In CNC machining, software is the driving force behind transforming designs into precise and efficient products. Whether you’re new to CNC or looking to expand your knowledge, understanding the essential software tools is vital for success. In this article, we’ll introduce you to eight must-know CNC software tools that will empower you to excel in machining.
#1 CAD
Computer-Aided Design (CAD) software is a fundamental tool in CNC machining that enables the creation of precise and detailed 3D models. It plays a critical role in translating design concepts into digital representations that can be manufactured with accuracy. Here, we introduce you to AutoCAD, one of the most widely used CAD software in the industry, and explore its key features and capabilities in CNC machining.
Recommendation: AutoCAD
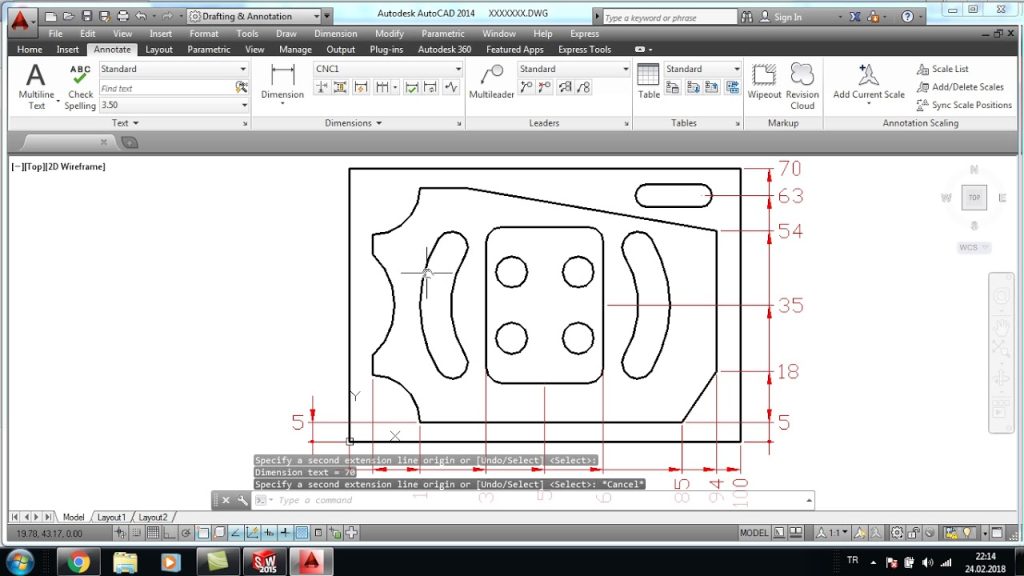
AutoCAD is a powerhouse in the world of CAD software, known for its robust capabilities and user-friendly interface. It offers a comprehensive set of tools and functionalities that facilitate the creation of intricate 3D models for CNC machining.
Key Features of AutoCAD for CNC Machining:
- Advanced Modeling Tools: AutoCAD provides a wide range of advanced modeling tools that allow users to create complex geometries with precision. These tools include 3D solids and surface modeling, parametric constraints, and dynamic blocks, empowering CNC machinists to design intricate components accurately.
- Dimensioning and Annotation: Accurate dimensioning and annotation are vital in CNC machining to communicate design intent. AutoCAD excels in this aspect, offering precise measurement tools, dimensioning options, and annotation capabilities, ensuring clear and comprehensive documentation for the manufacturing process.
- Compatibility and Interoperability: AutoCAD supports various file formats, making it compatible with other software used in CNC machining. This allows seamless integration with Computer-Aided Manufacturing (CAM) software, enabling a smooth transition from design to manufacturing.
- Customization and Automation: AutoCAD provides extensive customization options, allowing users to tailor the software to their specific needs. It supports the development of custom commands, scripts, and plugins, streamlining repetitive tasks and enhancing productivity in CNC machining workflows.
- Collaboration and Documentation: AutoCAD offers collaboration features that facilitate teamwork and communication among designers, engineers, and CNC machinists. Additionally, it enables the creation of detailed documentation, including technical drawings, part lists, and assembly instructions, ensuring clarity and accuracy throughout the manufacturing process.
AutoCAD’s powerful features and capabilities make it an indispensable tool for CNC machinists. Its intuitive interface and extensive functionality enable the creation of precise 3D models, laying the foundation for successful CNC machining projects.
#2 CAM
Computer-Aided Manufacturing (CAM) software is an essential component of CNC machining that bridges the gap between CAD models and machine instructions. It takes the digital designs created in CAD software and generates the toolpaths and instructions necessary for the CNC machine to manufacture the desired part. Know more about CAM in our CNC glossary for beginners.
Recommendation: Mastercam
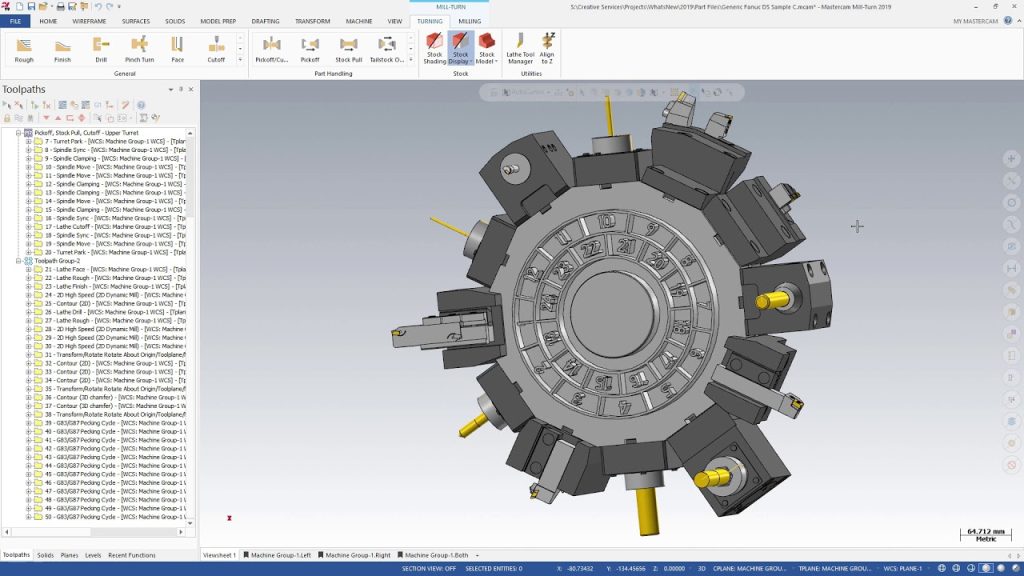
Mastercam is a leading CAM software that has gained popularity for its powerful features and versatility. It provides CNC machinists with a robust set of tools and functionalities to efficiently generate toolpaths, optimize machining operations, and deliver high-quality results.
Role of Mastercam in CNC Machining:
- Toolpath Generation: One of the primary functions of Mastercam is to generate toolpaths based on the CAD model and machining requirements. It offers a wide range of toolpath strategies, such as 2D contouring, 3D surface milling, pocketing, drilling, and more. These strategies allow CNC machinists to precisely define how the cutting tools will move to shape the part, ensuring optimal material removal and surface finish.
- Tool Library and Selection: Mastercam provides a comprehensive tool library that enables CNC machinists to define and manage various cutting tools. Machinists can select the appropriate tools based on material, operation type, and cutting parameters. This feature helps optimize machining processes and ensures accurate tooling selection for different operations.
- Simulation and Verification: Mastercam offers advanced simulation and verification tools that allow CNC machinists to visualize and validate the toolpaths before executing them on the CNC machine. This helps identify potential collisions, errors, or issues, preventing costly mistakes and ensuring safe and efficient machining operations.
- Post-Processing: After generating the toolpaths, Mastercam performs post-processing to convert the toolpath data into machine-specific instructions, usually in G-code format. This process ensures compatibility between the CAM software and the specific CNC machine being used.
- Optimization and Efficiency: Mastercam includes optimization features to enhance machining efficiency. These features may include optimizing toolpaths for faster cutting times, reducing tool wear, minimizing material waste, and improving overall productivity in CNC machining operations.
Mastercam’s extensive features and functions empower CNC machinists to streamline their workflows, optimize machining processes, and achieve precise and efficient results. Its user-friendly interface and comprehensive toolset make it a go-to choice for professionals in the CNC machining industry.
#3 Simulation and Verification
Simulation and verification software plays a vital role in CNC machining by allowing machinists to visualize and validate their machining operations before executing them on the actual CNC machine. This process is crucial for avoiding costly errors, reducing production time, and ensuring the highest quality of machined parts.
Recommendation: Vericut
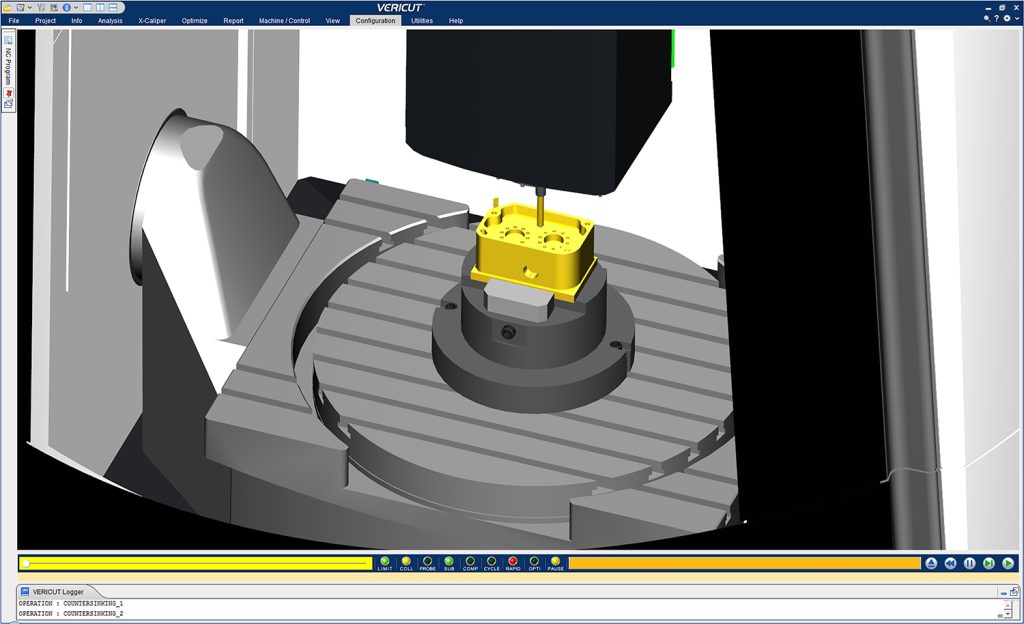
Vericut is a widely trusted simulation and verification software in the CNC machining industry. It offers comprehensive capabilities to simulate and verify CNC machining operations, enabling machinists to optimize their processes and deliver accurate results.
Key Features and Benefits of Vericut:
- Realistic Simulation: Vericut provides a realistic 3D simulation of the machining process, allowing machinists to visualize tool movements, material removal, and workpiece interactions. This helps identify potential collisions, interferences, and other issues that may arise during the actual machining process.
- Error Detection and Prevention: Vericut’s advanced algorithms analyze the toolpaths and machining operations, automatically detecting errors or potential issues. It alerts machinists to collisions, tool gouges, over-travel, and other problems, enabling them to make necessary adjustments and avoid costly mistakes.
- Optimization and Process Improvement: Vericut allows machinists to optimize toolpaths and machining parameters for maximum efficiency and improved surface finish. By simulating different scenarios, machinists can experiment with cutting strategies, feeds, speeds, and tool selections, ensuring the most efficient and productive machining process.
- Virtual Machine Environment: Vericut creates a virtual representation of the CNC machine, complete with its kinematics and controller. This realistic simulation provides machinists with a clear understanding of how the machine will execute the programmed toolpaths, helping to refine and fine-tune the machining process.
- Verification Reports: Vericut generates detailed verification reports that summarize the simulation results and provide insights into the machining process. Machinists can review these reports to analyze cutting times, tool engagements, and other important parameters, facilitating continuous process improvement.
#4 Tooling and Workholding Design
Tooling and workholding design software plays a significant role in CNC machining by enabling the creation of efficient and effective solutions for holding workpieces securely and optimizing the use of cutting tools. This software allows CNC machinists to design and develop tooling fixtures, jigs, and workholding devices that ensure precise and stable machining operations.
Recommendation: Autodesk Inventor
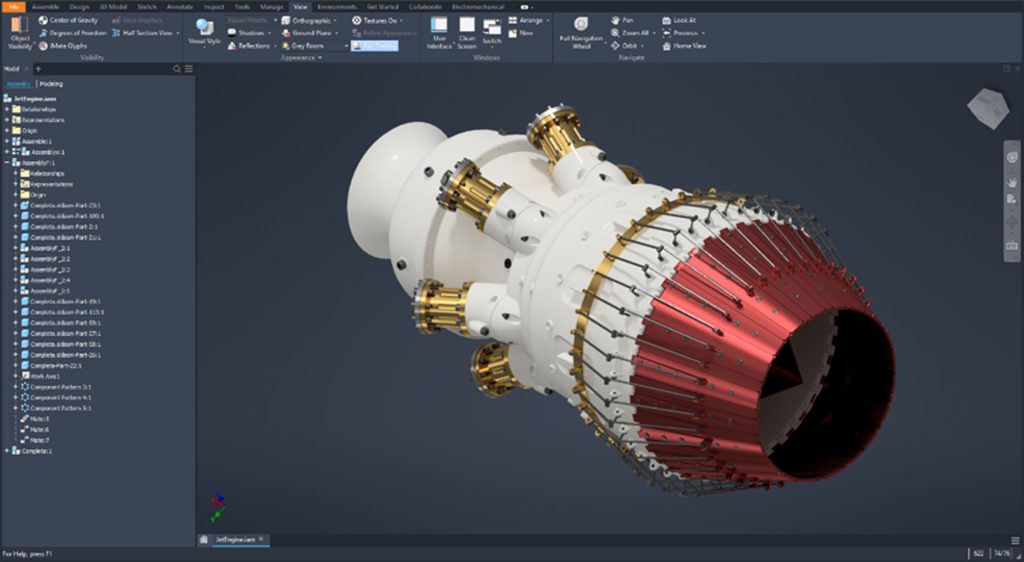
Autodesk Inventor is a powerful design software widely used in the CNC machining industry. It provides a comprehensive set of tools and functionalities specifically tailored for creating efficient tooling and workholding solutions.
Key Features and Benefits of Autodesk Inventor for CNC Machining:
- Parametric Design: Autodesk Inventor utilizes parametric design techniques, allowing CNC machinists to create 3D models of tooling fixtures and workholding devices. Parametric design enables the easy modification of dimensions, parameters, and features, ensuring flexibility and adaptability to specific machining requirements.
- Assembly Modeling: With Autodesk Inventor, machinists can assemble individual components of tooling and workholding systems to create a complete representation. This capability enables the visualization of how the components interact and fit together, ensuring proper alignment and functionality.
- Design Optimization: Autodesk Inventor offers tools for analyzing and optimizing designs. Machinists can simulate and evaluate the performance of tooling and workholding systems, considering factors such as stress analysis, material selection, and weight optimization. This aids in identifying potential issues and refining designs for enhanced performance.
- Collaboration and Documentation: Autodesk Inventor facilitates collaboration between designers, engineers, and CNC machinists. The software allows for the creation of detailed technical drawings, assembly instructions, and documentation for the manufacturing process. This ensures clear communication and precise execution of the tooling and workholding designs.
- Integration with CAM Software: Autodesk Inventor seamlessly integrates with CAM software, enabling the transfer of tooling and workholding designs directly into the machining workflow. This integration ensures compatibility and streamlines the transition from design to manufacturing, saving time and reducing errors.
#5 Nesting
Nesting software analyzes the shapes and dimensions of parts to be machined and generates the most efficient layout on a sheet of material, such as metal, wood, or plastic. By intelligently positioning and orienting the parts, nesting software aims to minimize scrap, optimize material usage, and reduce waste during the cutting process. This results in significant cost savings and improved efficiency in CNC machining operations.
Recommendation: SigmaNEST
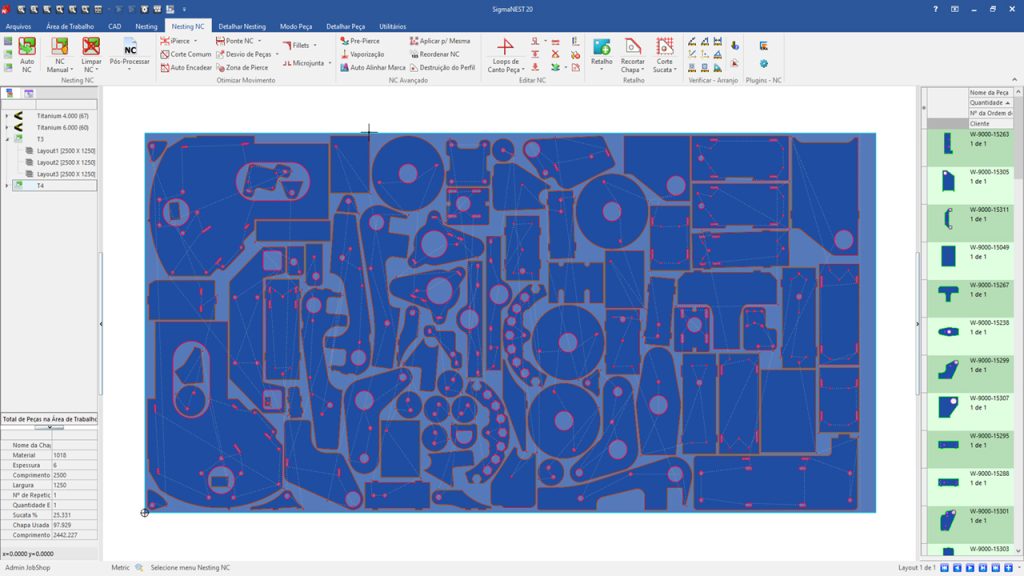
SigmaNEST is a leading nesting software trusted by CNC machinists for its advanced capabilities in material optimization. It offers a wide range of features and functionalities that contribute to maximizing material efficiency and reducing waste.
Key Benefits of SigmaNEST for CNC Machining:
- Advanced Nesting Algorithms: SigmaNEST utilizes sophisticated nesting algorithms that analyze part geometries, quantities, and material characteristics to determine the most efficient arrangement. It optimizes the layout by minimizing gaps and material remnants, resulting in significant material savings.
- Automatic Nesting: SigmaNEST automates the nesting process, saving time and effort for CNC machinists. With its automated capabilities, it quickly generates optimized layouts, reducing manual intervention and increasing productivity.
- Part-in-Part Nesting: SigmaNEST supports part-in-part nesting, where smaller parts can be nested within larger ones, taking advantage of unused space. This feature maximizes material usage, reduces waste, and enhances overall efficiency in CNC machining operations.
- Material Management: SigmaNEST provides tools for managing and tracking material inventory. It helps CNC machinists keep track of available stock, identify suitable material for nesting, and optimize the use of existing materials, leading to better inventory management and cost savings.
- Integration with CAD and CAM: SigmaNEST seamlessly integrates with CAD and CAM software, allowing CNC machinists to easily transfer part data and cutting instructions. This integration streamlines the workflow and ensures accurate communication between design, nesting, and machining processes.
#6 G-code Editors
code editors are essential tools in CNC machining that allow machinists to fine-tune and customize machine instructions written in G-code. G-code is the programming language used to control CNC machines and execute precise machining operations. G-code editors provide a user-friendly interface for editing, reviewing, and optimizing G-code programs.
Recommendation: Notepad++
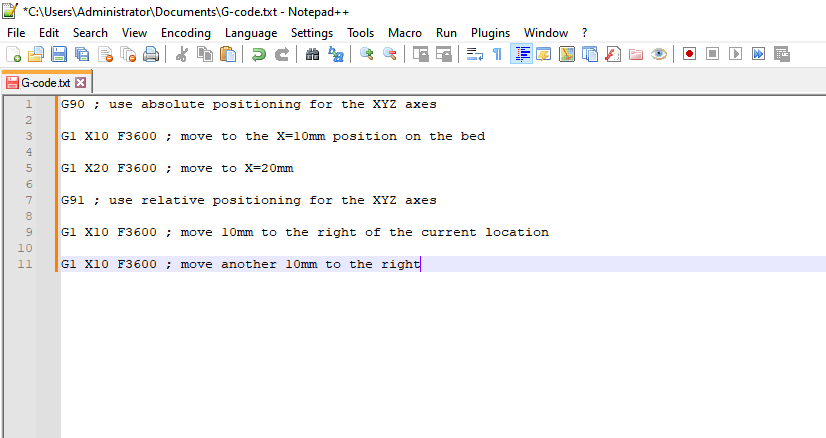
Notepad++ is a popular and versatile text editor that offers robust features for editing G-code and other programming languages. It provides a user-friendly environment with syntax highlighting, code formatting, and customizable options specifically tailored for G-code editing.
Key Features and Functionalities of Notepad++ for G-code Editing:
- Syntax Highlighting: Notepad++ recognizes G-code syntax and highlights different elements, making it easier to read and understand the code structure. It helps identify commands, parameters, comments, and other important elements, improving code readability and minimizing errors.
- Code Formatting and Indentation: Notepad++ supports code formatting and indentation, allowing machinists to organize and structure the G-code program for clarity. It enhances code legibility, simplifies navigation, and aids in identifying and resolving coding issues.
- Search and Replace: Notepad++ provides powerful search and replace functionalities, enabling machinists to quickly locate specific lines of code or make bulk changes. This feature saves time and effort when editing or customizing G-code programs.
- Macro Recording and Playback: Notepad++ allows users to record and save macros, which are sequences of editing commands. Machinists can record repetitive tasks and play them back, automating certain editing operations and improving productivity.
- Plug-ins and Customization: Notepad++ supports a wide range of plug-ins, extending its capabilities for G-code editing. Machinists can customize the editor by adding plug-ins to enhance functionality, integrate additional features, or tailor the environment to their specific needs.
#7 Post-Processor
CAM software generates G-code programs based on the part geometry, tooling, and machining parameters. However, different CNC machines have specific requirements and formats for interpreting G-code. Post-processor software takes the generic G-code output from the CAM software and customizes it to match the unique language and commands of the target CNC machine. This customization ensures seamless communication between the CAM software and the CNC machine, enabling accurate and optimized machining operations.
Recommendation: PostHASTE
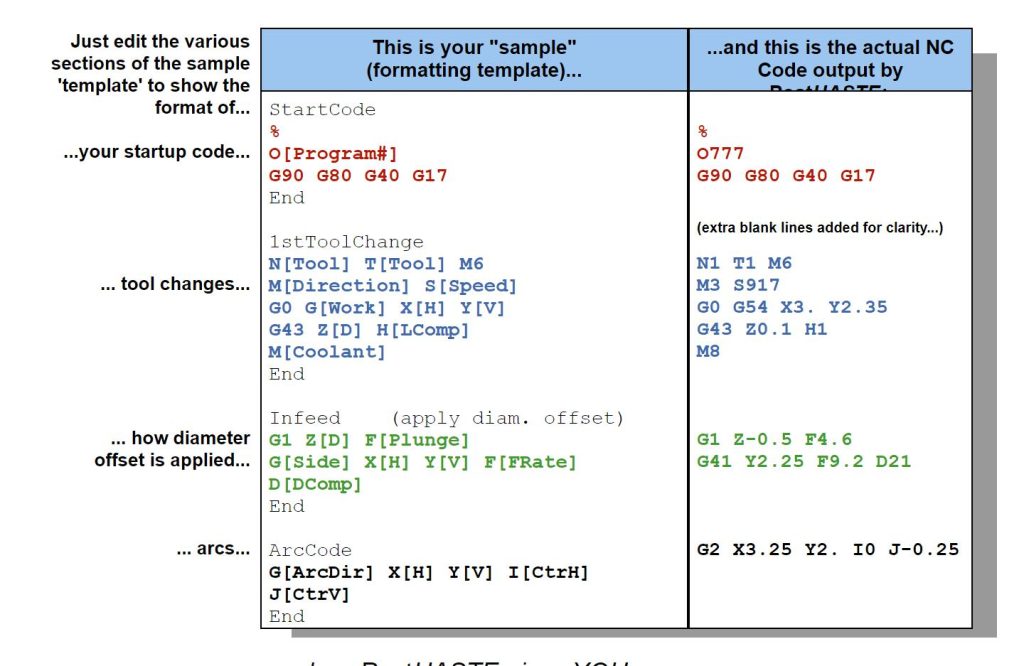
PostHASTE is a well-regarded post-processor software widely used in CNC machining. It offers a range of features and capabilities to customize and optimize G-code programs for specific CNC machines, ensuring compatibility and efficient execution.
Key Features and Benefits of PostHASTE for CNC Machining:
- Machine-Specific Customization: PostHASTE allows CNC machinists to tailor the G-code output to match the specific language and syntax of their CNC machine. It provides extensive customization options to define machine-specific codes, commands, and parameters, ensuring accurate interpretation and execution.
- Compatibility with CAM Software: PostHASTE seamlessly integrates with various CAM software, facilitating a smooth transfer of G-code programs. It supports common file formats and communication protocols, enabling CNC machinists to import G-code from different CAM systems and ensure compatibility with their CNC machines.
- Optimization and Code Efficiency: PostHASTE offers optimization features to enhance the efficiency and performance of G-code programs. It can analyze the generated code, identify potential improvements, and apply optimizations such as toolpath smoothing, code reduction, or adaptive feed rates. These optimizations improve machining speed, accuracy, and overall productivity.
- Simulation and Verification: PostHASTE provides simulation and verification capabilities to visualize and validate the customized G-code program. It allows CNC machinists to review the post-processed code, check for errors, visualize tool movements, and ensure proper machine operation before the actual machining process.
- Post-Processing Reports: PostHASTE generates detailed reports summarizing the post-processing results. These reports help CNC machinists review and validate the modifications made to the G-code, ensuring accuracy and providing documentation for future reference.
Recommended Read: 5 Exciting Evolutionary Milestones in CNC Machining History
#8 Metrology and Inspection
Metrology and inspection play a critical role in CNC machining by ensuring that the machined parts meet the required tolerances, dimensions, and specifications. By employing metrology and inspection techniques, CNC machinists can identify any deviations or defects in the manufactured parts, allowing for corrective actions to be taken promptly. This process helps maintain high-quality standards, reduces waste, and ensures customer satisfaction.
Recommendation: PolyWorks
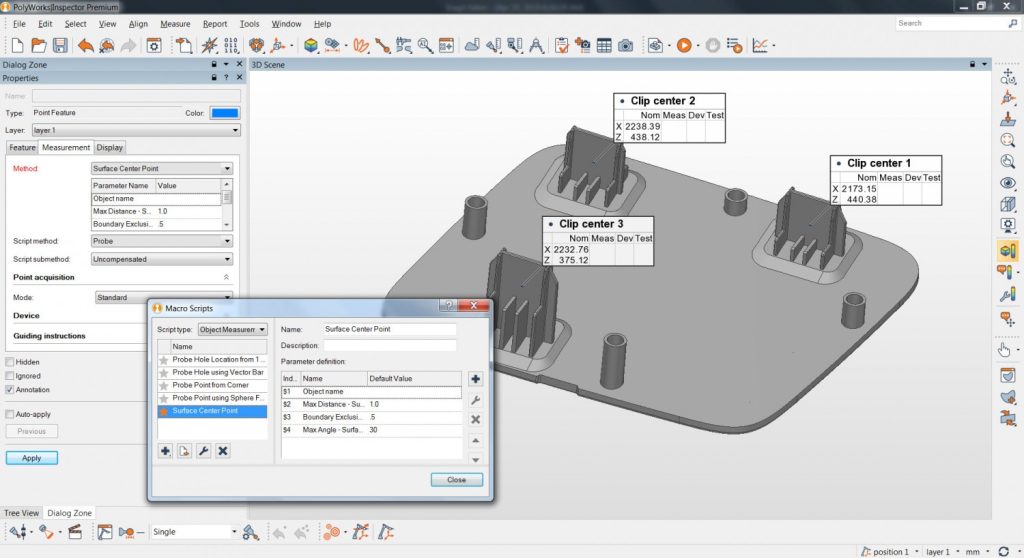
PolyWorks is a renowned metrology and inspection software widely used in CNC machining. It provides a comprehensive set of tools and functionalities for accurate measurement, analysis, and reporting of machined parts.
Key Features and Benefits of PolyWorks for CNC Machining:
- Measurement Capabilities: PolyWorks supports various measurement techniques, including point cloud scanning, laser scanning, and probing. It enables CNC machinists to capture precise measurements of machined parts, ensuring accuracy and repeatability.
- Dimensional Analysis: PolyWorks offers advanced dimensional analysis tools to evaluate the measured data and compare it against the desired specifications. It helps identify any deviations or out-of-tolerance conditions, allowing for corrective actions to be taken to ensure the quality and precision of the machined parts.
- Surface Inspection: PolyWorks provides surface inspection capabilities, allowing CNC machinists to analyze surface quality, detect defects, and verify the integrity of machined surfaces. It helps identify issues such as surface roughness, imperfections, or deviations from the desired surface profile.
- Reporting and Documentation: PolyWorks facilitates the creation of detailed inspection reports, providing comprehensive documentation of the measurement results. Machinists can generate customized reports with graphical representations, statistical analysis, and annotations. These reports serve as valuable records and aid in communication with stakeholders, ensuring transparency and accountability.
- Compatibility and Integration: PolyWorks is compatible with a wide range of measurement devices and CNC machines, allowing seamless integration into the machining workflow. It supports standard file formats for data exchange, ensuring compatibility with other software and enabling efficient data sharing.
Other Articles You Might Enjoy
- Revolutionizing CNC Machining for the Future of Smart Wearables
Introduction: CNC Machining and Smart Wearables CNC (Computer Numerical Control) machining is a manufacturing process that utilizes computerized controls to operate and manipulate machine tools, converting raw materials into finished…
- Plastic vs. Metal CNC Machining: A Detailed Comparison?
CNC Machining: An Essential Process Across Industries Computer Numerical Control (CNC) machining is a digital manufacturing technology that makes use of pre-programmed computer software to dictate the movement of various…
- Cobalt Chrome Alloys in Medical Implant Manufacturing: CNC Machining Considerations?
Introduction: Overview of Cobalt Chrome Alloys in Medical Implant Manufacturing Cobalt chrome alloys are extensively involved in the production of medical device implants due to their superior characteristics such as…