The aluminum milling industry’s revenue is growing due to increased demand from numerous end-use industries such as manufacturing, construction, automotive, and aerospace.
The cost-effectiveness and lightweight characteristics of aluminum, which make it a perfect material to be utilized in high-performance and fuel-efficient automobiles are also credited with the industry’s growth. The Asia-Pacific region is anticipated to have significant revenue development in the aluminum milling sector.
The Asia-Pacific region is anticipated to have significant revenue development in the aluminum milling sector due to the increasing industrialization and expansion of end-use industries in nations like China and India, Aluminum is a metal with various qualities that make it perfect for milling. One reason is that aluminum is a soft, flexible material that can be easily molded by a machine.
Furthermore, aluminum has become a popular material for prototypes due to its low cost and ease of use.
Aluminum is a corrosion-resistant, lightweight metal. Aluminum is a great material choice for a variety of purposes, from the construction of aircraft to the parts of automobiles.
Aluminum also has a high heat conductivity and is non-magnetic. It’s perfect for high-voltage applications where heat must be quickly dissipated.
Overall, CNC-milled aluminum is a great material to mill because of its balance of properties.
What Is CNC Aluminum?
Aluminum is the world’s third most abundant metal, accounting for 8% of the earth’s crust. Aluminum is the most widely used metal following steel due to its flexibility. Aluminum metal was first synthesized about 170 years ago, while aluminum alloys have been used for a long time.
The material is easy to deal with because it is flexible, light, non-combustible, and melts at a temperature of about 660°C. The material itself well deflects heat and light, protecting it from rust.
Pure aluminum has high electrical conductivity, is ductile, and is resistant to corrosion. One of the lightest industrial metals, aluminum has a strength-to-weight ratio that is higher than that steel.
What Is Aluminum for Milling Materials?
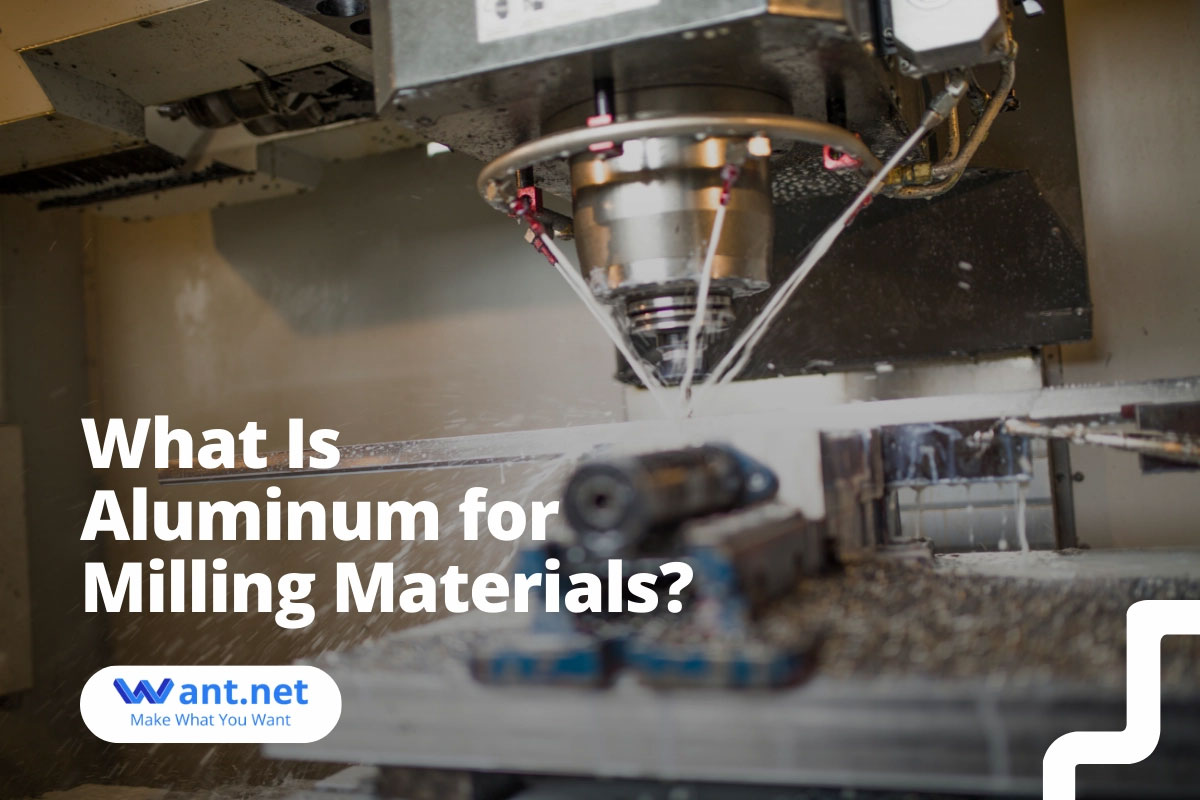
The process of milling aluminum involves using a milling machine to remove material from an aluminum workpiece. There are many different types of CNC-milled aluminum, and when milling, certain measures must be taken for each variety.
There are various factors to consider when deciding on the best material for a task. There are two main types of aluminum: cast and wrought.
Cast aluminum is weaker and less heat-resistant than wrought aluminum, but it also costs more. On the other side, cast aluminum is more versatile but weaker. The type of aluminum you choose will ultimately depend on the requirements of your project.
Use the proper cutting tools and techniques for aluminum blocks for milling them to prevent damaging the material.
What Are the Different Grades of Aluminum?
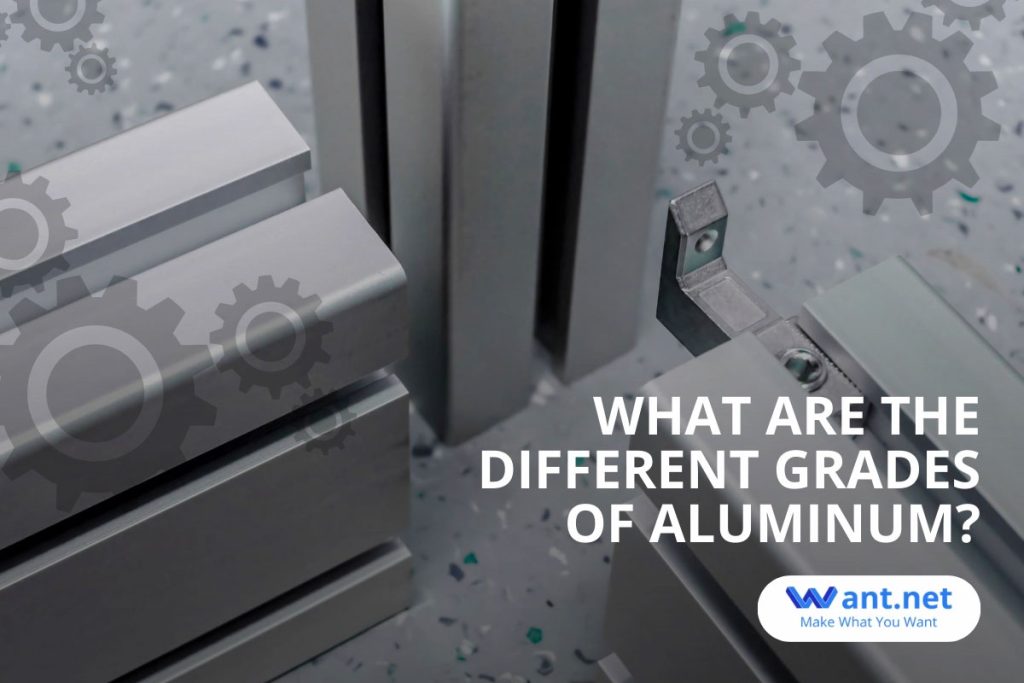
Aluminum is a versatile building material that comes in several popular varieties. Moreover, seven categories of aluminum alloys can be distinguished.
- Aluminum 2024-T351. It is the toughest aluminum and is mostly used in aviation. It is also renowned for being tough on machines since it needs specialized equipment and unique manufacturing environments.
- Aluminum-alloy foil. In comparison, the most malleable type of aluminum has a restricted number of alloy machining options.
- Sheet aluminum. It takes the shape of fabricated aluminum workpieces. Metal sheets can be produced by spinning, stamping, or hammering. Aluminum alloys of different types may be mixed during the process to get different qualities.
- Clad aluminum. It’s known as treated aluminum. It is covered with a coating of any kind, including zinc, silicon, nickel, or magnesium. Treated aluminum is more resistant and has additional qualities due to the coating.
- Bare or pure aluminum. It is pure, raw metal, as is clear from the name. Usually, it is required for usage at a later stage of the production process. It is rarely utilized as a material for preparing workpieces and producing additional components. It can be explained by the low durability and lack of corrosion resistance.
- Aluminum alloys: There are eight different grades (series) of aluminum. Each of them has distinctive characteristics and particular uses.
- The 1000 series has 99% aluminum.
- The 2000 series is an alloy of aluminum and copper.
- The 3000 series is a manganese-infused aluminum alloy.
- The 4000 series is a silicon-infused aluminum alloy.
- The 5000 series is an alloy of aluminum and magnesium.
- The 6000 series is an aluminum alloy containing silicon and magnesium.
- The 7000 series is an alloy of aluminum.
What Are the Cutting Tools for Aluminum?
The trick is this: There are more than a few hard-enough pieces of metal in CNC tooling for cutting aluminum. The most popular tool categories are listed below, along with some notable features that they share.
What Are the Commonly Used Cutting Tool Types?
The most important thing to remember is that you should under no circumstances use any cutting tools that are made for general usage. Aluminum is unique among other metals for the reasons mentioned above. Thus, the listed tools must only be acquired if a source certifies that they are suitable for aluminum.
- Drill bits for cutting small areas
- End mills for cutting material down directly without a hole or other pre-drilled feature.
- Face mills are used to machine flat sections.
- Reamers for expanding already drilled holes
- Gear cutters for quickly creating various gear types.
- Hollow mills that successfully increase pre-thread diameter by enclosing and rotating a cylindrical workpiece.
- Internal and external threads can be cut with ease using thread mills.
- Slab mills use rapid wide and narrow cuts to produce flat surfaces.
- Fly cutters use deep, wide cuts to create a smooth surface finish.
Which are the best milling tools for Aluminum?
YG-1 Alu Power HPC
The Alu Power HPC line from YG-1, frequently referred to as the “king of aluminum CNC milling,” is the supreme milling equipment for high metal extraction of aluminum and aluminum alloys. They have large flute pockets and sharp cutting edges, which, in combination with their ultra-fine micro-grain carbide construction, make them perfect for machining aluminum.
YG1 Alu Power HPC delivers outstanding results in a variety of alloy machining applications, like slotting, profiling, pocket milling, ramping, and plunge milling.
YG-1 Alu Power
The YG-1 Alu Power is the ideal carbide milling cutter created for non-ferrous materials like aluminum. They beat ordinary milling cutters in terms of performance, tool life, and wear resistance without breaking the bank, thanks to the micro-grain carbide substrate. The unique shape of aluminum simultaneously ensures the highest chip control and surface finish.
Korloy A+ End Mills
Korloy’s A+ End Mills are excellent cutters for aluminum finishing operations since they function similarly to the Alu-Power line. These two or three-lapped flute cutters use u-shaped flutes and a 45° to 50° helix angle to produce a mirror surface polish of the finest quality. This range is intended only for side cutting and profiling; plunge cutting is not permitted.
YG-1 Alu-Cut HSS
The YG-1 Alu-Cut is manufactured from a durable HSS substrate with 8% cobalt and works well with manual machines in unstable machining environments. This is because, in the case of any vibrations during the machining process, HSS is a more robust substrate compared to carbide and therefore less likely to chip.
What Are the Best Strategies and Tips for Aluminum Machining?
We have compiled a list of techniques, guidance, and recommendations to help you with CNC machining aluminum.
- Maintain stable temperature. Temperature changes in the workplace may result in an excess of humidity, which accelerates the oxidation of aluminum.
- Clean metal chips. Indeed, dust collectors could help get rid of sticky aluminum ships. But, manually cleaning the machine while it is running is important. In order to make the metal chips less sticky, you can spray coolant through the machine.
- Reduced the flutes. The distance between cutting edges is compressed by excessive flutes. It results in the stacking of metal chips, which lowers the quality of machining aluminum and the life of the cutting tools. Three flutes are typically sufficient for cutting aluminum.
- Increase production rates only when necessary. A serious mistake is to cut corners on extra cuts in order to increase production rates.
The tooling life quickly decreases if a CNC machine is forced to perform fewer but deeper cuts. Moreover, it produces metal chips that are more difficult to remove. In general, shallow passes function significantly better.
Applications of CNC Machined Aluminum Parts:
There are several uses for aluminum machined parts across numerous industries. Aluminum alloys are used as a component in the industrial sector because of their high surface finishing, long machining life, and low production costs.
- They are used for the manufacture of automobile parts including engine blocks and transmissions.
- In the aerospace sector, machined aluminum machined parts are used to create components for planes like fuselage panels and wing spars.
- Aluminum machined parts are used to create implants and prosthetic devices in the medical sector.
- Aluminum machined parts are used to create doors, windows, and other components in the building sector.
- Aluminum alloys are mostly employed in electronic parts and appliances due to their high conductivity.
- Aluminum alloys are used in many different types of heavy machinery, mostly in the production of complex parts, cement factories, coal power plants, and other industries.
- In the medical sector, lightweight and durable medical equipment is made from aluminum alloys.
- CNC machined aluminum components are frequently utilized in rockets and spacecraft.
Conclusion
Aluminum is a durable material that can be easily cut and molded, but it must be handled with care. You must be aware of the most effective techniques for handling them if you are to get the results you want.
You must make sure that your tool crib, machine settings, and toolpaths are all optimized for aluminum if you want to maintain a lead over your rivals and improve the efficiency of your shop.
Other Articles You Might Enjoy
- Innovative CNC Machining for Complex Surgical Tools
Introduction to CNC Machining and its Significance in Surgical Tools Manufacturing CNC machining, an acronym for Computer Numerical Control machining, plays a significant role in the manufacturing world. Being an…
- CNC Machining for the Defense Industry: Titanium vs. Aluminum Alloy Selection
CNC Machining and Its Significance in The Defense Industry Computer Numerical Control (CNC) machining is a crucial manufacturing process whereby pre-programmed computer software dictates the movement of machinery and tools.…
- CNC Machining Materials: Acrylic vs. Polycarbonate for Transparent Components
CNC Machining: An Introduction and the Importance of Material Type Computer Numerical Control (CNC) machining is a manufacturing process where pre-programmed computer software dictates the movement of factory tools and…