At the forefront of modern production lie intelligent manufacturing systems, meticulously crafted to meet the flexible demands of cnc machining various parts and swiftly adapt to the ever-changing needs of customers. These systems enable true rapid machining. However, the complexity arises during the initial installation and setup of all the components. In this article, we will delve into the realm of jigs and fixtures systems for smart manufacturing solutions. But before we delve into that, let’s examine the current state of intelligent manufacturing technology.
Intelligent Manufacturing Today
Intelligent manufacturing stands as an inseparable component of the Industry 4.0 theory, which is still in its developmental stage, constantly evolving and refining. While the concept continues to be perfected, the smart manufacturing market is poised to experience exponential growth once the technology reaches maturity. These advanced systems align perfectly with the requirements of modern customers who seek rapid production of small batches or even customized individual parts with minimal lead time. At present, several solutions automate the rapid cnc machining process to a significant extent. Automating the machine tool itself is a relatively straightforward process that involves loading the required numerical control (NC) programs in the correct sequence.
However, the real challenge lies in loading, unloading, and fixing the parts in their correct positions. Robotic arms handle the loading and unloading operations, but the responsibility of securing the part during the cnc machining process rests with the jigs and fixtures. The complexity arises when the intelligent manufacturing system needs to process entirely different parts, such as small cylinders, plates, or crankshafts, each requiring specialized clamping techniques. While intelligent clamping solutions can partially address this issue by incorporating adjustable jigs and fixtures capable of clamping multiple similar parts, a comprehensive solution is still needed.
Jigs & Fixtures for Intelligent Manufacturing
Before we delve further, let’s clarify the distinction between jigs and fixtures. Jigs are primarily used to restrict the movement of the blank within the working zone of the machine tool. For instance, they may include stoppers that prevent horizontal movement of the part on the mill’s working table. Fixtures, on the other hand, are specialized tools employed to securely hold the part in place, such as bolts and special nuts used to fasten the blank. At Want.Net, we specialize in providing Quick-turn, CNC machining services, catering to various requirements such as rapid prototyping, forming and fit testing, jigs and fixtures, and functional components for end-use applications.
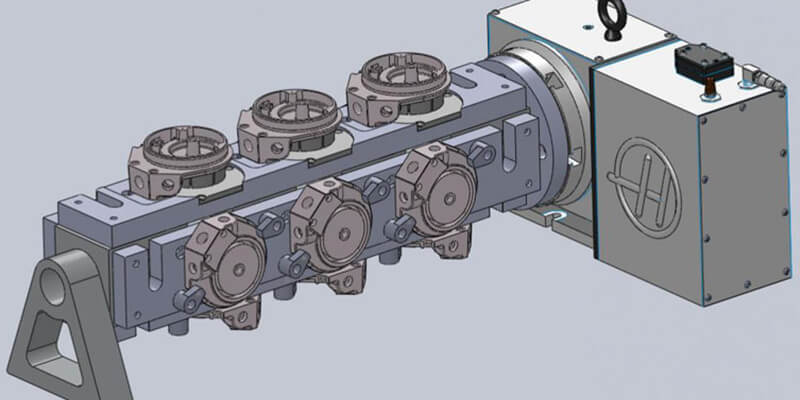
Several types of jig and fixture mechanisms exist, each serving different purposes. The simplest and most flexible approach involves assembling standard blocks using bolts, akin to constructing with LEGO bricks. Although this method offers versatility, it is time-consuming to assemble such fixtures. Alternatively, universal standard clamps and chucks can be utilized, providing flexibility in manual machining operations as operators can inspect and rectify any setup issues. However, smart manufacturing systems necessitate the use of automated flexible jig tools to streamline production processes.
Main Stages of Jig and Fixture Design for Smart Manufacturing Systems
Designing jigs and fixtures for intelligent manufacturing is a complex process that often surpasses the challenges involved in developing the actual product manufactured using these fixtures. To achieve the desired CNC fixturing tool, several key stages must be completed:
- Choosing the base surfaces: It is advantageous, if possible, to incorporate multiple sets of base surfaces within a single system, enhancing its flexibility and adaptability.
- Determining the adjustment interval: This decision determines the level of intelligence and flexibility of the system. A wider and more variable adjustment interval corresponds to a more sophisticated and adaptable tooling setup.
- Selecting the fixtures: Careful selection of appropriate fixtures is crucial for optimal clamping and stability during machining operations.
- Choosing the fixture mechanism: Automated systems can employ various drive mechanisms such as electric, pneumatic, hydraulic, or mixed drives. The choice depends on the machine tool’s existing drive system, although specific tools may require their own dedicated drives. For example, pneumatic drives are suitable for vacuum fixture designs, while electric drives are necessary for magnet tooling.
- Designing the complete assembly: This involves creating all the necessary parts and determining the precise fixture cycle to ensure efficient and reliable operations.
- Programming the tooling: To achieve automation, the drives are controlled by specialized numerical control (NC) programs, tailored for each specific system.
- Preparing for manufacturing: Once the design and programming stages are completed, the system is prepared for production, ensuring that all components are fabricated and assembled according to specifications.
The Significance of Fixture Development
Intelligent adjustable clamping systems offer numerous advantages, making the lengthy and complex development and manufacturing process worthwhile:
- Cost reduction: A well-built intelligent jig tool can replace multiple simpler clamping mechanisms, leading to significant cost savings in manufacturing.
- Operator exclusion: For efficient smart manufacturing systems, minimizing human intervention is crucial. Intelligent clamps enable fully automated setup changes for successive batches, eliminating the need for constant operator involvement.
- Time savings: The setup process for different parts is often the most time-consuming aspect of rapid machining. With an adjustable intelligent clamping system, a wide range of parts can be machined without the need to alter the tooling. Operators need only ensure that the parts fall within the adjustment boundaries.
In conclusion, adapting fixtures and jigs for intelligent manufacturing entails overcoming complex challenges. By leveraging adjustable clamping systems, smart manufacturing can achieve efficient production, reduced costs, increased automation, and substantial time savings. With ongoing advancements and continuous improvement, the future of intelligent manufacturing holds immense promise for the industry.
Recommended Reads:
- Mastering the Art of Plastic CNC Machining: A Comprehensive Guide
- Mastering Teflon Machining: From Design to Finished Product
- Minimizing Chatter in CNC Machining: Tips and Tricks for Better Surface Finish
- Which Is the Most Expensive CNC Machine?
- 6 CNC Machining Design Mistakes to Avoid
Other Articles You Might Enjoy
- Precision CNC Machining for High-Performance Industrial Machinery
Precision CNC Machining for High-Performance Industrial Machinery The process of Precision CNC (Computer Numerical Control) machining is at the core of manufacturing high-performance industrial machinery. This technique leverages a computer's…
- CNC Machining for Medical Applications: Compliance and Material Selection?
Introduction to CNC Machining in Medical Applications CNC or Computer Numerical Control machining is a manufacturing process wherein pre-programmed computer software dictates the movement of factory tools and machinery. This…
- Material Versatility in CNC Machining: From Titanium to Thermoplastics
Introduction to CNC Machining CNC machining stands as a cornerstone in the manufacturing sector, enabling the precise creation of parts and components. This process utilizes computer numerical control (CNC) to…