CNC machining services produce high-quality parts with accuracy and efficient production. These CNC machines use computer numerical control machining tools to cut and shape materials precisely. Additionally, CNC machining services offer speed, flexibility, automation, and cost-effectiveness. These are the advantages of a CNC machining shop.
Due to these advantages of CNC machining services, it has become an attractive option for industries.
Advantages of CNC Machining vs. Conventional Machining
There are two different manufacturing production processes. i.e., CNC machining and conventional machining. Conventional machining is a manual machining process. In this process, manual labor operates the machines. But in the case of CNC machining, computer programs control the whole process.
1) CNC machining produces different parts of machinery with greater precision. This precision is achieved by computer numerical control. Human error can be eliminated with this process.
2) CNC machining advantage is that we can accelerate the production process. These machines can produce different parts of machinery quickly and efficiently. Additionally, we can run these machines 24/7 with little downtime for some maintenance. So efficiency will increase overall.
3) CNC machines are used to produce elementary and complex parts. These are highly versatile. So we can start its shopping or business with low-volume production runs.
4) CNC machining reduces the need for manual labor. As its production capacity is so high due to its speed and accuracy. So it is a cost-effective method.
5) With the help of CNC machining, we can produce consistent parts, a significant issue in conventional machines.
6) The AI computer programs control CNC machining. So its process is automated without human error and human intervention. Due to these qualities, production will increase.
10 Benefits of CNC Machining and CNC Milling
CNC machining is a process in which we use some particular computer program to produce precise and complex parts. This process has many benefits. We will discuss these benefits one by one as follows
1) The production of CNC machining and CNC milling is exact. We can get precision up to 0.001 or more.
2) To make all parts identical, use CNC machines and CNC milling.
3) CNC machining is very beneficial for producing mass production. Because it can create identical parts.
4) CNC machining and milling processes can produce a wide range of parts from simple to complex geometry. So these are versatile machining processes.
5) A few trained people are required to run CNC and milling machines. So these machines are cost-saving machines
6) In these machines, less material will waste. Because of the precise control of these machining processes.
7) CNC machining and milling machining processes can produce high-quality parts free from human defects and errors. Its result will be better product quality.
8) These processes are safer than traditional machining processes because they require fewer human inversions.
9) With these machines’ help, we can make any design specifications to produce a desired product.
10) To further accelerate production, we must integrate CNC machines with automation technologies such as Robots, etc.
What Level of Skill Is Required to Operate CNC Machines?

To operate a CNC machine, machinists require skill and knowledge. Skill and knowledge may vary on behalf of a particular machine. Here we discuss general skills which are required to operate CNC machines
1) Machinists should have basic computer skills to read and write relevant programs. He should have the basic knowledge to navigate software programs and troubleshoot problems with standard computers.
2) Machinists should have the technical skills of the machine to cut parameters correctly. These skills comprise tooling, spindle speeds, and feeds.
3) Mathematical skilled operators can easily interpret part drawings and calculate paths to adjust cutting operations.
4) Problem-solving skill is essential to operate CNC machines. With this skill, the machinist will be able to diagnose This skill include tool breakage, incorrect tool calibration, and part alignment.
High Precision and Improved Accuracy
CNC milling machines have high precision and improved accuracy. The following reasons make CNC milling machining more prominent than the traditional manual machining processes.
1) As Computer programs govern CNC milling machines. These computer programs control the movements and adjustment of cutting tools. So we get high precision in the production of parts.
2) CNC milling machines can operate automatically. These machines use cutting tools without the intervention of humans. So it reduces errors caused by the manual machining process.
3) CNC machines are programmed to perform consistent cutting operations such as speed and depth. Each cut is performed with high precision and accuracy.
What are the Applications for CNC Milling?
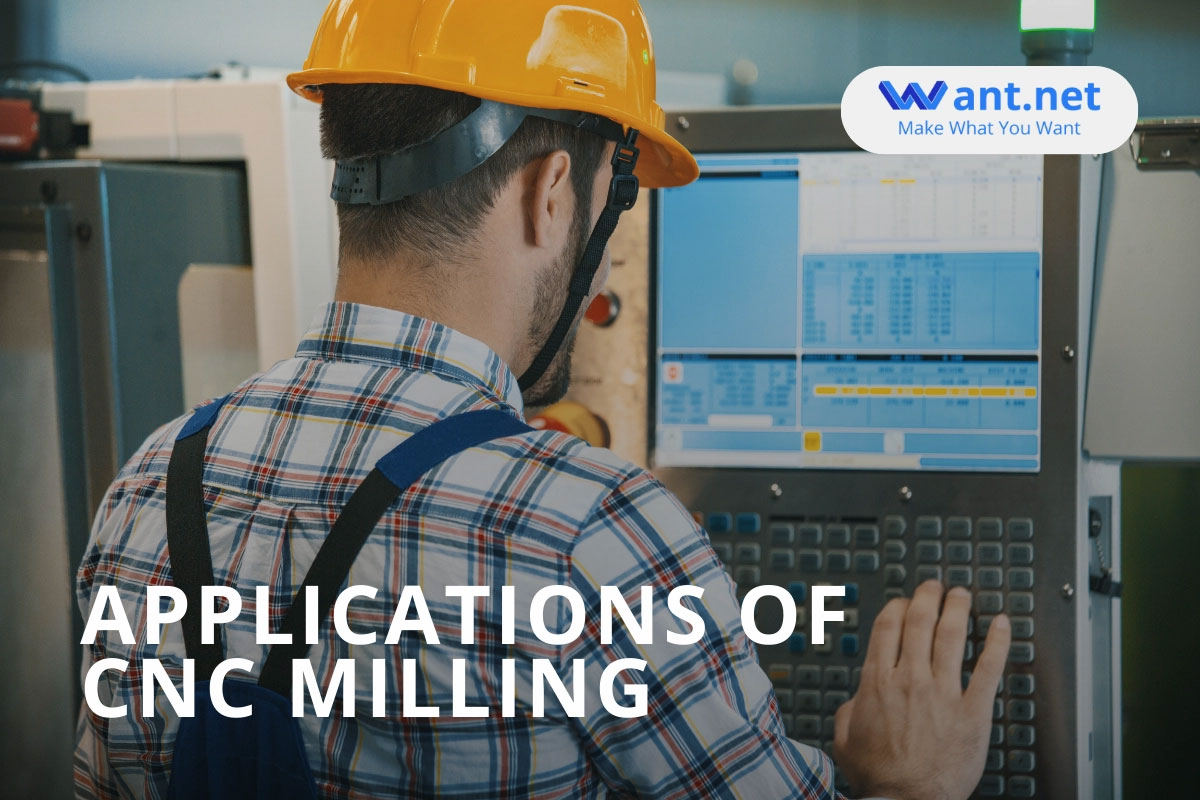
CNC milling has a wide range of applications. We will discuss them one by one:
CNC milling machines are used in the aerospace industry. We use it to produce engine components, structural components, and landing gear for airplanes.
CNC milling machines are also used in the production of automotive parts. These parts consist of the engine, transmission system, front, and rear axle steering system
CNC milling machines are used in the medical field to produce surgical instruments such as forceps, scissors and clamps, orthopedic braces, dental implants, and hearing aids.
CNC milling machine is also used in the furniture industry. It is used to create table legs, chair arms, and decorative elements of furniture with high precision.
CNC milling machines are used in the electronics industry. We can produce multiple electronic devices such as PCB (printed circuit boards), connectors, heat sinks, and housing devices.
What Can Materials Be Used in CNC Machining?
CNC machines are made up of different materials. The most common materials are metals, plastics, composites, wood, foam, and ceramics.
Working CNC machining requires materials like aluminum, brass, copper, stainless steel, titanium, and steel. It requires plastic materials like acrylic, polypropylene, PVC, Teflon, and nylon. Some composites, such as carbon fiber, fiberglass, and kevlar, are also used in CNC machining.
Ceramic materials are also the main type of materials which is used in the CNC machining process. Some ceramic materials are zirconia, alumina, and silicon carbon. Different types of wood, i.e., hardwoods and softwood, are also used in CNC machining. Additionally, foam such as polyurethane foam and polystyrene form is also used.
Limitations of CNC Milling Machines
With many CNC machining advantages, CNC milling machines have some limitations. such as
- axis movements
- prototype size
- drill bit size
The CNC milling machining process involves components such as a control panel, spindle, cutting tools, worktable, axis system, tool changer, and coolant system. It is a costly project, and we cannot use it for small-scale production.
Experienced engineers are required to operate CNC machines. So it requires additional cost.
Size Limitations of CNC
The limitation of a CNC milling machine depends upon its size and shape. The maximum size attained by a large CNC milling machine is about 105 ft by 21 ft. The minimum range of parts formed by a small CNC milling machine is around 9 inches on the x-axis, 5.125 inches on the y-axis, and 6.5 inches on the z-axis.
Should You Use CNC Machining?
Make your decisions by considering the different Pros and cons of CNC machining. With the advancement in every field of life, we should change the industry pattern as the world requires more production, which conventional machining can’t provide.
Other Articles You Might Enjoy
- Aluminum CNC Machining Service for Custom Parts
Aluminum CNC machining stands at the forefront of modern manufacturing, epitomizing precision, versatility, and efficiency. With its widespread applications across industries ranging from aerospace to automotive and beyond, aluminum CNC…
- Applications and Advantages of Bronze CNC Machining
1. Introduction: The Enduring Allure of Bronze in CNC Machining In this opening section, we explore the timeless appeal of bronze as a material for CNC machining. From its rich…
- 9 Advantages of CNC Machining Over Conventional Machining
In today's manufacturing landscape, the utilization of numerical systems has become ubiquitous across various industries, thanks to the advent of personal computers. Among the favored fabrication and manufacturing applications, the…