If you want to learn more about the process of molding intricate parts from raw workpieces, you must look into CNC machining machines.
CNC turning centers like want.net use state of the art lathe tools. Nevertheless, commonly available information regarding their unique qualities and unique features is often inaccurate and confused with related pieces of equipment known as CNC milling centers. It results from the complexity of selecting a CNC turning machine that is suitable for the requirements of a specific company.
Also Read: 3 Types of CNC Milling Machines
You can find a comprehensive overview of CNC turning machines below.
What Is a CNC Turning Machine?
CNC stands for computer numerical control. A cutting tool is used to remove material from a rotating object during CNC turning, commonly referred to as a subtractive machining technique.
As a result, a CNC turning machine can be described as a computer-controlled piece of equipment used to precisely remove material components from a rotating workpiece.
These tools are used in the industrial and commercial manufacture of the following prepared materials as components.
The terms “lathe” and “turning machine” often cause confusion among readers. Although there is no technical distinction, a CNC lathe is typically thought of as a more basic turning machine. These tools simply require the X and Z axes to execute turning operations. A CNC turning machine or center can also incorporate a Y-axis, milling, drilling, and sub-spindle capabilities.
It is possible to create machine parts with axial symmetry using CNC turning machines. It may be required to incorporate drilling, tapping, slots, recesses, and other features, depending on the particular component’s unique curvatures.
CNC turning machines are commonly used for the high-volume manufacture of symmetrical and generally basic components made of a variety of materials.
What Is CNC Turning?
CNC turning is a common subtractive manufacturing method that involves removing pieces of a material from its outside with a cutting tool. The workpiece spins as pieces are chipped off until it has the appropriate form, diameter, and size of the final piece.
Furthermore, the cutting tool is not rotary and usually has a single-point end. Instead, it only rotates in regard to the workpiece. The most common industrial machines for turning tasks are CNC lathes.
Meanwhile, CNC turning can be used to cut various polymers, wood, metals, and even plastics. Another benefit of the turning manufacturing process is that it produces high-dimensionally accurate goods since it uses computer-generated instructions and codes.
What Sort of Materials Can Be Used for CNC Turning?
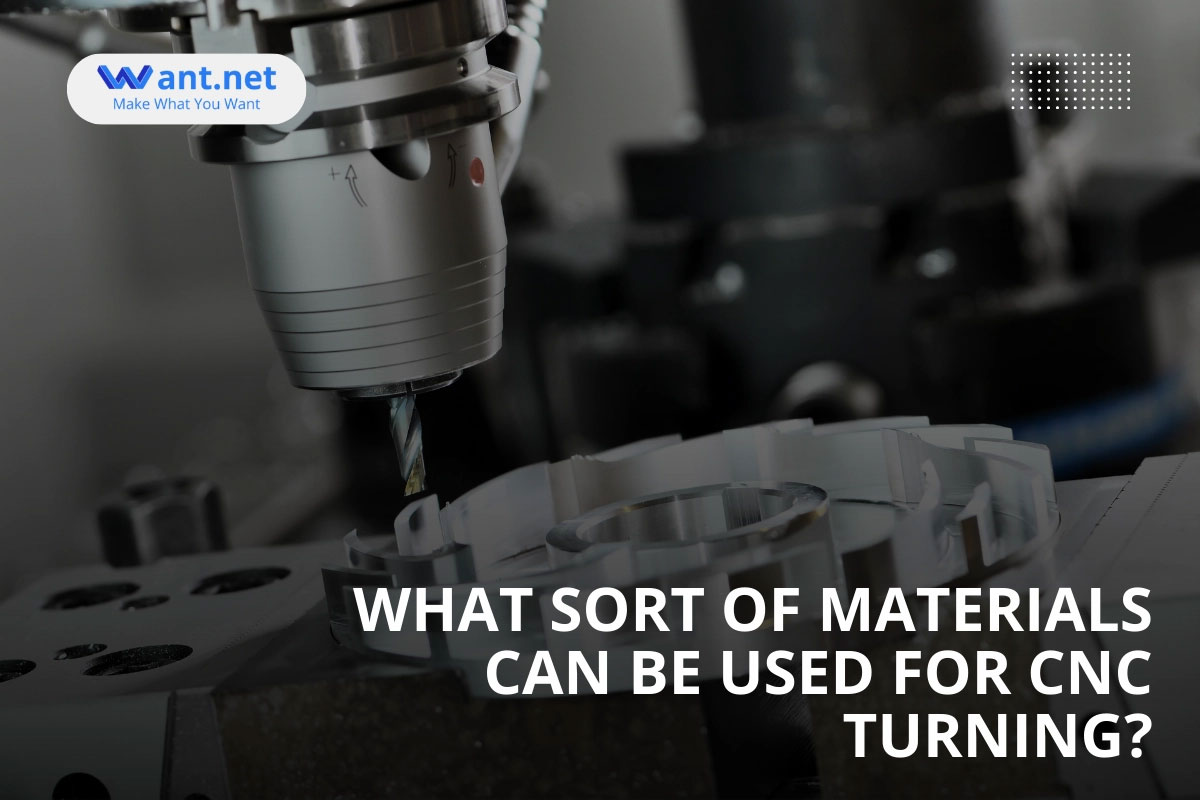
The versatility of CNC machining with a wide range of materials is one of its main advantages. The majority of metal and plastic materials are also suitable for CNC turning operations. These include materials like aluminum, nylon, copper, steel, wood, titanium, PEEK, glass, PVC, brass, wax, and more.
Each material has a distinct level of structural integrity, so it can need a particular lathe or turning center with specific requirements for the flow rate and turning speed.
What Are the Types of CNC Turning Machines?
In fact, the most common machines for turning are lathes. These devices come in a variety of varieties; each best adapted for particular turning activities. For your machining tasks, there are four main types of CNC turning machines.
Horizontal CNC Lathes
Modern lathes are among the most often used tools for many industrial purposes since they have all the qualities of a standard lathe. They can, however, be used for both boring and turning operations. Moreover, a CNC-turner machine runs computer programs.
Vertical CNC Lathes
The fundamental distinction from a horizontal lathe is how the workpiece is positioned, as one might expect. Before rotation, spinning, and cutting, the material is placed vertically – from the bottom up. Thus, these machines are best suited for use in enclosed spaces. Also, they function best with large and hefty workpieces.
Horizontal Turning Centers
Horizontal turning centers are machines that can drill and mill. The turning center has a horizontal orientation, and tools located above spin and cut into the workpiece, depending on gravity to clear the cuts.
Vertical Turning Centers
This machine includes the features of a CNC miller and a horizontal turning center. Due to its design, working with large workpieces is made easier because the rotating chuck is positioned near the ground.
How to Operate CNC Turning Machine?
The CNC turning center’s operation can be divided into four steps. They are responsible for designing the CAD model, changing the CAD file to a CNC program or pre-programming, installing a CNC machine, and performing the machining operation and material cutting.
Designing the CAD Model
The abbreviation CAD stands for computer-aided design. The goal is to design an object as a 2D vector or 3D solid part so that a CNC turner machine can build a model with the required technical parameters.
A virtual reality product with the same characteristics as a real object can be created with the help of CAD modeling. The following characteristics can be taken into account: material, weight, size, and optical characteristics, among others.
A finished CAD design should be converted to a file format that is compatible with CNC machines, such as STEP or IGES.
Then, a CAD file must be converted into a real CNC program, with which a CNC turning machine works.
Pre-Programming
In CNC turning, the axis of the machine is handled by pre-programmed CAD software placed on a computer linked to a CNC turning center. Instructions for the turning machine should be programmed using G-code and M-code in order to be carried out.
Several software applications, including CAD systems that contain this feature, allow the conversion of a CAD file into a CNC file. The fundamental difference is that they all use the G and M coding languages. It enables the programmable logic controller of a CNC turner machine to be activated and performs the desired function.
G-code
A CNC machine is directly controlled using this software programming language. Its aim is to instruct a CNC turning machine to modify the geometric alignment of its tool axes.
G-code, which consists of a series of instructions, is represented by the letter “G” and a number. “G00,” for instance, denotes a quick, non-cutting action. Commanding a center to modify the geometric coordinates is another G-code feature.
It appears to be the name of an axis, such as “X,” followed by a numerical representation of a distance, such as “-80.” Such a CNC turning machine instruction entails moving the X-axis -80 mm.
M-code
M-code is in charge of non-geometry machine operations. Examples include starting and stopping the spindle, changing the pallet, turning on and off the flood coolant, and more.
What Are the Primary Parts of CNC Turning Machines?
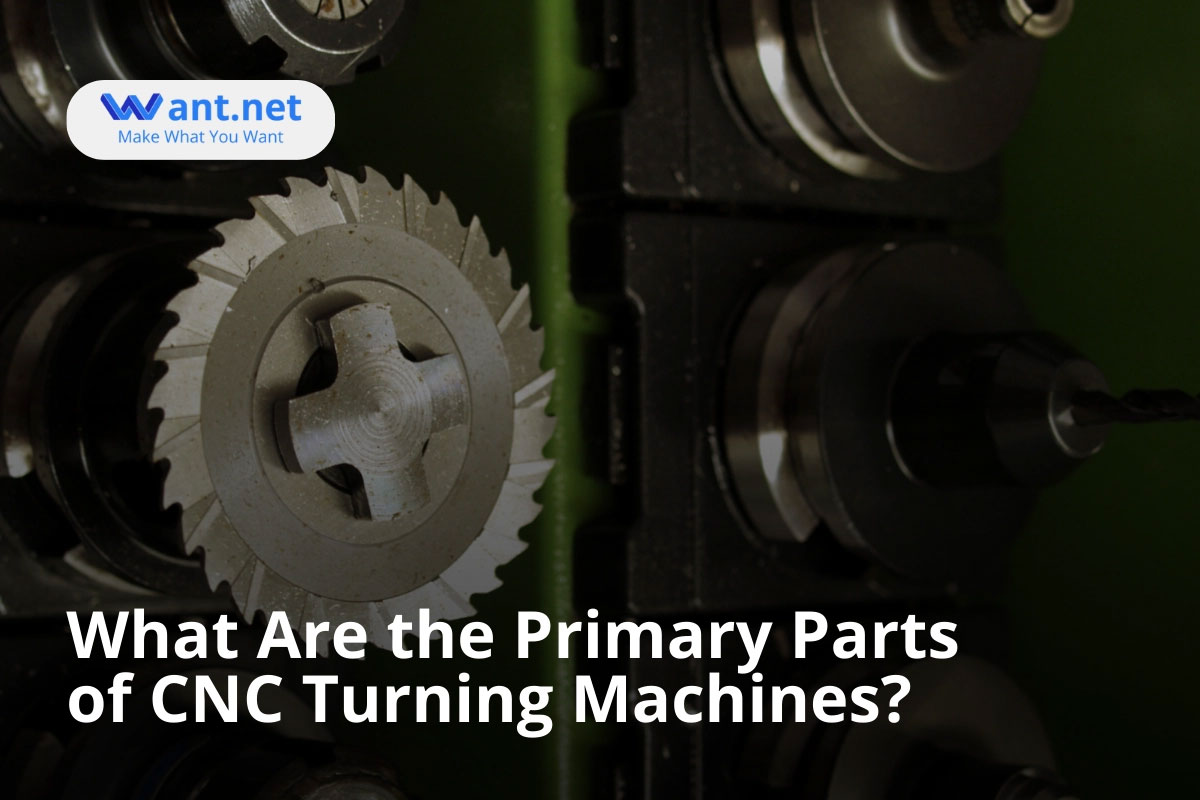
The primary parts of CNC turning machines are detailed below.
- Machine bed. It is sometimes referred to as a CNC turning center’s primary foundation, on which the various parts are installed.
- Headstock. This wall-holding device, which is positioned on the left side of the machine, has a main spindle attached to servo motors that act as spindle drivers.
- Sub-spindle. It is different from the primary one and designed to perform additional cutting tasks.
- Tailstock. It is movable along the length axis and provides axial support for the workpiece.
- Chuck. The workpiece is held in place by this three-jaw hydraulic component.
- Tool turret. This component makes it possible to replace the necessary cutting tools for machining.
- Guideway. This component allows the tool to rotate vertically or horizontally.
What Types of CNC Turning Centers Are There?
There are a few common types of CNC turning centers available for purchase.
- Basic 2-axis CNC lathe. The primary turning device that carries out common tasks.
- 3-axis CNC lathe. It is similar to the conventional one but has additional axes and milling options.
- Multi-spindle/dual turret. These machines have two turrets and two spindles, either equal in number or one main and one sub, to speed up the turning machining process.
- Chucking lathe. This CNC turning machine, which is used for two-way turning, lacks a tailstock. It is known as a more compact version of the typical one.
- Flatbed CNC lathe. It has an adjustable gap for bigger turning diameters.
Milling vs Turning
CNC Milling
A milling technique is usually used when a part lacks necessary cylindrical properties. When a revolving cutter moves around the workpiece, removing material, it is stationary. The workpiece must be manually turned on a 2 or 3-axis CNC milling turning machine in order to cut the various faces. A 4 or 5-axis machine may automatically move the workpiece or spindle to create complex forms and shapes.
CNC Turning
A turning technique is often used to produce objects with symmetrical and cylindrical characteristics. A single-point cutting tool is placed against the spinning workpiece to remove material while the material is placed in a chuck and moved quickly.
Turning actions on a CNC lathe can be extremely effective for large-scale runs. A bar feeder can be added to the operation to help automate it and reduce the machinist’s manual labor.
What Is A CNC Turner?
A CNC operator operates the turning lathe machine to guarantee that parts are precisely cut into cylindrical shapes. in order to manage the rotation speed throughout the turning manufacturing process as extra material is taken away from the workpiece. In comparison to milling and drilling, where the tool spins while the workpiece is stationary, turning is a distinct process from those operations.
Although computer numerical control (CNC) turners use this technology, it’s still important to comprehend the different kinds of turning lathes, such as manual, semi-automatic, and automatic lathes. Place the cutting tool in a precise cutting position and provide it with guidance on manual and semi-automatic turning lathes.
The initial setup is all that is needed for the automatic lathe. Yet, the CNC turning machines carry out the commands from your chosen programs automatically.
Conclusion
Turning is the backbone of the manufacturing sector. It is best to use that fabrication technique to produce accurate results for axisymmetric parts. Large-batch production is possible with nearly identical results thanks to the versatility and production capacity.
Large CNC machining centers now have CNC milling turning features. These machines become even more powerful for producing complex parts when milling machines are included.
Other Articles You Might Enjoy
- Ceramics in CNC Machining: A Viable Alternative to Traditional Metals?
CNC Machining and Its Importance in Manufacturing Computer Numerical Control (CNC) machining stands as a critical pillar within the sphere of manufacturing, lauded for its accurate and fast production capabilities.…
- CNC Turning: A Deep Dive into Rivet Production(cnc laser cutting Adolph)
Introduction:Computer numerical control (CNC) represents one of the most crucial inventions in manufacturing technology. It pertains to a method used to control an array of complex machinery using computer programs…
- CNC Turning: A Closer Look at Rivet Production(g code cnc Lester)
Computer Numeric Control (CNC) machining is a manufacturing process that has revolutionized the industrial sector, introducing precision and control in ways never before possible. CNC turning is one element of…