Part production requires metal surface finishing. Quality metal surface finishing will make any part look better, no matter how well it is finished.
There are many types of metals. Welder fabricators and machining manufacturers use different metal finishing techniques. Uncertainty about the right metal finishing techniques can lead to material loss and increase manufacturing costs. That could also lead to a longer production time. You need to properly finish your product to avoid these issues.
We cover everything about metal surface finishes in this post to help you build a better understanding of them.
The basic concept of Surface finishes
Surface finishing can also refer to surface texture, roughness, or topology. This name is enough to explain what surface finishing stands for. This is the act of changing a metal’s surface by adding, removing, or reshaping. Machinists use metal surface finishing to beautify and protect metal surfaces from chemical reactions.
Choosing the right metal finish is as important as the metal itself. The product’s intended use will determine the type of finish used. Medical-grade and optical instruments, for example, require the best surface finishing. Other industries and applications may not need such fine finishing.
Why Surface Finishes is important
Machinists do not use surface finishes for aesthetic purposes only. They are also used to protect the metal.
Surface finishes offer many exciting benefits, such as:
It enhances aesthetics
The product’s aesthetics are just as important as its performance to clients. Your metal surface will look great with metal surface finishing.
Surface finishes increase the metal’s resistance against corrosion
Corrosion is the number one killer of metal surfaces and components. A well-done finish can protect the metal surface and make it last longer.
Facilitate the manufacturing process
Surface finishing is key to making the manufacturing process more efficient. A well-brushed and sandpapered surface makes it easier to adhere to paints, which relieves the manufacturer of stress.
- Surface finishes can improve the conductivity of metals
- It protects it from chemical attack by increasing its surface resistance to chemicals
- It improves strength and resistance to wear
- Good surface finishing helps reduce friction
Metal Surface Finishes
You have many options for choosing the right metal finish for your next project. The type of project you are working on will determine the type of finish that you choose. Here are some common metal surfaces you should be aware of:
Anodizing
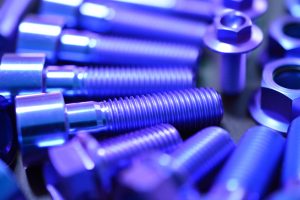
Machining manufacturer use this electrolytic passivation process to increase the thickness of the natural oxide layer on metal surfaces. To increase the resistance to corrosion and wear Machinists anodize metallics. This allows primers and glues to adhere more easily to metal surfaces than normal metals. Anodizing a metal would alter the microstructure of the metal’s surface. Anodized metal surfaces appear to be more durable than normal metal surfaces.
Powder Coating
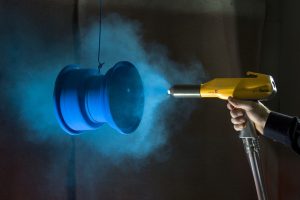
This method uses electricity to deposit dry powder on the surface of the metal. The machinist electrostatically deposits the powder onto the surface and then moves the metal into an oven for better adhesion.
This metal finish is used extensively in the military, automotive, and tool manufacturing industries.
Pickling
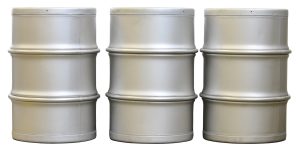
This is a process for removing impurities and irregularities from metal surfaces. Pickle liquor is required for this method. This acidic substance is called pickle liquor. Pickle liquor can be used for many purposes, including preventing metal corrosion. Machining manufacturers use pickling in all aspects of metal manufacturing. An oxide layer may form if a metal is heated during metal fabrication.
Pickling is a great solution. Pickling helps smoothen the surface by removing any traces of dirt. Pickling can also lead to corrosion due to its acidic nature. Pickling should be done before any other surface treatment. These will eliminate any problem that may arise during pickling.
Polishing
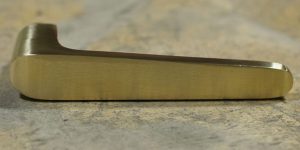
Polishing refers to creating shiny metal surfaces using chemicals or physical rubbing.
Grinding

Grinding is a common machining process that removes irregularities from a metal surface. This process is used by manufacturers after construction, before coating or painting. The grinding process smoothens the metal surface using a hand-held machine called a grinder or a wheel.
Some common metals that pass through the grinding process are aluminum, mild steel, and cast iron.
Lapping
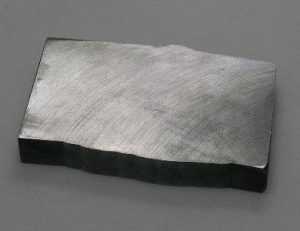
This precision technique is used when a metal surface needs to be flat and refined. Lapping is a skilled metal finishing technique. You will use a soft iron tool and a mild abrasive solution to smoothen the metal surface. Lapping does not require any special equipment. It can be done by hand on small parts of metal. Lapping correctly will fill in tiny holes and smoothen out irregular surfaces.
How to Measure Surface Finish
Measurement of the metal’s surface roughness is necessary to determine its surface finish. You must examine the surface and analyze the irregularities.
Two common methods to identify irregularities are:
Use a surface roughness comparator
First, you will need to use a surface roughness comparator. This is a manual process, so it has low accuracy. For common finishing processes such as casting, shot blasting, and grit blasting, the surface turned, cylindrical grounded, conventional machining, and electrical discharge machining, roughness comparators can be used.
Use a surface profile scanner
A surface profile scanner is required for the second method. Laser scanning allows for more accurate measurements. It is the most popular method because of its high accuracy.
A coordinate measuring machine
In order to measure the dimensions of the parts, machining manufacturer used coordinate measuring machines (CMM). These machines now have sensors that automatically measure the surface finishes. You can easily switch between surface finish measurement and part scanning.
Surface Finish Roughness Chart
A surface finish roughness chart can be used to compare the surface finishes. The most commonly used parameter to measure surface roughness is the Ra. Ra is the arithmetical average deviation of the surface.
Ra is a measure of surface roughness. The lower the Ra, it indicates the smoother surface. Micrometers are a standard method to indicate surface roughness. For your convenience, here is a surface roughness chart.
N | Rt | Ra | CLA | RMS | Cut-off Length (mm) |
1 | 0.3 | 0.025 | 1 | 1.1 | 0.08 |
2 | 0.5 | 0.5 | 2 | 2.2 | 0.25 |
3 | 0.8 | 0.1 | 4 | 4.4 | 0.25 |
4 | 1.2 | 0.2 | 8 | 8.8 | 0.25 |
5 | 2 | 0.4 | 16 | 17.6 | 0.25 |
6 | 4 | 0.8 | 32 | 35.2 | 0.8 |
7 | 8 | 1.6 | 63 | 64.3 | 0.8 |
8 | 13 | 3.2 | 125 | 137.5 | 2.5 |
9 | 25 | 6.3 | 250 | 275 | 2.5 |
10 | 50 | 12.5 | 500 | 550 | 2.5 |
11 | 100 | 25 | 1000 | 1100 | 8 |
12 | 200 | 50 | 2000 | 2200 | 8 |
Rt = Roughness, total in microns
CLA = Center line average in microinches
RMS = Root mean square in microinches
Ra = Roughness, average in microns
How to choose metal surface finishes
It is simple to choose the right metal surface finish. All you need is to consider certain factors. These factors are:
Speed
Different metal surfaces require different time frames. Some take longer than others. Consider the delivery time of any project you are responsible for. Consider the processing times of all metal finishing options. If you need to finish a project quickly, consider choosing the fastest surface finishing option.
Material
All metal surfaces are not compatible with all metals. You will need to first consider the material of your piece and then choose a suitable surface finish. Some materials can be damaged by using an abrasive technique. Some materials are very strong and should not be handled too lightly.
Budget
It is possible to find the perfect finishing for your project. But do you have the necessary facilities? Are you able to afford new facilities that will affect the finishing? It’s important not to exceed your budget. It would be best if you chose cost-effective finishing. You may sell low-quality finished materials; however, applying an expensive finish to the ones you make could increase costs and scare away potential customers. It is safer to choose cost-effective finishes.
Conclusion
Metal parts manufacturing requires proper surface finishing. It is beneficial for the end-user and advantageous for the manufacturer. But, if manufacturers don’t know the right way to do things, it could put end-users and manufacturers at a disadvantage. You can avoid this by taking the time to understand your requirements, finding the best finishing options for the job, learning how to do it, and then setting out to make it happen.
Other Articles You Might Enjoy
- Surface Finishes Options For Custom Metal Parts
Although the tool marks on metal parts made using CNC machining services can be visually appealing, there may be cases where additional processing is required. You have many options to…
- Navigating the Complexities of Lightweight Metal Finishing: China Machining Manufacturer's Guide to Chrome Removal
Introduction: The Significance of Chrome Removal in Lightweight Metal Finishing In the realm of manufacturing, the finishing of lightweight metals stands as a pinnacle of engineering finesse, blending aesthetics with…
- Duplex Stainless Steel vs. Super Duplex in CNC Machining: Features and Applications?
Introduction to CNC Machining and Duplex Stainless Steels In the domain of manufacturing, Computer Numerical Control (CNC) machining plays a pivotal role due to its precision, efficiency, and versatility. Essentially,…