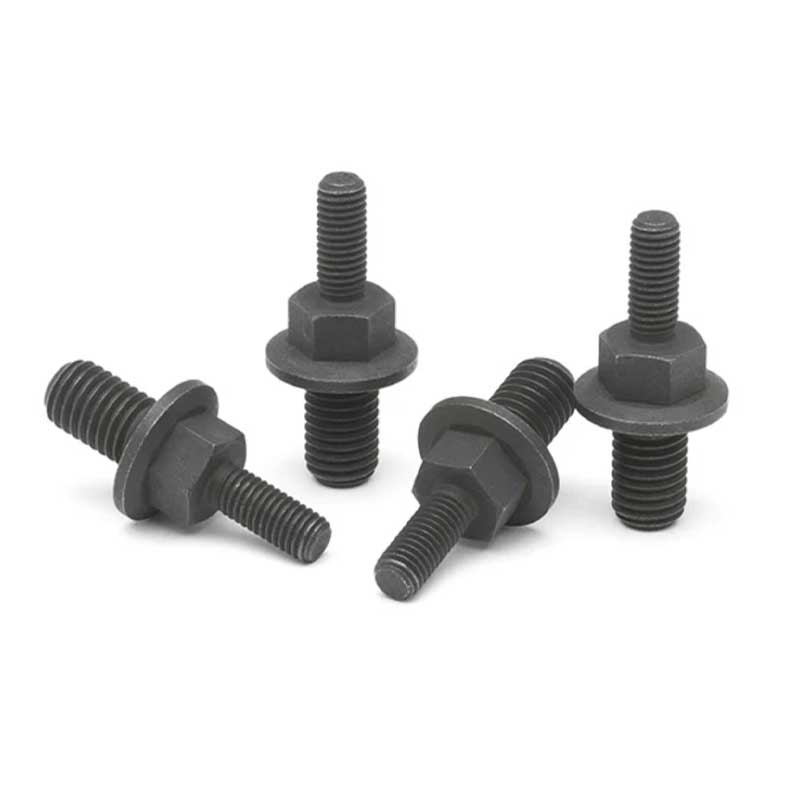
Home » CNC Machining » CNC Machined Parts » Heatsinks
Custom machined heatsinks are specialized heat dissipation devices created through CNC machining processes, tailored to specific requirements in terms of size, shape, and material. These heatsinks are designed for particular applications, such as electronics, automotive, or industrial equipment, where standard heatsinks may not be adequate. Custom machining allows for precise control over intricate features, such as fins or grooves, which enhance the heatsink’s cooling efficiency. By using materials like aluminum or copper, custom machined heatsinks offer optimized thermal performance to meet demanding operational conditions.
At our machining facility, we understand the vital role that precise custom heatsinks play in diverse industries. These heatsinks are meticulously engineered to meet exact specifications, ensuring optimal thermal performance, reliability, and durability in demanding applications. Whether you need custom heatsinks for automotive, aerospace, industrial, or other sectors, our expertise and capabilities allow us to deliver outstanding results tailored to your needs.
each with its unique challenges and requirements for precision, material handling, and surface treatment. Here’s a further breakdown of each challenge with some additional context on optimizing processes:
To add to your comparison, adaptive machining (real-time toolpath adjustments) and high-speed machining can further improve tolerance and surface finish, especially in high-stability machines designed for intricate work.
Each technique in the CNC process, when strategically chosen and combined, allows engineers to push the limits of heatsink performance while managing the inherent challenges of each material and design constraint.
Our manufacturing services are backed by advance inspection equipments. Take a closer look at our quality inspection process.
You’re one step from the factory-direct price of part manufacturing services.