When it comes to creating prototypes for milling machine parts, the selection of suitable materials plays a crucial role in the overall success of the project. At Want.Net, we understand the importance of making informed decisions when it comes to material choices. In this article, we will delve into two real stories inspired by actual projects, highlighting the significance of material selection in achieving desired outcomes. These stories provide valuable insights into the decision-making process, focusing on aesthetics, functionality, and cost-effectiveness. Our commitment to providing optimal services to our customers drives us to consider even the smallest details.
Case #1: Maintaining Color Consistency Across Different Plastic Parts
One of our longstanding customers approached us with a new prototype inquiry. The customer specifically requested white PA6 (Nylon) for three of the parts, with two of them needing to be glued together and polished. However, we encountered a challenge with Nylon—a material known for its “self-lubricating” properties—making it unsuitable for effective gluing with other materials. Additionally, due to the nature of the material, polishing the milled surface would result in a rougher texture.
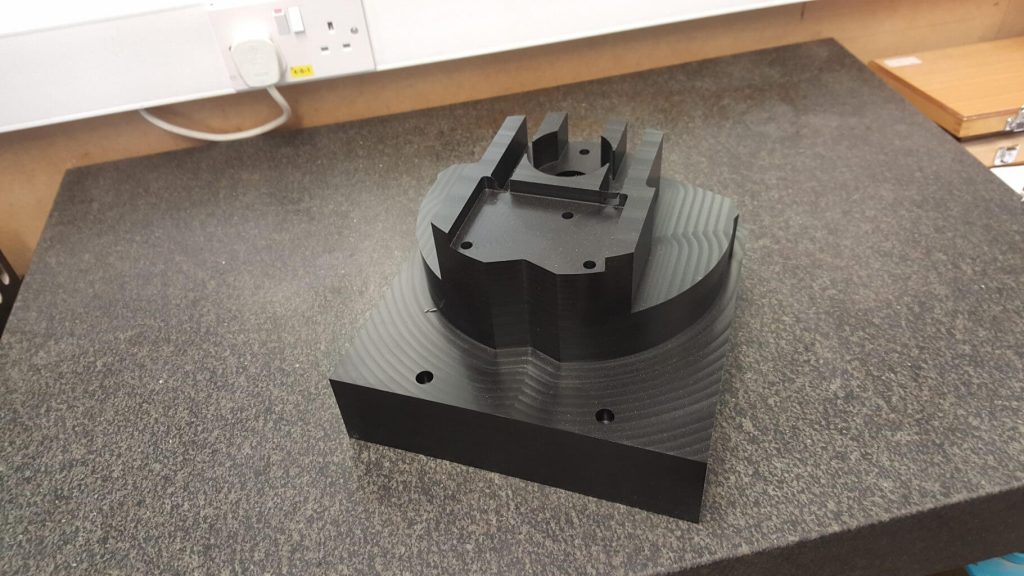
To address this issue, we proposed an alternative solution to the customer. We suggested replacing the two parts that required gluing with white PC, a material that could be glued, although with slightly less strength. Moreover, PC could be polished to achieve a smoother finish. However, the customer had a specific concern regarding the aesthetics of the prototype. In order to present a cohesive appearance to important clients or at exhibitions, it was crucial to maintain color consistency among the parts.
Although both PC and Nylon were white, they exhibited slight variations in color. To help the customer understand this distinction, we provided them with photographs showcasing the differences in color. These images effectively conveyed the importance of color consistency, especially for prototypes intended for high-stake presentations.
After reviewing the photographs, the customer decided to proceed with white ABS for all three parts. The choice of ABS ensured both structural integrity and consistency in color, resulting in a satisfying overall appearance for the prototype.
Case #2: Exploring Alternatives for Clear PC Milling Machine Parts
In another project, a new customer approached us with design files and a clear objective: to create a clear, polished polycarbonate prototype. The customer also mentioned a specific part that needed to be made from clear Teflon (details concealed for confidentiality reasons).
To gain a deeper understanding of the project requirements, we initiated a conversation with the customer. During our discussion, we discovered that the entire part needed to hold approximately 5 gallons of water. We also learned that the material did not necessarily have to be PC; the customer was open to cost-effective alternatives as long as the prototype fulfilled its intended functionality. Clarity was a secondary concern, as partial visibility into the part was deemed acceptable, even if achieving absolute clarity would be costly.
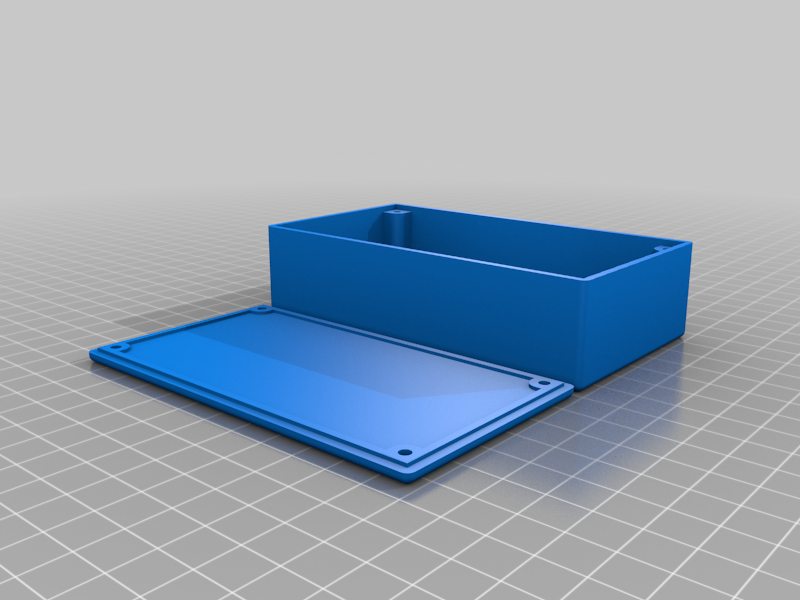
Given these requirements, we proposed 3D printing as a viable solution. 3D printing offered several advantages, including the ability to create complex shapes and a lower overall cost compared to CNC machining. In cases where a part exceeded the capabilities of milling machines, it would typically need to be divided into multiple sections, machined separately, and then bonded together. However, in this specific project, splitting the parts was not advisable due to the substantial amount of water the prototype needed to contain. The strength of the adhesive used to bond the sections could potentially be compromised under such conditions.
By utilizing 3D printing, we eliminated the need for splitting the parts, ensuring the structural integrity necessary for containing the large volume of water. However, it’s important to note that 3D printing does have its limitations. The printed parts may contain small clear bubbles, and the range of available materials is somewhat restricted. For SLA printing, the only material option is photosensitive resin, while SLS-produced parts often have rough surfaces that cannot be easily polished or painted for improved aesthetics.
To assist the customer in making an informed decision, we presented five machining proposals, each with its own advantages and limitations: CNC milling PC with vapor polish, CNC milling PC without vapor polish, 3D printing with clear polish, 3D printing without polish, and 3D printing with only one part polished. Sample photos were shared with the customer, providing a visual representation of the final appearance of each proposed option.
After careful consideration, the customer chose to proceed with 3D printing, accompanied by the clear polishing of a specific part that required optimal clarity. The resulting prototype not only fulfilled its intended functionality but also satisfied the customer’s cost-efficiency requirements. With the prototype now ready for injection molding, the project has entered its next phase.
Conclusion
The selection of suitable plastic materials may appear as a minor detail, but its impact on the success of milling machine parts cannot be underestimated. At Want.Net, we are committed to delivering optimal services to our customers, prioritizing even the smallest details. Whether it is achieving color consistency among parts or exploring alternative materials, we understand the significance of making informed decisions. By considering aesthetics, functionality, and cost-effectiveness, we ensure that our customers’ expectations are met and exceeded.
Recommended Reads:
- Role of Prototyping Companies in the CNC Prototyping Industry
- Jewelry Prototyping with CNC Machining
- How to Create a Waterproof Plastic Prototype Cases
- How to Reduce Production Costs in CNC Project Management
- How Industry 4.0 Revolutionizes CNC Machining
- 3 Essential Solutions for Manufacturing Prototyping Projects
Other Articles You Might Enjoy
- The Advantages of Using Molybdenum in CNC Machining Applications
CNC Machining Applications and the Role of Molybdenum Computer Numerical Control (CNC) machining is a revolutionary process transforming raw materials into intricate components. This cutting-edge approach automates control of machining…
- Unraveling the World of CNC Machined Plastic Parts(CNC machined plastic parts Mabel)
Modern innovations have taken traditional manufacturing methods to new heights. One such innovation that stands out is Computer Numerical Control (CNC) machining, a process used extensively in various industries from…
- CNC Machined Plastic Parts: An In-depth Overview(CNC machined plastic parts Norman)
Computer Numeric Control (CNC) machining is an advanced manufacturing process where pre-programmed software dictates the movement of factory machinery and tools. These applications can carry out complicated manufacturing tasks with…