Surface finish is the texture, roughness, and precision of a machined surface on a part in CNC machining. It impacts the part’s appearance and performance and is usually specified by the client.
A good surface finish is essential for ensuring a part will fit and function properly. The most common surface finish for CNC machining is a fine, smooth finish obtained through milling, turning, grinding, or polishing.
What Is the Future of Surface Finished CNC Products In 2023?
In 2023, surface-finished CNC products will have a very bright future. There are countless options for surface-finishing CNC items as technology develops and more materials become accessible. CNC technology improves efficiency and adaptability, enabling quicker production and more customization.
Also Read: 2023 Best CNC Machining Company From China: Machined Parts Guide for Beginners
The potential for surface finishing CNC items is expanding due to 3D printing technology improvements.
We may anticipate a wide range of surface finishes for CNC items in 2023, including:
- Laser etching
- Anodizing
- Powder coating and unique finishes made with 3D printing technology.
Why Is Surface Finishing Important in CNC Machining?
In CNC machining, surface finishing is important because it can change how the finished product feels and looks. It can also improve the product’s performance and durability. A clean finish also contributes to the product’s aesthetic value.
It also acts as a barrier against corrosion and wear, and strain. Finally, a quality surface finish can minimize the need for manual finishing or additional processing.
What Is the Difference Between Heat Treatment and Surface Finish?
Heat treatment is the process of heating and cooling metal to change its physical and chemical properties. Heat treatment is a technique used to change the metal’s hardness, flexibility, and strength and increase its fatigue resistance.
Surface finishing is a technique that creates a consistent, smooth surface by removing flaws like burrs and scratches from a material’s surface. It is frequently applied to metal parts and is used to enhance the appearance and usability of a material.
What’s the Difference Between Surface Finishing and Surface Roughness?
The process of polishing, grinding, and lapping a final surface is known as surface finishing. This procedure enhances a part’s aesthetic, precision, and longevity.
On the other hand, surface roughness is a measurement of a surface’s microscopic unevenness. Usually, using a profilometer, it is calculated by measuring the surface’s profile.
8 Methods of Heat Treatment Finishing in CNC Machining: Pros & Cons
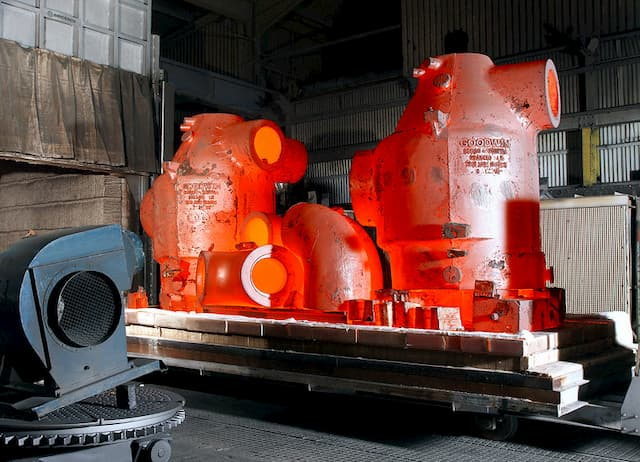
1. Annealing:
In this process, the metal is first heated to a temperature exceeding its critical temperature before being progressively cooled. The metal’s ductility and brittleness are both improved by this procedure.
Pros:
- It improves the metals’ machinability and ductility, making cutting and shaping easier.
- It reduces internal tensions and stops component cracking.
- It softens objects, enhancing their malleability and usefulness.
- It increases the metals’ fatigue strength, enhancing their toughness.
Cons:
- Annealing involves expensive machinery and is a time-consuming procedure.
- In some metals, it can cause increased brittleness and warping.
- As a result, components may oxidize and become highly corrosive.
- Annealing can be challenging to manage and may call for specific understanding to produce the best results.
2. Normalizing:
During this procedure, the metal is additionally heated above its critical temperature before being cooled in the air. The consistency of the metal’s characteristics is improved, and this technique improves the grain structure.
Pros:
- Normalizing the heat treatment and finishing process helps lower internal tensions in the material, improving its mechanical characteristics, including tensile strength and flexibility.
- Additionally, it aids in making the material more machinable, which can provide more exact and precise parts.
- Heat treatment procedures like welding can aid in lowering distortion.
Cons:
- High temperatures are needed to normalize heat treatment finishing, which may result in higher energy expenses.
- Additionally, depending on the application, it can result in a slight loss of hardness, which may not be desirable.
- Some materials may experience increased grain development due to normalizing heat treatment finishing, resulting in a loss of strength and toughness.
3. Hardening:
The metal must be heated over its critical temperature during this procedure, followed by rapid cooling. The metal’s strength and hardness are both improved by this procedure.
Pros:
- It increases the surface’s hardness and offers improved wear resistance.
- It can enhance the part’s dimensional stability, making it less likely to distort or move while in use.
- It can strengthen the component’s ability to resist corrosion, making it less resistant to rust or corrosion.
- Hardening can greatly increase the part’s strength and durability.
Cons:
- It can be costly, based on the size and complexity of the component.
- The part needs to be handled carefully because hardening can make it brittle.
- The part can crack or suffer other damage if it is not properly hardened.
4. Hardening can also decrease a part’s machining capacity, making it more challenging to work with.
4. Tempering:
This procedure involves quenching the metal after a hardening operation and then reheating it at a lower temperature. This treatment reduces the metal’s brittleness.
Pros:
- The material becomes stronger, harder, and more resistant to wear.
- The material also becomes more fracture-tough.
- Tempering also increases the material’s flexibility and decreases its brittleness.
- It can be applied to reduce residual stresses brought on by previous heat treatments.
- Tempering is a reasonably simple and affordable process.
Cons:
- The material may distort somewhat after tempering.
- The material may even lose some of its toughness.
- Tempering may make some materials less resistant to corrosion.
- If done incorrectly, it may result in the material cracking or brittleness.
5. Stress Relief:
This method gently cools the metal after being heated to a temperature below its critical point. This procedure helps to reduce the metal’s residual stresses.
Pros:
- Stress reduction makes metals and alloys more durable and stronger.
- Improves fatigue and wear resistance by increasing surface hardness.
- Reduces distortion, warping, and twisting while increasing dimensional stability.
- Improves corrosion resistance, resulting in a longer component lifespan.
- Enhances machinability, enabling better drilling and cutting.
Cons:
- Heat treatment has resulted in a price increase.
- If heat treatment is not done properly, it might lead to distortion and cracking.
- Heat-treating can degrade some metals, especially if too much heat is applied.
- Heat treatment may produce residual strains, resulting in component failure before its time.
6. Carburizing:
In this procedure, the metal is heated to a lower temperature than its critical temperature before being exposed to an environment high in carbon. The metal’s surface hardness is increased as a result of this treatment.
Pros:
- The surface becomes harder and more resistant to wear and tear after carburizing heat treatment and finishing.
- Additionally, it boosts the metal’s ability to endure greater temperatures and its fatigue strength.
- Carburizing heat treatment finishing is a simple and affordable process.
- Carburizing increases the hardness of many metals, including cast iron, stainless steel, and steel.
Cons:
- Carburizing heat treatment finishing is not appropriate for all types of metals, as well as some metals may not react favourably to the treatment.
- The size and complexity of the component being treated will determine how long the treatment will take.
- The part may weaken if the carburizing heat treatment is improperly carried out.
- The method is not eco-friendly and generates a lot of fumes.
7. Induction Hardening:
This procedure involves quenching after the metal has been heated with an induction coil. The metal’s strength and hardness are improved due to this process.
Pros:
- Induction hardening is a quick and effective procedure for particular hardening sections of a workpiece.
- It is a targeted heat treatment procedure that protects the workpiece’s non-hardening components.
- The method is very repeatable and can quickly harden huge quantities of identical parts.
- The procedure is controlled and can be used to harden specific areas of a workpiece precisely.
Cons:
- Induction hardening requires specific tools and materials, making the process expensive.
- The procedure can be dangerous since it involves high temperatures.
- The method can only be used on magnetic metals; it is ineffective on non-magnetic metals.
Tips & Tricks for Choosing Surface Finishes for CNC Machining
Consider the material:
Surface finishes must be different for various materials. Generally speaking, softer materials need a finer finish, whilst harder materials could need a coarser finish.
Analyze the application:
The application should help you to choose the surface finish. Consider the part’s usage environment, the load it will bear, and any potential contact points.
Check the Cost:
It would help to consider the surface finish’s cost when making your choice. Choose a less expensive finish if cost is a primary consideration.
Know the allowable tolerance:
Tolerance limits vary depending on the surface finish. Select a finish with the tolerance required for your application, and be careful to do so.
Focus on the aesthetics:
Additionally, the part’s aesthetics may be impacted by the surface treatment. You should select a finish that creates the intended impact if the part must have a specific look or feel.
What Are Major Applications of CNC Surface Finish?
1. Automotive CNC Machined Parts: CNC surface finish techniques are frequently used to create automotive components, including wheels, brake discs, and camshafts, to produce a high-quality finish.
2. Aerospace CNC Machined Parts: Aerospace components, such as turbine blades, requires a clean surface finish to guarantee that air passage is not obstructed. CNC surface treatment processes provide precision and accuracy for these components.
3. Medical CNC Machining Parts: The medical business uses parts that have a smooth, uniform finish thanks to CNC surface finishing processes. These parts can be used in medical implants, prostheses, and other equipment.
4. Food CNC Machining Processing: CNC surface treatment techniques are used in food processing machines like grinders and blenders. These devices can run more efficiently if the surface is smooth.
5. Electronics CNC Machined Parts: The manufacture of electrical components, such as printed circuit boards, uses CNC surface finishing techniques (PCBs). A smooth surface prevents components from being harmed during assembly.
6 Professional Tips for Surface Finish in CNC Machining
Develop A Workflow Chart:
Create a process map outlining the workflow for your CNC machining. This will assist you in identifying the various machining steps and any areas in that you want improvement.
Apply Latest CNC Machining Tools:
A great surface finish can only be obtained by employing the proper tools for the task. Choose cutting tools appropriate for the material you’re working with and the surface finish you want.
Select Accurate Feed and Speed Rates:
You may get the required surface finish by choosing the appropriate feed and speed rates. Speed is the pace at which the cutting tool rotates, and feed is the rate at which it moves across the material’s surface.
Never Underestimate Finishing Tools:
You can improve the surface finish by using finishing tools like deburring and polishing equipment. The quality of the finish can be improved by combining these tools with traditional machining tools.
Observe Tool Path:
You can improve the surface finish by modifying the tool path. This may require changing the tool path, the cut direction, or the depth of the cut.
Track Your Process:
You can find any potential issues by checking the machining process. Make sure to monitor the machining procedure and adjust as necessary.
How to Choose A Company for CNC Surface Finish?
Research on Best CNC Machining Companies:
First, research the available CNC surface treatment alternatives and contrast them based on their features, price, and quality.
Do not forget to read customers’ reviews:
You can learn more about a company’s performance, and whether or not it provides the services you’re seeking by reading reviews from previous and present clients.
Request CNC machining quote Online:
You can Request quotes from the companies you’re thinking about working with to get a sense of the cost and response time.
Check CNC Machining certifications:
Ensure the company has the appropriate certifications before hiring them since this will confirm their expertise and knowledge of the field.
Ask questions:
Make sure the company is the best fit for your project by asking questions about their approach, experience, and turnaround time.
Consider the time frame:
Make sure the company can fulfil your deadline by considering the project’s timeframe.
Other Articles You Might Enjoy
- Surface Refinement: Leveraging Bead Blasting for CNC Machining
In the realm of CNC machining, surface quality plays a pivotal role in determining the overall performance and aesthetics of the final product. Leveraging bead blasting as a surface refinement…
- Precision CNC Machining of Steel: High-Volume Production
Precision CNC Machining and High-Volume Production As an integral part of modern manufacturing processes, Precision Computer Numerical Control (CNC) machining brings about unmatched accuracy and consistency in the production of…
- Minimizing Chatter in CNC Machining: Tips and Tricks for Better Surface Finish
Are you tired of poor surface finish in your CNC machining? Chatter might be the culprit. Chatter is a common problem that can cause poor surface finish, reduced tool life,…