When it comes to CNC machining, choosing the right material is a crucial decision that can significantly impact the cost, performance, and longevity of the final product. Two of the most commonly used materials in CNC machining are titanium and aluminum. Both materials offer unique advantages and are widely used across various industries, from aerospace and automotive to medical and consumer electronics. However, they also have distinct differences that can influence their suitability for specific applications. This article will explore the key factors that should guide your choice between titanium and aluminum, with a particular focus on their cost implications in CNC machined parts.
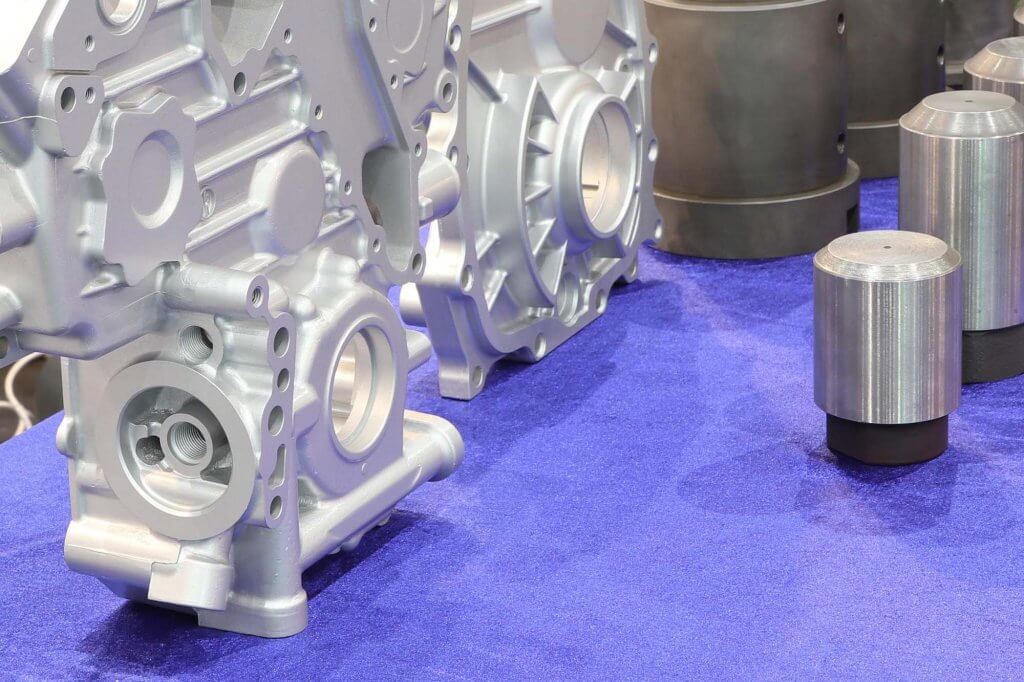
Introduction
CNC machining is a highly versatile manufacturing process that can produce complex parts with high precision. The choice of material plays a vital role in determining the performance, durability, and overall cost of the final product. Titanium and aluminum are two of the most popular materials used in CNC machining due to their favorable properties, but selecting between them requires a thorough understanding of their differences.
Titanium is renowned for its high strength, excellent corrosion resistance, and ability to withstand extreme temperatures. These properties make it an ideal choice for applications where durability and performance are paramount. However, titanium is also more expensive and challenging to machine compared to aluminum.
Aluminum, on the other hand, is valued for its lightweight, good electrical and thermal conductivity, and ease of machining. It is also more cost-effective than titanium, making it a preferred choice for applications where weight and cost are critical factors. But how do these characteristics translate into actual costs and performance in CNC machined parts? Let’s delve into the details.
Performance Comparison: Titanium vs. Aluminum
When choosing between titanium and aluminum for CNC machining, it’s essential to consider several key performance factors, including their elemental composition, density, strength, corrosion resistance, heat resistance, thermal conductivity, and electrical conductivity.
Element Composition
The elemental composition of a material can significantly affect its suitability for different applications.
- Titanium: Primarily composed of titanium, it also contains trace amounts of other elements such as hydrogen, nitrogen, oxygen, iron, carbon, and nickel. These elements, though present in small quantities, play a crucial role in enhancing titanium’s strength and corrosion resistance.
- Aluminum: Aluminum alloys typically contain a mix of elements such as zirconium, zinc, chromium, silicon, magnesium, titanium, manganese, iron, and copper. This diverse composition gives aluminum its lightweight nature, good electrical conductivity, and corrosion resistance.
Density and Strength
Density and strength are critical factors in material selection, especially in industries where weight reduction is essential.
- Titanium: Titanium has a density of 4.51 g/cm³, making it about twice as heavy as aluminum but three times stronger. The high strength-to-density ratio of titanium alloys makes them ideal for applications that require high structural integrity and durability.
- Aluminum: With a density of 2.7 g/cm³, aluminum is lighter than titanium but has lower strength. However, aluminum alloys can achieve a good balance between strength and weight, making them suitable for many applications where weight is a primary concern.
Material | Density (g/cm³) | Strength (MPa) | Strength-to-Density Ratio |
---|---|---|---|
Aluminum | 2.7 | 290 | 107 |
Titanium | 4.51 | 900 | 199 |
Corrosion Resistance
Corrosion resistance is vital in applications exposed to harsh environments, such as marine or aerospace applications.
- Titanium: Titanium offers superior corrosion resistance, particularly in oxidizing environments, due to the formation of a stable oxide layer. This makes it suitable for applications in chemical processing, marine, and aerospace industries.
- Aluminum: Aluminum also has good corrosion resistance, primarily due to its natural oxide layer. However, it is more susceptible to corrosion in certain environments, such as in the presence of chlorides. Modern coatings and treatments can enhance aluminum’s corrosion resistance, making it suitable for a wide range of applications.
Heat Resistance
Heat resistance is another critical factor, especially in high-temperature applications.
- Titanium: Titanium alloys maintain their strength and performance at temperatures up to 500°C, making them suitable for high-temperature environments such as aerospace engine components.
- Aluminum: Aluminum begins to lose its strength at temperatures around 150°C, limiting its use in high-temperature applications. However, its lightweight and thermal conductivity make it ideal for applications where heat dissipation is crucial.
Material | Maximum Operating Temperature (°C) |
---|---|
Aluminum | 150 |
Titanium | 500 |
Thermal Conductivity
Thermal conductivity is important for applications where heat dissipation or retention is critical.
- Titanium: Titanium has a low thermal conductivity, which can be a disadvantage in applications where heat dissipation is required.
- Aluminum: Aluminum has excellent thermal conductivity, making it ideal for heat exchangers, radiators, and other components where efficient heat transfer is necessary.
Material | Thermal Conductivity (W/m·K) |
---|---|
Aluminum | 121 |
Titanium | 17 |
Electrical Conductivity
Electrical conductivity is a key factor in applications involving electrical components.
- Titanium: Titanium has relatively low electrical conductivity, making it less suitable for applications requiring efficient electrical transfer.
- Aluminum: Aluminum offers good electrical conductivity, approximately 64% of that of copper, making it a better choice for electrical applications such as wiring and conductive components.
Cost Analysis: Titanium vs. Aluminum
Cost is a significant factor in material selection for CNC machining, especially when it comes to balancing performance with budget constraints. Let’s explore the cost implications of using titanium versus aluminum in CNC machined parts.
Material Costs
Titanium is significantly more expensive than aluminum. This is due to the higher cost of raw titanium, the complexity of its extraction and refinement, and its challenging machinability. Aluminum, being more abundant and easier to process, is generally more affordable.
- Titanium Costs: The cost of titanium can be up to 10 times higher than that of aluminum, depending on the alloy and market conditions. This makes titanium a less economical choice for projects with tight budget constraints.
- Aluminum Costs: Aluminum is a cost-effective material, particularly for projects requiring large quantities of material or where budget constraints are a priority. Its lower cost makes it an attractive option for mass production.
Material | Average Cost ($/kg) |
---|---|
Aluminum | 2 – 4 |
Titanium | 20 – 30 |
Machining Costs
The machining process for titanium is more complex and time-consuming than for aluminum. Titanium’s hardness and strength make it more challenging to cut, requiring specialized tools, slower cutting speeds, and more frequent tool changes. This increases the overall machining cost.
- Titanium Machining: Machining titanium can be up to three times more expensive than machining aluminum due to the need for specialized equipment and slower machining speeds. Additionally, the wear and tear on tools when machining titanium further increases costs.
- Aluminum Machining: Aluminum is easier to machine, allowing for faster production times and lower costs. The material’s softness means less wear on tools, reducing the frequency of tool changes and further lowering costs.
Material | Relative Machining Cost |
---|---|
Aluminum | Low |
Titanium | High |
Waste and Efficiency Considerations
Material waste is an important factor in CNC machining, especially when using expensive materials like titanium.
- Titanium: Due to its high cost, minimizing waste is critical when machining titanium. However, the material’s properties make it more difficult to minimize waste compared to aluminum.
- Aluminum: Aluminum’s lower cost makes material waste less of a concern, although minimizing waste is still important for cost efficiency.
Applications of Titanium and Aluminum in CNC Machined Parts
Both titanium and aluminum have a wide range of applications across various industries, thanks to their unique properties. Here’s a look at where these materials are most commonly used.
Aerospace Industry
- Titanium: Titanium is widely used in the aerospace industry for components such as aircraft frames, engine components, and landing gear. Its high strength-to-weight ratio and excellent corrosion resistance make it ideal for these demanding applications.
- Aluminum: Aluminum is also extensively used in aerospace, particularly for components such as aircraft skins, wings, and fuselage frames. Its lightweight nature and good corrosion resistance make it suitable for reducing aircraft weight while maintaining structural integrity.
Medical Industry
- Titanium: Titanium is favored in the medical industry for implants, surgical instruments, and prosthetics due to its biocompatibility, strength, and resistance to bodily fluids.
- Aluminum: While not as common as titanium in medical applications, aluminum is used in medical devices and equipment where weight and cost are more critical than biocompatibility.
Automotive Industry
- Titanium: Titanium is used in high-performance automotive applications, such as exhaust systems, suspension components, and engine parts, where strength and corrosion resistance are critical.
- Aluminum: Aluminum is widely used in the automotive industry for engine components, wheels, body panels, and structural components due to its lightweight nature and good strength-to-weight ratio.
Consumer Electronics
- Titanium: Titanium is used in high-end consumer electronics for its durability and premium appearance. It’s often found in luxury watches, smartphones, and laptops.
- Aluminum: Aluminum is the material of choice for most consumer electronics due to its lightweight, cost-effectiveness, and ease of machining. It’s commonly used in casings, frames, and internal components.
Construction and Infrastructure
- Titanium: While less common in construction due to its cost, titanium is used in specialized applications requiring high corrosion resistance, such as in chemical plants and offshore structures.
- Aluminum: Aluminum is widely used in construction for roofing, window frames, and structural components due to its lightweight and corrosion resistance.
Choosing the Right Material for Your CNC Machined Parts
When deciding between titanium and aluminum for your CNC machined parts, it’s essential to consider your project’s specific requirements and how each material’s properties align with those needs.
Project Requirements and Performance Criteria
- Strength and Durability: If your project requires high strength and durability, especially in demanding environments, titanium is likely the better choice despite its higher cost.
- Weight Considerations: For projects where weight is a critical factor, aluminum’s lighter density may be more advantageous.
- Cost Constraints: If budget is a significant concern, aluminum’s lower material and machining costs make it the more economical choice.
- Environmental Resistance: For applications exposed to harsh environments, titanium’s superior corrosion and heat resistance could justify the higher cost.
- Machinability: If ease of machining and fast production times are priorities, aluminum is the preferred material due to its lower machining costs and faster turnaround.
Cost vs. Benefit Considerations
It’s essential to balance the upfront costs with the long-term benefits when choosing between titanium and aluminum.
- Titanium: While titanium may have higher material and machining costs, its durability, strength, and resistance to corrosion and extreme temperatures can result in longer-lasting parts that may reduce maintenance and replacement costs over time.
- Aluminum: Aluminum’s lower cost and ease of machining make it ideal for projects with tight budgets and quick turnaround times. However, its lower strength and durability compared to titanium may require more frequent maintenance or replacement in demanding applications.
Conclusion
Choosing between titanium and aluminum for CNC machined parts requires a careful consideration of multiple factors, including performance, cost, and application requirements. While titanium offers unmatched strength, durability, and corrosion resistance, aluminum provides a more cost-effective solution with good machinability and sufficient performance for many applications. By understanding the strengths and weaknesses of each material, you can make an informed decision that aligns with your project’s needs and budget.
FAQ
- What are the most common types of aluminum alloys used in CNC machining?
- The most common types of aluminum alloys used in CNC machining include 6061, 7075, 5020, and 8020 aluminum. Each alloy offers a different balance of strength, corrosion resistance, and machinability.
- Which is better for CNC machining, titanium or aluminum?
- The choice between titanium and aluminum depends on the specific requirements of the project. Titanium offers superior strength and corrosion resistance, while aluminum is more cost-effective and easier to machine.
- Is aluminum easier to machine than titanium?
- Yes, aluminum is generally easier to machine than titanium due to its softer nature, which allows for faster machining speeds and less wear on tools.
- Does titanium last longer than aluminum?
- Titanium generally lasts longer than aluminum due to its higher strength, corrosion resistance, and durability, making it ideal for applications in harsh environments.
Other Articles You Might Enjoy
- Unraveling the World of CNC Machined Plastic Parts(CNC machined plastic parts Mabel)
Modern innovations have taken traditional manufacturing methods to new heights. One such innovation that stands out is Computer Numerical Control (CNC) machining, a process used extensively in various industries from…
- CNC Machined Plastic Parts: An In-depth Overview(CNC machined plastic parts Norman)
Computer Numeric Control (CNC) machining is an advanced manufacturing process where pre-programmed software dictates the movement of factory machinery and tools. These applications can carry out complicated manufacturing tasks with…
- Enhancing CNC Machining with Smart Alloys: Shape Memory Metals vs. Traditional Alloys
Introduction to CNC Machining Computer Numerical Control (CNC) machining stands as a cornerstone in modern manufacturing, enabling the precise and automated shaping of materials. This technology relies heavily on the…
- CNC Machining for Aerospace Applications: Titanium vs. Aluminum Alloys
CNC Machining in Aerospace: An Introduction and Overview Computer Numerical Control (CNC) machining is a manufacturing process that utilizes software-directed machines to fabricate complex parts with high accuracy and repeatability.…
- The Advantages of Using LSR (Liquid Silicone Rubber) in CNC Prototyping and Production?
Introduction to LSR in CNC Prototyping and Production The utilization of Liquid Silicone Rubber (LSR) in CNC prototyping and production has been growing exponentially due to its numerous advantages. For…
- The Evolution of Plastics in CNC Machining: From ABS to PEEK?
The Evolution of Plastics in CNC Machining: From ABS to PEEK CNC machining, also known as Computer Numerical Control machining, plays an integral role in contemporary manufacturing processes. It enables…