What is a Lathe and Why is it Important?
What is a Lathe?
A lathe is one of the oldest and most versatile machine tools used in manufacturing and production processes. It operates by rotating a workpiece on its axis while various tools are applied to shape, cut, sand, drill, or otherwise modify the material. The workpiece, often cylindrical, rotates while stationary cutting tools move along predefined paths to create the desired shape.
Historically, the lathe has been a cornerstone of precision manufacturing, dating back to ancient civilizations. Early forms of lathes were manually operated and rudimentary, but the basic concept of using rotation for material shaping has remained consistent throughout centuries of technological advancement.
The modern lathe, especially CNC (Computer Numerical Control) lathes, has revolutionized the way industries handle complex machining tasks. It combines automation with precision, allowing manufacturers to produce parts with exceptional accuracy and efficiency.
Why is a Lathe Important?
The importance of the lathe in the world of manufacturing cannot be overstated. It serves as a fundamental tool for creating parts that are integral to industries such as aerospace, automotive, medical devices, and more. Lathes are not just limited to metalworking but are also used in woodturning, plastic machining, and other applications, making them an essential tool across diverse sectors.
Here are some reasons why the lathe holds such critical importance:
- Versatility: Lathes can perform a wide range of operations, including turning, facing, drilling, boring, threading, and knurling. This versatility allows them to produce everything from simple cylindrical objects to complex parts with intricate details.
- Precision: Modern lathes, especially CNC lathes, can produce parts with micrometer-level precision. This level of accuracy is essential for industries where even the smallest deviation can result in failure, such as in aerospace or medical device manufacturing.
- Efficiency: Lathes streamline production processes by combining various machining operations into one workflow. Automated CNC lathes further enhance this by reducing manual intervention, allowing manufacturers to produce large quantities of parts with minimal downtime.
- Customizability: Lathes can be easily adapted with different attachments, tools, and settings to meet the needs of specific projects. For instance, adding a milling attachment transforms the lathe into a hybrid machine capable of both turning and milling, significantly expanding its capabilities.
- Critical for Prototyping: In product development and prototyping, lathes are often used to create precise models of parts. Their flexibility allows designers and engineers to quickly iterate on designs, producing functional prototypes for testing and validation before moving to mass production.
- Widespread Industrial Application: Lathes are used in virtually every manufacturing industry. Automotive companies rely on them to produce engine components, transmission parts, and shafts. The aerospace industry uses them to craft turbine blades, landing gear components, and other critical parts. Even the medical field uses lathes to produce implants, surgical tools, and other precision devices.
The Evolution of the Lathe
The lathe has undergone significant transformation since its inception. Ancient Egyptians are credited with creating the first recorded lathe, a simple two-person mechanism where one person rotated the workpiece while the other operated the cutting tool. The Romans later enhanced this design by adding a turning bow.
In the 18th century, the advent of the mechanical lathe marked a turning point in manufacturing. The incorporation of a foot pedal to drive the rotation and the addition of gears and pulleys allowed for greater control over the machining process. The Industrial Revolution then paved the way for even more sophisticated lathes, introducing steam power and, eventually, electric motors to drive the machines.
The most revolutionary development in lathe technology came with the introduction of CNC machines in the mid-20th century. CNC lathes replaced manual control with computer programming, allowing for automation and repeatability in machining tasks. Today’s CNC lathes can operate autonomously, following complex toolpaths and producing parts with minimal human intervention. This shift has drastically improved production speeds, reduced human error, and allowed manufacturers to take on increasingly complex projects.
Types of Lathes
There are many types of lathes, each designed for specific tasks. Here’s a breakdown of some common types:
- Engine Lathe: This is the most common type of lathe found in general-purpose machining. It can handle a wide variety of tasks, making it a go-to machine in many workshops.
- Turret Lathe: In a turret lathe, tools are mounted on a rotating turret, allowing multiple cutting operations to be performed in sequence without the need for manual tool changes. This design improves efficiency in high-volume production.
- CNC Lathe: CNC (Computer Numerical Control) lathes are programmed using a computer to carry out precise operations. They can work continuously, making them highly efficient for mass production.
- Vertical Lathe: Also known as a vertical boring mill, this lathe is used for large, heavy workpieces that need to be supported from below. Its vertical design allows gravity to assist in stabilizing the workpiece.
- Wood Lathe: Designed specifically for woodturning, these lathes are simpler in construction than metal lathes and often used by craftsmen and hobbyists to create bowls, furniture parts, and decorative objects.
- Toolroom Lathe: This is a high-precision lathe used in tool and die making. It is known for its accuracy and smooth operation, making it ideal for tasks requiring fine tolerances.
- Capstan and Turret Lathe: These are semi-automatic lathes designed for repetitive production of small and medium-sized parts. The turret holds multiple tools, allowing for quick tool changes and reducing production time.
- Special Purpose Lathes: These include lathes designed for very specific tasks, such as watchmaking, optical machining, or the production of intricate parts in the electronics industry.
Key Innovations in Lathe Design
The history of lathe design is marked by a series of important innovations that have enhanced the machine’s capabilities and expanded its range of applications. Some of these key innovations include:
- CNC Control: The introduction of CNC technology was perhaps the most significant innovation in lathe history. By allowing machines to be controlled via computer programs, CNC technology has vastly increased the precision, repeatability, and efficiency of lathe machining.
- Power Turrets: Power turrets allow multiple tools to be mounted on a rotating platform, enabling the lathe to switch between cutting tools without manual intervention. This dramatically speeds up production, particularly for parts requiring multiple operations.
- Live Tooling: Live tooling allows CNC lathes to perform milling, drilling, and tapping operations in addition to turning. This multifunctionality reduces the need for additional machines, making production more streamlined.
- Tailstock Quill Automation: In traditional lathes, the tailstock quill had to be manually operated, but modern designs often include automation. This enables more consistent pressure and better results, particularly in high-precision applications.
Impact of the Lathe on Modern Manufacturing
The lathe’s impact on modern manufacturing is profound. It forms the backbone of many production lines, shaping raw materials into usable components that serve as the building blocks of everything from automobiles to airplanes to medical devices. In industries where precision and reliability are paramount, the lathe’s role is indispensable.
In fact, many manufacturing advancements can be directly attributed to improvements in lathe technology. The ability to create precision parts with tight tolerances has allowed engineers to push the boundaries of design and innovation. Industries such as aerospace and defense, where components must meet stringent safety and performance standards, rely heavily on lathe technology to deliver parts that meet exacting specifications.
Moreover, the automation and flexibility of modern lathes have paved the way for the rise of smart manufacturing and Industry 4.0. CNC lathes can now be integrated into automated production lines, communicating with other machines and systems to optimize workflow and minimize downtime. This integration allows manufacturers to produce more complex and customized products while reducing lead times and costs.
The Future of Lathe Technology
Looking forward, the lathe will continue to evolve in tandem with advances in automation, artificial intelligence, and material science. The next generation of lathes may feature enhanced AI-driven capabilities, allowing machines to learn and adapt to new tasks autonomously. This will further reduce the need for human intervention and enable even greater levels of precision and efficiency.
Furthermore, as new materials such as composites, advanced alloys, and 3D-printed materials become more commonplace, lathes will be adapted to work with these materials. The ability to machine a broader range of materials will open up new possibilities in product design and manufacturing.
In summary, the lathe is a cornerstone of modern manufacturing, providing unparalleled versatility, precision, and efficiency. Its evolution from a manually operated tool to a fully automated CNC machine represents the broader shift towards automation and innovation in industry. As new technologies and materials emerge, the lathe will undoubtedly continue to play a central role in shaping the future of manufacturing.
How Does a Lathe Work?
A lathe operates on a relatively simple principle that revolves around rotating a workpiece while a fixed or moving tool cuts or shapes the material. This concept, though basic, is integral to its function and is adapted to perform highly complex machining tasks across various industries. To understand how a lathe works, it’s essential to break down its operations, key components, and the types of movements involved in machining. In this chapter, we will explore the inner workings of a lathe, how it performs different operations, and how CNC technology has transformed traditional lathe operation.
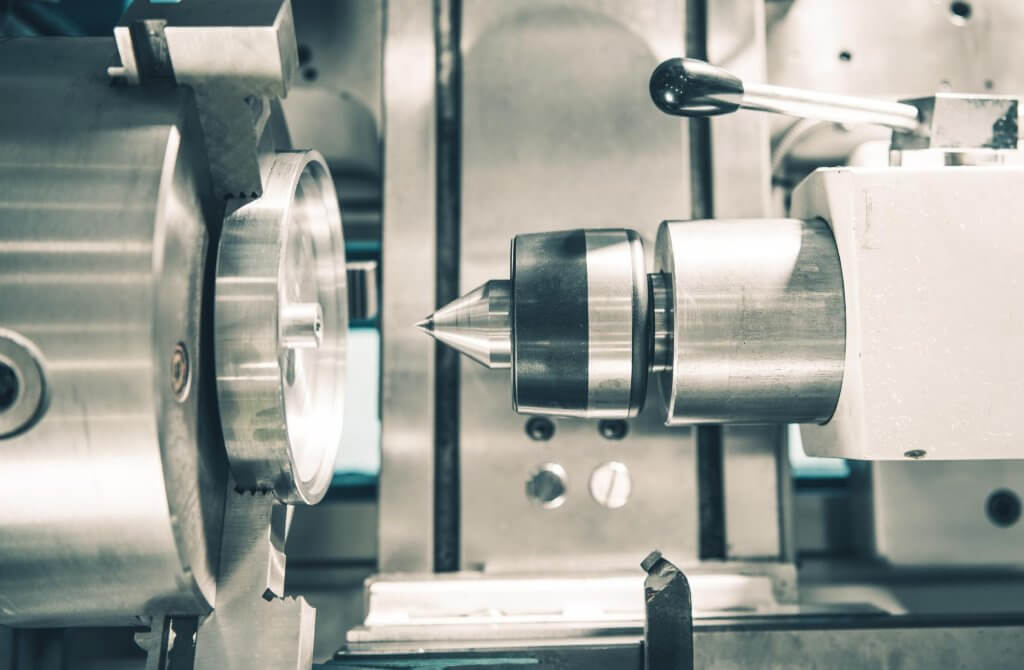
The Basic Working Principle of a Lathe
At its core, a lathe operates by rotating the workpiece on its central axis while applying a cutting tool to remove material and shape the object. The process begins by securely holding the workpiece in place, usually in a chuck or between centers, and rotating it at varying speeds depending on the material and the desired finish.
The cutting tool is either fixed in position or moves along specific paths to remove material. The lathe’s ability to precisely control the position of the tool and the speed of rotation is what allows it to produce accurate and consistent parts.
Here’s a simplified breakdown of the lathe operation:
- Workpiece Rotation: The workpiece rotates at high speeds around a fixed axis. Depending on the material, rotation speeds can range from several hundred to thousands of RPM (revolutions per minute).
- Tool Movement: The cutting tool is held in a carriage or tool post that can move in two directions: longitudinally (parallel to the workpiece’s axis) and transversely (perpendicular to the axis). This movement allows the tool to cut material as the workpiece spins.
- Material Removal: The cutting tool, usually made of carbide or high-speed steel, removes material from the workpiece to shape it into the desired form. The depth and speed of the cut determine the rate of material removal and surface finish.
- Spindle Speed: The lathe’s spindle controls the rotational speed of the workpiece. By adjusting the spindle speed, the operator can optimize the machining process for different materials and cutting conditions.
- Feed Rate: The feed rate refers to the speed at which the cutting tool moves along the workpiece. This rate affects the smoothness of the finished part and the overall machining time.
Key Components of a Lathe and Their Roles in Operation
To fully understand how a lathe works, it’s crucial to familiarize yourself with its key components and their roles in the machining process. Each part of the lathe has a specific function that contributes to the overall operation:
- Headstock: The headstock is located at the left end of the lathe and houses the spindle, gears, and motor that drive the rotation of the workpiece. It is responsible for controlling the speed and torque applied to the workpiece.
- Tailstock: Positioned opposite the headstock, the tailstock is used to support the other end of the workpiece, particularly for longer pieces that may bend or flex during machining. The tailstock can hold accessories such as a drill chuck or center, depending on the operation.
- Spindle: The spindle is a rotating shaft in the headstock that holds and rotates the workpiece. The workpiece is typically attached to the spindle via a chuck or faceplate.
- Chuck: The chuck is a clamping device that holds the workpiece securely in place. It typically has jaws that can be adjusted to accommodate various workpiece sizes.
- Bed: The bed is the foundation of the lathe and supports all the components. It provides stability during machining and ensures the carriage and tool post can move smoothly along the workpiece.
- Carriage: The carriage moves along the bed and supports the tool post and cutting tools. It moves either manually or automatically to allow the tool to cut along the length of the workpiece.
- Tool Post: The tool post is mounted on the carriage and holds the cutting tool in place. It can rotate to various angles, allowing the tool to approach the workpiece from different directions.
- Lead Screw and Feed Rod: The lead screw and feed rod are responsible for the automatic movement of the carriage during threading and feeding operations. The lead screw ensures precise threading, while the feed rod provides smooth, consistent motion during normal turning operations.
- Cross Slide and Compound Rest: The cross slide moves the tool post perpendicular to the workpiece’s axis, allowing the tool to make cuts across the face of the workpiece. The compound rest sits on top of the cross slide and can be adjusted to different angles for taper cutting or other intricate operations.
- Steady Rest and Follower Rest: These are support devices used when working with long, slender workpieces that may bend or flex during machining. The steady rest is fixed, while the follower rest moves along with the carriage.
Types of Operations Performed on a Lathe
Lathes are capable of performing a wide variety of operations, from simple turning to complex threading. Below are some of the most common operations:
- Turning: Turning is the most basic lathe operation, where material is removed from the outer diameter of the workpiece to create a cylindrical shape. It involves moving the tool parallel to the workpiece’s axis while the workpiece rotates.
- Facing: In facing, the cutting tool is moved perpendicular to the axis of rotation to create a flat surface on the end of the workpiece. This is often the first step in preparing the workpiece for further operations.
- Boring: Boring is used to enlarge an existing hole in the workpiece. The boring tool is mounted on the carriage and moved along the axis of the hole to achieve the desired diameter and depth.
- Drilling: A drill bit is mounted in the tailstock and advanced into the rotating workpiece to create holes. Drilling is typically followed by boring to refine the size and surface finish of the hole.
- Parting: Also known as cut-off, parting involves using a thin blade-like tool to cut through the workpiece, separating a finished part from the stock material.
- Threading: Threading on a lathe is done by moving the cutting tool along the workpiece at a specific feed rate synchronized with the rotation of the spindle. This creates helical threads on the outer diameter or inside a hole.
- Knurling: Knurling is a process that creates a textured pattern on the surface of a workpiece, often for grip purposes. It is done by pressing a set of knurling wheels against the rotating workpiece.
- Taper Turning: Taper turning involves gradually changing the diameter of the workpiece along its length. This is typically achieved using the compound rest or by offsetting the tailstock.
CNC Lathe Operation: Precision and Automation
CNC lathes operate on the same basic principles as manual lathes but offer the advantages of automation and precision through computer control. The key difference is that CNC lathes use pre-programmed instructions (G-code) to control the movements of the cutting tool and the rotation of the workpiece. This allows for more complex operations, faster production, and higher precision than manual lathes.
- G-Code Programming: CNC lathes rely on G-code, a programming language that specifies the movements, speeds, and operations of the machine. The operator inputs a set of instructions that the CNC system follows, allowing for consistent and repeatable results.
- Tool Paths: In CNC lathes, the tool path is pre-determined by the G-code. This ensures that the cutting tool follows the exact contour required for the part, making it possible to create intricate geometries that would be difficult or impossible to achieve with manual control.
- Multi-Axis Machining: Many CNC lathes are equipped with multiple axes of movement (typically X and Z axes), allowing for complex cuts and faster machining. Some advanced CNC lathes also have Y-axis movement or live tooling, which allows them to perform milling operations in addition to turning.
- Precision and Efficiency: One of the major advantages of CNC lathe operation is the level of precision it offers. The machine can execute complex instructions with sub-millimeter accuracy, making it ideal for industries where tight tolerances are critical. Moreover, the automation of tool changes and machining processes reduces cycle times and increases production efficiency.
- Batch Production: CNC lathes are particularly well-suited for high-volume production, where multiple identical parts need to be produced with consistent quality. Once the program is set, the machine can operate continuously with minimal human intervention.
Advantages of CNC Lathes Over Manual Lathes
- Increased Productivity: CNC lathes can operate 24/7 with minimal downtime, significantly boosting productivity in high-volume manufacturing environments.
- Consistency: Since the operations are controlled by a pre-programmed set of instructions, each part produced is identical to the previous one. This consistency is especially important for industries like aerospace and medical devices.
- Complex Operations: CNC lathes can perform intricate machining tasks that would be extremely challenging or impossible to accomplish on a manual lathe.
- Safety: CNC lathes reduce the need for manual intervention, lowering the risk of injury. Operators do not need to stand close to the machine, reducing exposure to moving parts or debris.
- Lower Skill Requirement: While operating a CNC lathe still requires training and skill, it does not demand the same level of manual dexterity and expertise needed for traditional lathe operation. The programming of the machine takes precedence over manual tool manipulation.
The lathe is a machine tool built on simple yet highly effective principles. By rotating the workpiece and applying cutting tools with precision, the lathe can create a wide variety of parts used in industries across the globe. The introduction of CNC technology has further enhanced the lathe’s capabilities, enabling faster production, greater precision, and the ability to tackle complex machining tasks with ease. Whether for simple turning or intricate multi-axis machining, the lathe remains an indispensable tool in modern manufacturing.
What Are the Main Components of a Lathe?
Lathes are versatile machines with multiple components working in tandem to execute precise machining operations. Understanding each part of a lathe and its function is essential for appreciating how these machines operate efficiently. In this chapter, we will explore the key components of a lathe, their roles, and how they contribute to the machine’s overall performance. Whether you are working with a manual or CNC lathe, the fundamental components remain similar, although CNC machines add some advanced features and automation capabilities.
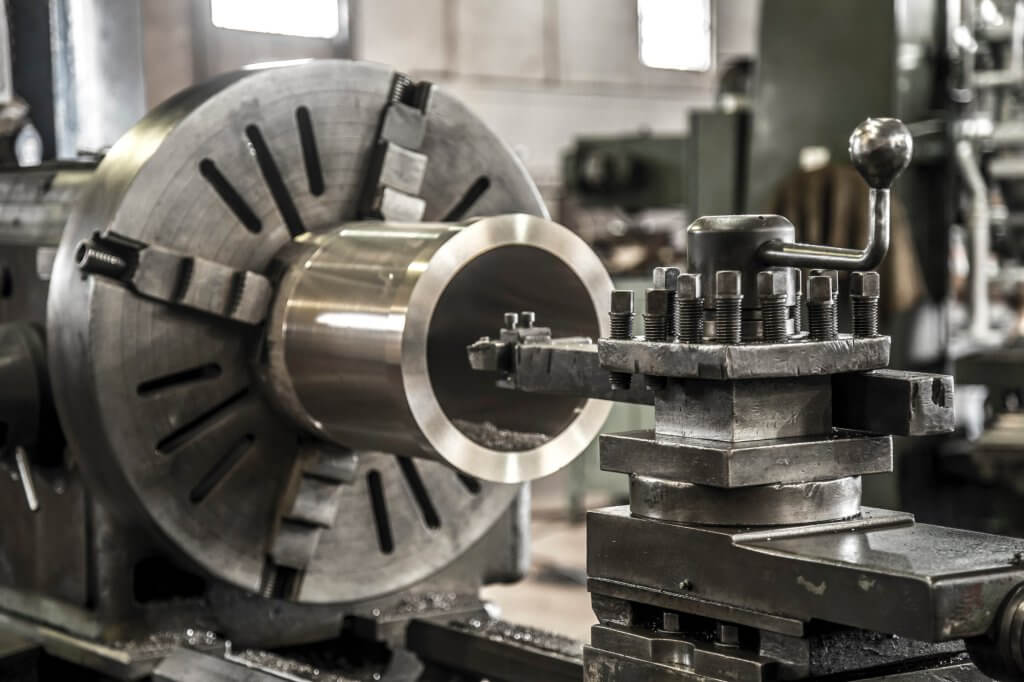
Overview of Key Components
At a high level, a lathe is comprised of several main components, each serving a specific purpose. These components can be categorized into three major systems:
- The holding and rotating system: This includes parts that hold and rotate the workpiece, such as the spindle, chuck, and headstock.
- The cutting and tooling system: This involves components responsible for the positioning and movement of the cutting tool, including the carriage, tool post, and cross slide.
- The support and stability system: This system provides stability and structural support for the entire machine, including the bed, tailstock, and various rests.
Let’s break down these components in detail.
1. Headstock: The Power Source of the Lathe
The headstock is located on the left end of the lathe and serves as the housing for the motor, gears, and other mechanical components that drive the machine. The headstock is responsible for powering the rotation of the spindle, which in turn rotates the workpiece. It is the powerhouse of the lathe and contains several important elements:
- Spindle: The spindle is a rotating shaft that holds the workpiece. It is the main component that provides rotational motion, which is essential for all machining operations on a lathe. The spindle speed can be adjusted to optimize cutting based on the material being worked on and the desired finish. Spindle speeds typically range from a few hundred RPM to thousands of RPM for different operations.
- Gearbox: Most lathes have a gearbox housed within the headstock, allowing the operator to control the speed and torque of the spindle. By changing gear settings, the lathe can rotate the workpiece at different speeds, depending on the operation being performed.
- Motor: The motor drives the spindle via belts or gears. In modern CNC lathes, electric motors provide precise control over spindle speed and torque, ensuring that the machine can operate efficiently at various speeds.
2. Tailstock: Support for Long Workpieces
The tailstock is located on the opposite end of the lathe from the headstock and serves as a support system for the other end of the workpiece. The tailstock is particularly important when working with long or slender pieces that would otherwise bend or flex during machining. The tailstock can be adjusted along the length of the bed to accommodate different workpiece sizes.
- Tailstock Quill: The quill is the part of the tailstock that moves forward and backward to engage or disengage the workpiece. It typically holds a center or a drill chuck, depending on the operation.
- Centers: Tailstocks often hold a live center (which rotates with the workpiece) or a dead center (which remains stationary) to support the workpiece during machining. These centers reduce friction and allow for smoother, more precise turning.
3. Bed: The Foundation of the Lathe
The bed is the horizontal structure that forms the foundation of the lathe. It supports all other components, ensuring that they remain aligned and stable during operation. The bed is usually made of cast iron or steel to provide rigidity and reduce vibration, both of which are crucial for precision machining.
- Guideways: The bed has guideways, also known as ways, which are precision-machined tracks that allow the carriage and tailstock to slide smoothly along the length of the bed. These guideways ensure accurate tool movement and positioning.
4. Carriage: Tool Movement and Positioning
The carriage is one of the most important components of the lathe. It holds and moves the cutting tool along the workpiece. The carriage travels along the bed, providing controlled movement of the tool either manually or automatically.
- Saddle: The saddle is part of the carriage and sits directly on the guideways. It is the part that physically moves along the bed as the operator or CNC system controls the motion.
- Cross Slide: The cross slide sits on top of the saddle and moves perpendicular to the axis of the workpiece (along the X-axis in most lathes). This movement allows the cutting tool to move toward or away from the centerline of the workpiece, making it ideal for operations such as facing or cutting grooves.
- Compound Rest: The compound rest is mounted on the cross slide and can be adjusted to different angles. It is particularly useful for cutting tapers or angles on a workpiece. The operator can set the compound rest to a specific angle, allowing for precise cuts.
- Apron: The apron is located on the front of the carriage and contains the controls for moving the carriage along the bed. It also houses the gears and levers for automatic feed control, which allows the carriage to move at a steady rate without manual intervention.
5. Tool Post: Holding the Cutting Tool
The tool post is mounted on top of the compound rest and serves as the holding device for the cutting tool. It is one of the most crucial components in determining the accuracy and finish of the workpiece. The tool post can be rotated to various angles, allowing the operator to adjust the cutting tool’s position for different operations.
- Quick-Change Tool Post: In many modern lathes, a quick-change tool post system is used, which allows the operator to quickly switch between different tools without the need to reset the machine. This improves efficiency, especially in high-volume production environments.
- Turret Tool Post: Some lathes, particularly CNC lathes, use a turret tool post, which holds multiple tools and can automatically switch between them as the machine moves from one operation to the next. This feature is especially useful for complex parts that require multiple operations.
6. Chuck: Gripping and Holding the Workpiece
The chuck is a clamping device that securely holds the workpiece during machining. It is attached to the spindle and rotates the workpiece as it is machined. The chuck’s jaws can be adjusted to accommodate different sizes and shapes of workpieces.
- Three-Jaw Chuck: A three-jaw chuck is the most common type, and it automatically centers the workpiece as it is clamped. It is typically used for round or hexagonal workpieces.
- Four-Jaw Chuck: A four-jaw chuck allows for individual adjustment of each jaw, making it suitable for irregularly shaped workpieces or operations that require off-center work.
- Collet Chuck: Collet chucks use a collet, which contracts around the workpiece as it is tightened. This type of chuck is ideal for small, precise work where minimal runout (eccentricity) is required.
- Faceplate: For irregularly shaped workpieces or those that cannot be held in a chuck, a faceplate can be used. The workpiece is bolted or clamped directly to the faceplate, which is mounted on the spindle.
7. Lead Screw and Feed Rod: Controlling Motion
The lead screw and feed rod are responsible for moving the carriage automatically during operations such as threading and turning. They ensure precise, consistent movement along the length of the bed.
- Lead Screw: The lead screw is specifically used for threading operations. It engages with the half-nut in the apron, moving the carriage at a precise rate that matches the rotation of the spindle. This synchronization is essential for cutting threads accurately.
- Feed Rod: The feed rod provides automatic movement of the carriage for general turning operations. It ensures smooth and consistent feed rates, reducing the need for manual control during long, continuous cuts.
8. Steady Rest and Follower Rest: Supporting the Workpiece
When machining long, slender workpieces, additional support is often needed to prevent bending or flexing during rotation. This is where steady rests and follower rests come into play.
- Steady Rest: The steady rest is a stationary support device mounted on the bed. It provides additional support for long workpieces by preventing deflection as the workpiece rotates.
- Follower Rest: Unlike the steady rest, the follower rest moves along with the carriage, providing continuous support as the tool moves along the workpiece. This is especially useful for precision machining on long shafts or rods.
9. Coolant System: Keeping the Tool and Workpiece Cool
Many lathes are equipped with a coolant system that helps reduce the heat generated during machining. The coolant, usually a mixture of water and soluble oil, is directed at the cutting tool and the workpiece to prevent overheating. This serves several important functions:
- Improved Tool Life: By keeping the cutting tool cool, the coolant reduces wear and extends the life of the tool.
- Better Surface Finish: Coolant reduces friction and minimizes heat buildup, resulting in a smoother surface finish on the workpiece.
- Chip Removal: The coolant helps wash away metal chips or swarf from the cutting area, preventing them from interfering with the operation or damaging the surface of the workpiece.
10. Digital Readout (DRO) Systems and CNC Controls
In modern lathes, especially CNC lathes, advanced digital readout (DRO) systems
or full CNC controls play a crucial role in ensuring precision and automation.
- DRO Systems: A digital readout system provides real-time feedback on the position of the cutting tool, allowing operators to make fine adjustments with high precision. DRO systems are common in manual lathes to assist in achieving accuracy without relying solely on hand dials.
- CNC Controls: In CNC lathes, the entire operation is controlled by computer software. The operator inputs a program that dictates every movement of the machine, from tool changes to cutting paths, speeds, and feeds. This allows for automated, precise, and repeatable machining of complex parts.
Understanding the main components of a lathe is key to mastering its operation. Each part, from the spindle to the tool post, plays a vital role in ensuring that the machine can produce high-quality, precise parts. Whether you are using a manual lathe or a CNC lathe, knowing how these components interact will help you get the most out of the machine and perform machining operations efficiently and accurately.
What Are the Different Types of Lathes?
Lathes come in various types, each designed to perform specific tasks depending on the material, the complexity of the part, and the desired precision. While all lathes operate on the same fundamental principle of rotating a workpiece against a fixed or moving tool, their configurations, size, and capabilities vary widely. In this chapter, we’ll explore the different types of lathes, their uses, and the industries in which they are commonly employed.
Understanding the types of lathes available will help in selecting the right machine for particular applications, from simple manual lathes used by hobbyists to advanced CNC lathes used in high-precision industries.
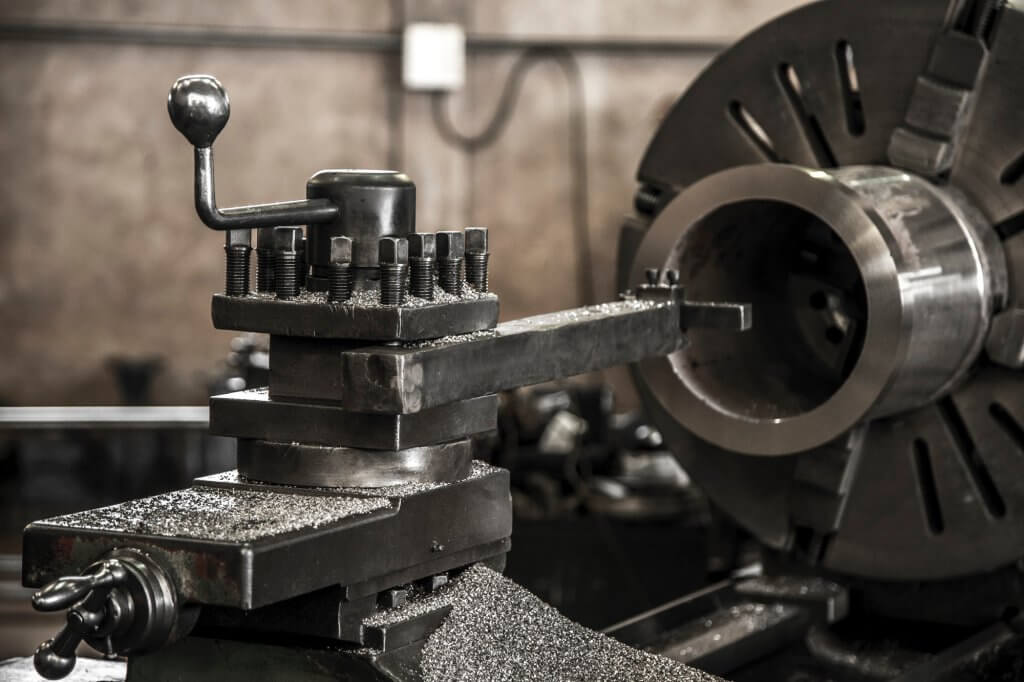
1. Engine Lathe: The Workhorse of General Machining
The engine lathe is perhaps the most common and versatile type of lathe. It is often referred to as the “workhorse” of the machine shop due to its wide-ranging capabilities. Engine lathes can perform basic turning operations, threading, boring, and drilling, and they are ideal for producing both simple and complex cylindrical parts.
- Manual Control: Engine lathes are primarily manually operated, which makes them highly flexible. They are often used in general machining workshops where a variety of tasks are performed, from custom parts to repair jobs.
- Wide Range of Sizes: Engine lathes come in various sizes, from small benchtop models used by hobbyists to large floor-standing machines capable of handling long and heavy workpieces.
- Basic Components: The typical components of an engine lathe include a headstock, tailstock, bed, carriage, and quick-change gearbox for threading and feed operations.
- Applications: Engine lathes are widely used in automotive repair shops, small job shops, and educational institutions for teaching basic machining principles.
2. Turret Lathe: Designed for Mass Production
Turret lathes are specialized machines designed to streamline production in environments where multiple operations are required on the same part. Unlike engine lathes, turret lathes are equipped with a rotating turret that holds several different cutting tools. This allows the operator to switch between tools quickly and efficiently without stopping the machine.
- Automated Tool Changes: The turret allows multiple tools to be mounted at once, and it can rotate into position as needed, significantly reducing the time spent changing tools.
- Capstan Lathe: A variation of the turret lathe, known as the capstan lathe, is used for light-duty work and features a lighter, quicker tool indexing system compared to the traditional turret lathe.
- Applications: Turret lathes are ideal for repetitive production of small to medium-sized parts, especially in industries where high-volume production is necessary, such as the automotive or appliance industries.
3. CNC Lathe: The Precision Powerhouse
CNC (Computer Numerical Control) lathes are some of the most advanced and powerful lathes available today. Unlike manual lathes, CNC lathes are controlled by pre-programmed computer software, which allows for automation, precision, and repeatability. CNC lathes can perform complex operations that would be impossible or extremely difficult to execute manually.
- Automation and Efficiency: CNC lathes are designed to operate autonomously after being programmed, which greatly enhances productivity and reduces the potential for human error.
- Multi-Axis Capabilities: Many CNC lathes feature multiple axes (typically X, Y, and Z) that allow for more complex and detailed machining. This enables the lathe to perform milling, drilling, and turning operations in a single setup.
- Live Tooling: Some CNC lathes are equipped with live tooling, which allows the machine to perform operations such as milling and drilling while the workpiece is held in place. This adds versatility and reduces the need for multiple machines.
- Applications: CNC lathes are used in high-precision industries such as aerospace, automotive, medical device manufacturing, and electronics. They are ideal for producing parts with tight tolerances, complex geometries, and large production volumes.
4. Vertical Lathe: Ideal for Heavy Workpieces
A vertical lathe, also known as a vertical boring mill, is designed for handling large and heavy workpieces that are difficult to machine on a traditional horizontal lathe. In a vertical lathe, the workpiece is held on a horizontal rotating table, while the cutting tool is mounted on a vertical axis.
- Gravity-Assisted Setup: The vertical configuration uses gravity to assist in holding and stabilizing heavy workpieces, making it ideal for machining large parts such as flywheels, brake drums, and industrial components.
- Applications: Vertical lathes are often used in industries such as heavy equipment manufacturing, energy production, and shipbuilding, where large and bulky components are machined.
5. Wood Lathe: Simplicity for Craftsmanship
While most lathes are used for metalworking, wood lathes are specifically designed for woodturning. They are much simpler in design and construction compared to metalworking lathes and are commonly used by craftsmen and hobbyists for creating artistic and functional wooden objects, such as bowls, furniture legs, and spindles.
- Manual Control: Wood lathes are manually operated, and the cutting tools are typically handheld chisels or gouges, giving the operator full control over the shaping process.
- Applications: Wood lathes are used in woodworking shops, furniture manufacturing, and by artists for creating custom, hand-turned wooden objects.
6. Toolroom Lathe: Precision for Small-Scale Machining
A toolroom lathe is a high-precision lathe designed for making fine tools, dies, and molds. These lathes are known for their accuracy and smooth operation, which makes them ideal for jobs requiring extremely tight tolerances. Toolroom lathes are typically smaller and more refined than engine lathes, with additional features for precise tool setting and fine adjustments.
- Applications: Toolroom lathes are widely used in tool and die manufacturing, as well as in workshops that produce prototypes, specialized tools, or small batches of highly precise parts.
7. Capstan and Turret Lathe: Semi-Automatic Production Power
While turret lathes are typically manual, capstan and turret lathes are semi-automatic and are designed to handle repetitive work for medium-volume production runs. These machines are particularly efficient in environments where similar parts are produced frequently, but full automation is not required.
- Multiple Tooling: Like turret lathes, capstan and turret lathes allow multiple tools to be mounted at once, but the semi-automatic feature enables the machine to complete several operations without manual intervention.
- Applications: These lathes are often used in the production of precision components such as screws, bolts, and other fasteners, especially in the automotive and machinery industries.
8. Special Purpose Lathes: Tailored for Specific Tasks
Special purpose lathes are customized machines built to perform specific, often highly specialized tasks. These lathes may be modified versions of traditional machines or completely unique designs tailored to a particular industry or application. Examples include:
- Watchmaker’s Lathe: A small, highly precise lathe used by horologists for making tiny components in watches and clocks.
- Wheel Lathes: Used specifically for machining locomotive or railway wheels.
- Crankshaft Lathe: Designed for machining large crankshafts in engines.
- Applications: Special purpose lathes are found in industries where unique or highly specialized components need to be machined, such as in watchmaking, railways, and large-scale engine manufacturing.
9. Swiss Lathe: Extreme Precision for Small Parts
Swiss lathes, also known as Swiss-type automatic lathes, are highly precise machines designed for machining small, complex parts. Originally developed for the Swiss watch industry, these machines are now used in a wide range of industries for producing precision components.
- Sliding Headstock: One of the key features of a Swiss lathe is its sliding headstock, which moves the workpiece through a guide bushing, allowing for incredibly accurate and stable cuts.
- Applications: Swiss lathes are used in industries such as medical device manufacturing, electronics, and the production of intricate components for watches and precision instruments.
The wide variety of lathes available today reflects the machine’s adaptability to a vast array of industries and applications. Whether you’re machining small, intricate parts on a Swiss lathe or large industrial components on a vertical lathe, selecting the right type of lathe for the job is critical to achieving precision, efficiency, and productivity. Each lathe type has its strengths and is suited for specific tasks, making it one of the most versatile machine tools in the world of manufacturing.
How is a Lathe Different from Other Machine Tools?
Lathes are one of the most widely used and versatile machine tools in manufacturing, but they are often confused with other types of machining equipment, such as milling machines, drilling machines, and grinders. Although these machines share some similarities, each has unique features and is suited for different types of tasks. In this chapter, we will compare lathes with other common machine tools, highlighting their distinctive characteristics, advantages, and specific applications.
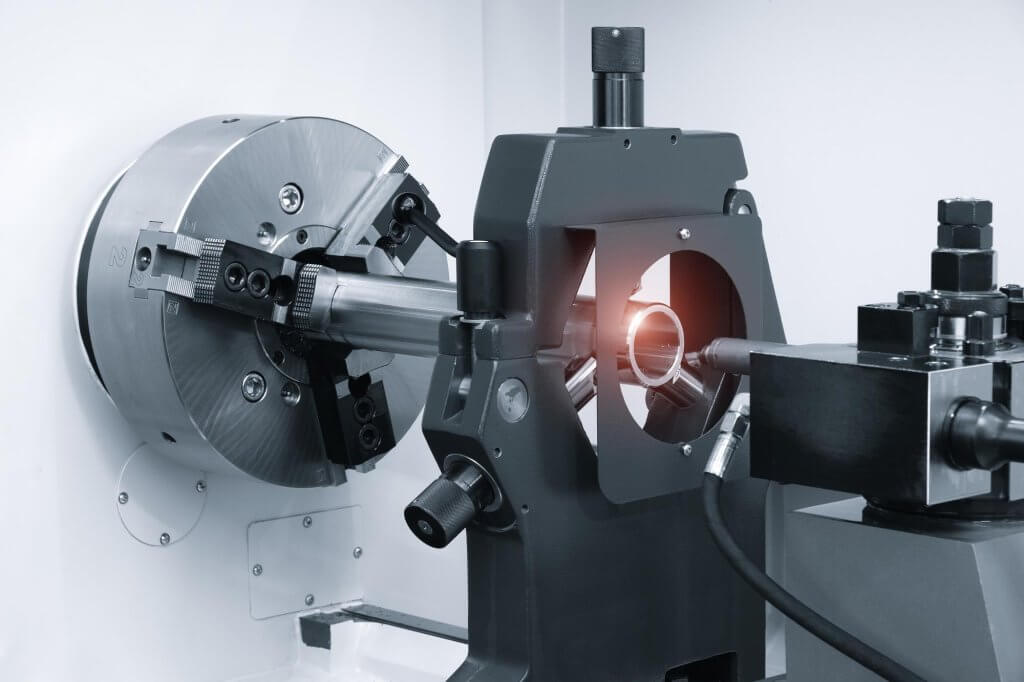
What Makes a Lathe Unique?
The defining feature of a lathe is that the workpiece rotates while the cutting tool remains stationary (or moves along specific paths). This is the fundamental difference between a lathe and other machine tools, where the cutting tool is usually the part that rotates while the workpiece remains fixed.
- Rotating Workpiece: In a lathe, the workpiece is mounted on a spindle and rotates around its central axis. This rotation is crucial for operations such as turning, threading, and facing. The fixed or moving cutting tool removes material by interacting with the rotating workpiece.
- Linear Tool Movement: The cutting tool in a lathe is either fixed in a tool post or mounted on a carriage that moves linearly (along X and Z axes) to perform various operations. The movement of the tool in relation to the rotating workpiece allows for precision shaping.
- Cylindrical Shaping: Lathes are primarily used for creating cylindrical or symmetrical shapes. While other machine tools can produce a variety of shapes, the lathe excels at producing round objects, such as shafts, bushings, and threaded rods.
- Concentric Operations: A key advantage of the lathe is its ability to perform concentric operations, where the entire workpiece rotates around a central axis. This ensures uniformity in diameter and surface finish.
Let’s compare the lathe with other machine tools based on their unique features, operations, and applications.
Comparison of Lathe vs. Milling Machine
Milling machines are another type of versatile machine tool, but they operate on a fundamentally different principle compared to lathes. In a milling machine, the cutting tool rotates, and the workpiece is held stationary or moves in different axes (usually X, Y, and Z). Here’s a detailed comparison:
Feature | Lathe | Milling Machine |
---|---|---|
Workpiece Movement | Rotates on a spindle | Held stationary or moved along X, Y, Z axes |
Tool Movement | Moves linearly along the workpiece | Rotates at high speeds to cut material |
Primary Operations | Turning, threading, facing, boring | Milling, drilling, contouring, slotting |
Typical Products | Cylindrical parts (shafts, rods, bushings) | Flat or complex shapes (gears, slots, holes) |
Precision | High precision for cylindrical objects | High precision for complex and flat surfaces |
- Milling Applications: Milling machines are more suited for creating complex shapes, grooves, and flat surfaces. They can be used to produce parts like gears, slots, holes, and intricate 3D contours that are difficult to achieve on a lathe.
- Lathe Applications: On the other hand, lathes are perfect for producing parts that require high concentricity and symmetry. Operations such as turning, facing, threading, and boring are best suited for lathes, particularly when working with long or cylindrical materials.
Comparison of Lathe vs. Drilling Machine
Drilling machines are another essential tool in any machine shop, designed primarily for creating holes in a workpiece. While both lathes and drilling machines can drill holes, their methods and purposes differ significantly.
Feature | Lathe | Drilling Machine |
---|---|---|
Primary Function | Turning, threading, boring | Drilling holes |
Workpiece Movement | Rotates on a spindle | Stationary workpiece |
Tool Movement | Moves along workpiece for shaping | Drill bit moves vertically into workpiece |
Additional Operations | Threading, boring, facing | Primarily limited to drilling holes |
- Drilling on a Lathe: Lathes can also drill holes, but the process is different from a drilling machine. The workpiece rotates on a lathe, while the drill bit is fed into it from the tailstock. This allows for accurate, concentric holes, especially in cylindrical parts.
- Drilling Machines: Dedicated drilling machines are more efficient for creating straight, vertical holes in flat workpieces. They are often used when multiple holes need to be drilled in a row or when working with sheet metal or flat stock.
Comparison of Lathe vs. Grinder
Grinding machines are designed for removing small amounts of material to achieve a fine surface finish or precise dimensions. While lathes can achieve a certain degree of precision, grinding machines are used for finishing operations that require extremely tight tolerances.
Feature | Lathe | Grinder |
---|---|---|
Material Removal | Cuts away material using cutting tools | Abrasive wheel grinds away material |
Surface Finish | Moderate to high, depending on tooling | Extremely high, mirror-like finish |
Primary Operations | Turning, threading, boring, facing | Surface finishing, precision dimensioning |
Precision | High for cylindrical shapes | Ultra-high for surface finishes and precision |
- Lathe Applications: Lathes are ideal for producing the basic shape of a workpiece, especially cylindrical parts. However, they may not achieve the ultra-smooth surface finish required for certain applications, such as bearings or precise shafts.
- Grinder Applications: Grinders are used for finishing parts that require high precision, such as engine components, gears, or machine parts that need to meet extremely tight tolerances. Grinding is typically the final step in the machining process, used after the part has been shaped on a lathe or milling machine.
Comparison of Lathe vs. CNC Machining Centers
CNC machining centers are highly advanced, fully automated machine tools that can perform a variety of tasks, including milling, drilling, tapping, and sometimes even turning operations. CNC lathes and CNC machining centers overlap in terms of automation and precision, but each has distinct strengths.
Feature | CNC Lathe | CNC Machining Center |
---|---|---|
Workpiece Movement | Rotates on spindle | Stationary workpiece; multiple tool movements |
Tool Movement | Linear (X, Z, sometimes Y axes) | Multi-axis (X, Y, Z, B, C axes) |
Primary Operations | Turning, threading, boring, facing | Milling, drilling, tapping, contouring |
Typical Products | Cylindrical parts | Complex 3D shapes, molds, flat surfaces |
Precision | High for cylindrical parts | High for multi-axis complex parts |
- CNC Lathe Applications: CNC lathes are ideal for parts that require symmetrical or cylindrical features. They excel at turning and boring operations, as well as threading and facing.
- CNC Machining Center Applications: Machining centers are better suited for parts with complex geometries, multiple faces, and intricate features. They are commonly used for mold making, parts with cavities, and precision components that require operations on multiple axes.
Advantages and Disadvantages of a Lathe
While lathes offer many advantages, they are not suitable for all types of machining operations. Below is a summary of the key advantages and limitations of using a lathe:
Advantages of a Lathe | Disadvantages of a Lathe |
---|---|
High precision for cylindrical parts | Limited to parts with rotational symmetry |
Versatile – can perform multiple operations | Not suited for flat or complex shapes |
Ideal for turning, threading, boring, and facing | Cannot perform contouring or cavity creation |
Can produce smooth finishes with appropriate tooling | Requires skilled operators for manual machines |
Suitable for both small-scale and large-scale production | Often slower for complex, multi-face parts |
Lathes are distinguished from other machine tools by their unique ability to rotate the workpiece, making them ideal for machining cylindrical and symmetrical parts. While milling machines, drilling machines, grinders, and CNC machining centers each have their own areas of expertise, lathes excel in operations that require concentricity, cylindrical shaping, and precise surface finishes.
By understanding the key differences between lathes and other machine tools, machinists can select the appropriate equipment for their specific manufacturing needs, ensuring higher productivity, efficiency, and precision in their operations.
What Materials Can Be Machined Using a Lathe?
One of the key factors influencing the selection and setup of a lathe is the material being machined. Different materials exhibit distinct mechanical properties that affect how they are cut, shaped, and finished. From soft metals like aluminum to hard and abrasive materials such as titanium or ceramics, lathes are equipped to handle a wide range of materials. This versatility makes lathes an essential tool across numerous industries, including automotive, aerospace, medical, and consumer products.
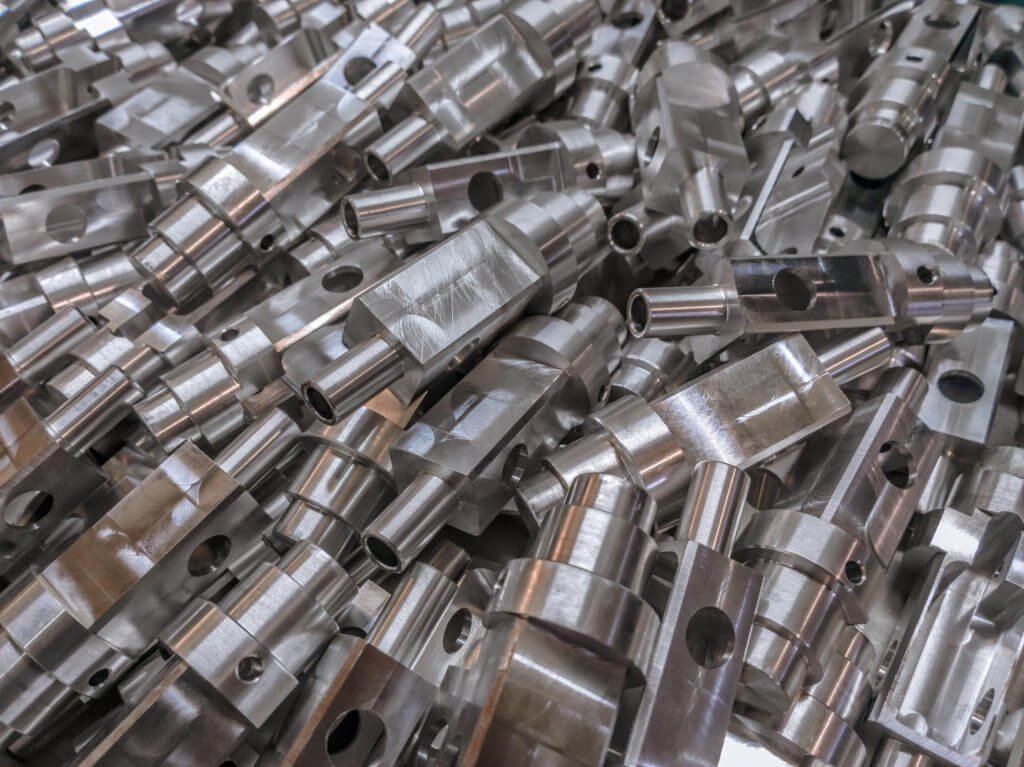
Classification of Machinable Materials
Lathe machining materials can generally be classified into the following categories:
- Metals: Ferrous and non-ferrous metals, including alloys.
- Plastics and Polymers: Including thermoplastics and thermosetting plastics.
- Composites and Fiberglass: Engineered materials made of two or more constituents.
- Woods: Used primarily in woodworking lathes for creating artisanal or functional objects.
- Ceramics and Hard Materials: Difficult to machine, often requiring specialized tools and techniques.
Each material class presents unique machining requirements, including cutting speeds, feed rates, and the type of tools required. The following sections break down each class of material, offering examples of common materials and their typical applications.
1. Metals: Ferrous and Non-Ferrous
Metals are the most common materials machined on a lathe, and they can be broadly divided into ferrous (those containing iron) and non-ferrous (those without iron) categories.
Metal Type | Example Materials | Machinability Rating | Common Applications |
---|---|---|---|
Ferrous | Steel, Cast Iron, Stainless Steel | Moderate to Low | Automotive parts, machinery, tools |
Non-Ferrous | Aluminum, Copper, Brass, Titanium | High to Moderate | Aerospace components, consumer products, electronics |
Ferrous Metals:
- Steel: One of the most versatile and commonly used materials in lathe machining, steel comes in various grades (carbon steel, tool steel, stainless steel). Machining steel requires robust tooling and optimal cutting speeds to prevent tool wear and heat buildup.
- Applications: Steel is commonly used in the manufacturing of automotive components, tools, machinery, and industrial equipment. It is also a preferred material for structural parts requiring high strength.
- Cast Iron: Known for its brittleness but excellent compressive strength, cast iron is a good choice for parts that need to withstand high mechanical loads. However, it is prone to cracking and chipping during machining, requiring specialized cutting tools.
- Applications: Engine blocks, machine bases, pipes, and heavy-duty automotive parts.
Non-Ferrous Metals:
- Aluminum: Aluminum is a soft, lightweight, and highly machinable metal, making it a favorite for industries where weight reduction is critical, such as aerospace and automotive. Its high thermal conductivity helps dissipate heat quickly during machining, reducing the risk of tool wear.
- Applications: Aerospace components, automotive parts, electronic housings, and consumer goods.
- Copper and Brass: These metals are known for their excellent machinability and thermal conductivity. Copper is often used in electrical components due to its high electrical conductivity, while brass is widely used for fittings, valves, and decorative elements.
- Applications: Plumbing fixtures, electrical components, and musical instruments.
- Titanium: Known for its strength-to-weight ratio and corrosion resistance, titanium is a challenging material to machine due to its hardness and tendency to cause tool wear. However, its unique properties make it indispensable in industries such as aerospace, medical devices, and high-performance sports equipment.
- Applications: Aircraft parts, medical implants, and high-performance automotive components.
2. Plastics and Polymers
Plastics, particularly high-performance engineering plastics, are increasingly being machined on lathes for use in various industries. Plastics offer advantages such as corrosion resistance, lightweight properties, and electrical insulation, making them suitable for a wide range of applications.
Plastic Type | Example Materials | Machinability Rating | Common Applications |
---|---|---|---|
Thermoplastics | ABS, Nylon, Polyethylene, PVC | High | Consumer products, automotive, medical devices |
Thermosets | Epoxy, Bakelite, Phenolic | Moderate to Low | Electrical components, high-strength applications |
Thermoplastics:
- ABS (Acrylonitrile Butadiene Styrene): ABS is a tough and durable plastic with good machinability. It is often used for 3D printing and in products requiring impact resistance and strength.
- Applications: Consumer electronics, automotive interior parts, toys.
- Nylon: Nylon is strong, lightweight, and wear-resistant. It has good machinability and is often used in industrial applications where friction and abrasion are a concern.
- Applications: Bearings, gears, bushings, and wear-resistant parts.
- PVC (Polyvinyl Chloride): PVC is widely used due to its resistance to corrosion and chemicals. It is easy to machine and is used in both consumer products and industrial applications.
- Applications: Pipes, fittings, and chemical containers.
Thermosetting Plastics:
- Epoxy: Thermosetting plastics like epoxy are harder to machine than thermoplastics but offer excellent chemical resistance and strength. They are often used in applications requiring high performance under heat and stress.
- Applications: Adhesives, electronics, structural parts.
3. Composites and Fiberglass
Composites are materials made from two or more constituent materials with different properties. Fiberglass, carbon fiber, and other composite materials are becoming increasingly popular in industries that require lightweight yet strong materials. However, machining these materials presents challenges, such as tool wear and dust management.
Composite Type | Example Materials | Machinability Rating | Common Applications |
---|---|---|---|
Fiberglass | Glass Fiber-Reinforced Plastic (GFRP) | Low to Moderate | Automotive, construction, marine applications |
Carbon Fiber | Carbon Fiber-Reinforced Polymer (CFRP) | Low | Aerospace, sports equipment, automotive |
- Fiberglass (GFRP): Glass fiber-reinforced plastic is difficult to machine due to its abrasive nature, which quickly wears out cutting tools. However, it is widely used in the construction and automotive industries due to its strength and resistance to corrosion.
- Applications: Body panels, boat hulls, roofing materials.
- Carbon Fiber (CFRP): Carbon fiber composites are extremely strong and lightweight but pose challenges during machining due to their tendency to fray and generate dust. Specialized tooling and vacuum systems are often needed to handle these materials.
- Applications: Aerospace components, high-performance automotive parts, sporting goods.
4. Woods: For Artisanal and Functional Objects
Wood, although less commonly machined on metal lathes, remains a staple material for woodworking lathes. Woodturning is a craft that creates both functional and decorative items such as furniture, bowls, and sculptures.
Wood Type | Example Materials | Machinability Rating | Common Applications |
---|---|---|---|
Hardwoods | Oak, Walnut, Maple | High | Furniture, flooring, high-end products |
Softwoods | Pine, Cedar, Fir | High | Structural components, furniture |
- Hardwoods: Hardwoods like oak and walnut are prized for their strength, durability, and aesthetic appeal. They are commonly used in high-end furniture and flooring.
- Applications: Cabinets, tables, flooring, decorative objects.
- Softwoods: Softwoods like pine and cedar are easier to machine and are often used in construction and furniture making. While they lack the durability of hardwoods, they are more cost-effective and easier to work with.
- Applications: Building frames, furniture, outdoor structures.
5. Ceramics and Hard Materials
Ceramics and other hard materials such as glass and carbide are difficult to machine on conventional lathes due to their brittleness and hardness. These materials require specialized tooling, such as diamond-coated or carbide-tipped tools, to machine without causing damage or cracking.
Hard Material Type | Example Materials | Machinability Rating | Common Applications |
---|---|---|---|
Ceramics | Alumina, Silicon Carbide | Low | Medical devices, aerospace, electronics |
Hard Metals | Tungsten Carbide, Inconel | Low | Cutting tools, high-temperature applications |
- Ceramics: Ceramic materials are known for their hardness, corrosion resistance, and ability to withstand high temperatures. They are commonly used in medical devices, aerospace components, and electronics.
- Applications: Cutting tools, bearings, medical implants.
- Tungsten Carbide: Tungsten carbide is a hard, dense material commonly used in cutting tools and wear-resistant applications. It is extremely difficult to machine, requiring specialized equipment and tools.
- **Applications
**: Cutting tools, high-wear parts, dies and molds.
Machinability Chart for Common Materials
The machinability of a material is often evaluated based on several factors, including cutting speed, tool wear, and surface finish. Below is a table summarizing the relative machinability of common materials:
Material | Machinability Rating | Typical Cutting Speed (m/min) | Notes on Machining Challenges |
---|---|---|---|
Aluminum | High | 300-600 | Easy to machine, good surface finish |
Steel (Carbon) | Moderate | 60-180 | Tool wear at higher speeds |
Stainless Steel | Low | 20-50 | Hardness increases tool wear |
Titanium | Low | 20-40 | Prone to heat buildup, difficult to cut |
ABS Plastic | High | 400-800 | Tends to melt if overheated |
Glass Fiber Composite | Low | 15-40 | Extremely abrasive, causes tool wear |
A wide variety of materials can be machined on a lathe, ranging from metals and plastics to composites and hard materials. The machinability of these materials varies significantly, depending on their hardness, thermal properties, and resistance to wear. By understanding the specific characteristics and challenges of each material, machinists can optimize their tooling, speeds, and processes to achieve the best results in lathe machining.
The ability to machine diverse materials with precision makes the lathe an invaluable tool in industries such as aerospace, automotive, medical, and consumer goods. Matching the material to the right cutting tools, speeds, and techniques is essential for achieving high-quality parts and maximizing efficiency.
What Operations Can Be Performed on a Lathe?
Lathes are versatile machines capable of executing a wide variety of operations, which makes them invaluable in manufacturing. Each operation has a distinct function, contributing to shaping, modifying, or refining a workpiece. In this chapter, we will cover the key operations that can be performed on a lathe, ranging from the basic to the more complex. Understanding these operations is crucial to maximizing a lathe’s utility and ensuring the production of precise, high-quality parts.
1. Turning: The Core Operation
Turning is the most fundamental operation performed on a lathe. It involves the removal of material from the outer diameter of a rotating workpiece to reduce its size and create a cylindrical shape. The cutting tool moves along the length of the workpiece, shaving off layers to reach the desired dimension.
- Types of Turning:
- Rough Turning: Removes large amounts of material quickly to shape the workpiece roughly to size.
- Finish Turning: Uses finer cutting tools and smaller cuts to produce smooth, accurate surfaces.
- Applications: Turning is used to manufacture components like shafts, rods, and cylindrical parts for engines and machines.
2. Facing: Creating Flat Surfaces
Facing is the process of cutting across the face of the rotating workpiece to create a flat surface at the end. This operation is typically performed to prepare the workpiece for further machining or assembly.
- Process: The cutting tool moves perpendicular to the rotating axis of the workpiece, removing material and creating a smooth, flat surface.
- Applications: Facing is commonly used to finish the ends of rods, prepare parts for joining, or refine components for further machining, such as drilling.
3. Drilling: Creating Holes in a Workpiece
Although drilling is typically associated with drill presses, it can also be performed on a lathe. Drilling involves using a drill bit held in the tailstock and feeding it into the rotating workpiece.
- Process: As the workpiece rotates, the stationary drill bit advances into the material, cutting a hole. This method allows for highly accurate, centered holes, especially in round or cylindrical parts.
- Applications: Drilling on a lathe is used to create holes for shafts, bolts, fasteners, or preparation for boring.
4. Boring: Enlarging Existing Holes
Boring is an internal cutting operation that enlarges an existing hole. Unlike drilling, boring requires the tool to remove material from the inside of the workpiece to refine the hole size or achieve a precise internal diameter.
- Process: The boring bar, mounted on the tool post, is fed into the rotating workpiece to enlarge and refine the hole.
- Applications: Boring is often used to create precision holes with tight tolerances, commonly seen in parts such as bearings, cylinders, and housings.
5. Threading: Cutting Internal or External Threads
Threading involves cutting a helical groove into the surface of a workpiece, either internally or externally, to create threads for screws, bolts, or fasteners. This operation can be performed manually or automatically, depending on the type of lathe used.
- Process: The cutting tool is fed along the workpiece’s axis in synchronization with its rotation, cutting threads of specific pitch and depth.
- Applications: Threading is used to produce bolts, nuts, and other fasteners, as well as components requiring threaded joints.
6. Knurling: Creating Textured Patterns
Knurling is a unique operation where the lathe creates a textured pattern on the surface of a workpiece. Instead of cutting, knurling displaces material to form a series of ridges, commonly in a diamond or straight pattern. This pattern enhances grip and aesthetic appeal.
- Process: Knurling tools are pressed against the rotating workpiece to emboss the surface with the desired pattern.
- Applications: Knurling is frequently used on tool handles, knobs, and fasteners where grip is critical or a decorative finish is required.
7. Parting (Cutting Off): Separating a Finished Part
Parting (or cutting off) is the operation of cutting a workpiece to separate a finished component from the remaining material. This is often one of the final steps in lathe machining.
- Process: A thin cutting tool is fed perpendicular to the workpiece until it cuts through, effectively “parting off” the finished section.
- Applications: Parting is used in batch production to separate multiple finished components from a single piece of stock material or to create grooves or recesses.
8. Grooving: Cutting Narrow Channels
Grooving is the process of cutting narrow channels or recesses into a workpiece. This is usually performed to prepare parts for assembly with rings, seals, or to create specific surface features.
- Process: The tool is fed perpendicular to the rotating workpiece, cutting a specific width and depth into the surface.
- Applications: Grooving is often used to create channels for O-rings, retaining rings, or other types of sealing and locking components.
9. Reaming: Refining Holes for Precision
Reaming is used to enlarge and finish an existing hole to a precise diameter with a smooth finish. Reamers are fed into the workpiece using the lathe’s tailstock, refining the hole created by a previous operation such as drilling or boring.
- Process: A reamer is fed slowly into the rotating workpiece, removing a small amount of material to improve accuracy and surface quality.
- Applications: Reaming is used for creating precision holes with exact diameters and smooth finishes, commonly required for fitting dowels, pins, or shafts.
Lathe operations are highly versatile, allowing machinists to perform a wide variety of tasks from basic shaping to intricate detailing. Understanding each operation’s purpose and how to execute it effectively is key to producing high-quality parts. Whether you’re roughing out a shaft or creating precision threads, knowing the available operations on a lathe ensures that you can choose the right technique for any machining project.
When Should You Use a Lathe vs. a Machining Center?
Both lathes and machining centers are essential tools in the world of manufacturing, but they have distinct purposes. Choosing the right machine depends on the nature of the workpiece, the type of operation, and the desired outcome. In this chapter, we’ll explore the differences between lathes and machining centers, and discuss when each machine should be used.
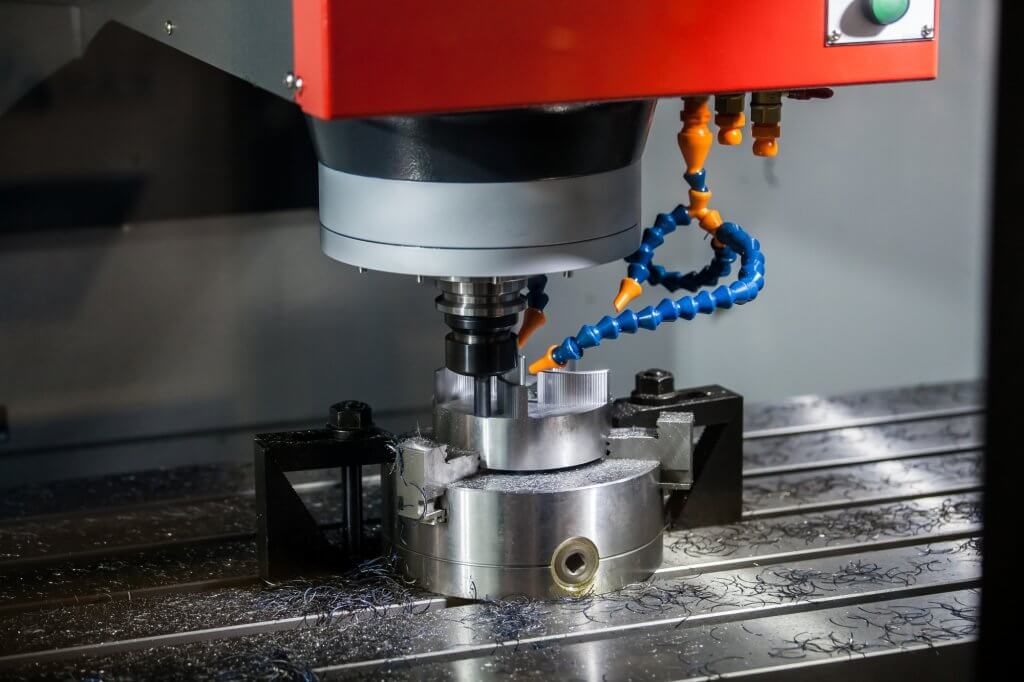
Understanding the Core Difference: Lathe vs. Machining Center
At the most basic level, the fundamental difference between a lathe and a machining center lies in how each machine handles the workpiece and the cutting tool:
- Lathe: The workpiece rotates around its axis while the cutting tool remains stationary (or moves linearly along the workpiece). Lathes are ideal for cylindrical or symmetrical parts.
- Machining Center: The workpiece remains stationary (or moves along certain axes), while the cutting tool rotates and moves across multiple axes. Machining centers are designed for more complex, multi-dimensional shapes and contours.
Comparison | Lathe | Machining Center |
---|---|---|
Workpiece Movement | Rotates around its axis | Fixed; cutting tool moves in multiple directions |
Primary Operations | Turning, threading, boring, facing, knurling | Milling, drilling, tapping, contouring |
Typical Workpiece | Cylindrical shapes (shafts, bushings, fasteners) | Complex 3D shapes (gears, molds, machine components) |
Number of Axes | Typically 2 axes (X, Z) | Can have up to 5 axes (X, Y, Z, plus rotational axes) |
1. When to Choose a Lathe
Lathes are best suited for operations where the workpiece is cylindrical or needs to be symmetrical around a central axis. Here are common situations where a lathe is the preferred machine:
- Turning Cylindrical Parts: If the part is primarily cylindrical, such as a shaft, rod, or bushing, a lathe is ideal. The rotating workpiece allows for consistent, even cuts along its length.
- Threading Operations: Lathes excel at producing both internal and external threads, ensuring precise, uniform helical grooves that are essential for fasteners and fittings.
- Facing and Boring: Lathes provide excellent control for creating flat surfaces (facing) or enlarging existing holes (boring), particularly in long, cylindrical workpieces.
- Small Batch and Prototyping: Lathes are generally easier to set up for simpler operations, making them more efficient for small batch production or one-off prototypes.
Lathe Best Uses | Example Applications |
---|---|
Cylindrical Turning | Shafts, axles, rods, bushings |
Threading | Bolts, screws, pipes, threaded fasteners |
Boring | Enlarging holes in cylindrical parts like bearings |
Facing | Preparing ends of cylindrical parts, creating flat surfaces |
Knurling | Textured surfaces for tool handles, fasteners, and grips |
2. When to Choose a Machining Center
A machining center is a versatile, multi-functional tool capable of performing a wide variety of operations beyond the capabilities of a lathe. Choose a machining center when:
- Complex 3D Shapes Are Required: For parts with intricate geometries, multiple faces, or complex contours, a machining center is the better choice. Machining centers excel at multi-axis operations, allowing for drilling, tapping, milling, and contouring in one setup.
- High Precision Is Needed on Multiple Planes: If the part requires precision machining on more than one face (e.g., cube-like or multi-faceted parts), a machining center offers greater flexibility with its ability to work on multiple axes.
- Batch Production of Complex Parts: If the parts require multiple machining processes (e.g., drilling, milling, and tapping), machining centers allow for greater efficiency. They reduce the need for manual intervention between operations, which lowers setup time and increases productivity in batch production.
- Five-Axis Operations: For industries like aerospace and automotive that need extremely complex, precise parts, five-axis machining centers allow for machining from multiple angles in a single setup, reducing errors and ensuring accuracy.
Machining Center Best Uses | Example Applications |
---|---|
Complex 3D Milling | Molds, dies, gears, engine blocks |
Multi-Axis Machining | Aerospace components, medical implants, automotive parts |
Drilling and Tapping | Producing holes, threaded features on flat or irregular surfaces |
Contouring | Sculpting parts with complex geometries like turbine blades |
High-Volume Production | Efficient for parts that require multiple operations in one setup |
3. Hybrid Solutions: Combining Lathes and Machining Centers
In modern manufacturing environments, it’s common to use both lathes and machining centers in tandem to take advantage of their respective strengths. Many manufacturers opt for CNC turning centers with live tooling capabilities, which blur the line between a traditional lathe and a machining center. Live tooling allows the lathe to perform some milling and drilling operations in addition to traditional turning.
- When to Use Hybrid Machines: If a part requires both cylindrical turning and secondary milling or drilling operations, a turning center with live tooling can complete all operations in a single setup, reducing the need for moving parts between machines.
- Advantages: The combination of turning and milling in one setup reduces errors from re-fixturing and increases overall production efficiency. This is especially beneficial for complex parts that would traditionally require multiple machines and setups.
Hybrid Machine Capabilities | Example Applications |
---|---|
Turning and Milling in One Setup | Complex shafts with features like flat surfaces, slots, or holes |
Reducing Setup Time | High-precision parts requiring multiple machining operations |
Efficiency in Batch Production | Small-to-medium batch production of intricate cylindrical parts |
4. Cost and Efficiency Considerations
When deciding between a lathe and a machining center, cost and efficiency are important factors. Lathes are generally more affordable and simpler to set up, making them a good option for smaller operations or when producing simple cylindrical parts. Machining centers, on the other hand, are more expensive but can handle more complex parts and offer higher efficiency in certain operations, especially when multiple machining processes are required.
Cost and Efficiency | Lathe | Machining Center |
---|---|---|
Initial Cost | Lower | Higher |
Setup Time | Quick for cylindrical parts | Longer, but capable of multiple operations |
Suitability for Complex Parts | Limited to cylindrical shapes | Ideal for complex, multi-axis parts |
Productivity | Efficient for simple, repetitive tasks | More productive for multi-process parts |
Choosing between a lathe and a machining center comes down to the specific needs of the project. Lathes are best suited for cylindrical parts and simpler operations, while machining centers excel at handling complex geometries and multi-axis machining. In many cases, both machines can be used together to optimize production efficiency. Understanding the strengths of each machine ensures that you select the right tool for the job, improving both precision and productivity.
How to Choose the Right Lathe for Your Project?
Selecting the right lathe for a particular project involves understanding the specific needs of your workpiece, production volume, and material requirements. Lathes come in a wide range of types and sizes, each suited for different applications, so making the right choice ensures optimal performance, precision, and efficiency in manufacturing. In this chapter, we will discuss the key factors to consider when choosing a lathe for your project.
1. Workpiece Size and Complexity
The size and complexity of the workpiece are the primary considerations when selecting a lathe. The lathe’s size, power, and capabilities must match the dimensions and features of the workpiece.
- Length and Diameter: Different lathes accommodate different workpiece lengths (also called swing) and diameters. The swing is the maximum diameter a lathe can handle, while the distance between centers defines the maximum workpiece length. If your workpiece is long or wide, you’ll need a lathe with larger capacity.
- Complexity of Shape: For simpler cylindrical parts, a standard lathe is sufficient. However, if your part requires intricate features, threading, or multi-step operations, you might need a more advanced CNC lathe.
Workpiece Factor | Considerations for Choosing a Lathe |
---|---|
Length (Distance Between Centers) | Long parts like shafts may require a lathe with extended bed length. |
Diameter (Swing) | Larger workpieces require a lathe with a bigger swing over the bed. |
Part Complexity | Simple parts suit manual lathes, while complex geometries may require CNC lathes. |
2. Type of Lathe
There are various types of lathes designed for specific applications, from manual lathes for basic operations to more advanced CNC (Computer Numerical Control) lathes that offer precision automation. Let’s look at the different types of lathes and when each is appropriate:
- Manual Lathe: A manual lathe is ideal for small projects or operations where intricate precision is not required. It’s a good choice for single parts, simple turning, and one-off prototypes.
- CNC Lathe: CNC lathes are computer-controlled and can automate multiple operations, including turning, threading, drilling, and boring. These machines are best for producing complex parts with high precision and consistency in medium to large production volumes.
- Turret Lathe: A turret lathe allows for quick tool changes by utilizing multiple tools mounted on a turret. This lathe is ideal for repetitive production runs, where the same operations are performed on a large number of parts.
Lathe Type | Best For |
---|---|
Manual Lathe | One-off prototypes, small batch production, simple parts |
CNC Lathe | Complex geometries, high precision, medium to large batch production |
Turret Lathe | Repetitive production, quick tool changes, large batch production |
3. Material Considerations
The material being machined plays a major role in selecting the right lathe. Different materials have different hardness levels, machining properties, and tool wear characteristics, which can affect the lathe’s power requirements and tooling options.
- Soft Materials (e.g., Aluminum, Plastics): Soft materials like aluminum and certain plastics can be machined with relatively low-power lathes. A standard manual or CNC lathe with basic tooling will suffice for most soft materials.
- Hard Materials (e.g., Steel, Titanium): For harder materials like steel, stainless steel, or titanium, you’ll need a lathe with more power and rigidity to handle the higher forces during cutting. These materials may also require specialized carbide or ceramic tooling to maintain precision and reduce tool wear.
- Exotic Materials (e.g., Inconel, Ceramics): Materials like Inconel or ceramics are difficult to machine and require high-precision CNC lathes with specialized tooling and cutting parameters. These materials also demand advanced cooling and lubrication systems to prevent tool degradation.
Material | Lathe Requirement |
---|---|
Soft Materials | Standard manual or CNC lathes with basic tools |
Hard Materials | High-power lathes, specialized tooling (carbide or ceramic tools) |
Exotic Materials | Precision CNC lathes, advanced cooling, and specialized tooling |
4. Precision and Tolerance Requirements
The level of precision and tolerance required for your project will dictate the type of lathe and the level of automation needed. Precision is especially critical in industries like aerospace, medical devices, and automotive, where tight tolerances are essential for safety and performance.
- High Precision: If your project demands extreme precision (e.g., aerospace components or medical implants), CNC lathes are the best choice. They offer tight control over tool movement and cutting speed, ensuring that parts meet exact specifications consistently.
- Low to Moderate Precision: For projects with less stringent tolerance requirements (e.g., general-purpose parts, non-critical components), a manual lathe may be sufficient, especially for smaller batches or prototypes.
Precision Level | Recommended Lathe |
---|---|
High Precision (±0.001 mm) | CNC lathe with advanced control features |
Moderate Precision (±0.01 mm) | Standard CNC or manual lathe |
Low Precision (±0.1 mm) | Manual lathe, suitable for non-critical components |
5. Production Volume
The volume of production is another critical factor in choosing the right lathe. Different lathes are suited for different levels of production, from one-off parts to mass production.
- Low Production Volume: For small batch sizes or one-off prototypes, a manual lathe or basic CNC lathe is usually the most cost-effective option. These machines can be set up quickly and are flexible enough to handle a variety of operations without long changeover times.
- Medium to High Production Volume: For larger production volumes, CNC lathes or turret lathes are better suited. CNC lathes provide consistent precision and can handle repetitive tasks efficiently, while turret lathes excel in quick tool changes for high-speed production runs.
Production Volume | Lathe Type |
---|---|
Low Volume (1-50 parts) | Manual lathe, basic CNC lathe |
Medium Volume (50-500 parts) | CNC lathe, turret lathe |
High Volume (500+ parts) | CNC lathe with automation, turret lathe |
6. Automation and Flexibility
Automation plays an increasingly important role in modern manufacturing. CNC lathes offer high levels of automation, which can reduce the need for manual intervention, decrease errors, and improve production efficiency.
- CNC Lathes with Automation: CNC lathes equipped with robotic loading/unloading systems, tool changers, and live tooling are ideal for high-volume production with minimal operator intervention. These systems provide flexibility for complex parts and allow for multiple operations to be performed in a single setup.
- Manual Lathes for Flexibility: Manual lathes offer more flexibility for smaller, custom jobs where setup time and precision requirements are lower. They are ideal for shops that handle a wide variety of different parts in small quantities.
7. Cost Considerations
Finally, cost is always an important factor. Lathes vary widely in price depending on their capabilities, size, and level of automation.
- Manual Lathes: Typically, the most affordable option, manual lathes are best for small shops or operations with a lower budget and less stringent precision requirements.
- CNC Lathes: More expensive but capable of higher precision and efficiency, CNC lathes are an investment for shops that prioritize automation and productivity.
- Turret and Specialty Lathes: These machines tend to be on the higher end of the price spectrum due to their ability to handle large production volumes and specialized tasks.
Lathe Type | Price Range |
---|---|
Manual Lathe | $5,000 – $30,000 |
CNC Lathe | $50,000 – $500,000+ |
Turret Lathe | $100,000+ |
Choosing the right lathe for your project depends on several key factors, including the size and complexity of the workpiece, the material being machined, precision requirements, production volume, and cost considerations. By evaluating these aspects carefully, you can select a lathe that meets your specific needs, ensuring optimal performance, efficiency, and quality in your machining operations.
What Are the Safety Precautions for Using a Lathe?
Operating a lathe requires strict attention to safety procedures due to the inherent risks involved with rotating parts, sharp cutting tools, and high-speed operations. Whether using a manual lathe or a CNC lathe, understanding and following key safety protocols is essential for preventing accidents, protecting the operator, and ensuring a secure working environment. In this chapter, we will cover the critical safety precautions necessary when working with a lathe, from proper personal protective equipment (PPE) to machine maintenance and operational guidelines.
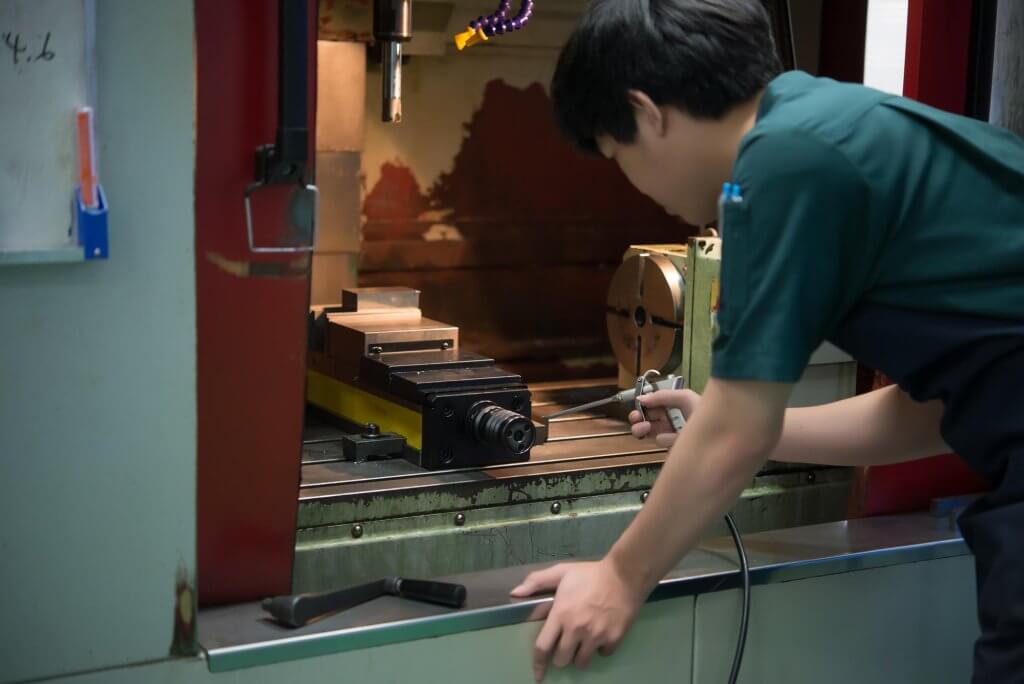
1. Personal Protective Equipment (PPE)
Wearing the correct personal protective equipment (PPE) is the first and most essential step in maintaining safety during lathe operations. The right gear ensures that operators are protected from flying debris, sharp objects, and potential hazards associated with machine operation.
- Safety Glasses or Goggles: Always wear safety glasses or goggles to protect your eyes from metal chips, dust, and debris. Flying particles are common when machining, and even small fragments can cause serious eye injuries.
- Face Shield: In addition to safety glasses, a face shield offers extra protection, especially during high-speed operations or when machining hard materials like steel or titanium.
- Hearing Protection: Lathes can produce significant noise levels, particularly during heavy cutting operations. Hearing protection, such as earplugs or earmuffs, is recommended to prevent hearing damage, especially in noisy workshops.
- Appropriate Clothing: Avoid wearing loose-fitting clothing, long sleeves, ties, or jewelry that could get caught in moving parts. Fitted clothing reduces the risk of entanglement. Additionally, long hair should be tied back securely.
- Gloves: While gloves are useful for handling raw materials, they should never be worn while the lathe is in operation. Gloves can easily get caught in rotating parts, leading to serious injury.
- Steel-Toe Boots: To protect your feet from heavy objects that might fall, especially during material setup or removal, wearing steel-toe boots is recommended.
2. Lathe Machine Guards and Shields
Lathe machines come equipped with guards and shields designed to protect operators from potential hazards, such as rotating parts and flying debris. It is important to ensure that these guards are correctly positioned and used during every operation.
- Chuck Guard: The chuck is a key rotating component that holds the workpiece in place. The chuck guard prevents accidental contact with the rotating chuck and shields the operator from flying debris. Always ensure that the chuck guard is securely in place before starting the machine.
- Tool Post Guard: This guard protects the area around the tool post, where cutting tools are mounted. Chips and small fragments can fly off during machining, and the guard helps to prevent these from reaching the operator.
- Splash Guard: If coolant is being used during the machining process, a splash guard helps to contain any splashing of coolant or chips that could strike the operator.
- Emergency Stop Button: Every lathe should be equipped with an easily accessible emergency stop button. This button allows for immediate shutdown of the lathe in case of a malfunction or unexpected situation, preventing further accidents.
3. Pre-Operation Inspection
Before starting any lathe operation, conducting a thorough pre-operation inspection is crucial for ensuring that the machine is in proper working order. A checklist of key items to inspect includes:
- Check for Loose Parts: Make sure that the chuck, tool post, and tailstock are all securely fastened. Loose components can cause instability during machining, leading to accidents or poor-quality results.
- Inspect Tools: Before use, check all cutting tools for signs of wear, chips, or cracks. A damaged tool can break during operation, creating hazardous flying debris.
- Workpiece Setup: Ensure that the workpiece is securely mounted in the chuck and properly centered. An unbalanced or loosely held workpiece can wobble or even be ejected during rotation, posing a serious danger to the operator.
- Lubrication and Coolant: Verify that the lathe is properly lubricated and that the coolant system (if applicable) is functioning. Lubrication helps reduce friction and wear, while coolant prevents overheating and prolongs tool life.
- Speed and Feed Settings: Double-check that the correct speed and feed rates are selected based on the material and type of operation. Incorrect settings can lead to tool breakage or poor-quality finishes.
4. Safe Operating Procedures
Once the machine has passed inspection and the workpiece is securely in place, it’s important to follow safe operating procedures to minimize risk during lathe operations.
- Never Leave the Machine Unattended: Always remain near the lathe while it is running. Leaving a machine unattended, even briefly, can lead to unexpected accidents or damage to the workpiece.
- Keep Hands Away from Moving Parts: Never attempt to adjust the tool or workpiece while the lathe is in operation. Keep hands and fingers away from rotating parts to avoid injury.
- Remove the Chuck Key Immediately: After tightening the chuck, immediately remove the chuck key. Accidentally leaving the chuck key in place when starting the lathe can cause it to be thrown at high speed, potentially causing serious injury.
- Control Chip Formation: During machining, long, continuous chips can form, especially when working with softer materials. These “bird nests” of chips are hazardous and should be cleared regularly using a chip brush or air blower, not your hands. Proper chip-breaking techniques and tools should be employed to prevent long chip formation.
- Turn Off the Machine Before Adjusting: Always turn off the lathe completely before making any adjustments to the tool, chuck, or workpiece. Attempting to make adjustments while the machine is running can lead to accidents.
5. Post-Operation Safety
After completing lathe operations, certain steps must be taken to ensure the safety of both the operator and the machine. Following these post-operation procedures is critical for maintaining a safe work environment.
- Turn Off and Unplug the Machine: After finishing the job, turn off the lathe and, if applicable, unplug it before performing any cleanup or maintenance. This prevents accidental startups while cleaning or servicing the machine.
- Remove Cutting Tools: Once the operation is complete, remove the cutting tools from the tool post. This reduces the risk of injury during machine cleanup or when setting up for the next job.
- Clean the Lathe: Remove any chips, debris, and coolant residue from the lathe bed, carriage, and surrounding area. A clean machine not only prevents accidents but also helps maintain the longevity of the lathe.
- Inspect the Machine: After each operation, check the lathe for any signs of wear or damage. Catching issues early can prevent more serious malfunctions down the line and help avoid costly repairs.
6. Lathe Maintenance for Safety
Regular lathe maintenance is essential not only for optimal performance but also for ensuring a safe working environment. By keeping the lathe in good condition, you reduce the likelihood of mechanical failure that could lead to accidents.
- Lubrication: Keep the lathe well-lubricated, following the manufacturer’s specifications. Proper lubrication prevents wear on moving parts, reduces friction, and ensures smooth operation.
- Check for Wear: Periodically inspect critical components such as the bearings, belts, and gears for signs of wear. Worn-out parts should be replaced immediately to avoid machine breakdowns or unsafe working conditions.
- Electrical System: Regularly check the lathe’s electrical system, including wiring, switches, and emergency stop functions. Faulty wiring or malfunctioning controls pose serious safety hazards.
- Calibration: Regularly calibrate the lathe’s settings and measuring instruments to maintain precision and accuracy. Improper calibration can lead to poor part quality and increase the risk of operator error.
7. Training and Awareness
Proper training and awareness are key elements of lathe safety. Operators must be fully trained in the use of the specific lathe they are working on, including both manual and CNC models.
- Operator Training: All operators should receive thorough training on the lathe’s operation, including how to safely set up, operate, and shut down the machine. Training should cover emergency procedures, safe handling of materials, and proper use of personal protective equipment.
- Awareness of Hazards: Operators must be aware of the hazards involved in lathe operations, such as flying debris, sharp edges, and rotating parts. They should know how to mitigate these risks through proper procedures and the use of guards and safety equipment.
- Ongoing Safety Education: Safety training should be an ongoing process. Regular safety meetings, workshops, and refresher courses help ensure that all operators stay up-to-date with the latest safety protocols and practices.
Safety is paramount when working with lathes. By adhering to proper safety precautions, such as wearing personal protective equipment, using machine guards, performing regular inspections, and following safe operating procedures, operators can significantly reduce the risk of accidents and injuries. Additionally, proper maintenance and ongoing training ensure that both the lathe and its operator remain in top condition, fostering a safe and productive working environment.
What Maintenance is Required for a Lathe?
Maintaining a lathe is critical to ensuring its longevity, efficiency, and precision. Regular maintenance not only prevents costly breakdowns but also ensures that the machine operates safely and consistently. Whether you’re using a manual or CNC lathe, following a strict maintenance schedule is key to optimizing performance. This chapter will explore the essential maintenance tasks required to keep a lathe in top condition, including daily, weekly, and periodic checks.
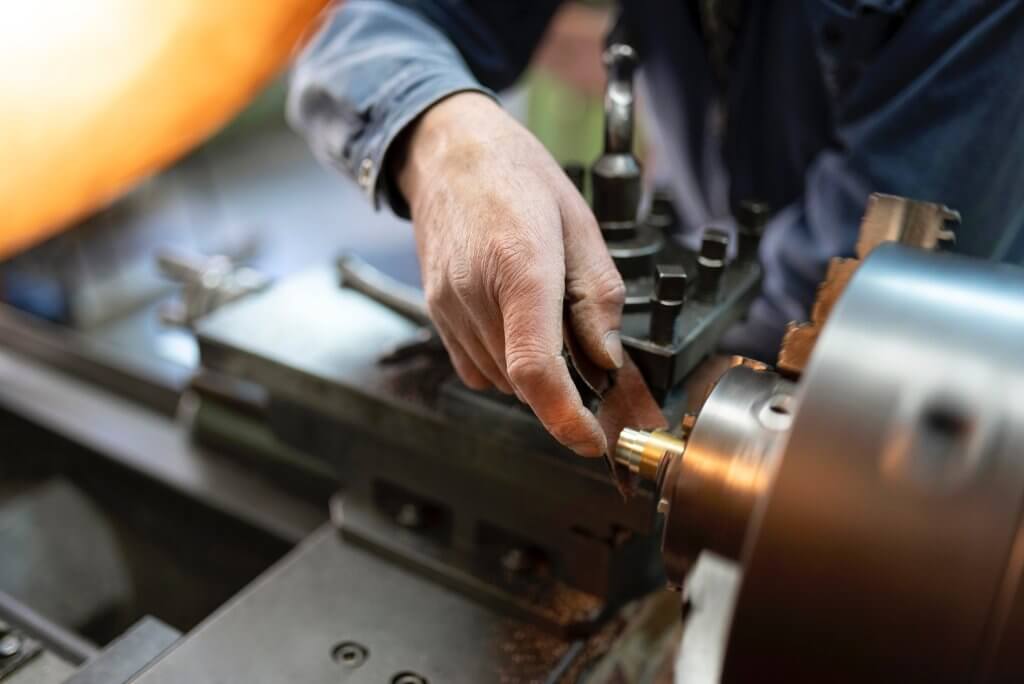
1. Daily Maintenance
Daily maintenance is essential for keeping your lathe in good working order and preventing minor issues from escalating into major problems. Most daily tasks involve cleaning and inspection, which ensures that the machine is free of debris and that any signs of wear or damage are addressed promptly.
- Cleaning the Machine: After each use, clean the lathe thoroughly. Metal chips, dust, and coolant residue can build up in the lathe bed, carriage, and tailstock areas, potentially causing damage over time. Use a brush or compressed air to remove chips from the bed and components, but avoid using compressed air near delicate electrical components to prevent contamination.
- Lubrication: Ensure that all moving parts, such as the carriage, lead screws, and ways, are well-lubricated. Lubrication reduces friction between moving parts and prevents premature wear. Always use the manufacturer-recommended lubricants for the machine’s specific parts.
- Inspect for Wear: Visually inspect the machine for any signs of wear or damage. Pay close attention to critical areas such as the chuck, tool post, and spindle bearings. Any unusual noise, excessive vibration, or looseness in these components could indicate wear that needs attention.
- Check the Coolant System: If your lathe uses coolant, check the coolant level and ensure the system is operating efficiently. Dirty or low coolant can lead to overheating of the workpiece or excessive wear on the cutting tools.
- Tighten Loose Parts: Check and tighten any loose fasteners, especially around the tool post, chuck, and tailstock. Loose parts can lead to inaccuracies during machining and pose safety hazards.
2. Weekly Maintenance
Weekly maintenance tasks involve deeper inspections and more thorough cleaning, targeting areas that may not require daily attention but still need regular care to ensure the lathe’s long-term reliability.
- Inspect the Belts and Pulleys: Check the condition of the drive belts for any signs of wear, cracks, or fraying. Proper belt tension is crucial for smooth operation. If the belts appear damaged, replace them immediately to avoid breakdowns during operation.
- Check Gibs and Ways for Alignment: The gibs and ways are critical for smooth, precise movement of the carriage and cross-slide. Inspect these components for alignment and wear. If you notice any rough movement or slop, adjust the gibs according to the machine manual.
- Test the Electrical System: Ensure that all electrical connections, switches, and controls are functioning properly. Loose or damaged wiring can lead to machine failure or even pose a fire hazard. Test emergency stop functions to ensure they work as intended.
- Clean and Refill the Coolant Tank: Depending on how frequently the lathe is used, the coolant tank may need to be drained and refilled weekly. Dirty or contaminated coolant can clog the system and reduce cooling efficiency, leading to tool wear and poor surface finishes.
3. Monthly Maintenance
Monthly maintenance focuses on more detailed inspections of the lathe’s critical systems. These checks can identify potential problems before they become major issues, ensuring that the machine continues to perform optimally.
- Spindle Alignment Check: Over time, heavy use can cause the spindle to lose alignment with the tailstock or the lathe bed. Misalignment can affect the accuracy of the machine and the quality of the workpieces. Use a dial indicator to check spindle alignment and adjust if necessary.
- Test the Chuck and Jaws: The chuck is one of the most important components of the lathe, holding the workpiece in place during machining. Inspect the chuck and its jaws for wear and ensure they are functioning smoothly. If the jaws are not gripping the workpiece securely, replace or adjust them.
- Examine the Gearbox and Leadscrew: The gearbox and leadscrew control the speed and precision of the lathe’s operations. Inspect the gears for any signs of wear, such as chipped teeth or unusual noise during operation. Lubricate the leadscrew to ensure smooth movement and consistent accuracy.
- Tailstock Maintenance: The tailstock is often overlooked but plays a crucial role in supporting long workpieces. Check the tailstock for proper alignment and ensure the quill operates smoothly without excessive play.
4. Semi-Annual or Annual Maintenance
Some maintenance tasks need to be performed less frequently but are critical to ensuring the machine’s long-term durability and precision. These include full inspections of the machine’s key systems and more in-depth calibration.
- Complete Machine Calibration: Over time, the lathe’s components can drift out of alignment due to wear and heavy use. Semi-annual or annual calibration ensures that the machine maintains its accuracy. This involves checking the alignment of the headstock, tailstock, and cross-slide, as well as adjusting the gibs and leadscrews.
- Bearing Inspection and Replacement: Spindle bearings undergo a lot of stress, especially during heavy or high-speed machining. Inspect the spindle and motor bearings for any signs of wear, noise, or heat buildup. Replace bearings if necessary to avoid future breakdowns.
- Replace the Drive Belts: Even if the belts appear to be in good condition, it’s advisable to replace them periodically (typically annually) to avoid sudden failures during critical operations.
- Check and Replace Filters: If your lathe uses a coolant filtration system or air filtration for dust and particles, check and replace the filters regularly. Clean filters ensure that the coolant remains effective and the machine components are protected from contamination.
5. CNC Lathe-Specific Maintenance
CNC lathes require additional maintenance due to their more complex electronic and mechanical systems. Regular upkeep of the CNC components ensures that the machine can perform highly automated and precise tasks without interruption.
- Inspect and Clean the CNC Control Panel: Keep the control panel free of dust and grime. Ensure that all buttons, switches, and displays are functioning properly. Faulty controls can lead to incorrect machine operation, resulting in faulty parts or machine crashes.
- Check Servo Motors and Drives: Servo motors control the precise movement of the machine’s axes. Inspect the servo motors and their drives for any signs of overheating, noise, or irregular movement. Faulty servo motors can lead to inaccuracies in part production or machine breakdowns.
- Backup CNC Programs: Regularly back up your CNC programs and machine settings to avoid data loss in case of a system failure. This is especially important if you rely on highly customized programs for production.
- Update CNC Software and Firmware: Keep your CNC software and firmware up to date with the latest versions provided by the manufacturer. Updated software often includes bug fixes, performance improvements, and enhanced security features.
6. Preventive Maintenance Schedule
Following a preventive maintenance schedule ensures that all the necessary tasks are completed on time. This schedule should be customized based on the type of lathe you use, the frequency of operation, and the specific demands of your work environment. A well-maintained machine will operate more efficiently, produce higher quality parts, and reduce the likelihood of unexpected breakdowns.
- Daily Tasks: Cleaning, lubrication, basic inspections.
- Weekly Tasks: Deeper cleaning, checking belts and gibs, testing electrical systems.
- Monthly Tasks: Chuck and spindle inspection, alignment checks, gear inspection.
- Semi-Annual/Annual Tasks: Full calibration, bearing checks, filter and belt replacement, CNC system maintenance.
Proper maintenance is essential for keeping a lathe in excellent working condition and ensuring it operates safely and efficiently. Daily, weekly, monthly, and annual tasks help prevent breakdowns, extend the machine’s lifespan, and maintain its accuracy. Whether you’re working with a manual lathe or a sophisticated CNC model, following a strict maintenance schedule is key to achieving consistent performance and high-quality results in machining operations.
What Industries Rely on Lathe Machining?
Lathes are indispensable tools across a wide range of industries due to their ability to produce high-precision parts with great efficiency. From manufacturing tiny, intricate components to large-scale industrial parts, lathes are widely used in various sectors that demand precision, versatility, and reliability. In this chapter, we will explore the industries that rely heavily on lathe machining, highlighting the specific applications and contributions of lathe technology to each field.
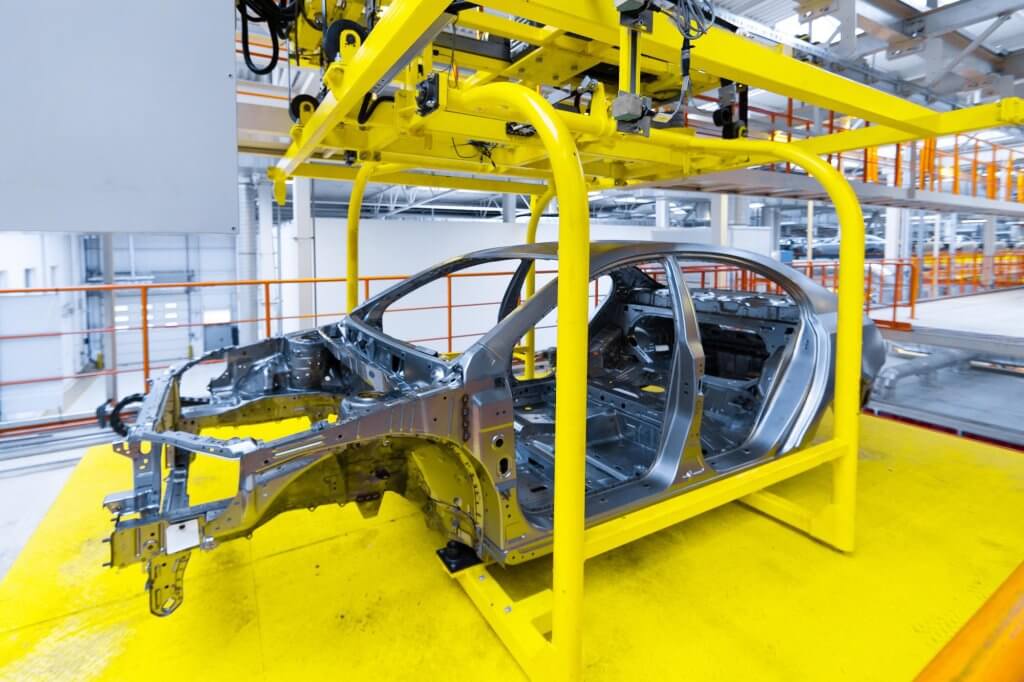
1. Automotive Industry
The automotive industry is one of the largest users of lathe technology. Lathes are used extensively to manufacture critical components that require high precision, durability, and adherence to tight tolerances. Given the complex mechanical systems in vehicles, lathe machining plays a key role in producing essential parts.
- Applications in Automotive:
- Engine Parts: Lathes are used to machine engine parts such as camshafts, crankshafts, pistons, and cylinder liners. These components must meet stringent specifications to ensure the engine operates smoothly and efficiently.
- Transmission Components: Lathe machining is integral in producing gears, shafts, and bearings, which are critical for vehicle transmissions. Accurate machining ensures proper gear meshing and performance.
- Brake Systems: Components like brake discs and drums are machined on lathes to achieve the necessary surface finish and concentricity, ensuring reliable braking performance.
Lathes are vital in the production of parts that require high strength and precision, making them indispensable to the automotive manufacturing process.
2. Aerospace Industry
In the aerospace industry, where safety, reliability, and precision are non-negotiable, lathes play a crucial role in manufacturing components for aircraft, spacecraft, and defense applications. The ability to machine high-performance materials like titanium and aluminum to exact specifications makes lathes a cornerstone of aerospace manufacturing.
- Applications in Aerospace:
- Engine Components: Turbine blades, shafts, and engine casings are machined on lathes, requiring exacting tolerances and the ability to withstand extreme temperatures and pressures.
- Landing Gear: The production of landing gear parts involves machining strong, durable materials like titanium or high-strength steel, making lathes essential for their fabrication.
- Fasteners and Connectors: Aerospace-grade fasteners and connectors, which hold together the aircraft’s structure, are often manufactured using CNC lathes due to the high precision required.
The aerospace industry often works with exotic materials and complex geometries that demand advanced CNC lathes capable of multi-axis machining and high tolerance control.
3. Medical Device Industry
The medical device industry relies on lathe machining for the production of intricate and high-precision parts used in a variety of medical applications. The parts made on lathes need to meet the stringent standards of the healthcare sector, where even minor deviations can affect device performance and patient safety.
- Applications in Medical Devices:
- Surgical Instruments: Lathes are used to manufacture precise surgical tools like scalpels, forceps, and bone drills, which must meet exact specifications for both form and function.
- Orthopedic Implants: Components such as knee and hip joint replacements, bone screws, and dental implants are often machined from titanium or surgical-grade stainless steel using CNC lathes.
- Medical Equipment Components: Parts for medical diagnostic machines, such as MRI or CT scanners, often require high-precision machined components for the mechanical and functional aspects of these devices.
In the medical field, biocompatibility and precision are critical, and lathes provide the necessary control over the machining process to ensure that all parts meet strict regulatory and performance standards.
4. Oil and Gas Industry
The oil and gas industry requires robust and durable components capable of operating in harsh environments. Lathes are frequently used to machine parts that must withstand high pressures, temperatures, and corrosive conditions, making precision and material integrity vital.
- Applications in Oil and Gas:
- Drill Bits and Downhole Tools: Lathe machining is used to manufacture complex drill bits and downhole tools that can endure the extreme conditions found in oil drilling operations.
- Valve Components: Lathes are essential for machining valve bodies, stems, and seats used in oil and gas pipelines. These components need to have precise fits to prevent leaks and ensure safe operation.
- Pump Shafts: Machining pump shafts with tight tolerances ensures that oil extraction and pumping operations run smoothly and efficiently.
Given the high stakes and challenging environments in oil and gas exploration, lathes help produce the highly durable and precise components required for safety and performance.
5. Electronics Industry
In the electronics industry, the demand for miniaturization and precision has led to the widespread use of CNC lathes for producing small, intricate parts with tight tolerances. Lathes are used in the production of components for consumer electronics, telecommunications equipment, and more.
- Applications in Electronics:
- Connector Pins: Lathes are used to manufacture small, precision connector pins for electronics that require high accuracy for proper electrical contact.
- Housings and Enclosures: Lathes are involved in creating housings and enclosures for electronic devices, such as smartphones, laptops, and cameras, which must meet aesthetic and dimensional requirements.
- Semiconductor Equipment Parts: Components used in the machines that manufacture semiconductors are often machined with CNC lathes to ensure that they meet the exacting standards required for semiconductor production.
The need for precision and reliability in electronic components makes lathe machining a key part of the electronics manufacturing process.
6. Defense and Military Industry
The defense and military industry depends on lathe machining for producing a variety of components used in weapons systems, vehicles, and defense equipment. Precision, strength, and reliability are critical requirements for military-grade parts.
- Applications in Defense:
- Firearms Components: Lathes are used to manufacture barrels, bolts, and other firearm components that require high precision and strength.
- Missile and Rocket Components: Complex parts such as rocket nozzles, casings, and guidance system components are often machined on CNC lathes.
- Military Vehicle Parts: Lathes are used to produce parts for tanks, armored vehicles, and aircraft that require high durability and precision.
In defense applications, components must meet rigorous specifications and withstand extreme conditions, making precision machining a vital part of the production process.
7. Power Generation Industry
The power generation industry uses lathes for manufacturing parts in power plants, including both conventional and renewable energy sectors. These components must operate under high stress and with minimal failure.
- Applications in Power Generation:
- Turbine Components: Lathes are used to machine blades and rotors for steam, gas, and wind turbines. These parts must have exact dimensions to ensure efficient energy generation.
- Generator Shafts: Machining the shafts used in generators requires precision to ensure balanced rotation and longevity in operation.
- Nuclear Power Components: In nuclear power plants, lathe machining is used to manufacture critical parts that must withstand radiation, high temperatures, and pressures.
The high reliability requirements in power generation make precision machining indispensable for producing components that ensure uninterrupted energy supply.
Lathe machining is foundational to a wide array of industries, from automotive to aerospace, medical devices, and beyond. Each of these industries depends on the precision, flexibility, and reliability that lathes provide in manufacturing parts that meet strict tolerances and operational demands. As industries continue to evolve, particularly with advancements in materials and technology, lathe machining will remain integral to producing the high-quality components needed across various sectors.
FAQ
1. What are the advantages of using a CNC lathe over a manual lathe?
A CNC lathe offers automation, higher precision, and the ability to handle complex operations that would be difficult on a manual lathe. CNC lathes can run multiple operations in a single setup with minimal human intervention, making them ideal for high-volume production and parts with intricate geometries. They also provide better repeatability and consistency, reducing errors and improving overall part quality.
2. How can I determine the right spindle speed for my material?
Spindle speed depends on the material being machined and the cutting tool used. Harder materials like steel require lower spindle speeds, while softer materials like aluminum or plastics can handle higher speeds. Manufacturers often provide recommended speed ranges for different materials, or you can use the formula ( \text{RPM} = \frac{1000 \times \text{Cutting Speed}}{\pi \times \text{Workpiece Diameter}} ) to calculate it. CNC lathes automatically adjust speeds based on pre-programmed parameters.
3. What is live tooling in CNC lathe operation?
Live tooling refers to the use of powered tools in a CNC lathe that allows for milling, drilling, and tapping operations in addition to turning. This eliminates the need to move the workpiece to a separate milling machine, improving efficiency and reducing cycle times. Live tooling is particularly useful for parts that require features like slots, holes, or flat surfaces in addition to cylindrical machining.
4. What is the difference between rough turning and finish turning?
Rough turning is the process of removing large amounts of material quickly to bring the workpiece close to its final dimensions. Finish turning, on the other hand, involves removing smaller amounts of material to achieve the final size, surface finish, and precision. Rough turning typically uses higher cutting speeds and larger depth of cuts, while finish turning prioritizes accuracy and surface quality.
5. How can I reduce vibration during lathe operations?
To reduce vibration during lathe operations, ensure the workpiece is properly balanced and securely mounted in the chuck. Using sharp tools, reducing the depth of cut, and optimizing spindle speed can also help minimize vibration. In some cases, using a tailstock or steady rest to support long workpieces can improve stability. Additionally, ensuring the machine is properly leveled and all components are tightened can prevent excess vibration.
6. What types of cutting tools are used in lathe machining?
Lathe cutting tools come in various shapes and materials, each suited for specific tasks. Common tools include carbide-tipped tools, high-speed steel (HSS) tools, and ceramic or diamond-tipped tools for machining harder materials. Tools are typically classified based on their shape (e.g., turning, boring, threading, or parting tools) and their application (roughing or finishing). Each material and tool shape is designed to optimize performance based on the workpiece material and operation.
7. What is a steady rest and when should it be used?
A steady rest is a support device used in lathe operations to stabilize long or thin workpieces that tend to deflect or vibrate under cutting forces. It prevents workpiece flexing and helps maintain precision by providing additional support along the length of the workpiece. Steady rests are particularly useful when turning slender shafts, long rods, or tubing.
8. How can I prevent tool wear in lathe machining?
Tool wear can be minimized by using proper cutting speeds, feed rates, and lubrication. Ensuring that the cutting tool is sharp and made from the appropriate material (e.g., carbide for hard materials) also helps prolong tool life. Using coolant during operations helps reduce heat buildup, which is a common cause of tool wear. Regularly inspecting and replacing worn tools will prevent excessive tool wear from affecting part quality.
9. What is the importance of tool geometry in lathe operations?
Tool geometry refers to the shape and angles of the cutting tool, such as the rake angle, clearance angle, and cutting edge. Proper tool geometry ensures efficient material removal and reduces cutting forces, heat generation, and tool wear. Different materials require different tool geometries; for example, softer materials may require a larger rake angle to ensure smooth cutting, while harder materials need sharper, stronger cutting edges.
10. Can lathes be used for thread cutting?
Yes, lathes are commonly used for cutting both internal and external threads on cylindrical parts. Thread cutting can be done manually on a standard lathe or automatically on a CNC lathe. The tool follows the thread lead and pitch as specified in the part design, ensuring the correct helical shape is formed on the workpiece. CNC lathes offer more precise thread cutting capabilities, especially for complex or high-precision threads.
11. What coolant types are used in lathe machining, and when should they be applied?
There are several types of coolants used in lathe machining, including water-based coolants, oils, and synthetic fluids. Coolant helps reduce heat buildup, improve surface finish, and extend tool life. Water-based coolants are common for general-purpose machining, while oil-based coolants are used for high-pressure or fine-finishing operations. The choice of coolant depends on the material being machined and the type of cutting tool used.
12. What is backlash in a lathe and how can it affect machining?
Backlash refers to the slight movement between machine components, such as the lead screw and nut, when the direction of motion is reversed. This can cause inaccuracies in machining, especially in precision applications. Backlash can be minimized by properly adjusting or replacing worn components, using anti-backlash nuts, and utilizing software compensation in CNC lathes.
13. What is taper turning and how is it done on a lathe?
Taper turning is the process of producing a conical shape on a workpiece where the diameter changes gradually along its length. This can be done by adjusting the tailstock, using the compound slide at an angle, or setting the machine to a specific taper attachment. Tapered parts are common in machine tools, automotive components, and specialized fittings.
14. How do I select the right cutting fluid for my lathe operations?
Choosing the right cutting fluid depends on the material being machined and the type of cutting operation. Water-soluble coolants are effective for general-purpose machining, while oils or synthetic fluids may be better for high-speed or precision finishing. Cutting fluids help to cool the tool and workpiece, remove chips, and improve surface finishes. It’s important to match the coolant type with the specific material, such as using oil-based fluids for steel and water-based fluids for aluminum.
15. What are some common lathe problems and their solutions?
Common lathe problems include chatter (vibration during cutting), tool wear, poor surface finish, and misalignment of the workpiece. Solutions include using a sharper cutting tool, adjusting the spindle speed, reducing the depth of cut, and ensuring the workpiece is properly centered and balanced. Regular maintenance, such as lubrication and inspection of machine components, can also prevent these issues.
16. How can I improve the surface finish of my lathe parts?
To improve surface finish, ensure that your cutting tool is sharp and appropriate for the material being machined. Reduce feed rates, adjust spindle speed, and minimize depth of cut for a smoother finish. Using a proper cutting fluid and ensuring the workpiece is free of vibration or chatter will also improve the final surface quality. Additionally, performing a final pass with a fine feed rate or polishing operation can help achieve a better surface.
Other Articles You Might Enjoy
- Is Grizzly Lathe the Right Choice for Your CNC Needs
In the world of machining, selecting the right lathe for your projects can be a crucial decision, especially if you're considering a versatile tool like the Grizzly lathe. This machine…
- JET Lathe Models for CNC: A Complete Selection Guide
In the world of CNC machining, the right lathe model can make all the difference. For many users, JET lathes offer a blend of reliability, precision, and durability. However, with…
- Choosing a Lathe Chuck for CNC: Essential Tips and Techniques
Introduction to Lathe Chucks in CNC Machining In CNC machining, the lathe chuck plays an indispensable role in holding and securing workpieces for accurate and efficient production. The lathe chuck’s…
- Ultimate Showdown: CNC Lathe vs. CNC Turning Center – A Comprehensive Analysis
Introduction to CNC Machinery and Core Differences Between CNC Lathes and Turning Centers CNC (Computer Numerical Control) machinery represents the pinnacle of precision engineering, utilizing computerized systems to control machining…
- Precision Machining with Tool Offsets for CNC Lathe Parts
When it comes to CNC machining, precision is key. Achieving high precision in CNC lathe parts requires a deep understanding of tool offsets and their functions. Let's dive into the…
- Exploring the World of CNC Machining Parts: From Mills to Lathes
In today's manufacturing world, CNC (Computer Numerical Control) machines are indispensable. These high-tech machines are capable of producing incredibly precise and complex parts, making them essential for industries ranging from…
- Diversity in CNC Machining Parts: From Standard Lathes to Multi-Axis Turning Centers
Walk into any machine shop, and you'll likely see a variety of lathes humming away. These versatile machines are the backbone of many manufacturing processes, especially when it comes to…
- Workpiece Sketching and Calculations in CNC Machining Parts
In CNC machining, the accuracy and efficiency of the final product often hinge on the initial planning and calculations. One of the critical steps in this process is creating detailed…