In the early days of manufacturing, Henry Ford revolutionized the industry with his automated assembly lines, producing identical high-quality products at an affordable price. People were thrilled to have access to goods that would have otherwise been out of their reach. However, in today’s world, consumers are seeking something more than uniformity. With increased wealth and a desire for individuality, the demand for custom prototypes is on the rise, poised to surpass mass production in the future.
Emphasizing Individuality through Customization
The public has grown weary of conformity. Thanks to modern banking and increased affluence, expensive gadgets and cars are within reach for many. Consequently, it’s no surprise that everyone seems to own the same items. Imagine purchasing a brand-new Lexus, only to spot an exact replica of your car the very next day.
Now, consider this: you order custom prototype lights for your Lexus. Not only will no one else have the same lights, but you also have the opportunity to participate in the design process, making them as extravagant as you desire. Customization allows for the creation of unique objects or modifications to existing ones, ensuring individuality and personal expression.
Perfectly Tailored Results
We’ve all experienced the disappointment of purchasing something that doesn’t quite fit. Whether it’s clothes, shoes, furniture, or even electronic devices and appliances, finding the perfect fit can be a challenge. In the past, we had to settle for products that were “close enough” or endure the inconvenience of ill-fitting items.
However, modern custom manufacturers can create products that are perfectly tailored to your specifications. Advanced technologies like 3D scanning enable engineers to take precise measurements in minutes, ensuring a perfect fit. Whether it’s a shoe, a car light installation, or a prosthetic limb, customization allows for precise adaptation to individual needs.
The Need for Rapid Product Development
In the past, a single automated production line could churn out the same product for years on end. But in today’s fast-paced society, consumers crave constant innovation. New iPhone models are released annually, and car designs are updated every few years. Traditional mass production methods are struggling to keep up with the demand for customization and rapid prototyping. Manufacturers need flexible equipment, rapid prototyping capabilities, and increased customization options to satisfy even the most discerning customers.
Technological Advancements Driving Custom Prototyping
The industrial landscape is evolving at an astonishing rate, with new techniques and equipment continually emerging to enhance manufacturing efficiency and meet customer demands. A clear trend toward custom prototyping, individual orders, and small-batch manufacturing of highly personalized products is evident in the recent developments in manufacturing techniques.
3D Printing: Pushing the Boundaries of Customization
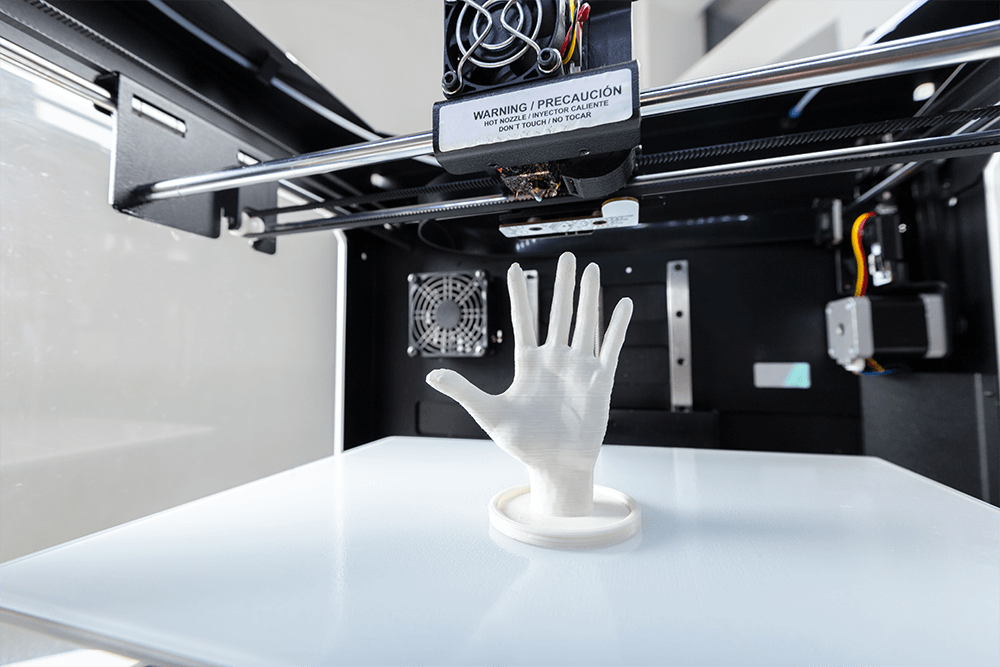
One such advancement is 3D printing, also known as additive manufacturing. This revolutionary technology utilizes lasers and computer-programmed movements to create three-dimensional objects layer by layer. Not only can 3D printers produce plastic prototypes with a wide range of material properties, but they also eliminate the need for special tooling or blanks, making the manufacturing process more efficient and cost-effective.
The versatility of 3D printing is remarkable. From intricate geometries to functional parts, this technology is capable of producing complex and customized objects, pushing the boundaries of what was once thought possible. In the medical field, 3D printing has enabled the creation of artificial bones using titanium, prosthetics tailored to individual patients, and metal dental implants. The potential for customization and personalization in 3D printing is truly limitless.
Vacuum Casting: Bridging the Gap between Small Batches and Custom Goods
Another technique making waves in the realm of custom prototypes is vacuum casting. Building upon the foundation of silicone casting, this method involves pouring liquid polymerinto a pre-made silicone mold to create plastic prototypes. Vacuum casting is particularly well-suited for small-batch production, catering to specific groups or allowing for live condition tests on prototypes.
Previously considered a hobbyist activity, silicone casting has now evolved with the advent of vacuum casting, gaining traction in professional prototyping shops. By obtaining a master model, typically through CNC machining for durability, manufacturers can create multiple silicone molds, expanding the production capacity from small to medium-sized or even large batches.
Vacuum casting bridges the gap between custom goods and mass production, offering flexibility and efficiency. It provides the opportunity for small-scale production runs, meeting the demands of niche markets and customers with unique requirements. This method enables manufacturers to deliver highly customized products without sacrificing quality or cost-effectiveness.
CNC Machining: Precision and Versatility in Custom Manufacturing
CNC machining, a fundamental and complex manufacturing process, has also undergone significant advancements. Gone are the days of large plants filled with machinists operating intricate machinery. Today, a small workshop equipped with a few CNC machine tools can produce a wide range of products with precision and versatility.
The introduction of advanced CNC machining services has simplified the process, eliminating the need for technical expertise. Now, customers can bring their sketches of customized vapes, car steering wheels, sculptures, and more. With the guidance of skilled professionals, the appropriate materials can be chosen based on functionality and properties. From there, the CNC machine, guided by computer programming, executes precise movements to manufacture even the most complex parts quickly and cost-effectively.
CNC machining offers unparalleled customization options, enabling manufacturers to fulfill individual needs and design specifications. It allows for the creation of intricate details, precise dimensions, and various material options, resulting in high-quality custom prototypes that meet the unique demands of customers.
Remarkable Speed in Custom Prototyping
In addition to the advancements in customization capabilities, modern technologies have drastically reduced the time required for rapid prototyping. For example, a 3D printer can create a medium-sized part within a matter of days. Similarly, silicone molding and CNC machining processes offer quick turnaround times, typically within a week. With such efficiency, custom products can be obtained almost as quickly as their mass-produced counterparts, with shipping costs and delivery times being comparable.
This remarkable speed in custom prototyping empowers manufacturers to meet tight deadlines, respond rapidly to market demands, and iterate designs efficiently. It also allows customers to enjoy personalized products without sacrificing convenience or prompt delivery.
Embracing a Customized Future
As consumer expectations continue to evolve, the future of manufacturing lies in custom prototypes. The desire for individuality, perfectly tailored products, and rapid innovation is driving the shift away from traditional mass production. Technological advancements in 3D printing, vacuum casting, and CNC machining have unlocked new possibilities, enabling manufacturers to offer highly customized, precision-crafted goods at a competitive pace.
In this customized future, every product becomes a unique reflection of its owner, combining functionality, aesthetics, and personal expression. As manufacturers and customers embrace the power of customization, the manufacturing landscape will be transformed into a realm where creativity, innovation, and individuality thrive.
Recommended Reads
- 9 Advantages of CNC Machining Over Conventional Machining
- How to Optimize Metal Machining Strategies for Improved Prototyping
- CNC Milling: Revolutionizing Automotive Part Production
- How Should Manufacturers Choose Materials For Their Prototypes?
- Preparing Your CAD Model for CNC Machining
Other Articles You Might Enjoy
- Precision CNC Machining for High-Performance Industrial Machinery
Precision CNC Machining for High-Performance Industrial Machinery The process of Precision CNC (Computer Numerical Control) machining is at the core of manufacturing high-performance industrial machinery. This technique leverages a computer's…
- CNC Machining for Medical Applications: Compliance and Material Selection?
Introduction to CNC Machining in Medical Applications CNC or Computer Numerical Control machining is a manufacturing process wherein pre-programmed computer software dictates the movement of factory tools and machinery. This…
- The Future of Manufacturing: Exploring the Potential of Insert Molding in CNC Machining
As the manufacturing industry evolves, innovative techniques such as insert molding are reshaping the landscape of CNC machining. This article delves into the potential of insert molding in CNC machining…