Introduction to Delrin Material
Delrin, also known as POM-H (Polyoxymethylene Homopolymer), is a high-performance engineering thermoplastic. It is widely used in precision machining, 3D printing, and injection molding due to its exceptional material properties. For procurement managers looking to source cnc machined parts made from Delrin, understanding its unique characteristics and its suitability for high-speed cutting applications is essential. Delrin has earned a reputation as a versatile material that can deliver durability, strength, and dimensional stability, making it a favored choice in many industries.
As a homopolymer of acetal resin, Delrin offers superior performance compared to other plastics like ABS or even other variants of POM, such as POM-C (copolymer). In this guide, we’ll take a closer look at Delrin’s material properties, its role in precision machining, and the capabilities that suppliers must have to meet the high demands of producing Delrin-based components.
What Is Delrin and What Makes It Unique?
Delrin is part of the polyoxymethylene (POM) family, specifically the homopolymer variant (POM-H), which stands out due to its high crystallinity. Delrin is manufactured through a polymerization process where hydrocarbons are distilled to produce its final resin form. This process creates a thermoplastic with exceptional mechanical properties, such as low friction, high tensile strength, and excellent dimensional stability.
The key characteristics that set Delrin apart include its high stiffness, resistance to wear, low coefficient of friction, and wide operating temperature range (-40°C to 120°C). These properties make it ideal for creating precision parts that can perform under high mechanical loads and in varying environmental conditions.
Delrin was commercially synthesized by DuPont in 1956 and has since become a preferred material for manufacturing high-precision parts. Below is a table summarizing the essential properties that make Delrin a standout material in manufacturing:
Property | Delrin Material Value | Description |
---|---|---|
Tensile Strength | 60 – 89.6 MPa | Provides high mechanical strength and resistance to stress. |
Yield Strength | 48.6 – 72.4 MPa | Maintains shape under high loads. |
Modulus of Elasticity | 2.5 – 4 GPa | High stiffness and rigidity, critical for durable components. |
Operating Temperature | -40°C to 120°C | Wide range of operational temperatures. |
Coefficient of Friction | Low | Excellent for parts requiring low friction. |
Dimensional Stability | Excellent | Minimal deformation under load, ideal for precision parts. |
Water Absorption | Low | Resists moisture, making it suitable for humid environments. |
How Is Delrin Manufactured?
The production of Delrin involves several critical steps that ensure the material maintains its high-performance characteristics. Delrin is created by polymerizing formaldehyde, a process that involves converting hydrocarbons into formaldehyde gas, which is then polymerized to form long chains of polyoxymethylene. This polymerization reaction results in the formation of highly crystalline thermoplastic granules that can be further processed into various shapes through molding or machining.
DuPont, the original developer of Delrin, introduced the material as a part of the larger family of acetal resins. The manufacturing process ensures Delrin retains its superior properties such as stiffness, high fatigue resistance, and excellent machinability, making it ideal for a variety of precision parts.
Key Applications of Delrin Material Across Industries
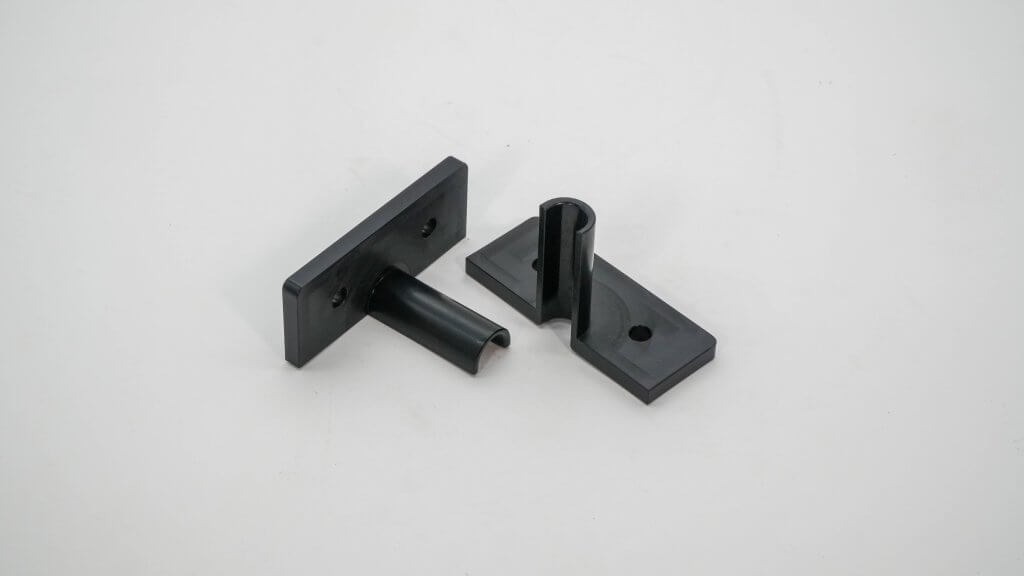
Delrin’s material properties allow it to replace metals like steel, aluminum, and copper in many industries. It can be used in applications where weight reduction, corrosion resistance, and wear resistance are required. This makes Delrin an excellent choice for a variety of industries, including:
- Automotive Industry: Delrin is widely used to manufacture gears, bushings, bearings, and fuel system components. Its low friction and wear resistance make it ideal for parts that are constantly in motion or subject to mechanical stress.
- Aerospace Industry: In aerospace applications, Delrin is often used to produce lightweight, precision parts that must withstand harsh environmental conditions. It is used in applications such as control mechanisms, landing gear components, and fasteners.
- Medical Devices: Delrin’s biocompatibility and high precision make it ideal for manufacturing medical instruments and devices like insulin pens, inhalers, and other disposable medical tools.
- Consumer Electronics: Delrin’s strength and durability also make it suitable for various electronic components, such as connectors, housings, and other high-stress parts that require precision.
- Industrial Machinery: Delrin is used in machinery for creating precision gears, rollers, and pump components that need to endure repetitive motion and friction while maintaining dimensional stability.
Delrin in High-Speed Cutting Applications
One of Delrin’s most significant advantages is its high machinability. When combined with high-speed cutting technologies, Delrin offers significant benefits for manufacturers. Its ability to maintain dimensional stability during machining, resist warping, and be easily cut at high speeds makes it a cost-effective choice for precision parts.
Suppliers specializing in high-speed machining of Delrin can produce parts with tight tolerances more efficiently than with many other materials. Delrin’s low friction also means less wear on cutting tools, extending tool life and reducing overall production costs.
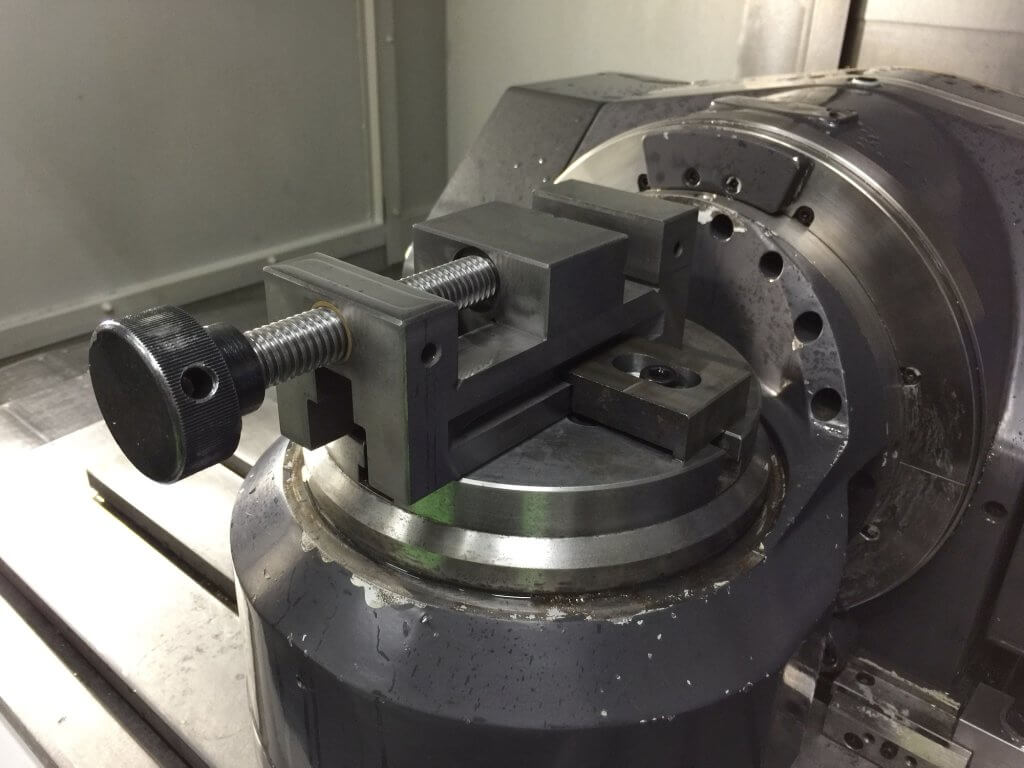
Below is a breakdown of Delrin’s high-speed cutting parameters:
Cutting Parameter | Recommended Value | Impact on Machining |
---|---|---|
Cutting Speed | 240-500 m/min | Ensures precise cuts with minimal material deformation. |
Feed Rate | 0.05 – 0.30 mm/rev | Optimizes material removal rate while maintaining precision. |
Depth of Cut | 2 – 5 mm | Allows for medium-depth cuts, maintaining dimensional accuracy. |
Tool Material | Carbide or Diamond-Coated | Ensures clean, high-precision cuts and extends tool life. |
Tool Life | Long | Delrin’s low wear rate results in longer tool lifespan. |
Cooling Requirements | Minimal (air blast or dry cutting) | Delrin requires less cooling, simplifying the machining process. |
The chart above illustrates how Delrin’s properties align with the needs of high-speed cutting, particularly for applications that require rapid production without sacrificing part accuracy or tool longevity.
Proper Surface Finishes for Delrin Parts
Surface finishes is an important consideration for parts made from Delrin, especially for those used in applications where appearance or additional surface durability is required. While Delrin typically offers a smooth finish directly after machining, additional surface treatments can further enhance its performance.
Common surface treatments for Delrin include:
- Bead Blasting: This process gives Delrin parts a uniform matte finish and can help remove any machine marks that might be present after cutting or milling. Bead blasting also improves the part’s resistance to wear and impact.
- Laser Marking: For parts that require identification, logos, or precision markings, laser marking is often used. Delrin responds well to laser marking and produces sharp, clear marks without damaging the material’s surface.
- Painting and Coating: While Delrin is naturally resistant to moisture and many chemicals, parts that need additional aesthetic qualities or environmental resistance can be coated or painted. For example, Delrin parts can be painted and cured at temperatures up to 160°C.
- Metallization: Delrin parts can be metalized with copper, chrome, or aluminum to enhance both their appearance and durability. This process is especially useful for components that are visible or need to withstand additional mechanical wear.
Each of these surface treatments enhances the material’s durability and appearance, making Delrin a versatile option for various industrial applications.
How Much Does It Cost to Machine Delrin Parts?
The cost of machining Delrin parts depends on several factors, including the complexity of the design, the quantity of parts needed, and the machining techniques required. Delrin is generally considered to be one of the more affordable engineering plastics due to its machinability, which reduces production time and tool wear.
Key cost factors include:
- Material Cost: Delrin is slightly more expensive than other plastics like ABS but offers superior performance, especially in precision applications.
- Machining Complexity: Simple parts with minimal design features will naturally cost less than complex parts with intricate geometries that require longer machining times.
- Tooling and Setup: While Delrin is easier to machine compared to metals, the cost of tooling and machine setup will also influence the final price. Carbide and diamond-coated tools are recommended for high-speed machining, which could increase tooling costs but reduce wear and tear.
- Volume: As with most manufacturing processes, the cost per unit decreases with larger production volumes. Ordering larger quantities of Delrin parts will help spread out the setup and tooling costs, lowering the overall price.
What Are Delrin’s Limitations?
Despite its many advantages, Delrin does have a few limitations that should be considered during the design and manufacturing process. Understanding these limitations will help you choose the right material for your specific application.
- Difficulty with Bonding: One of Delrin’s primary drawbacks is its resistance to adhesives
. Due to its low surface energy, Delrin does not easily bond with many types of adhesives. This can complicate assembly processes where bonding is necessary, and alternative mechanical fastening methods like screws or snap-fits are often required.
- Heat Sensitivity: While Delrin can withstand temperatures up to 120°C, prolonged exposure to high temperatures can cause the material to degrade. Additionally, Delrin is flammable and must be handled carefully in applications where high heat is involved.
- Limited Resistance to Strong Acids and Bases: Delrin is resistant to many chemicals, but it can degrade when exposed to strong acids and bases, particularly at high temperatures. In environments where the material will come into contact with such substances, an alternative plastic or metal may be more appropriate.
- UV Sensitivity: Delrin is not UV-stable, meaning it can degrade over time when exposed to direct sunlight. For outdoor applications, Delrin should either be coated with a UV-resistant material or another plastic should be considered.
Design Limitations for Delrin Parts
Designing with Delrin offers a great deal of flexibility, but there are still some key considerations that should be kept in mind to ensure optimal performance and machinability. Here are a few design limitations and best practices:
- Avoid Thin Walls: While Delrin is strong and durable, very thin walls can warp or become brittle, especially during machining. It’s recommended to design parts with sufficient wall thickness to ensure structural integrity.
- Tight Tolerances: Delrin is dimensionally stable, but it’s essential to avoid overly tight tolerances unless absolutely necessary. Excessively tight tolerances can increase machining costs and complexity.
- Include Internal Radii: In CNC machining, it’s difficult to cut sharp 90-degree internal corners because of the circular nature of milling tools. Including internal radii in the design not only eases machining but also reduces tool wear and time.
- Depth of Threads: In threaded parts, it’s advised to keep thread depths below three times the hole diameter to avoid excessive machining time and tool wear. Deeper threads can increase the complexity of machining and drive up costs.
Conclusion
Delrin is a versatile and highly machinable material that offers substantial advantages for precision machining and high-speed cutting applications. For procurement managers and sourcing professionals, understanding Delrin’s unique properties and the machining expertise required to work with it effectively is key to making informed decisions when selecting a supplier.
Whether used in automotive, aerospace, medical devices, or industrial machinery, Delrin delivers exceptional performance, durability, and cost-efficiency, making it an ideal choice for a wide range of precision parts. Ensuring that your supplier has the right capabilities, including experience with high-speed machining and quality control, will ensure that your Delrin components meet the highest standards of performance and reliability.
FAQs about Delrin Material and Machining
- What makes Delrin a preferred material for high-speed machining?
Delrin offers excellent machinability, strength, and low friction, making it ideal for high-speed cutting and precision machining processes. - How does Delrin compare to metals like aluminum or steel?
Delrin is lighter, more corrosion-resistant, and easier to machine than metals, making it a preferred alternative in many applications. - How is Delrin manufactured?
Delrin is made through a polymerization process involving formaldehyde, which creates a high-crystallinity polymer with excellent mechanical properties. - What are the common surface treatments for Delrin parts?
Common surface treatments include bead blasting, laser marking, painting, and metallization, all of which enhance the appearance and durability of Delrin parts. - How much does it cost to machine Delrin parts?
The cost varies depending on factors like part complexity, material volume, and tooling setup, but Delrin is generally affordable due to its machinability. - What are Delrin’s limitations?
Delrin is difficult to bond with adhesives, can degrade under high heat or UV exposure, and is not resistant to strong acids or bases. - What design limitations should be considered when machining Delrin?
Designers should avoid thin walls, overly tight tolerances, and sharp internal corners to optimize machinability and reduce costs.
Other Articles You Might Enjoy
- Delrin in CNC Machining: The Ultimate Guide for Engineers
Introduction to Delrin and Its Role in CNC Machining Delrin, a high-performance engineering plastic, has become a cornerstone material for industries relying on precision machining. This polyoxymethylene homopolymer (POM-H) is…
- How CNC Machining Delivers Precision in Custom POM Plastic Parts
Working with POM plastic in CNC machining has become a popular choice for manufacturers due to its excellent mechanical properties, low friction, and high dimensional stability. Customizing parts using this…
- Machining Materials: Delrin vs. PEEK in High-Precision Applications
Machining Materials: An Introduction to Delrin and PEEK Machining materials, as the term implies, are types of substances specifically designed to be cut and fashioned into usable items by machining…
- What material is delrin
Introduction to Delrin Delrin, also known as Polyoxymethylene (POM), is an engineering thermoplastic commonly used in precision parts that require high stiffness, low friction, and excellent dimensional stability. Recognized for…
- Machining Precision and Its Control
In machining, controlling precision is a crucial aspect that directly affects the quality and performance of the final product. This chapter details the factors influencing machining errors, geometric errors of…
- High-Precision CNC Machining for Military Applications
Introduction to High-Precision CNC Machining in Military Applications The technical realm of high-precision Computer Numeric Control (CNC) machining is fast becoming integral to the military sector. This process, which relies…
- Delrin in CNC machining technology
Delrin, a trademarked name for polyoxymethylene (POM), is an engineering thermoplastic known for its high strength, rigidity, and resistance to friction and wear. This semi-crystalline plastic boasts exceptional dimensional stability…
- CNC Machining Tolerances and Material Selection: Precision Engineering Insights
Introduction to CNC Machining, Tolerances and Material Selection CNC machining is a prevalent manufacturing process that entails the use of pre-programmed computer software to dictate the movement of factory machinery…