A Brief Introduction to the Importance of Titanium and Steel in Manufacturing
In the modern world, manufacturing has become the backbone of economic development, driving industries, innovation, and infrastructure. At the heart of this process are materials that shape the products we use every day, ranging from industrial machinery to consumer electronics, medical devices, and aerospace components. Among the most vital materials in manufacturing are titanium and steel. These metals have become indispensable due to their unique properties, such as strength, durability, and versatility. While steel has long dominated industrial applications, titanium has emerged as a strong contender, particularly in specialized fields requiring lighter, corrosion-resistant materials.
Applications and Importance of Titanium in Manufacturing
The value of titanium in manufacturing extends beyond its physical properties. Its unique characteristics make it essential in industries where high-performance materials are required. Below are some of the key sectors where titanium plays a critical role:
1. Aerospace Industry
Titanium’s high strength-to-weight ratio and resistance to extreme temperatures make it a preferred material in the aerospace industry. Aircraft manufacturers use titanium in engine components, landing gear, and structural parts of aircraft to reduce weight without sacrificing safety or durability. Titanium is also essential in spacecraft and satellite construction, where both weight and the ability to withstand the harsh environment of space are critical.
In jet engines, titanium’s ability to retain strength at high temperatures makes it ideal for components such as compressor blades, discs, and casings. The use of titanium reduces fuel consumption by lowering the overall weight of the aircraft, which is a significant advantage in the aerospace industry.
2. Medical Industry
Titanium’s biocompatibility has made it a material of choice in the medical field, particularly in the production of implants, prosthetics, and surgical instruments. Titanium is used in bone and joint replacements because it integrates well with human tissue without causing adverse reactions. It is also corrosion-resistant, ensuring that implants made from titanium last longer inside the human body.
Dental implants, hip replacements, and pacemaker casings are just a few examples of titanium’s applications in the medical field. Titanium’s use in these critical devices highlights its importance in improving the quality of life for patients and advancing medical technology.
3. Chemical Processing and Marine Applications
In chemical processing plants, titanium is used in equipment exposed to highly corrosive substances. Its resistance to corrosion from acids and chemicals ensures the longevity and safety of processing equipment. Titanium heat exchangers, condensers, and reactor vessels are common in industries such as oil and gas, pharmaceuticals, and petrochemicals.
In marine applications, titanium’s corrosion resistance to seawater makes it ideal for use in shipbuilding, submarines, and offshore oil rigs. Components such as propeller shafts, valves, and hulls benefit from titanium’s ability to withstand the corrosive effects of saltwater, ensuring durability and reliability in harsh marine environments.
4. Automotive Industry
While titanium is not as widely used in the automotive industry as steel due to its cost, it has found applications in high-performance and luxury vehicles. Titanium’s lightweight and high strength make it suitable for exhaust systems, suspension components, and engine valves. These applications help reduce the vehicle’s overall weight, improving fuel efficiency and performance.
As the automotive industry continues to push for more fuel-efficient and environmentally friendly vehicles, the demand for lightweight materials like titanium is expected to increase.
Applications and Importance of Steel in Manufacturing
Steel’s versatility and cost-effectiveness have made it the backbone of manufacturing for centuries. It is used in a wide range of industries and applications, some of which are highlighted below:
1. Construction Industry
Steel is an essential material in the construction of buildings, bridges, and infrastructure. Its high tensile strength and durability make it the ideal material for structural frameworks, reinforcing bars (rebar), and support beams. Steel’s ability to withstand heavy loads and resist natural forces such as earthquakes and strong winds makes it a staple in modern architecture and engineering.
In skyscraper construction, steel allows for taller and more stable structures, while in bridges, it provides the necessary strength to span long distances while supporting substantial weight. The Golden Gate Bridge and the Eiffel Tower are famous examples of steel’s impact on engineering and architecture.
2. Automotive Industry
The automotive industry relies heavily on steel for the production of vehicles. Steel’s strength, formability, and affordability make it the material of choice for car bodies, frames, and engine components. High-strength steel is used in modern vehicles to improve safety by enhancing the vehicle’s ability to absorb impact in the event of a collision.
Steel’s recyclability also plays a crucial role in the automotive industry’s sustainability efforts. By using recycled steel in vehicle manufacturing, automakers can reduce their environmental footprint while maintaining the material’s performance characteristics.
3. Tool and Machinery Manufacturing
Steel’s hardness and durability make it the material of choice for producing tools and machinery. Tool steels, which contain high levels of carbon and alloying elements, are specifically designed to withstand wear and deformation, making them ideal for cutting, drilling, and shaping other materials.
Steel is also used in the manufacture of industrial machinery such as conveyor belts, machine parts, and agricultural equipment. The durability and strength of steel ensure that these machines can operate under heavy loads and in harsh environments, making it indispensable to industries such as manufacturing, mining, and agriculture.
4. Energy Industry
In the energy sector, steel is used in the construction of oil rigs, pipelines, and power plants. The material’s strength and corrosion resistance make it suitable for use in offshore oil drilling platforms, where it must withstand both the mechanical stress of drilling and the corrosive effects of seawater.
Steel pipelines are essential for transporting oil, gas, and water over long distances. The durability of steel ensures that these pipelines can safely operate for decades with minimal maintenance, making them a critical component of global energy infrastructure.
The importance of titanium and steel in manufacturing cannot be overstated. As industries evolve and new technologies emerge, both materials will continue to play a critical role in shaping the future of manufacturing.
The material properties comparison of titanium and steel
In CNC machining, the choice between titanium and steel is often influenced by their distinct material properties. These two metals exhibit significantly different chemical compositions, densities, strengths, and behaviors under different conditions, making them suitable for different applications. This section provides a detailed comparison of their properties, which play an essential role in the decision-making process when selecting the best material for a given project.
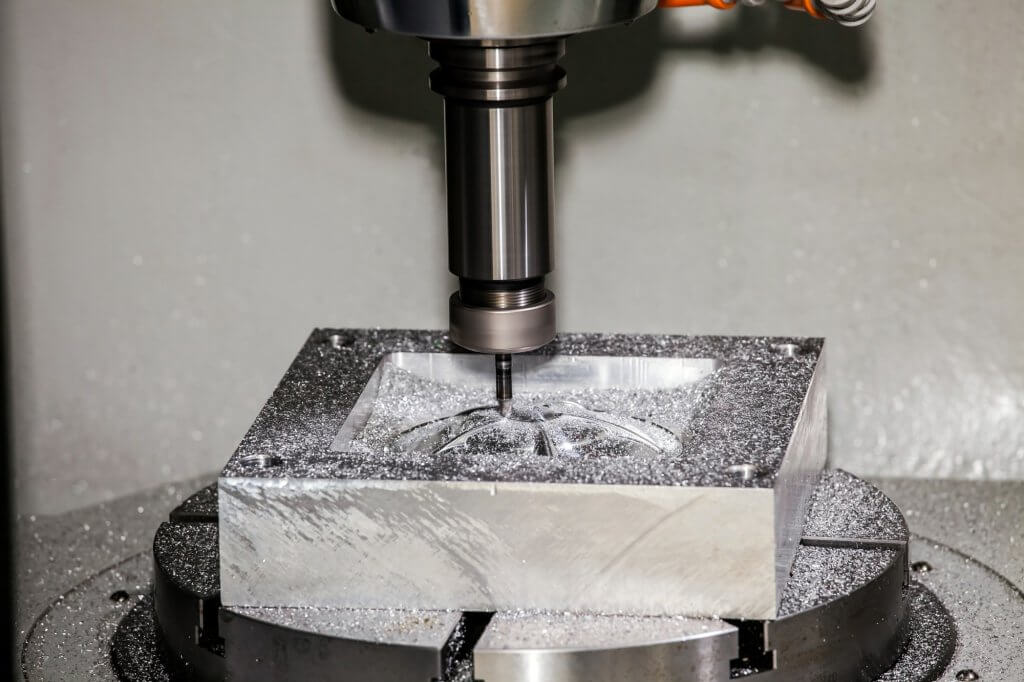
Titanium
1. Chemical Composition and Classification
Titanium, an element with the atomic number 22, is known for its versatility. The most commonly used titanium alloy in manufacturing is Ti-6Al-4V, which consists of:
- 6% aluminum (Al)
- 4% vanadium (V)
- The remaining percentage being pure titanium.
This alloy is popular due to its excellent balance between strength, lightweight, and corrosion resistance. In addition to Ti-6Al-4V, other titanium alloys are categorized into three major groups:
- Alpha alloys: These have excellent weldability and are used in high-temperature applications. However, their strength is lower than other titanium alloys.
- Beta alloys: Known for their flexibility, beta alloys have a higher density and are used where both strength and formability are necessary.
- Alpha-Beta alloys: Ti-6Al-4V falls into this category, combining the best of both alpha and beta alloy properties.
Titanium Alloy | Primary Alloying Elements | Application | Strength |
---|---|---|---|
Ti-6Al-4V | Aluminum, Vanadium | Aerospace, Medical, Marine | High |
Ti-5Al-2.5Sn | Aluminum, Tin | High-Temperature Applications | Moderate |
Ti-10V-2Fe-3Al | Vanadium, Iron, Aluminum | Automotive, Aerospace | Very High |
2. Density and Weight
Titanium is known for having an exceptionally high strength-to-weight ratio. The density of titanium is 4.5 g/cm³, which is significantly lower than steel. This makes titanium ideal for applications where reducing weight is critical, such as in aerospace, automotive, and sports equipment manufacturing.
For example:
- Steel typically has a density of about 7.8 g/cm³, making it nearly twice as dense as titanium. This means for the same volume, steel parts will weigh more than titanium counterparts.
This lightweight feature makes titanium a preferred material in industries where performance is heavily influenced by the mass of components.
3. Strength, Stiffness, and Corrosion Resistance
Titanium is renowned for its strength and stiffness. Despite its lightness, titanium alloys like Ti-6Al-4V can achieve tensile strengths as high as 1000 MPa (megapascals). However, one drawback is that titanium is less stiff than steel, meaning it can deform more under stress. However, this does not take away from its advantage in many applications where lightness and durability are needed over absolute stiffness.
Corrosion resistance is another standout feature of titanium. In environments where metals are prone to corrosion, such as in marine or chemical processing industries, titanium remains unaffected by seawater, chlorine, or acidic substances. This property gives it a significant edge over steel in long-term, harsh environments.
4. Heat Resistance
One of the defining features of titanium is its ability to maintain strength even at high temperatures. It can retain its mechanical properties at temperatures up to 600°C (1,112°F). This makes titanium alloys essential in the aerospace industry, especially for parts exposed to extreme heat, such as jet engines and spacecraft.
5. Biocompatibility
Titanium’s biocompatibility is unrivaled in the medical field. It is non-toxic and non-reactive with human tissues, making it the preferred material for medical implants, such as hip replacements, dental implants, and pacemakers. Unlike steel, titanium does not corrode inside the body, ensuring longevity and compatibility for patients with medical implants.
Steel
1. Chemical Composition and Classification
Steel is an alloy made primarily of iron and carbon, but it often contains various other elements such as chromium, manganese, nickel, and molybdenum to enhance specific properties. There are several types of steel, each with its unique chemical composition and application:
- Carbon Steel: Contains mainly iron and carbon and is the most widely used type of steel. Its properties can vary based on carbon content.
- Stainless Steel: Contains at least 10.5% chromium, which provides corrosion resistance. It is commonly used in kitchenware, medical devices, and industrial machinery.
- Tool Steel: Alloyed with elements such as tungsten, molybdenum, and vanadium, it is known for its hardness and ability to retain a cutting edge.
Type of Steel | Primary Alloying Elements | Application | Strength |
---|---|---|---|
Carbon Steel | Iron, Carbon | Construction, Structural Components | Moderate |
Stainless Steel | Chromium, Nickel | Kitchenware, Medical Instruments | High |
Tool Steel | Tungsten, Molybdenum, Vanadium | Cutting Tools, Molds, Dies | Very High |
2. Density and Weight
Steel is significantly heavier than titanium, with a density of approximately 7.8 g/cm³. This makes steel parts almost twice as heavy as titanium parts of the same size. While this can be seen as a disadvantage in applications where weight reduction is critical, it is an advantage in situations where mass and inertia are beneficial, such as in structural applications.
3. Strength, Stiffness, and Corrosion Resistance
Steel’s primary advantage is its high strength and stiffness. Depending on the type of steel, tensile strengths can range from 400 MPa to over 2,000 MPa, especially in high-carbon and tool steels. This makes steel the go-to material for structural applications like bridges, buildings, and heavy machinery.
However, compared to titanium, steel is more prone to corrosion, especially in humid or marine environments. Stainless steel can resist corrosion due to its chromium content, but even it can suffer from rust and pitting over time if exposed to certain conditions.
4. Wear Resistance and Ductility
Steel is known for its high wear resistance, especially tool steels that are engineered for heavy-duty applications like cutting, drilling, and machining. Steel’s ductility (ability to deform without breaking) is another notable property, which makes it easier to weld, bend, and shape in manufacturing processes.
Ductility also allows steel to absorb energy better than titanium, which can fracture under impact. This makes steel ideal for applications where materials need to bend or stretch rather than break under stress.
5. Impact of Heat Treatment
One of the significant advantages of steel is its ability to be heat treated to adjust its mechanical properties. Through processes like quenching and tempering, steel can be made harder, softer, or tougher, depending on the desired characteristics.
Steel Type | Heat Treatment | Effect on Properties |
---|---|---|
Carbon Steel | Annealing | Increases ductility, reduces hardness |
Tool Steel | Quenching and Tempering | Increases hardness and wear resistance |
Stainless Steel | Solution Annealing | Restores corrosion resistance, softens |
Heat treatment provides flexibility in manufacturing, allowing steel to be tailored for a wide range of applications that require specific hardness, strength, or wear resistance.
Comparison Summary Table: Titanium vs Steel
Property | Titanium | Steel |
---|---|---|
Density | 4.5 g/cm³ | 7.8 g/cm³ |
Tensile Strength | 900-1000 MPa (for Ti-6Al-4V) | 400-2000 MPa (varies by steel type) |
Corrosion Resistance | Excellent (in seawater, acids) | Moderate (except for stainless steel) |
Wear Resistance | Moderate | High (especially in tool steel) |
Ductility | Moderate | High (varies by steel type) |
Heat Resistance | Up to 600°C | Varies (depending on type and treatment) |
Biocompatibility | Excellent | Good (but can corrode in the body) |
Cost | High | Moderate to Low |
Weight | Lightweight (nearly half that of steel) | Heavy (nearly twice that of titanium) |
How Does the Machinability of Titanium and Steel Compare in CNC Machining?
When it comes to CNC machining, the machinability of a material directly affects production efficiency, tooling costs, and final product quality. Both titanium and steel present unique challenges and opportunities for machinists, depending on the type of alloy, the desired precision, and the cutting techniques applied. In this section, we will explore the machinability of titanium and steel, considering factors such as tool wear, heat dissipation, and the optimization of cutting speeds and feed rates.
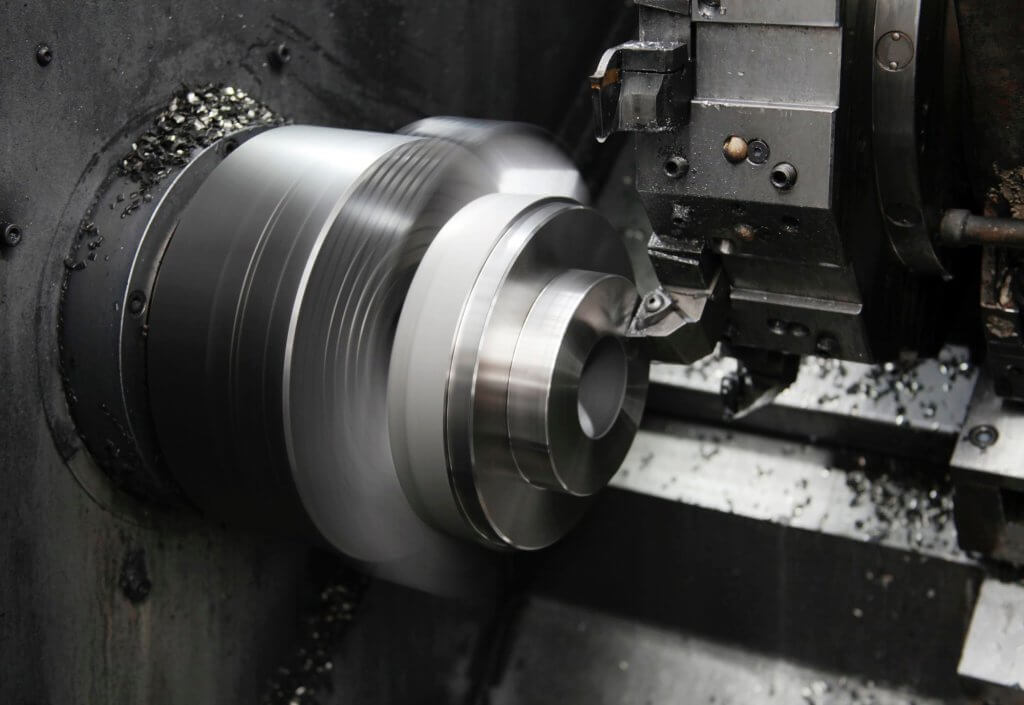
Machinability of Titanium
1. Titanium’s Machining Challenges
Titanium is widely known for being a difficult material to machine. While its strength-to-weight ratio, corrosion resistance, and heat resistance make it desirable for high-performance applications, these same properties contribute to its poor machinability. Several factors contribute to titanium’s challenging behavior during CNC machining:
- High Hardness: Titanium’s strength means it has a high hardness level, which results in significant resistance to cutting and tends to cause rapid wear on cutting tools. This increases the cost of tooling and can lead to more frequent tool changes, thereby affecting productivity.
- Low Thermal Conductivity: Titanium has poor thermal conductivity compared to other metals. This characteristic causes heat to concentrate at the cutting zone rather than being absorbed or dissipated. As a result, excessive heat can build up, which not only reduces tool life but can also cause thermal damage to the workpiece surface, leading to inaccuracies in the final product.
Titanium Machining Challenges | Effects |
---|---|
High Hardness | Accelerated tool wear, higher tooling costs |
Low Thermal Conductivity | Heat buildup, poor surface finish, reduced accuracy |
2. Tool Wear and Heat Dissipation Challenges
Tool wear is a significant concern when machining titanium. As the cutting tools interact with titanium, the poor heat dissipation exacerbates the wear, particularly at the tool’s cutting edge. This leads to rapid degradation of the tool’s sharpness, reducing machining precision and increasing surface roughness.
To counter this, machinists often employ specialized tools made from carbide or diamond-coated materials, which can better withstand the extreme conditions of titanium machining. Even with high-quality tools, optimizing tool geometry—such as choosing the correct rake angles—can minimize wear and improve performance. Additionally, using high-pressure coolant systems can help dissipate heat and flush away chips, reducing tool wear.
3. Optimizing Cutting Speeds and Feed Rates
The key to successful titanium machining lies in optimizing cutting speeds and feed rates. Due to the material’s hardness and heat sensitivity, the following parameters must be carefully adjusted:
- Cutting Speed: Titanium requires slower cutting speeds than other metals to prevent overheating. Typical cutting speeds for titanium range from 30 to 60 meters per minute. Exceeding this range can lead to rapid tool wear and poor surface quality.
- Feed Rate: A higher feed rate should be used with caution. Titanium does not respond well to aggressive cutting, and slower feed rates (around 0.1 to 0.3 mm/rev) are often preferred to maintain surface quality while extending tool life.
Parameter | Recommended Range |
---|---|
Cutting Speed | 30-60 meters per minute (m/min) |
Feed Rate | 0.1-0.3 mm/revolution |
Achieving the right balance between cutting speed and feed rate helps ensure a smooth machining process without damaging the tool or workpiece.
4. Coolant Strategy for Titanium Alloys
Using the right coolant strategy is essential when machining titanium. Coolants help reduce friction and heat at the cutting interface, which is crucial for preserving tool life and preventing thermal damage to the titanium workpiece. Coolants for titanium machining should have high-pressure capabilities to ensure they effectively penetrate the cutting zone.
Common strategies include:
- Flood Coolant Systems: Ideal for general cooling needs, although in titanium machining, this is often insufficient by itself.
- High-Pressure Coolants: Highly recommended, as they prevent heat buildup and help remove chips from the cutting zone, reducing the risk of workpiece distortion and tool wear.
5. CNC Machine and Tool Selection
Titanium machining requires rigid CNC machines with excellent vibration control. Titanium is sensitive to tool chatter, which can lead to poor surface finishes and part inaccuracies. CNC machines used for titanium machining need to have high torque at low speeds to handle the toughness of titanium without causing excessive vibrations. Additionally, CNC machines with adaptive control systems can dynamically adjust parameters based on real-time feedback, which is critical for maintaining precision in titanium machining.
Machinability of Steel
1. Machining Difficulty Based on Steel Type
Steel, despite being more easily machinable than titanium, presents a wide range of challenges depending on the type of steel used. For example:
- Carbon steel is relatively easy to machine and responds well to high-speed CNC processes.
- Stainless steel, however, is more difficult due to its higher toughness and tendency to work-harden, which can cause excessive tool wear.
- Tool steel and hardened steels are particularly difficult to machine because of their high hardness, often requiring specialized tools and cutting techniques.
Steel Type | Machinability Rating |
---|---|
Carbon Steel | High |
Stainless Steel | Moderate (due to work-hardening) |
Tool Steel | Low (due to hardness) |
2. Impact of Heat Treatment on Steel Machinability
One of the defining characteristics of steel is its ability to undergo heat treatment, which significantly impacts its machinability. Steel can be hardened to improve wear resistance or annealed to improve machinability.
- Annealed steel is easier to machine because the material is softer and more ductile, allowing for higher cutting speeds and feed rates.
- Hardened steel, on the other hand, is much more difficult to machine, requiring specialized tools like carbide or ceramic inserts to cut through the hard material.
Heat Treatment Type | Effect on Machinability |
---|---|
Annealing | Improves machinability |
Hardening | Reduces machinability, requires specialized tools |
3. Tool Life and Cutting Speeds
The tool life during steel machining varies significantly depending on the type of steel and the cutting conditions. Carbide tools are commonly used for machining steel due to their resistance to heat and wear, but even carbide tools can wear out quickly when machining hardened steel.
- For mild steel, cutting speeds of 100 to 200 m/min are typical.
- For stainless steel, cutting speeds drop to 50 to 90 m/min due to the material’s tendency to work-harden.
Steel Type | Recommended Cutting Speed |
---|---|
Mild Steel | 100-200 m/min |
Stainless Steel | 50-90 m/min |
Hardened Steel | 30-60 m/min |
Tool life can be extended by using appropriate cutting parameters and selecting tools with coatings like TiN (Titanium Nitride) or TiCN (Titanium Carbo-Nitride), which reduce wear and improve heat resistance.
4. Optimizing Cutting Parameters and Heat Dissipation
Unlike titanium, steel has higher thermal conductivity, which means it dissipates heat better during machining. However, heat dissipation becomes a challenge when machining high-alloy or stainless steels, where cutting tools can still overheat, leading to wear or breakage.
To optimize cutting parameters for steel:
- Higher cutting speeds and feed rates can be used for carbon steel.
- Moderate cutting speeds and slower feed rates should be used for stainless steel to prevent work-hardening.
In most steel machining applications, standard flood cooling or mist lubrication is sufficient to manage heat. However, for harder materials, high-pressure cooling or coolant-through tooling may be needed to extend tool life and maintain cutting precision.
5. CNC Machine and Tool Requirements
Steel machining requires CNC machines capable of handling the force and torque generated during the cutting process. Unlike titanium, steel can tolerate higher machining speeds, so machines with high spindle speeds are often preferred for working with carbon and mild steels.
For harder steels, rigid machines with high-torque, low-speed spindles are necessary to avoid vibrations and ensure smooth cutting. Tool selection also depends on the type of steel; for example, carbide or ceramic tools are necessary for machining hardened steel, while HSS (High-Speed Steel) tools may suffice for softer steels.
Comparison of Machinability: Titanium vs Steel
Property | Titanium | Steel |
---|---|---|
Cutting Speed | 30-60 m/min | 50-200 m/min |
Tool Wear | High (due to hardness and low conductivity) | Moderate to Low (depends on type) |
Thermal Conductivity | Low (heat builds up quickly) | High (better heat dissipation) |
Coolant Requirements | High-pressure coolant systems required | Standard coolant or mist lubrication suffices |
Tool Material | Carbide, diamond-coated | Carbide, HSS, or ceramic (for hardened steel) |
Machine Requirements | High rigidity, high torque at low speeds | High spindle speeds for softer steels |
Both titanium and steel pose unique challenges and opportunities in CNC machining. Titanium, with its hardness, low thermal conductivity, and poor machinability, requires careful optimization of cutting speeds, feed rates, and coolant strategies, along with the use of specialized tools. Steel, on the other hand, offers a wider range of machinability depending on the type and heat treatment, allowing for more flexibility in tooling and cutting parameters. By understanding the specific requirements and behaviors of each material, manufacturers can make informed decisions about machining strategies to optimize production efficiency and product quality.
Comparison of Material Costs and Machining Efficiency
When deciding between titanium and steel for CNC machining, both material cost and machining efficiency play crucial roles. While titanium and steel each offer unique advantages in terms of strength, weight, and durability, their costs—both in raw materials and processing—differ significantly. This section compares the costs and machining efficiency of titanium and steel, helping manufacturers make more informed decisions based on budget constraints and production requirements.
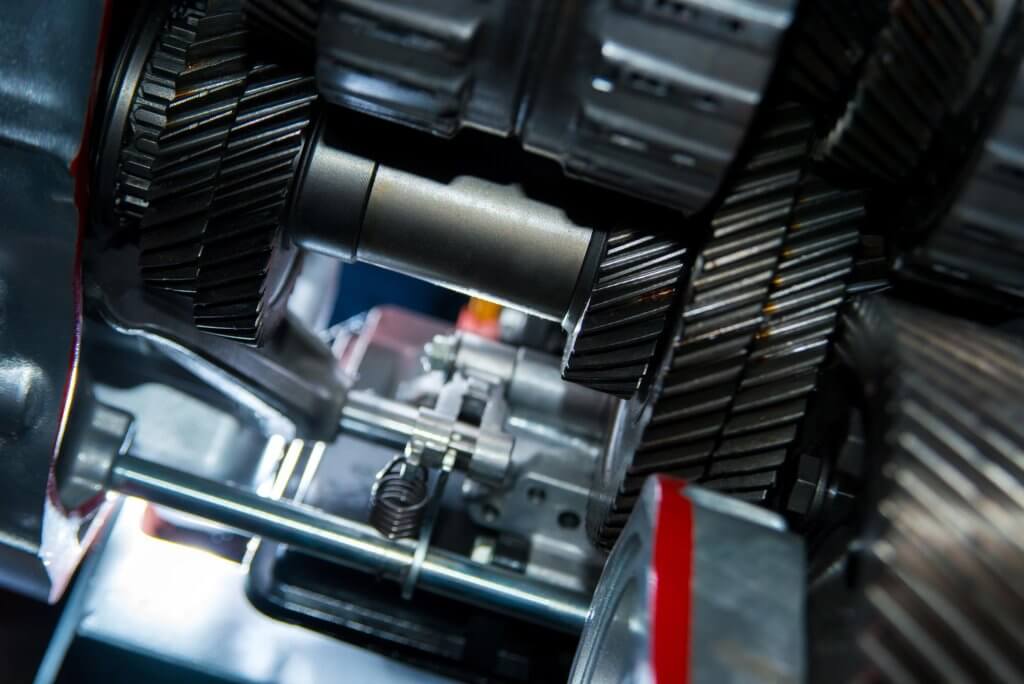
Cost of Titanium
1. High Raw Material Price
Titanium is known for its high raw material cost. The price of titanium is driven by several factors, including its complex extraction and refinement processes. Unlike steel, which is abundant and easy to refine, titanium requires a multi-step extraction process (usually from its ore, rutile or ilmenite) that is both energy-intensive and expensive.
Titanium’s raw material price fluctuates depending on global demand, production capacity, and market conditions. In general, titanium is four to ten times more expensive than common steel alloys.
Material | Average Cost per kg |
---|---|
Titanium | $35-50 USD |
Carbon Steel | $0.50-1.00 USD |
Stainless Steel | $3-5 USD |
2. High Machining Costs
In addition to the high cost of raw titanium, machining this material is significantly more expensive compared to steel due to the challenges it presents in the CNC process. The primary factors contributing to titanium’s higher machining costs are:
- Tool Life: Titanium’s high hardness and low thermal conductivity cause rapid tool wear. Machining titanium requires frequent tool replacements or specialized tools (such as carbide or diamond-coated tools), which are more costly and reduce machining efficiency.
- Longer Machining Time: Due to titanium’s properties, including its low thermal conductivity and tendency to gall or work-harden, it must be machined at slower speeds and with lower feed rates. This extends the overall machining time, leading to higher labor and machine operation costs. Titanium parts typically take two to four times longer to machine than similar steel parts.
- Coolant and Tooling Expenses: Since titanium tends to retain heat during the cutting process, additional cooling and lubrication are required, further driving up the costs.
Machining Factor | Effect on Titanium Machining Cost |
---|---|
Tool Wear | Frequent tool changes, costly tools |
Machining Time | Slower speeds, longer processing times |
Cooling Requirements | High-pressure cooling systems needed |
These factors combine to make the overall cost of machining titanium higher than that of steel. The high precision required for titanium machining, combined with its relatively poor machinability, often requires more advanced and expensive CNC equipment and highly skilled operators, further increasing production costs.
Cost of Steel
1. Lower Raw Material Price
Steel is much more affordable compared to titanium. As one of the most abundant metals on Earth, steel can be easily extracted and processed in large quantities, making it cost-effective. The price of steel, however, depends significantly on the specific type being used.
- Carbon Steel is the least expensive and most widely used type of steel. It is favored in industries like construction and automotive due to its low cost and versatility.
- Stainless Steel is more expensive than carbon steel due to the addition of chromium and nickel for corrosion resistance. However, even stainless steel is considerably cheaper than titanium, making it a cost-effective choice for applications that require corrosion resistance.
Type of Steel | Average Cost per kg |
---|---|
Carbon Steel | $0.50-1.00 USD |
Stainless Steel | $3-5 USD |
Tool Steel | $2-4 USD |
2. Machining Time and Efficiency
In terms of machining time, steel is much more efficient to work with compared to titanium. This efficiency varies by the type of steel used:
- Carbon Steel: This is the easiest type of steel to machine. It has good thermal conductivity and is relatively soft, allowing for higher cutting speeds and feed rates, which reduces overall machining time.
- Stainless Steel: While more difficult to machine than carbon steel, stainless steel is still easier to work with than titanium. It requires slower cutting speeds and more care to avoid work-hardening, but the machining time is still much shorter than that of titanium.
Additionally, steel’s better thermal conductivity means it dissipates heat more effectively, leading to lower tool wear and less need for high-pressure cooling systems. In most cases, standard flood coolant is sufficient when machining steel, reducing the overall cost.
Machining Factor | Effect on Steel Machining Cost |
---|---|
Tool Wear | Moderate, depending on steel type |
Machining Time | Faster than titanium |
Cooling Requirements | Standard cooling sufficient |
While tool steel and hardened steels may present more challenges in terms of tool wear and require more careful selection of cutting parameters, their machining costs are still typically lower than titanium, especially for large production runs.
Cost and Efficiency Comparison: Titanium vs Steel
The following table summarizes the cost and efficiency differences between titanium and steel, providing a side-by-side view of the key factors that influence material selection in CNC machining:
Factor | Titanium | Steel |
---|---|---|
Raw Material Cost | High ($35-50/kg) | Low to Moderate ($0.50-5/kg) |
Machining Time | Slow, 2-4x longer than steel | Fast, especially for carbon steel |
Tool Wear | High, frequent tool changes | Moderate, varies by steel type |
Cutting Speed | Slow (30-60 m/min) | Fast (50-200 m/min) |
Feed Rate | Low (0.1-0.3 mm/rev) | Moderate to High (0.3-0.7 mm/rev) |
Cooling Requirements | High-pressure coolant required | Standard coolant sufficient |
In summary, titanium’s higher raw material cost, combined with its challenging machinability, makes it an expensive option for CNC machining. The need for specialized tools, longer processing times, and additional cooling all contribute to increased production costs. However, for industries like aerospace, automotive, and medical, where weight reduction, strength, and corrosion resistance are critical, the investment in titanium can be justified.
Steel, by contrast, is far more cost-effective. Although some steel types, such as stainless steel or tool steel, may require more care during machining, the overall costs associated with steel—both in terms of raw materials and processing—are significantly lower than those for titanium. Steel remains the go-to choice for applications that demand strength, durability, and affordability in machining.
Comparison of Application Scenarios in CNC Machining
CNC machining has enabled the use of both titanium and steel in a wide variety of applications, but their specific properties dictate where and when each material is most advantageous. The choice between titanium and steel often depends on the requirements of the project, such as strength, weight, corrosion resistance, or cost-effectiveness. In this section, we’ll explore the typical applications of titanium and steel in CNC machining and compare scenarios where one material is preferred over the other.
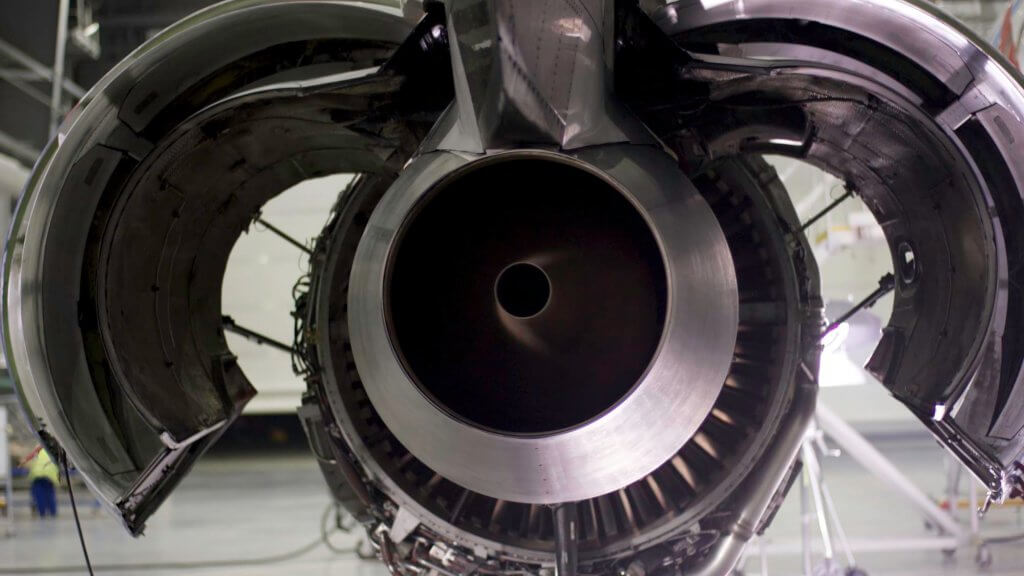
Typical Applications of Titanium
Titanium’s unique properties—high strength-to-weight ratio, corrosion resistance, and biocompatibility—make it ideal for high-performance industries where material performance is critical. Its applications are primarily found in demanding environments where failure is not an option.
1. Aerospace Industry
Titanium plays a critical role in the aerospace industry. Its high strength-to-weight ratio allows aircraft and spacecraft to be lighter, leading to improved fuel efficiency and higher payload capacity. Additionally, titanium’s corrosion resistance ensures longevity in harsh environments, such as exposure to jet fuel, seawater, or space conditions.
- Key components made from titanium include:
- Engine components (compressor blades, discs)
- Landing gear structures
- Airframe and structural parts
In aerospace applications, Ti-6Al-4V is the most commonly used alloy due to its balance of weight and strength. The use of titanium in these applications not only improves performance but also reduces operational costs over time through lower fuel consumption and extended component life.
2. Medical Devices (Titanium Implants)
Titanium is the go-to material for medical implants due to its biocompatibility. Since titanium is non-toxic and well-tolerated by the human body, it is widely used in medical devices and implants, where the material must integrate with human tissues without causing adverse reactions.
- Typical medical applications include:
- Joint replacements (hips, knees)
- Dental implants
- Pacemaker casings
In these applications, titanium’s corrosion resistance is essential, as implants are exposed to bodily fluids. Furthermore, titanium is lightweight and strong, making it perfect for long-term, load-bearing implants that reduce patient discomfort and allow for better recovery.
3. High-Performance Automotive Parts
In the automotive industry, particularly in high-performance and luxury vehicles, titanium is used in parts that require a combination of low weight and high strength. Titanium’s use in the automotive sector is primarily focused on reducing vehicle weight, which in turn improves acceleration, braking, and fuel efficiency.
- Automotive components made from titanium include:
- Exhaust systems
- Valve springs and connecting rods
- Suspension components
Although titanium is more expensive than steel, its application in high-end racing cars and luxury vehicles is justified by the performance benefits it offers. Reducing vehicle weight through titanium components can significantly enhance handling and overall performance.
Titanium Application | Industry | Components |
---|---|---|
Aerospace | Aerospace | Engine components, landing gear, airframes |
Medical | Medical Devices | Implants, pacemaker casings |
Automotive | Automotive | Exhaust systems, valve springs, suspensions |
Typical Applications of Steel
Steel’s versatility, strength, and cost-effectiveness make it indispensable across many industries. Unlike titanium, steel is more widely available and more affordable, allowing for large-scale use in construction, manufacturing, and heavy machinery.
1. Tool Manufacturing
Steel, particularly tool steel, is essential for manufacturing cutting tools, molds, and dies. Its hardness, wear resistance, and ability to retain a sharp cutting edge make it the ideal material for tools that shape, cut, or form other materials.
- Common applications include:
- Drill bits, saw blades, and cutting tools
- Injection molds and casting dies
- Punches and formers in industrial manufacturing
The use of tool steel allows for the precise and efficient shaping of parts in a variety of industries. Steel tools are durable, cost-effective, and capable of withstanding high mechanical stress, making them the standard in machining and manufacturing.
2. Construction and Heavy Machinery
In the construction industry, steel is a vital material for structural components due to its strength and affordability. Structural steel is used in everything from skyscrapers to bridges, providing the framework for some of the world’s most iconic structures. In addition, heavy machinery components are often made from steel due to its ability to withstand heavy loads and impact.
- Key steel applications in construction and machinery:
- Beams, girders, and columns in building construction
- Components for bulldozers, cranes, and excavators
- Piping systems, brackets, and fasteners
Steel’s ability to be heat-treated for enhanced strength makes it ideal for these applications, where both toughness and reliability are critical.
3. Structural Components in the Automotive Industry
In the automotive industry, steel continues to be the dominant material for structural components. Although aluminum and titanium are becoming more common in high-end or specialized vehicles, steel remains the primary material in mass production vehicles.
- Automotive steel components include:
- Car bodies and chassis
- Engine blocks and crankshafts
- Suspension systems and brackets
Steel’s high strength and relatively low cost make it ideal for mass production in the automotive industry. In applications where weight is not the primary concern, steel offers an excellent balance of strength, durability, and affordability.
Steel Application | Industry | Components |
---|---|---|
Tool Manufacturing | Manufacturing | Cutting tools, molds, dies |
Construction & Machinery | Construction | Beams, heavy machinery parts, piping systems |
Automotive | Automotive | Car bodies, engine blocks, suspension systems |
When to Choose Titanium vs. Steel
Choosing between titanium and steel depends on several factors, including the weight requirements, corrosion resistance, strength, and cost of the application. Both materials offer distinct advantages depending on the performance demands.
When to Choose Titanium
- Lightweight and Strength: When weight reduction is a key factor, such as in aerospace or high-performance automotive applications, titanium is preferred. Its strength-to-weight ratio is far superior to steel, allowing for lighter components without sacrificing strength.
- Corrosion Resistance: Titanium’s excellent resistance to corrosion makes it ideal for marine, chemical, and medical applications. When the material is exposed to harsh environments, such as saltwater or bodily fluids, titanium offers unmatched durability and longevity.
- High Temperatures: Titanium retains its strength at high temperatures, making it suitable for components that experience extreme heat, such as in jet engines or spacecraft.
When to Choose Steel
- Cost Efficiency: In applications where budget constraints are critical, steel is the more cost-effective option. Its lower raw material and machining costs make it the preferred choice in mass production, construction, and manufacturing.
- Structural Integrity: For heavy-duty applications, such as in construction or machinery, steel offers greater availability and the ability to handle heavy loads and impacts. Its hardness and toughness make it ideal for tools, industrial components, and building materials.
- Machinability: Steel is easier to machine than titanium, especially in large-scale manufacturing processes. For components that require high production volumes with minimal tooling costs, steel is a more practical choice.
Scenario | Choose Titanium | Choose Steel |
---|---|---|
Weight Reduction | Aerospace, high-performance automotive | Not as critical in large structures or machinery |
Corrosion Resistance | Marine environments, medical implants | Industrial, lower exposure to corrosives |
High-Temperature Resistance | Aerospace, high-temperature applications | Less critical in most automotive and construction |
Cost Efficiency | Luxury items, specialized industries | Mass production, construction, tools |
The choice between titanium and steel in CNC machining ultimately comes down to the specific needs of the application. Titanium excels in industries that demand high-performance, lightweight, and corrosion-resistant materials, such as aerospace, medical, and high-performance automotive parts. On the other hand, steel is widely used due to its affordability, strength, and ease of machining, making it ideal for mass production, construction, and industrial tooling.
Comparison of Machining Considerations
When working with titanium and steel in CNC machining, it’s essential to understand the specific challenges each material presents. While both materials are widely used in industrial applications, their machining characteristics differ significantly. We’ll examine the primary machining challenges for both titanium and steel, explore why they occur, and provide strategies for overcoming them.
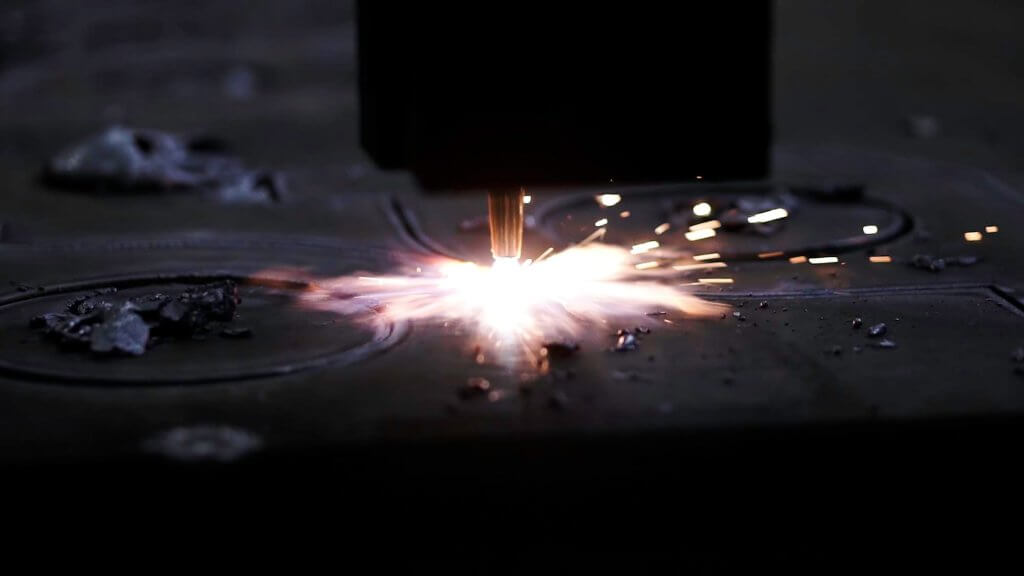
Titanium Machining Challenges
Titanium is widely regarded as a difficult material to machine due to its unique properties. While its strength and corrosion resistance make it valuable for aerospace, medical, and high-performance applications, these same properties present several challenges during CNC machining.
1. Heat Dissipation
One of the most significant issues when machining titanium is its low thermal conductivity. Unlike steel, titanium does not dissipate heat efficiently, which means that the heat generated during cutting tends to concentrate at the tool-workpiece interface. This can result in:
- Tool overheating: Excessive heat can lead to rapid tool wear and failure.
- Workpiece damage: Prolonged heat exposure can cause workpiece deformation, reduced surface quality, and even material cracking.
Titanium’s Heat Dissipation Issues | Effects |
---|---|
Low thermal conductivity | Heat concentration at tool interface |
Excessive heat buildup | Tool wear, workpiece deformation |
2. Tool Wear
Titanium’s hardness, combined with its low heat dissipation, leads to rapid tool wear. As the cutting tool comes into contact with titanium, the heat generated accelerates the breakdown of the tool’s cutting edge, causing premature failure. Additionally, titanium tends to chemically react with certain tool materials at high temperatures, further reducing tool life.
To overcome this challenge, machinists typically use carbide tools or diamond-coated tools, which are more resistant to wear and can handle the extreme conditions of titanium machining. Regular tool changes and optimized tool path strategies are essential for maintaining cutting precision and extending tool life.
3. Springback (Material Elasticity)
Titanium exhibits significant springback due to its high elasticity. During machining, especially when turning or bending operations are involved, the material tends to return slightly to its original shape after being deformed. This can lead to:
- Dimensional inaccuracies: Springback can cause parts to deviate from their intended dimensions, leading to a need for rework or part rejection.
- Reduced machining precision: The elasticity complicates achieving tight tolerances, especially in precision components.
Titanium Springback Issues | Effects |
---|---|
High elasticity | Dimensional inaccuracies, tolerance issues |
Springback after cutting | Potential part deformation |
Overcoming Titanium’s Machining Challenges
To mitigate these challenges, several strategies can be employed:
- Use of Coolants: High-pressure coolant systems are critical in titanium machining to reduce heat buildup. The coolant helps to remove heat from the cutting zone, minimizing the risk of tool wear and improving surface finish.
- Optimized Cutting Parameters: Slower cutting speeds and lower feed rates can help reduce heat generation during machining. Typically, cutting speeds for titanium range between 30 and 60 meters per minute, with feed rates kept at 0.1 to 0.3 mm per revolution to balance tool life and machining time.
- Advanced Tooling: The use of carbide, polycrystalline diamond (PCD), or ceramic tools helps mitigate wear caused by titanium’s hardness and chemical reactivity. These tools can withstand the extreme conditions generated during titanium machining.
Machining Strategy | How It Helps |
---|---|
High-pressure coolant systems | Reduces heat buildup, improves tool life |
Optimized cutting parameters | Minimizes heat, balances tool wear and time |
Advanced tooling (carbide, PCD) | Withstands high heat, extends tool life |
Steel Machining Challenges
Steel, particularly hardened or stainless steel, also presents unique challenges in CNC machining. While it’s generally more machinable than titanium, specific issues such as deformation and work-hardening must be addressed to achieve consistent and precise results.
1. Post-Machining Deformation
Steel, especially when machined in thin sections or high-stress applications, can experience post-machining deformation. This is due to internal stresses being released during the machining process. As these stresses relax, they can cause parts to bend, warp, or shift out of tolerance.
Steel Post-Machining Deformation | Effects |
---|---|
Internal stresses released during machining | Warping, bending, dimensional inaccuracies |
Thin sections or high-stress parts | Greater risk of deformation |
To avoid these issues, it’s crucial to:
- Use stress-relieved steel: Steel that has undergone stress relief through heat treatment is less likely to deform during machining.
- Strategic clamping and support: Ensuring that parts are securely clamped and supported during machining can reduce the risk of deformation, especially in thin or complex parts.
2. Work-Hardening
Certain types of steel, particularly stainless steel, are prone to work-hardening. This occurs when the material hardens at the cutting surface due to the heat and mechanical stress applied during machining. Once the steel work-hardens, it becomes significantly more difficult to cut, leading to:
- Increased tool wear: Work-hardened surfaces are harder and more abrasive, causing rapid tool degradation.
- Poor surface finish: Work-hardening can lead to surface roughness and poor-quality finishes if not managed correctly.
Steel Work-Hardening | Effects |
---|---|
Surface hardens during cutting | Increased tool wear, reduced machinability |
Heat and mechanical stress | Poor surface finish, dimensional inaccuracies |
3. Heat Treatment Effects on CNC Machining
Heat treatment plays a critical role in the machinability of steel. Annealed steel is generally easier to machine because it’s softer and more ductile, allowing for higher cutting speeds and feed rates. On the other hand, hardened steel can be extremely difficult to machine, requiring specialized tools and techniques to avoid excessive tool wear and achieve a smooth surface finish.
Heat Treatment Type | Machinability Impact |
---|---|
Annealed steel | Softer, easier to machine |
Hardened steel | Harder, requires special tools and slower speeds |
Overcoming Steel’s Machining Challenges
Several strategies can be used to mitigate the challenges of machining steel:
- Optimized Cutting Parameters: Higher cutting speeds and feed rates can be used when machining annealed or mild steels. However, for work-hardened or high-carbon steels, slower speeds and more careful cutting are necessary to avoid tool damage and ensure a good surface finish.
- Specialized Tooling: Using carbide tools or tools with special coatings (e.g., TiN or TiCN) can help manage the wear associated with machining hardened steels. These tools offer better heat resistance and wear properties, prolonging tool life.
- Proper Heat Treatment: To reduce post-machining deformation and make the steel easier to work with, it’s advisable to machine steel in its annealed state and perform final hardening after the machining process, when feasible.
Machining Strategy | How It Helps |
---|---|
Optimized cutting parameters | Balances tool life and surface finish |
Specialized tooling (carbide, TiN) | Reduces tool wear, handles hard steels |
Machining before final heat treatment | Reduces deformation, easier machining |
Titanium vs. Steel Machining Comparison
Challenge | Titanium | Steel |
---|---|---|
Heat Dissipation | Low, leads to heat concentration | Moderate, better heat dissipation |
Tool Wear | High, requires frequent tool changes | Moderate to high, depending on steel type |
Material Elasticity | High, springback can affect dimensions | Low, generally holds its shape |
Work-Hardening | Not common | Common in stainless and some alloy steels |
Post-Machining Deformation | Less prone | Can occur, especially in thin sections |
Heat Treatment Effects | No significant change | Softens annealed steel, hardens tool steel |
Machining titanium and steel both come with their own sets of challenges, but understanding these difficulties allows machinists to make informed decisions about tooling, cooling, and cutting strategies. Titanium’s primary difficulties arise from its heat retention, tool wear, and material elasticity, while steel presents challenges related to deformation, work-hardening, and the effects of heat treatment. With the right techniques—such as optimized cutting parameters, advanced tooling, and stress-relief processes—many of these challenges can be overcome, resulting in high-quality, precision-machined parts for a variety of industries.
Comparison of Surface Finishes and Durability
Surface finishes plays a crucial role in enhancing the durability, appearance, and performance of materials in CNC machining, particularly for titanium and steel. While both materials are renowned for their strength, their surface treatments can dramatically affect properties such as corrosion resistance, wear resistance, and overall durability. This section delves into the different surface treatments used for titanium and steel and how these treatments influence their longevity and resistance to environmental factors.
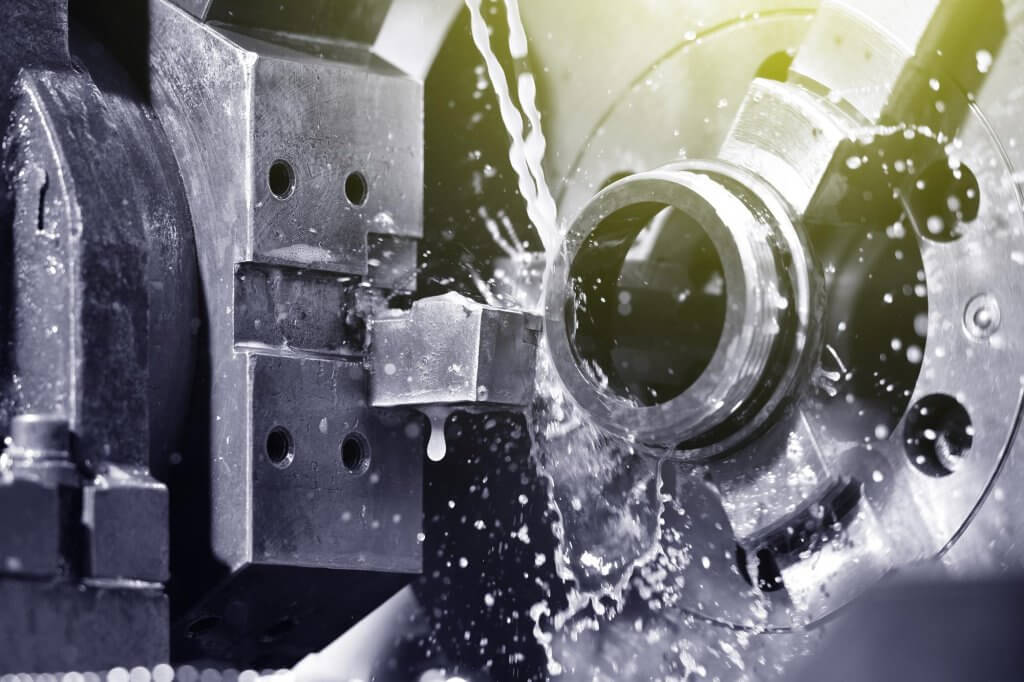
Surface Finishes for Titanium
Titanium’s natural properties provide it with a significant degree of corrosion resistance, but additional surface treatments can further enhance its performance and aesthetic qualities. Common surface treatments for titanium include anodizing, sandblasting, and polishing.
1. Anodizing
Anodizing is one of the most common surface treatments applied to titanium. During the anodizing process, an electrochemical reaction is used to create an oxide layer on the surface of the titanium part. This oxide layer offers several benefits:
- Corrosion resistance: The anodized layer enhances the already excellent corrosion resistance of titanium, making it even more resilient to harsh environmental conditions, including exposure to saltwater and chemicals.
- Aesthetic appeal: Anodizing can produce a range of colors on titanium surfaces, making it a popular choice for decorative purposes or to visually differentiate parts.
- Wear resistance: The oxide layer provides a harder surface that can withstand wear and mechanical stress better than untreated titanium.
Surface Treatment | Effect on Durability |
---|---|
Anodizing | Improves corrosion resistance and wear |
Oxide layer | Hardens surface, enhances aesthetic appeal |
2. Sandblasting
Sandblasting is a mechanical surface treatment used to clean and texturize titanium surfaces. In this process, fine particles of sand or other abrasive materials are blasted onto the surface at high speed, removing contaminants and providing a matte finish.
- Improved bonding: Sandblasting creates a rougher surface, which is beneficial when bonding or coating is required, as it increases the surface area for adhesion.
- Surface hardness: Although it doesn’t significantly improve wear resistance, sandblasting helps remove surface imperfections and can slightly improve surface hardness by compressing the material.
3. Polishing
Polishing titanium provides a smooth and reflective finish. It is often used for applications where appearance and minimal surface friction are essential, such as in medical or aerospace components.
- Reduced friction: A polished surface reduces friction, making it ideal for parts that are subject to sliding or contact with other materials.
- Enhanced aesthetics: Polished titanium has a sleek, reflective appearance, making it desirable for luxury or aesthetic-driven products.
Surface Treatment | Effect on Durability |
---|---|
Sandblasting | Improves adhesion for coatings, slight surface hardening |
Polishing | Reduces friction, enhances appearance |
Impact of Surface Treatments on Titanium’s Durability
The surface treatments applied to titanium play a significant role in its overall durability, particularly in terms of enhancing corrosion resistance and wear resistance. While titanium is naturally resistant to rust and corrosion, anodizing provides additional protection, making it ideal for marine environments and chemical processing industries. Sandblasting and polishing, while more focused on aesthetic and mechanical properties, still contribute to the longevity of the material by refining the surface and reducing the likelihood of wear or damage.
Surface Treatments for Steel
Steel requires a wide variety of surface treatments to protect it from corrosion, enhance its wear resistance, and improve its overall durability. Common surface treatments for steel include plating, coating, and post-heat-treatment processes.
1. Electroplating
Electroplating involves coating the surface of steel with a thin layer of another metal, such as chromium, zinc, or nickel, using an electrochemical process. Electroplating serves several purposes:
- Corrosion resistance: A plated layer of zinc (galvanizing) or chromium can protect steel from rust and oxidation. Zinc is commonly used in construction materials to protect against atmospheric corrosion.
- Enhanced wear resistance: Hard chrome plating increases the hardness and wear resistance of steel, making it more suitable for parts subject to high friction or impact.
Surface Treatment | Effect on Durability |
---|---|
Electroplating (zinc) | Protects against corrosion, especially in outdoor environments |
Electroplating (chrome) | Increases surface hardness and wear resistance |
2. Coatings
Steel is often coated with various materials, including powder coatings, ceramic coatings, and polymer-based coatings. These coatings provide an additional protective barrier against environmental factors and wear.
- Powder coating: This process applies a dry powder to the steel surface, which is then heated to form a durable protective layer. Powder coating is often used for steel components exposed to weather, such as in outdoor structures or automotive parts.
- Ceramic coatings: These coatings are ideal for high-temperature applications, such as in engines or exhaust systems, as they protect against both heat and corrosion.
Surface Treatment | Effect on Durability |
---|---|
Powder coating | Protects against weather and wear |
Ceramic coating | Provides heat resistance, protects against high temperatures |
3. Post-Heat Treatment Processes
After heat treatment, steel often undergoes post-processing treatments such as quenching and tempering. These processes are designed to enhance steel’s mechanical properties:
- Tempering: Following the hardening process, tempering helps reduce the brittleness of steel and improves its toughness. This is especially important for tools or components subject to impact.
- Surface hardening: Techniques like case hardening or carburizing increase the surface hardness of steel, making it more resistant to wear while maintaining a tough and ductile core.
Surface Treatment | Effect on Durability |
---|---|
Tempering | Reduces brittleness, improves toughness |
Case hardening | Hardens the surface, increases wear resistance |
Impact of Surface Treatments on Steel’s Durability
Steel benefits significantly from a range of surface treatments designed to enhance its corrosion resistance, wear resistance, and mechanical properties. Electroplating with zinc or chromium provides essential protection against rust, particularly in outdoor or industrial environments. Post-heat treatment processes such as tempering or case hardening significantly improve impact resistance and surface wear, making steel more durable for heavy-duty applications.
Comparison of Surface Treatment and Durability: Titanium vs. Steel
Factor | Titanium | Steel |
---|---|---|
Corrosion Resistance | Naturally corrosion-resistant, enhanced by anodizing | Requires electroplating (zinc, chrome) or coatings for corrosion protection |
Wear Resistance | Improved through anodizing, limited by polishing | Enhanced by chrome plating, surface hardening, and post-heat treatments |
Surface Hardening | Minimal improvements via sandblasting | Significant improvements via case hardening and carburizing |
Heat Resistance | Good, polished and ceramic coatings enhance | Ceramic coatings for heat resistance in high-temperature applications |
Aesthetic Appeal | Enhanced by anodizing, polishing | Powder coating, chrome plating for aesthetic and protective purposes |
Surface treatments are essential for maximizing the performance and durability of both titanium and steel. Titanium, with its natural corrosion resistance, benefits primarily from anodizing, which enhances both its appearance and wear resistance. Sandblasting and polishing also contribute to the overall quality and longevity of titanium components. Steel, on the other hand, requires more extensive surface treatments to combat corrosion and wear. Electroplating, coatings, and heat treatments all play a critical role in improving steel’s durability, particularly in demanding environments. Understanding the appropriate surface treatments for each material ensures that components not only meet the required mechanical specifications but also remain durable and reliable in their intended applications.
Is Titanium or Steel the Better Choice in CNC Machining?
When it comes to CNC machining, choosing between titanium and steel is not always straightforward. Both materials have unique properties that make them valuable in different applications. However, the decision often comes down to how well each material meets specific project requirements, balancing performance characteristics with cost-effectiveness.
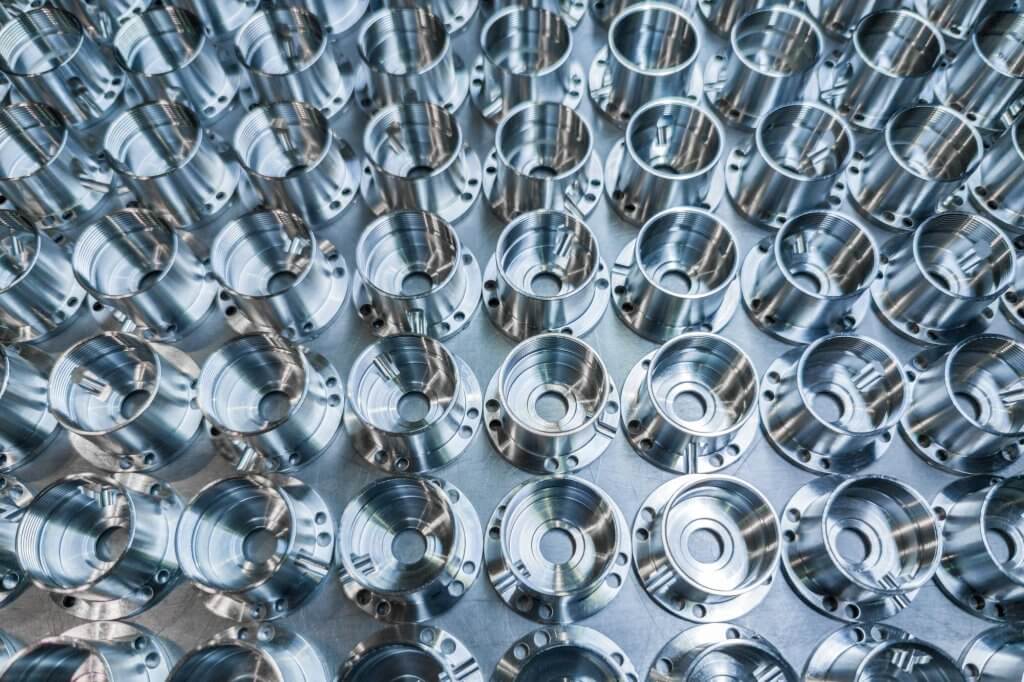
Titanium vs. Steel: Performance in CNC Machining
Titanium is prized for its exceptional strength-to-weight ratio, corrosion resistance, and biocompatibility, which make it a go-to choice for industries like aerospace, medical devices, and high-performance automotive parts. In CNC machining, titanium excels where weight reduction and extreme durability are crucial. Its ability to withstand high temperatures and resist corrosion in harsh environments further enhances its value in challenging applications, such as aircraft components or medical implants.
However, titanium’s benefits come with challenges. It is notoriously difficult to machine due to its low thermal conductivity, which causes heat to concentrate at the cutting interface, leading to tool wear and potential workpiece deformation. Additionally, the cost of titanium—both in terms of raw materials and machining time—tends to be much higher than steel. Specialized tools and techniques are often required, which can make machining titanium a more time-consuming and costly process.
On the other hand, steel is known for its versatility and cost-effectiveness. It comes in a wide range of alloys, from carbon steel to stainless and tool steel, allowing manufacturers to select the right type for their needs. Steel’s ease of machining, especially in its annealed form, makes it the preferred material in industries like construction, automotive, and heavy machinery. While it may not offer the same weight advantages as titanium, steel’s strength, durability, and affordability make it the default choice for many applications.
Steel does have its own challenges, particularly with post-machining deformation and work-hardening in certain alloys like stainless steel. However, these issues can often be mitigated through proper heat treatment, such as tempering or surface hardening, to enhance the steel’s toughness and wear resistance.
Choosing the Right Material: Application Needs vs. Cost Efficiency
When deciding between titanium and steel, it’s essential to consider the application’s specific requirements alongside the overall project budget.
- Weight and Strength: If reducing weight while maintaining strength is critical, such as in aerospace or high-performance automotive applications, titanium is the better choice. Its superior strength-to-weight ratio and resistance to corrosion give it an edge where these factors are prioritized.
- Corrosion Resistance: For applications that involve exposure to corrosive environments, like marine or chemical processing industries, titanium’s natural corrosion resistance makes it ideal. Steel can be treated with coatings or electroplating to improve its corrosion resistance, but it may not match the longevity of titanium in extreme environments.
- Cost Efficiency: If budget constraints are a major concern, steel is usually the more cost-effective option. It’s easier to machine, readily available, and can be heat-treated to improve its mechanical properties for demanding applications. This makes it suitable for mass-produced items, construction materials, and tools.
- Tooling and Machinability: Titanium demands specialized tooling, often carbide or diamond-coated, and requires more careful control over cutting speeds and feed rates to avoid excessive heat and wear. For applications that need high production volumes or fast turnaround times, steel’s easier machinability gives it a clear advantage.
- Durability and Wear Resistance: In high-wear applications, steel, especially when heat-treated or hardened, can offer superior wear resistance. This makes it an excellent choice for industrial tools, heavy machinery, and structural components that require long-term durability under stress.
Conclusion
In the end, choosing between titanium and steel in CNC machining boils down to understanding the balance between performance and cost. Titanium’s strength, corrosion resistance, and lightweight properties make it ideal for high-performance, low-weight applications, but it comes with higher material and machining costs. Steel, on the other hand, offers a more cost-effective and versatile option, particularly for mass production and applications where weight is not a primary concern.
Manufacturers should carefully assess their project’s requirements—whether it’s strength, weight, corrosion resistance, or budget—and choose the material that aligns best with their goals. In many cases, steel remains the default for its balance of durability and affordability, while titanium shines in industries that demand cutting-edge performance despite its higher cost.
Other Articles You Might Enjoy
- Is Titanium Stronger Than Steel Unveiling the Power of Titanium in CNC Machining
In the field of CNC machining, material selection is critical for determining product quality, durability, and cost-effectiveness. For procurement specialists and engineers alike, the question often arises: Is titanium stronger…
- CNC Machining in the Watchmaking Industry: Stainless Steel vs. Titanium Cases
CNC Machining and its Role in the Watchmaking Industry In the world of horology, CNC machining has proven itself to be an invaluable tool. This modern method allows custom parts…
- Leveraging CNC Machining for Medical Devices: Titanium vs. Stainless Steel Materials
CNC Machining in Medical Device Manufacturing: An Introduction Computer Numerical Control (CNC) machining is a critical practice within the field of medical device manufacturing. This advanced technology allows for precision-engineering,…
- The Efficiency of CNC Machining: Titanium vs. Steel for High-Performance Components
Introduction to CNC Machining and Material Selection Computer Numerical Control (CNC) machining revolutionizes the manufacturing space by enabling highly accurate, repeatable, and complex component production. In high-performance industries like aerospace…
- Zirconium vs. Titanium: A CNC Machining Material Showdown
Introduction to CNC Machining and Materials CNC machining, short for Computer Numerical Control machining, serves as a critical component in contemporary manufacturing processes. This computer-aided method builds components by removing…
- Mastering Material Removal Rates: Key to Success in China's CNC Titanium Machining
Introduction to CNC Titanium Machining in China The realm of CNC (Computer Numerical Control) machining in China has seen remarkable growth over the years, particularly in the domain of titanium…