errors. The stiffness of the process system largely determines the extent of this deformation.
- Process System Stiffness: This is the ratio of the external force to the deformation in the direction sensitive to machining errors. The formula for calculating the stiffness of the process system is:
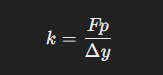
where kkk is the stiffness of the process system, FpFpFp is the cutting resistance, and Δy\Delta yΔy is the displacement of the process system.
Thermal Deformation of the Process System
The process system is affected by heat during machining, leading to thermal deformation and consequently affecting machining precision. Factors influencing thermal deformation include internal heat sources (such as cutting heat and friction heat) and external heat sources (such as ambient temperature).
- Workpiece Thermal Deformation: The workpiece undergoes uneven heating during machining, leading to thermal expansion at different parts and causing deformation. For example, during the machining of a long lead screw, a temperature rise of 1℃ can result in a thermal elongation of 0.005 mm.
Methods to Improve Machining Precision
Error Prevention Techniques
By reasonably adopting advanced processes and equipment, it is possible to effectively reduce original errors or minimize their impact. For instance:
- Transferring Original Errors: This involves transferring errors during the workpiece’s rotation, thereby averaging the original errors, such as in grinding.
- On-line Measurement and Compensation: Real-time measurement of machining dimensions during the process, with automatic compensation to improve machining precision.
Error Compensation Techniques
Introducing additional error factors artificially to offset or reduce the impact of original errors. For example:
- Elastic Deformation to Compensate Thermal Deformation: Using elastic deformation to counteract thermal expansion, such as by appropriately increasing clamping force to offset thermal expansion-induced deformation.
- Thermally Symmetrical Structures: Designing structures that maintain symmetry during thermal expansion to reduce the impact of thermal deformation on machining precision.
Statistical Analysis of Machining Errors
Statistical analysis helps in better understanding and controlling machining errors. Machining errors can be classified into systematic errors and random errors.
- Systematic Errors: These are errors whose magnitude and direction do not change or change according to a specific rule during the machining of a batch of parts. Systematic errors can be offset by appropriate adjustments or repairs to the process equipment.
- Random Errors: These are errors whose magnitude and direction change randomly during the machining of a batch of parts. Random errors are challenging to eliminate entirely but can be minimized.
Statistical analysis helps in determining whether the machining process is stable, assessing process capability, and taking appropriate improvement measures to enhance machining precision.
Other Articles You Might Enjoy
- Control of Machining Precision
Machining precision refers to the degree to which the actual geometric parameters of a machined part conform to the ideal geometric parameters (such as size, shape, and positional relationships). Improving…
- Aerospace Machining: Definition, Materials & Precision Machining Process
Aerospace machining is a crucial aspect of the aerospace industry, with the global market for aerospace machining services expected to surpass $8 billion by 2026. In fact, aerospace manufacturing is…
- Elevating Precision Standards through Chamfer in CNC Machining
1. Introduction: The Pursuit of Unparalleled Precision In the realm of CNC machining, precision is paramount. This section introduces the article by exploring the significance of precision in manufacturing and…
- Precision Prowess: Unveiling the Advantages of China CNC Machining
1. Introduction: The Role of Precision in Manufacturing Excellence In this introductory section, we delve into the critical role that precision plays in manufacturing and set the stage for an…
- Revolutionizing CNC Machining for Complex Aerospace Assemblies
Introduction to CNC Machining in Aerospace Assemblies Computer Numerical Control (CNC) machining represents a significant technological development playing a notable role in the creation of complex aerospace assemblies. CNC machining…
- The Role of Prototype Machining in Accelerating Product Development
Introduction: The Importance and Definition of Prototype Machining Prototype machining is a critical element advancing product development. It involves the technique of manufacturing an early model or sample, known as…