Hole machining plays a crucial role in various high-tech industries, such as aerospace and automotive. While many holes may seem trivial in terms of precision and depth, modern advancements in these industries have necessitated the development of specific techniques and careful planning to meet the demands of manufacturing parts with extremely precise or deep holes, as well as holes with precise positioning. CNC services have risen to the challenge, continuously improving their machining strategies and inventing new tools to fulfill these requirements.
The Challenges of Hole Processing
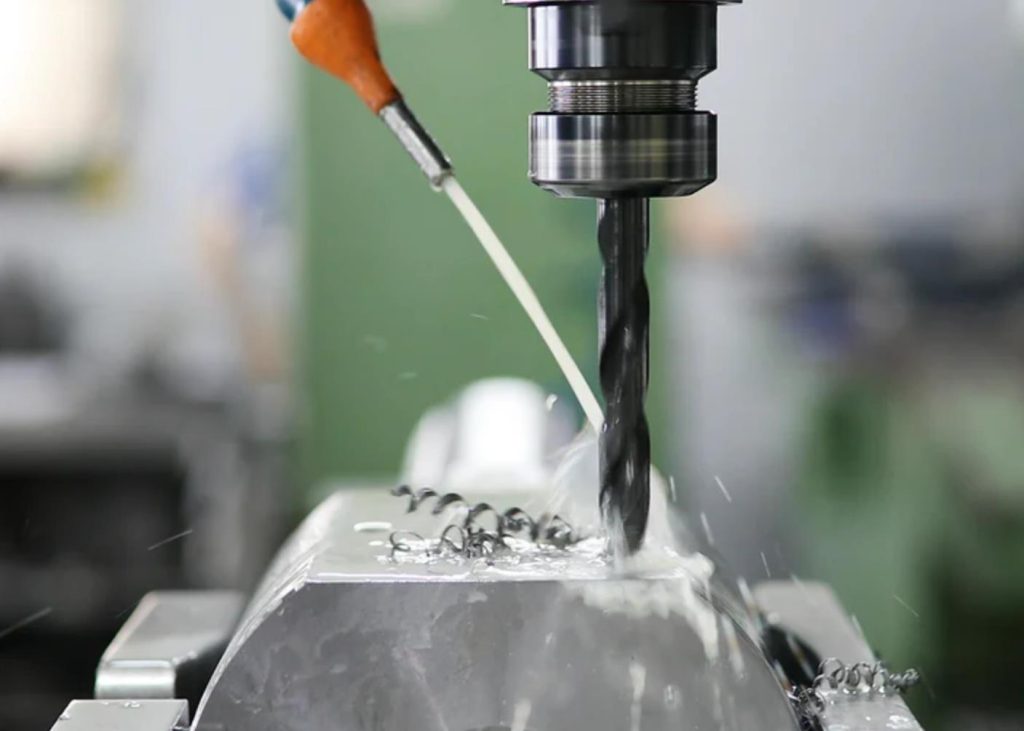
From a manufacturing perspective, hole manufacturing poses several significant challenges. One of the primary issues arises from the difficulty in effectively applying coolants into the hole. Due to the inaccessible nature of the hole, it becomes challenging to prevent the tool and the blank from overheating. Moreover, the machining process remains hidden from the machinist’s view, forcing them to rely solely on machine tool information and cut blindly. This lack of visibility makes measurements particularly difficult, especially in cases involving small-diameter holes. These are just a few examples of the obstacles encountered in hole manufacturing.
To overcome these challenges and achieve precise hole manufacturing, CNC services continuously innovate and refine their machining strategies. They develop new tools and techniques specifically tailored to meet the clients’ requirements and ensure high precision in hole production.
Conquering Deep CNC Drilling
CNC Drilling, in itself, may seem like a common and straightforward process. However, as the depth of the hole increases, maintaining its axis straight becomes increasingly difficult. This difficulty arises from the fact that longer drills possess less rigidity, and the two cutting edges cannot be made of identical lengths. Consequently, the cutting forces applied by the drill’s sides become unequal, leading to deviations from the intended straight axis and resulting in lopsided holes. Such imprecision is unacceptable when it comes to manufacturing high-precision CNC parts.
To address this challenge, the technique of gun drilling was invented. Initially used for manufacturing long stock guns, gun drilling has found applications in various other industries as manufacturing technologies advanced. The key distinction in this strategy lies in the tool employed. Unlike a simple drill, a gun drill features a single cutting edge, ensuring it stays on course throughout the drilling process. Additionally, gun drills possess larger chip removal grooves that serve as cooling channels. Coolant is pumped through these grooves at high pressure, effectively removing chips and cooling the drill more efficiently. However, it is important to note that the use of gun drills requires additional tooling and cannot be mounted on a standard CNC milling center. CNC machine shops reserve the use of gun drills for extreme cases, while employing specific strategies for drilling deep holes using conventional drills. These strategies involve segmenting the hole length into smaller depths, usually around 3-4 times the hole diameter. After each segment, the drill is ejected to allow the blank and tool to cool down, and to remove chips from the hole.
Achieving High-Precision Hole Processing
To achieve the desired level of precision in hole processing, CNC drilling typically involves the use of multiple instruments. The first tool employed is considerably smaller than the hole diameter, with subsequent tools gradually increasing in size. This approach helps reduce cutting forces and minimize axis deviation caused by the aforementioned challenges. In addition to using different-sized drills, other methods are often employed to enhance precision:
Core Drilling
Following the initial drilling, core drilling is performed. Core drills feature three cutting edges instead of one, providing increased stability during the cutting process. Although the depth of the cut is typically around 0.5 mm, core drilling excels in its ability to correct the axis, ensuring greater precision.
Reaming
When clients demand holes with tight tolerances (up to IT6) and a smooth surface finish, reaming comes into play. By using a reamer—a tool with multiple long cutting edges positioned along its sides—and employing an extremely low machining feed, highly precise holes can be achieved. For smaller holes, reaming is typically done manually.
Honing
Honing, an abrasive process, can be carried out on a CNC machine tool, although specialized honing machines tend to deliver superior results. A hone resembles a reamer, but instead of cutting blades, it features abrasive planks. The planks can be adjusted to achieve the desired hole diameter. During honing, the hone is inserted into the hole and revolves around its axis, with the planks grinding the material. Upon ejection, the revolution direction is reversed. This process results in crisscrossed microscopic grooves on the hole’s surface, significantly improving lubrication efficiency.
Strategies for Hole Threading
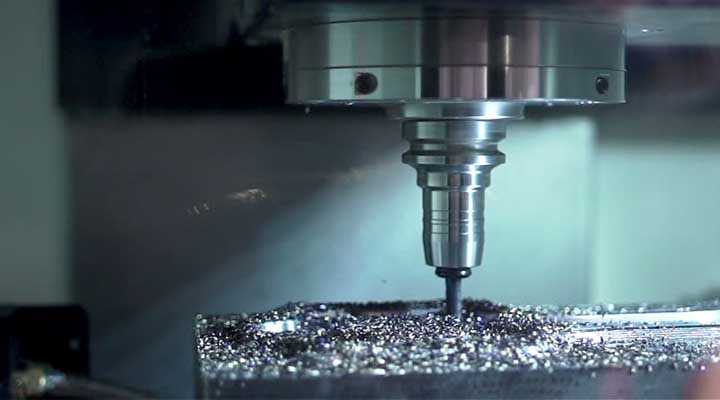
Threading holes poses a significant challenge in machining due to the complex and delicate nature of the thin surfaces involved. However, before threading can occur, it is crucial to carry out countersinking or counterboring. These processes create a conical or cylindrical groove at the entrance of the hole, facilitating the threading operation and subsequent assembly of parts. Let’s explore some threading strategies employed in CNC services:
Tap Drilling
Tap drilling involves the use of a specialized tool resembling a bolt. This tool features chip removal grooves and a long conical area at the front, gradually increasing the cut depth. During threading, including tapers, the machining feed aligns with the screw pitch. The tap drill is cautiously inserted into the hole, with each spiraling cutting edge gradually removing material to form the thread. In the case of small holes, tap drilling is performed manually, simulating the act of tightly screwing in a bolt. It is crucial to eject the tap drill with care, as improper unscrewing may lead to breakage, requiring the use of Electrical Discharge Machining to remove the broken tap.
Thread Milling
Thread milling offers improved results, as it operates at lower temperatures and allows for easier coolant application. A specialized mill, approximately 30-40% smaller than the hole diameter, moves in a spiral along the trajectory of the drill grooves while revolving around its axis for efficient cutting. The minimum hole diameter achievable depends on the minimum diameter of the mill used.
Thread Boring
Thread boring bears similarities to turning in terms of part setup and main movements. However, the tool employed is specifically designed to replicate the form of the thread groove. The tool is fed into the hole with the screw pitch, cutting the spiraling surfaces of the thread. It is important to note that while thread boring excels in processing large holes, it is not suitable for holes smaller than 20 mm.
Discover the Power of Precision CNC Machining with Want.Net
When it comes to precision machining and expertly designed part holes tailored to your project’s needs, Want.Net is your reliable partner. With cutting-edge services and a skilled team, they can help you achieve the desired results. Contact Want.Net today to explore the possibilities of precision CNC machining for your project.
Recommended Reads:
- What Is Plastic CNC Machining For Custom Parts
- The Application of Machining Parts in New Energy Vehicles
- 7 CNC Machining Advantages: Trends & Cost in 2023
- What Is Surface Finish in CNC Machining? Pros & Cons | Applications 2023
- 6 CNC Machining Design Mistakes to Avoid
Other Articles You Might Enjoy
- CNC Machining for Medical Applications: Compliance and Material Selection?
Introduction to CNC Machining in Medical Applications CNC or Computer Numerical Control machining is a manufacturing process wherein pre-programmed computer software dictates the movement of factory tools and machinery. This…
- Exploring Bead Blasting in CNC Machining(cnc machining services china Nicole)
Bead blasting is a process used extensively in the world of computer numerical control (CNC) machining. A standard part of many businesses, bead blasting enriches various products that we use…
- Precision CNC Machining of Steel: High-Volume Production
Precision CNC Machining and High-Volume Production As an integral part of modern manufacturing processes, Precision Computer Numerical Control (CNC) machining brings about unmatched accuracy and consistency in the production of…