A metal prototype serves as a physical model or sample used to verify new designs, concepts, or processes in the early stages of product development. It plays a vital role across a wide range of industries, including automotive, aerospace, medical device, electronics, and architecture.
Metal prototypes deserve recognition for their significant contribution to our society. They are the foundation upon which every product we use in our daily lives is built. The prototyping process acts as a crucial step between idea evaluation and finalization.
Understanding Metal Prototypes
A metal prototype is an object that serves as a sample or model of a new product. It allows manufacturers and designers to transform their ideas or concepts into tangible physical objects. These prototypes are essential in the product development process, facilitating testing, demonstration, and further design work.
Various methods can be employed to create metal prototypes, including 3D printing, CNC machining, casting, and sheet metal prototyping. While metal prototypes can be made from a wide range of materials, the most commonly used ones include aluminum, carbon steel, sheet metal, brass, copper, and bronze.
The Application and Function of Metal Prototypes
- Metal prototypes find applications across diverse industries, serving different purposes. In the construction industry, they are used to create models of new buildings or bridges, while the automotive field utilizes them to sample cars or trucks.
- Manufacturing processes often utilize metal prototypes to create and test new tools, fasteners, electronic devices, and household items. Liquid metal is employed to manufacture prototypes or test models, especially for tools, electronic devices, and household items.
- Prototyping enables manufacturers to test and refine new tools before commencing full-scale manufacturing and fabrication. Metal prototypes can take various forms based on the goals of the developer. Some serve as physical representations of proposed objects, while others possess full functionality, performing the same tasks or actions as the intended final product.
- Metal prototypes offer numerous advantages to manufacturers and designers. They allow for design and feature testing, enabling manufacturers to improve the product before initiating production. Additionally, metal prototypes can generate excitement among investors and potential buyers, showcasing the potential of a new product.
Why Choose Metal Prototypes?
When considering rapid prototyping, the choice between metal and plastic prototypes often arises. Metal rapid prototyping presents several competitive advantages over plastic alternatives. Let’s explore the advantages of metal prototypes:
- Excellent Strength: Metals such as stainless steel, aluminum, titanium, and magnesium alloys possess exceptional strength and durability. For parts subjected to extreme conditions or heavyweights, metal prototypes are the ideal choice. Plastic parts, in comparison, do not offer the same level of strength and durability.
- Incredible Cost-Effectiveness: While plastic may initially seem cheaper, it is more prone to wear and requires frequent replacement. Metal prototypes, on the other hand, provide superior cost-effectiveness due to their durability and extended lifespan. Metal prototypes prove to be a better long-term investment.
- Metallic Surface: If a metallic, smooth, and bright surface finish is desired, metal prototypes are the way to go. Metal prototypes can be anodized to achieve a corrosion-resistant finish, while plastic prototypes can only be painted. This makes metal prototyping unparalleled in terms of surface quality.
- Versatile Applications: The inherent properties of metal allow for more design freedom and versatility. Metal is preferable for both functional and aesthetic purposes, making it suitable for a wide range of fields. Whether in the prototype or production phase, metal offers flexibility and diverse applications.
Four Methods for Metal Prototyping
Several methods are commonly employed for metal prototyping, each with its advantages and disadvantages. Let’s explore the ins and outs of each method:
1. CNC Machining Metal Prototypes
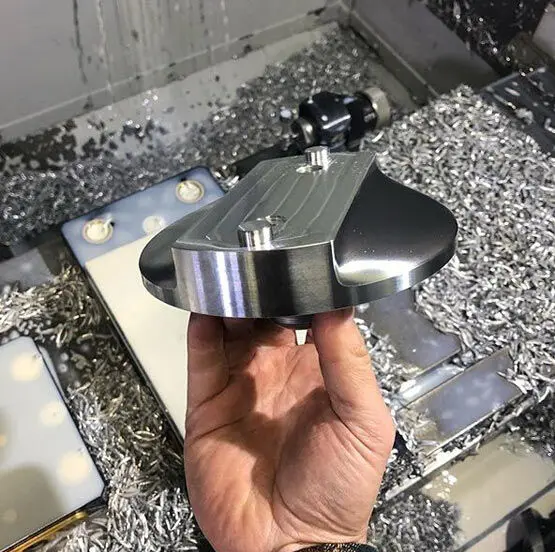
CNC machining (computer numerical control machining) is a computerized manufacturing process that utilizes pre-programmed software to control the movement of production equipment. CNC machines can work on multiple axes and are suitable for a variety of materials, including aluminum alloys, copper, steel (especially stainless steel), titanium alloys, zinc alloys, and magnesium alloys.
Key benefits of CNC machining:
- No minimum order quantity (MOQ): CNC machining eliminates the need for molds, allowing for low-volume production without MOQ requirements.
- More material options: CNC machining provides a wide range of metal blocks to choose from, with aluminum, steel, and copper being the most commonly selected materials due to their mechanical and thermal characteristics.
- High precision: CNC machining is capable of producing high-precision components, making it suitable for industries such as medical, aerospace, and robotics.
Disadvantages of CNC machining:
- Higher unit cost: Complex projects with high precision can be time-consuming and costly. When dealing with substantial quantities, CNC machining may not be cost-effective unless surface quality and precision are crucial factors.
- Material waste: CNC machining is a subtractive manufacturing method, resulting in material waste as metal blocks are cut to shape.
2. 3D Printing Metal Prototypes
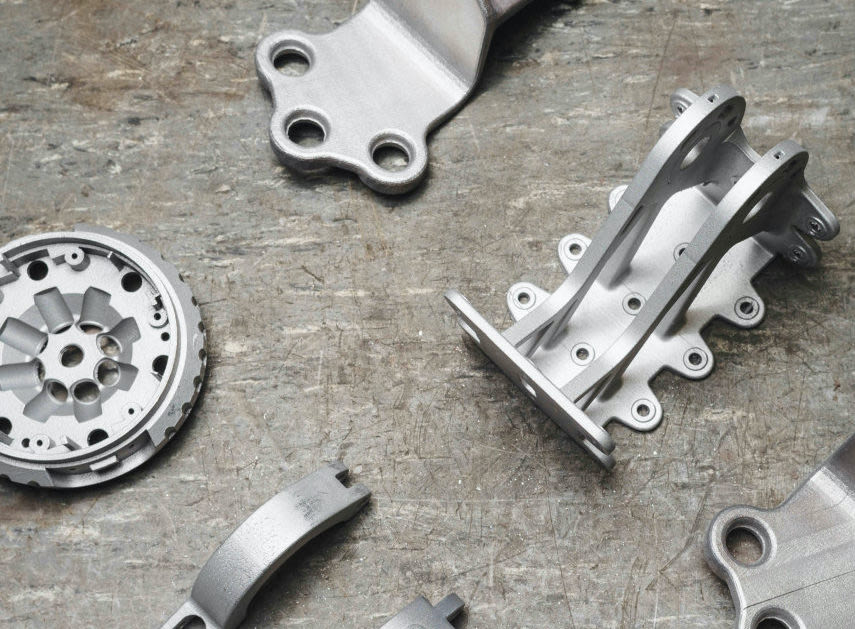
Metal 3D printing, also known as additive manufacturing, builds physical objects by printing layers of adhesive materials such as metal powder or plastic powder based on digital model files.
Key benefits of 3D printing:
- Design freedom: 3D printing allows for the creation of complex features and intricate geometries that are difficult to achieve with CNC machining. It provides designers and engineers with the freedom to prototype physical objects without design limitations.
- Quick turnaround time: 3D printing offers a rapid manufacturing process, making it suitable for projects with short production times or design iterations.
Disadvantages of 3D printing:
- Rough surface finish: 3D printed metal prototypes often exhibit a rougher surface finish compared to CNC machined parts, resulting in a coarse texture and uneven appearance.
- Low cost-effectiveness: Metal powder used in 3D printing can be expensive, making it less cost-effective compared to plastic 3D printing. This can pose challenges when profitability is a significant concern.
3. Metal Casting Prototypes
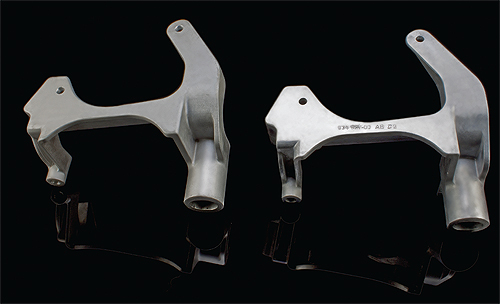
Metal casting involves the formation of rigid metal parts by pouring molten metal into a mold. Once the metal and mold cool down, the metal part is removed and ready for further processing.
Key benefits of metal casting:
- Production quality: Metal casting prototypes exhibit production-quality characteristics, making them suitable for projects where end products will be manufactured using casting. They provide a functional and solid representation of the final product, ensuring the prototype’s worth.
- Size and weight: Casting is the preferred method for creating large prototypes that cannot be produced using CNC machining or 3D printing. It offers the capability to create anything from small tabletop gadgets to large-scale structures like desalination tanks.
Disadvantages of metal casting:
- Expensive mold cost: The cost of molds used in metal casting can be high, making it less suitable for low-volume projects. Metal casting is typically more cost-effective for mass production.
- Coarse surface finish: Metal casting prototypes often exhibit a relatively rough surface finish, requiring wider tolerances. This makes them less suitable for prototypes with mating interfaces.
4. Sheet Metal Prototypes
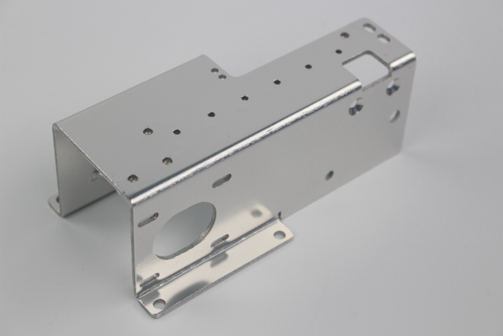
Sheet metal prototyping is a method that involves placing thin sheet metal onto a desk and using a laser cutter to perform patterning based on a program. Various forming processes like spinning, bending, punching, and welding are then employed to meet the desired geometry. Sheet metal prototypes are commonly used for enclosures, casings, and structural frames.
Key benefits of sheet metal prototypes:
- Cost-effectiveness: Sheet metal prototyping provides good-quality parts with a quick turnaround time, making it a cost-effective method for creating metal prototypes.
- Replaceability: One notable advantage of sheet metal is the ease of replacement. When several components are utilized for assembly, individual parts can be removed and replaced with new ones, resulting in cost savings, especially when making changes or adjustments.
Disadvantages of sheet metal prototypes:
- Limited design freedom: Sheet metal prototyping does not offer as much design freedom as CNC machining or 3D printing, restricting certain complex geometries.
- Wider dimensional tolerance: Sheet metal prototypes may have less tight dimensional tolerance compared to other metalworking methods, requiring considerations for wider tolerances.
In summary, the choice of metal prototyping method depends on specific requirements and considerations. For fast turnaround times and low costs, 3D printing is the best option. If high precision or complex geometries are essential, CNC machining is preferable. Metal casting and sheet metal prototyping are suitable for large or complex parts. Regardless of the chosen method, collaborating with a qualified prototype manufacturer ensures the best results.
Key Considerations for Metal Rapid Prototyping
When embarking on metal rapid prototyping, several key considerations should be taken into account:
- Material properties: It is crucial to consider the mechanical and physical properties of the chosen metal to ensure it aligns with the requirements of the prototype. This ensures the prototype functions as intended.
- Machinability: The machinability of a metal refers to its ease of being cut or shaped using machine tools. Some metals are more machinable than others, allowing for easier shaping into the desired form.
- Tooling: Producing a metal prototype requires the use of special tooling. It is important to consider the cost and availability of tooling before selecting a metal for prototyping. The availability of required tools can impact the feasibility and cost-effectiveness of the chosen method.
- Surface finish: The surface finish of metal parts is an important consideration when prototyping. Different metals exhibit varying surface finishes, which can affect both the appearance and function of the prototype. It is essential to select a metal with the desired surface finish properties.
- Cost: The cost of materials and manufacturing should be carefully considered before selecting a metal for rapid prototyping. Complex designs and subtractive manufacturing processes can increase the overall cost. Assessing cost implications ensures the feasibility of the chosen method within budgetary constraints.
- Volume and budget: The volume of mass production can be adjusted according to the available budget and the chosen method. It is essential to align the volume requirements with the budget to ensure efficient production.
In conclusion, metal prototypes are instrumental in the product development process, enabling designers and manufacturers to test their designs and make necessary improvements before moving on to production. By understanding the advantages of metal prototypes and considering the key aspects of metal rapid prototyping, manufacturers and designers can optimize their product development process. Working with a qualified prototype manufacturer, such as Want.Net, ensures expert guidance and the best possible results for your projects. Contact us today to enhance your product development journey!
Recommended Reads:
- Machining Projects: Exploring Types, Overcoming Challenges, and Getting Started
- Maximizing Manufacturing Efficiency with CNC Machining Technology
- Applying Lean Manufacturing Principles in a CNC Shop
- Choosing the Right CNC Factory for Your Porudct Prototype
- How CNC Machining Changed Sculpting
Other Articles You Might Enjoy
- Using CNC Machining to Fabricate Lightweight Metal and Remove Chrome From Metal( cnc machining services china Dana)
CNC (Computer Numerically Controlled) machining is an essential process in the manufacturing domain. With its precision, adaptability, and extensive applications, many industries rely on it for fabricating highly complex parts…
- Efficient CNC Machining of Lightweight Metal and Chrome Removal( cnc machining services china Atwood)
Computer Numerical Control (CNC) machining is a modern manufacturing process used in various industries, frequently dealing with lightweight metals or needing to remove chrome from metal surfaces. This article will…
- Material Versatility in CNC Machining: From Titanium to Thermoplastics
Introduction to CNC Machining CNC machining stands as a cornerstone in the manufacturing sector, enabling the precise creation of parts and components. This process utilizes computer numerical control (CNC) to…