In most cases, many people will directly understand CNC machining as a metal workpiece machining process. However, the fact is that CNC machining is not only widely used in metal processing but also widely used in plastics. It is one of the common processing techniques in different industries.
One of the reasons why CNC plastic machining is widely used is because of the wide variety of plastic CNC materials. Additionally, with the introduction of CNC machines, the process has become more precise, and faster and can produce parts with tight tolerances. So how much do you know about CNC plastic machining? This article will discuss the types of CNC plastic machining and some types of materials that can be applied in CNC plastic machining. Helping you turn designs into reality more accurately!
Types of CNC plastic machining
CNC plastic machining can be used in multiple industries, such as medical device manufacturing, food industry, semiconductor manufacturing, automotive and aerospace industries, etc. However, the types of CNC plastic machining required by different industries are also different. Here, we will introduce you one by one.
Plastic CNC turning
Plastic CNC turning involves fixing plastic parts on a lathe and then processing the components using rotating or turning motions. CNC turning comes in many different forms and therefore has its unique purpose and results. For example, straight and cylindrical CNC turning is suitable for maximum cutting, while tapered CNC turning can create unique conical shapes.
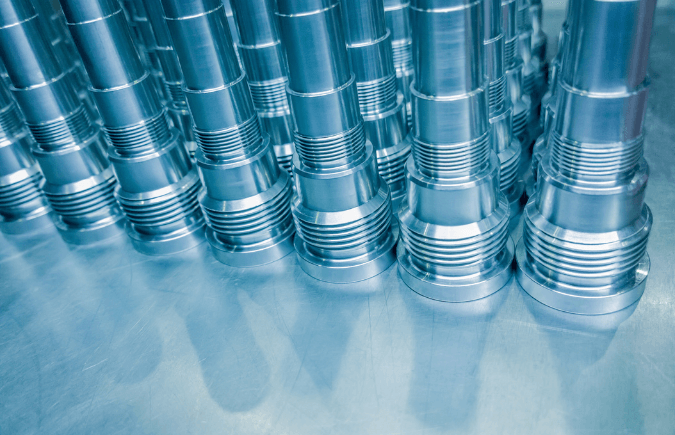
However, you can learn from the following tips when using plastic CNC turning:
- Make sure turning tools have a negative back rake to minimize friction.
- Use a large relief angle to cut the edges.
- To reduce material buildup and achieve a better finish, polish the top surface.
- Use fine C-2 grade carbide blades for better cutting of plastic components.
- If it is rough cutting, you can use a feed rate of 0.015 IPR; if it is fine cutting, you can use a feed rate of 0.005 IPR.
Plastic CNC milling
Plastic CNC milling is a computer-controlled milling process, which obtains finished parts by removing material from a solid workpiece using a cylindrical rotating tool of a milling cutter. CNC milling machines generally can be divided into two categories – 3-axis milling machines and multi-axis milling machines. 3-axis milling machines are better suited for creating simple designs, while multi-axis milling machines, including 4-axis milling machines, are better suited for manufacturing plastic parts with complex geometries. Some how-to guides are as follows:
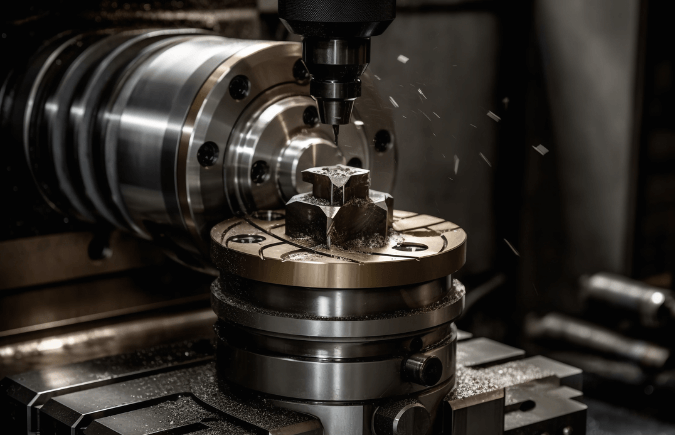
- For machining with glass or carbon fiber-reinforced thermoplastics, carbon tools are recommended.
- If higher spindle speeds are required, a clamp can be used.
- When using an end mill to create fillets or grooves, stress concentrations should be reduced.
Plastic CNC drilling
Plastic CNC drilling is a process that uses a drill bit to drill holes into plastic blocks. The hole of the required size is drilled by securing the plastic block to the machine tool and then lowering the spindle of the CNC drill onto the block. There are many drilling machines that can be used with CNC drilling machines during machining, such as vertical, benchtop, and radial CNC drilling machines.
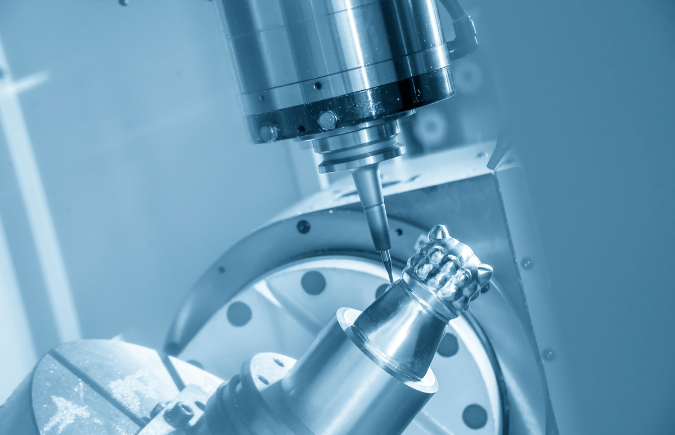
Of course, we have also compiled some CNC drilling machine usage guides for you:
- During the machining process, the CNC drill is sharp. Failure to do so will put too much stress on the part, causing tooling and performance issues.
- For most thermoplastics, a 90°-180° drill bit is recommended.
- CNC drilling generates more heat than other CNC machining processes, so reducing heat is crucial during the entire machining process.
- For safe use, it is not recommended to drill deeper than 3-4 times the diameter of the drill bit. The same is true when the drill is about to exit the material.
The types of plastic for CNC machining
There is a huge range of plastic materials to choose from when it comes to plastic CNC machining. Here we collate 11 of the most commonly used plastic materials that can be used for CNC machining.
Types | Pros | Cons | Application |
ABS | 1. Lightweight without loss of mechanical strength; 2. High machinability; Suitable low melting 3. Point and high tensile strength; 4. High durability | 1. Releases plastic fumes when heated; 2. Need proper ventilation; 3. The heat generated by CNC machine tools; 4. Can easily cause them to deform | Electrical and automotive manufacturing industries manufacture keyboard covers, electronic enclosures, automotive dashboards |
Nylon | 1. Excellent mechanical properties; 2. High tensile strength, heat resistance, and chemical resistance; 3. Lightweight polymer, cost-effective | 1. Low dimensional stability; 2. Easy to absorb moisture and sensitive to strong inorganic acids | Medical and automotive industries |
Acrylic | 1. Light, highly processable, high chemical resistance 2. Strong chemical resistance and strong UV resistance | 1. Not heat-resistant, easy to be impacted, easy to wear 2. Not resistant to chlorination/aromatic organic compounds 3. May crack under heavy load | Automobile manufacturing industry |
POM | 1. Easy processing, chemical resistance, high dimensional stability, durability | Poor acid resistance | Automotive, medical, consumer goods industries |
HDPE | 1. Highly resistant to pressure and chemicals 2. Excellent mechanical properties 3. Good durability and long service life | Poor UV resistance | Prototyping, medical device manufacturing |
LDPE | 1. Tough and flexible 2. High corrosion resistance 3. Easy to seal | 1. Tough and flexible 2. High corrosion resistance 3. Easy to seal | Custom gears, mechanical components, electrical components, and components with a polished or glossy appearance |
PTFE | 1. Resistant to chemicals and light 2. Lower coefficient of friction 3. Anti-adhesion properties | 1. Poor mechanical properties 2. There are restrictions on part thickness | Non-stick pans, washers, semiconductors, and heart patches |
PEKK | 1. Good mechanical properties and biocompatibility 2. Good environmental adaptability 3. Environmental friendly | 1. Not UV resistant, limited use 2. Expensive | Ideal for manufacturing parts that require the flexibility of plastics as well as the performance of metals |
Polycarbonate | 1. Has aesthetic value, light transmission 2. High tensile strength and durability 3. Resistant to acids, oils, and greases | 1. There is a possibility of degradation susceptible to wear and tear 2. Will turn yellow | Used in the manufacture of goggles and CD/DVD |
Polyethylene | 1. Light-weight, but good mechanical properties 2. High safety performance 3. High machinability 4. Low humidity performance, high tensile strength, and acid and alkali resistance | Easy to deform, easy to gather, easy to release smoke | Pharmaceutical, construction, chemical, food, and other industries |
PVC | 1. High corrosion resistance, good chemical resistance 2. High machinability electrical insulator 3. Tasteless, odorless and non-toxic | Poor heating stability Easy to release smoke and easy to deform | Different types can be used in a variety of different industries |
Conclusion
Now, you have learned about plastic CNC machining, all types of CNC machining processes, and the types of plastic materials that can be used. However, if you want to use the right processing methods or materials for your project, getting a reliable partner is necessary.
Here, Want.net will be your best choice. With advanced CNC machining technology and machines, and a professional manufacturing team, we can fully realize your design according to your needs. No complicated operations are required, upload your design and get a quote.
Other Articles You Might Enjoy
- Unraveling the World of CNC Machined Plastic Parts(CNC machined plastic parts Mabel)
Modern innovations have taken traditional manufacturing methods to new heights. One such innovation that stands out is Computer Numerical Control (CNC) machining, a process used extensively in various industries from…
- CNC Machined Plastic Parts: An In-depth Overview(CNC machined plastic parts Norman)
Computer Numeric Control (CNC) machining is an advanced manufacturing process where pre-programmed software dictates the movement of factory machinery and tools. These applications can carry out complicated manufacturing tasks with…
- Enhancing CNC Machining with Smart Alloys: Shape Memory Metals vs. Traditional Alloys
Introduction to CNC Machining Computer Numerical Control (CNC) machining stands as a cornerstone in modern manufacturing, enabling the precise and automated shaping of materials. This technology relies heavily on the…