CNC lathe is a machine tool widely used in the field of machining of custom parts. It utilizes computerized controls to automate and precisely control various machining operations. CNC lathes are widely used in manufacturing industries for tasks such as cutting, drilling, turning, and shaping materials like metal, plastic, and wood. With their ability to execute complex operations with speed and accuracy, CNC lathes have become indispensable in modern manufacturing processes.
Understanding the key components of a CNC lathe is crucial for beginners venturing into the world of CNC machining. These components play vital roles in the machine’s functionality and directly influence the quality of the custom machined parts. By familiarizing themselves with these essential components, beginners can grasp the fundamental aspects of CNC lathe operations and develop a strong foundation for their machining skills.
In this article, we will delve into the five essential components of a CNC lathe. By exploring each of them in detail, you will gain a comprehensive understanding of how these elements contribute to the functionality and capabilities of a CNC lathe.
#1 Chuck
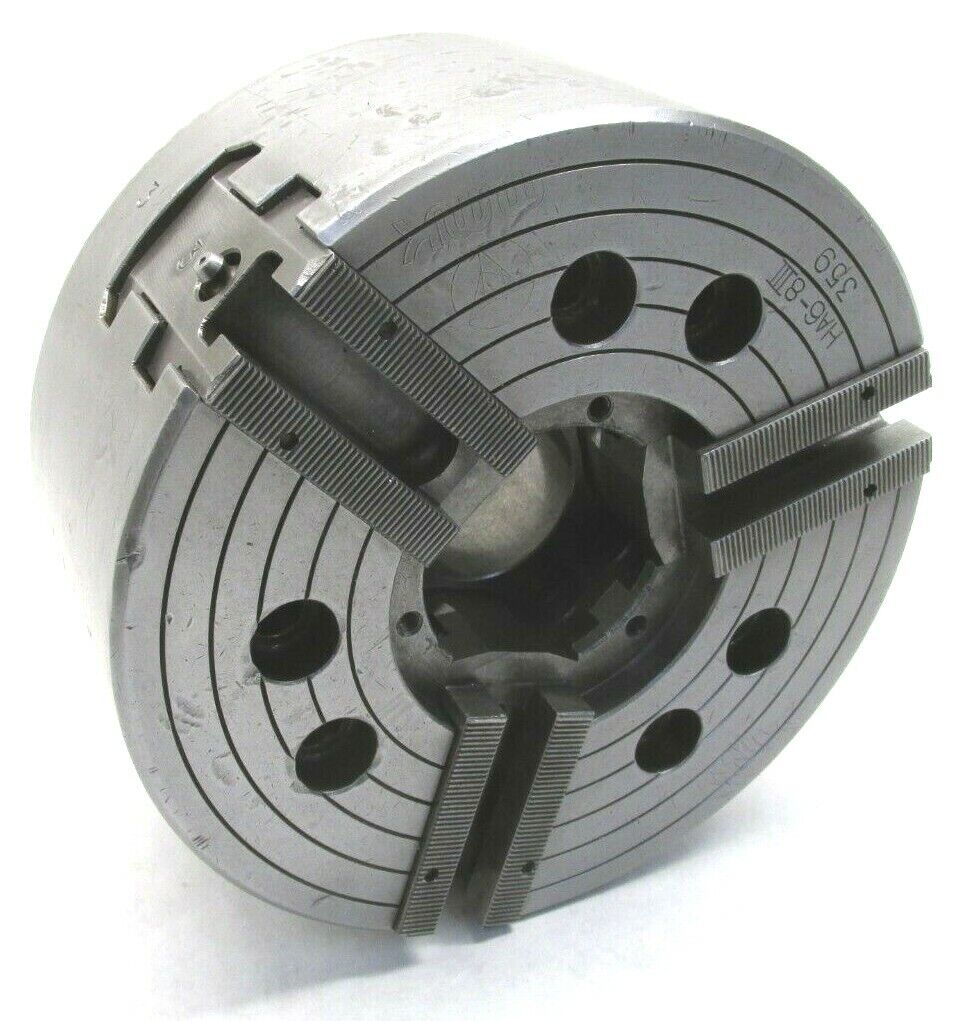
The chuck is a vital component of a CNC lathe that serves the purpose of securely holding the workpiece in place during machining. It is typically mounted on the lathe’s spindle and acts as a gripping mechanism for the workpiece. The chuck’s primary function is to provide a firm and stable grip on the workpiece, allowing it to rotate synchronously with the spindle. This rotational movement enables various cutting tools to engage with the workpiece and perform machining operations with precision.
There are different types of chucks available for CNC lathes, each designed for specific applications:
Three-jaw chucks
These chucks have three gripping jaws that move simultaneously and symmetrically. They are suitable for gripping cylindrical workpieces with a consistent diameter, offering quick and efficient setup.
Four-jaw chucks
Unlike three-jaw chucks, four-jaw chucks allow independent movement of each jaw. This feature enables them to grip irregularly shaped or non-cylindrical workpieces. Although it requires more time to set up, a four-jaw chuck provides greater flexibility in securing challenging workpiece geometries.
Proper alignment and tightening of the chuck are critical for achieving accurate machining results. A misaligned or loose chuck can lead to unwanted vibrations, poor surface finishes, and dimensional inaccuracies in the machined part. Therefore, it is crucial to align the chuck concentrically with the spindle axis and ensure proper tightening to maintain stability during machining operations. Regular inspection and maintenance of the chuck are essential to prevent any potential issues that may affect the overall machining accuracy. By paying attention to the chuck’s alignment and tightening, beginners can ensure consistent and precise machining results.
#2 Tailstock
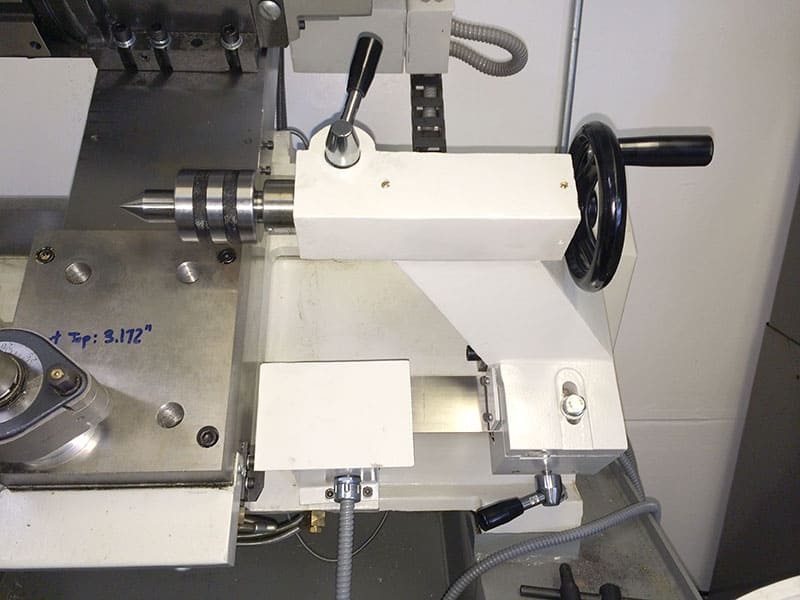
The primary task of the tailstock is to provide stability and support to the workpiece during machining. It helps counterbalance the cutting forces exerted on the workpiece, preventing it from bending or deflecting. The tailstock consists of a quill that can be extended or retracted, allowing it to make contact with the workpiece and provide additional support.
The tailstock is particularly useful when machining long workpieces that extend beyond the chuck. By adjusting the tailstock’s position and extending the quill, it can effectively support the free end of the workpiece, minimizing vibration and enhancing machining accuracy. Additionally, the tailstock can be used to stabilize workpieces that are prone to flexing or have irregular shapes, ensuring consistent and precise machining results.
Proper adjustment of the tailstock is essential for maintaining alignment and avoiding deflection during machining. Misalignment or improper adjustment can result in inaccurate hole depths, or increased tool wear. To ensure optimal performance, you should verify that the tailstock is aligned parallel to the lathe’s bed and securely clamped in place. Regular inspection and adjustment of the tailstock’s alignment are necessary to mitigate any potential deflection issues and ensure the production of accurate and high-quality machined parts.
#3 Spindle
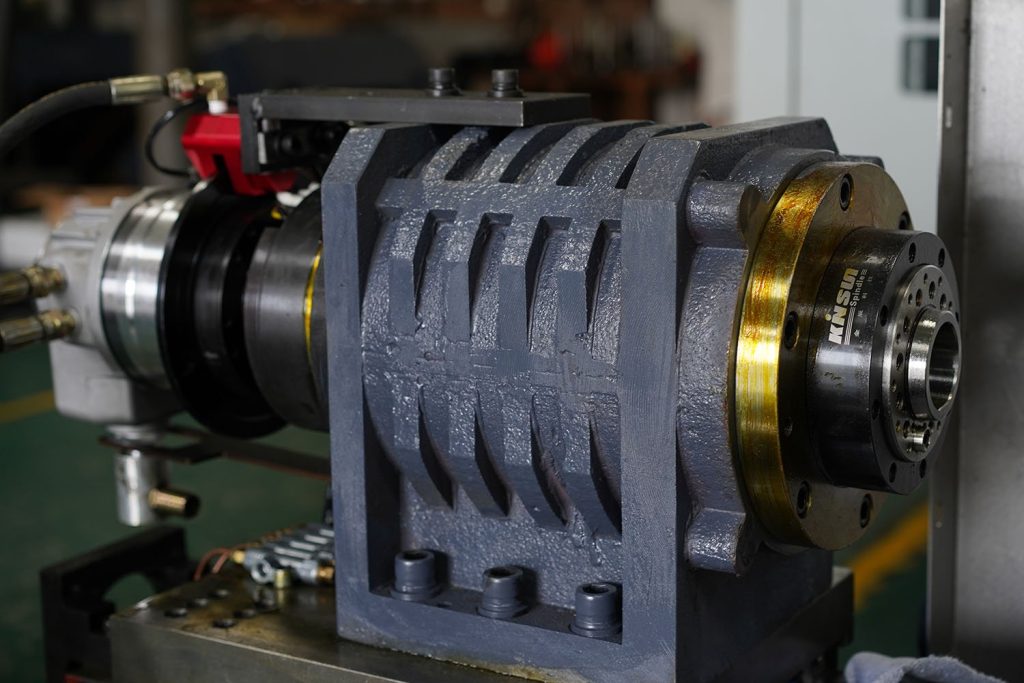
The spindle is typically driven by a motor and is responsible for providing the rotational motion necessary for machining operations, allowing the cutting tools to engage with the material and perform various machining operations such as turning, facing, drilling, and threading. The workpiece is securely mounted in the chuck, and as the spindle rotates, the cutting tools remove material to shape the workpiece according to the programmed specifications.
The spindle speed and direction can be adjusted to accommodate different machining operations and workpiece materials. Higher spindle speeds are often used for operations requiring precision, such as finishing cuts, while lower speeds are suitable for heavy roughing cuts. Additionally, the spindle can rotate in both clockwise and counterclockwise directions, enabling operations like internal threading or reverse turning.
Maintaining the precision of the spindle is crucial for achieving accurate and high-quality machined parts. Any misalignment or excessive runout in the spindle can result in dimensional inaccuracies, poor surface finishes, and increased tool wear. Regular inspection and maintenance, including checking for proper alignment and runout, are necessary to ensure the spindle’s precision.
Proper lubrication of the spindle is also essential to minimize friction and heat generation. Lubricants help reduce wear and ensure smooth rotational movement, extending the lifespan of the spindle and maintaining its performance. Regular lubrication and following the manufacturer’s guidelines for lubrication intervals are important practices for beginners to maintain the spindle’s optimal functioning and prolong its longevity.
#4 Tool Turret
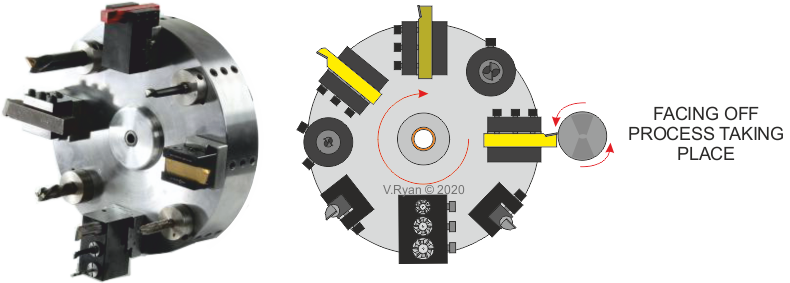
The tool turret is a vital component of a CNC lathe that serves the purpose of holding multiple cutting tools. It is typically positioned on the lathe’s cross-slide and is responsible for indexing and presenting the desired tool to engage with the workpiece.
The tool turret features multiple tool stations, each capable of holding a different cutting tool. These tools can include turning tools, boring tools, threading tools, and more. The turret is designed to enable rapid and precise indexing of the tool stations, allowing for seamless tool changes during machining operations.
The tool turret provides significant advantages in terms of efficiency and reduced setup time. With a tool turret, operators can pre-load multiple tools in the turret stations, eliminating the need to manually change tools for each operation. When a different tool is required, the turret can quickly rotate to present the desired tool, significantly reducing the time required for tool changes and enhancing productivity.
Proper tool selection and tool turret alignment are crucial for achieving efficient machining results. The selection of the appropriate cutting tools based on the specific machining requirements, workpiece material, and desired outcomes is essential. Each tool’s geometry, material composition, and cutting parameters must be considered to ensure optimal performance and tool life.
Moreover, accurate alignment of the tool turret is necessary to maintain precision during machining. Misalignment can lead to tool runout, poor surface finishes, and dimensional inaccuracies. Regular inspection and adjustment of the tool turret alignment, following the manufacturer’s guidelines, are essential practices for beginners to ensure efficient tool changes and consistent machining results.
#5 Tool Holders
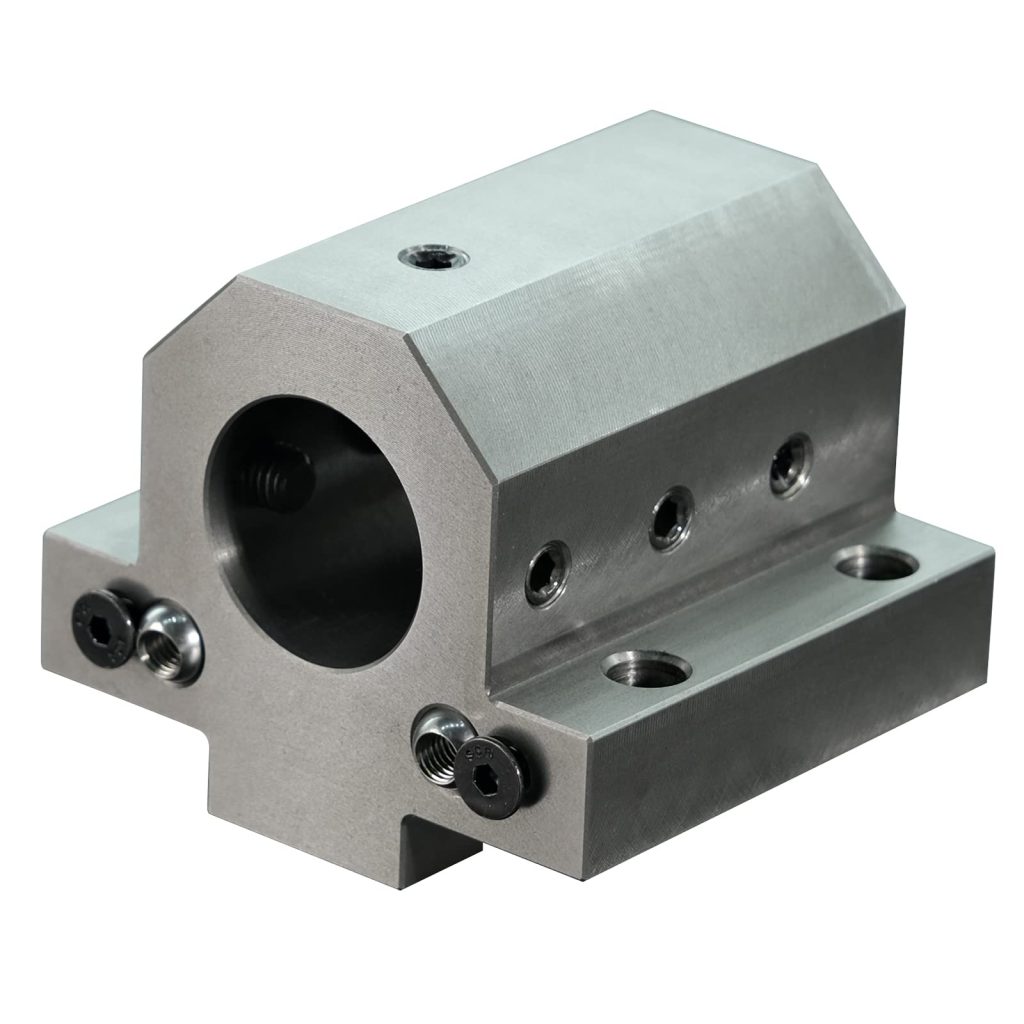
Tool holders are designed to securely grip the shank of the cutting tool and hold it firmly in place within the tool turret. They often feature clamping mechanisms such as collets, set screws, or hydraulic systems to ensure a tight and secure grip. The tool holder’s primary function is to provide stability and vibration damping, allowing for precise and efficient cutting.
There are various types of tool holders available, each suited for specific cutting tools and applications. Collet chucks, for example, utilize collets to hold the cutting tool and provide excellent gripping force and concentricity. Tool blocks, on the other hand, allow for the use of square or rectangular tool bits, offering versatility in tool selection.
Selecting the appropriate tool holders is crucial for achieving tool stability and accuracy during machining. The choice of tool holder depends on factors such as the type of cutting tool, the machining operation, and the desired precision. Proper tool holder selection ensures that the cutting tool remains securely in place, minimizing vibrations, tool deflection, and the risk of tool pull-out.
Additionally, the tool holder should provide sufficient clearance and accessibility for chip evacuation, as chip accumulation can negatively impact machining performance. Beginners should consult tool manufacturer recommendations and seek guidance from experienced machinists to choose the most suitable tool holders for their specific machining needs.
Conclusion
We’ve explored the vital components of a CNC lathe: chuck. Understanding these components is crucial for beginners in CNC machining as they form the foundation for operating the machine effectively and achieving precise results. It’s worth noting that CNC lathes share many components with CNC mills, such as the spindle and tool holders, which shows the versatility and commonality across different CNC machines.
However, practical experience and continuous learning are key to enhancing CNC lathe skills. By experimenting with different techniques and materials, beginners can refine their abilities and unlock new possibilities in machining. Remember, CNC machining is an ever-evolving field, so embrace the journey of becoming a skilled operator. With dedication and practice, you’ll unleash the full potential of a CNC lathe and produce remarkable precision parts.
Other Articles You Might Enjoy
- High-Precision CNC Machining for Cutting-Edge Biotechnology
Introduction to High-Precision CNC Machining in Cutting-Edge Biotechnology CNC (Computer Numerical Control) machining is a prominent automated manufacturing process that manipulates tools around multiple axes with computer-driven precision. Significantly, it…
- Custom CNC Machining Services: When to Choose Low Volume over High Volume Production?
Introduction to Custom CNC Machining and Volume Selection in Production Custom CNC machining is a technically advanced process that involves the use of computerized machinery to design, produce, and finish…
- Precision CNC Machining of Steel: High-Volume Production
Precision CNC Machining and High-Volume Production As an integral part of modern manufacturing processes, Precision Computer Numerical Control (CNC) machining brings about unmatched accuracy and consistency in the production of…