In the manufacturing industry, there are two commonly used methods for precision part production: CNC cutting and laser cutting. Both methods offer unique advantages and play a crucial role in various industries. Understanding the significant differences between these processes is essential for selecting the most suitable option for your specific needs.
What is CNC Cutting?
CNC cutting utilizes computer numerical control (CNC) machines, such as routers and lasers, to fabricate precise parts with exact positioning and velocity. CNC routers and CNC lasers share similar features and applications, including low waste production, high capacity, and increased productivity. These machines can work with various materials like foam, wood, plastic, and acrylic to create limitless designs.
One key distinction is that laser cutting operates through heat, while CNC cutting achieves results through friction. Unlike laser cutting, which uses a laser beam, CNC routers have the advantage of cutting straight lines, curved paths, and diagonal cuts that cannot be achieved through other methods.
Another significant difference is the cost. CNC cutting is generally more cost-effective compared to CNC laser cutting. While CNC cutting can handle materials similar to CNC lasers, such as foam, wood, plastic, and acrylic, CNC lasers excel in cutting tough gemstones and metals. CNC lasers use a laser beam to achieve custom shapes and designs, making them ideal for intricate parts with high tolerance. Laser cutting is a non-contact method that performs multiple processes, and parts manufactured by CNC lasers do not require post-finishing or polishing due to the clean cut achieved through burning techniques.
CNC cutting employs specific tools for fast and efficient part production. Design customization can be achieved through software such as AutoCAD and CorelDraw. CNC cutting can handle thick materials, offers control over the depth of cut, and ensures no discoloration of the edges. It also enables the production of three-dimensional cuts and eliminates the need for additional finishing processes.
CNC Cutting Tools: Ensuring Precision and Efficiency
Cutting tools play a vital role in the CNC cutting process, as they significantly impact the quality of work and production parts. Various cutting operations can be performed using CNC cutting tools, allowing CNC laser and cutting machines to execute multiple cuts and remove excess material through shear deformation.
Effective cutting tools possess the following features:
- High Thermal Conductivity: Ensures efficient heat dissipation during the cutting process.
- High Wear Resistance: Enhances the tool’s durability and longevity.
- Stability, Hardness, and Chemical Inertness: Contributes to the tool’s stability and resistance to wear and corrosion.
- Ease of Fabrication: Enables the manufacturing of cutting tools with precision and efficiency.
Common types of CNC cutting tools include ceramics, carbon steel, cemented carbide, and high-speed steel (HSS). Coatings can be applied to these tools to enhance their functionality and lifespan. Some commonly used cutting tool coatings include diamond, titanium nitride (TiN), chromium nitride (Crn), titanium carbo-nitride (TiCN), and super-life titanium nitride (AL-Tin). Selecting the appropriate tools for your project is critical to achieve accuracy, productivity, precision, and efficient machine operation.
5 Types of Cutting in CNC Routing
CNC routing offers various cutting methods to achieve different results. Let’s explore five common types of cutting in CNC routing:
- Drilling: This type of cut is used to create precise holes of specific sizes using specialized drill bits.
- Male Cuts/Male Tool Paths: Male cuts involve cutting the outside of a piece to achieve the final dimensions of the parts. The cutter moves around the object, ensuring accurate width, height, and dimensional specifications. However, achieving sharp inside corners with a 90-degree angle can be challenging due to the use of router bits.
- Female Cuts: Female cuts differ from male cuts as they involve removing material from the workpiece. The diameter of the tool used for female cuts is slightly larger than the CNC software’s diameter for generating tool paths. Female cuts result in round cuts, similar to male cuts inside corners.
- Online Cutting/On Center Cutting: Online cutting follows simple line segments and is primarily used for shaping shapes that require additional cuts. For example, beveling with a V-bit.
- Cleanouts: Cleanouts are used to create grooves in materials for 3D routing. They do not wrap during the cutting process and are ideal for cleaning large areas. Cleanouts achieve a specific depth and are comparable to hollowing out a canoe.
What is CNC Laser Cutting?
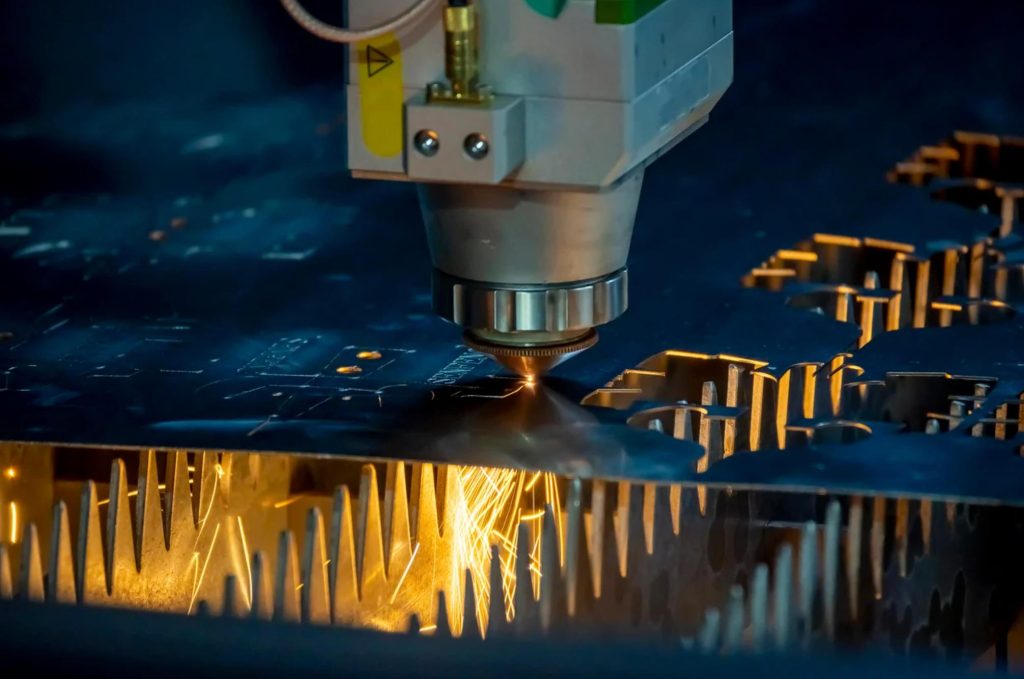
CNC laser cutting, also known as sheet metal cutting, utilizes a laser beam to vaporize, melt, and remove material from a workpiece. This process involves optics, a guidance system, and an assist gas to focus the laser beam onto the workpiece.
The main types of cutting lasers used in CNC laser cutting are hybrid laser cutting, flying optical cutting, and moving material cutting. CNC laser cutting ensures uniform cuts on complex parts and produces clean vertical lines. However, it may not be suitable for delicate parts due to its higher intensity.
Different laser types serve specific purposes:
- Nd laser: Ideal for drilling, with low-speed repetitions and high-energy impulses.
- CO₂ laser: Used for cutting, marking, drilling, and engraving applications.
- Nd-YAG lasers: Used for adjustment, engraving, and drilling, employing high-energy impulses.
CNC laser cutting is widely used in industries that require high precision, such as electronics, shipbuilding, and metallurgy. Its characteristics include high-quality cuts and speed, flexibility with minimal material deformation, and cost-effectiveness with low heat input.
Advantages and Benefits of Laser Cutting
Laser cutting offers several advantages and benefits for precision part production:
- Precision Cuts and High Accuracy: Laser cutting is renowned for its ability to achieve precise and high-quality parts. The focused beam of light enables cutting with exceptional accuracy and precision. Industries that require high tolerance, such as medical and aerospace, rely on laser cutting for their parts manufacturing. The tolerance achieved by laser cutting ranges from 0.003mm to 0.006mm.
- Low Power Consumption: Laser cutting consumes a minimal amount of energy and does not have any moving parts. Even when cutting reflective and thick materials, laser cutting maintains low power consumption. This reduces costs and positively impacts the overall manufacturing process.
- Higher Sheet Utilization with Less Waste: One of the main advantages of laser cutting is its ability to maximize the usage of sheet material. This results in a higher percentage of usable parts and components, reducing costs and accelerating production time. By minimizing the time required for shaping new sheets of material, laser cutting reduces material wastage.
- Lower Maintenance and Repair Costs: CNC laser cutting tools have fewer moving parts compared to other CNC cutting processes. As a result, they require less maintenance, reducing operational costs. Laser cutting proves cost-effective for both limited runs and large batch production due to its lack of physical cutting surfaces and the absence of tooling modifications.
Types of Laser Cutting for Sheet Metal
CNC laser cutting employs various laser types for cutting sheet metal. Let’s explore the three most common types:
- Fiber Laser: Fiber lasers are suitable for cutting a wide range of metals, including aluminum, copper, and brass. As solid-state lasers, they offer advantages such as high optical quality, temperature stability, vibration stability, high output power, and low maintenance requirements. The short wavelength of fiber lasers allows for small spot sizes, contributing to precise cutting.
- Nd: YAG Laser (Neodymium-doped yttrium aluminum garnet): Nd: YAG lasers use a crystal laser as a medium. They are a versatile choice for cutting various materials. Nd: YAG lasers excel in precision cuts and tight spots due to their high power density and capability for high dots per inch (DPI). They are also suitable for fast processing of thin materials. However, their short Rayleigh length and expensive pump diodes limit their ability to cut thick and rigid materials.
- Carbon Dioxide Laser: Carbon dioxide lasers are the most powerful laser type available. They produce a long infrared wavelength that can be absorbed by materials such as mild steel, titanium, aluminum, and stainless steel. Carbon dioxide lasers offer fast processing times and the ability to cut a wide range of materials. However, they have a larger focal spot and lower power density compared to other laser types, making them less effective for cutting infrared-reflecting materials.
Differences Between CNC Cutting and Laser Cutting
When choosing between CNC cutting and laser cutting, it’s essential to consider the following differences:
- High Precision and Cuts: Laser cutting offers unparalleled precision and the ability to achieve precise corners and curves. With a radius as small as 0.1mm (0.004 inches), laser cutting enables exact designing and reduces material waste and overall manufacturing costs. On the other hand, CNC milling typically cuts down to 2mm (0.08mm), limiting its precision compared to laser cutting.
- High Speed: CNC laser cutting provides double the speed compared to CNC milling. It can cut materials in a single pass and easily fabricate thick parts. CNC laser cutting eliminates the need for a workpiece and physical force, resulting in reliable and precise parts. It allows for the creation of a final product without clamping or post-processing procedures, significantly reducing project cost and time.
- Low Processing Cost: CNC lasers require no clamping or post-processing steps in the parts manufacturing process. This decreases the overall project cost. CNC laser cutting can achieve a finished product without the need for extensive processing and cutting around the product, which is difficult with CNC milling. CNC milling requires clamping and post-processing for the production of final parts.
- Minimal Post-Processing Requirements: Laser cutting eliminates several additional steps required in CNC cutting or milling methods. The laser can create a finished product without flame polishing, vacuum preparation, or material fixing steps. This reduces labor costs and increases the profit margin in parts manufacturing.
- Applications and Uses: Laser cutting has revolutionized industries such as shipbuilding, where precision and speed are essential for transfer accuracy and hull segmentation. Laser cutting offers advantages such as small thermal deformation, high cutting accuracy, reduced assembly cycles, decreased labor costs and workload, smooth surface finishes without dross, and the ability to handle small holes, circles, and curved surfaces. CO₂ laser cutting technology is commonly used in shipbuilding, steel metal, automotive, and other industries.
In contrast, CNC cutting excels in cutting larger parts and utilizes a rotary cutter to remove material from solid pieces of wood. CNC cutting offers advantages such as no discoloration of edges, great control over the depth of cut, and the ability to create three-dimensional objects or cuts. Additionally, CNC cutting is suitable for cutting thicker parts compared to CNC lasers.
CNC cutting systems find extensive applications, including the production of complex 3D parts, pipes, high-pressure container caps, and various profile shapes (e.g., V, Y, and K cross-sections). CNC cutting enables the machining of intricate parts.
How to Choose Between CNC Cutting and Laser Cutting
Based on the information provided, you can consider which CNC cutting or laser cutting method is the most optimal solution for your projects. It is crucial to ensure that the specific machines, laser cutting capabilities, and cutting applications align with your requirements.
When it comes to CNC machining, you can trust Want.Net to provide the expertise and experience needed to make the right choice for your projects. Our team is dedicated to delivering top-notch CNC machining services tailored to your specific requirements. Whether you need precision CNC cutting or laser cutting, we have the knowledge and technology to meet your needs. Visit our website or contact us today to learn more about how Want.Net can help bring your ideas to life with our exceptional CNC machining services.
Recommended Reads:
- How Industry 4.0 Revolutionizes CNC Machining
- 3 Essential Solutions for Manufacturing Prototyping Projects
- What is Diamond Machining
- Why Custom Prototypes Are Shaping the Future of Manufacturing
- Precision Rotor Blade Prototypes through 5-Axis Machining
Other Articles You Might Enjoy
- Beyond Cutting: Exploring the Multifaceted CNC Machining Process
1. Introduction: Unveiling the Layers of CNC Machining In this introductory section, we peel back the layers of the CNC machining process, going beyond the traditional understanding of cutting. It…
- Comparing Machinability of Various Tool Steels: What's the Best Choice?
Understanding Tool Steels and their Machinability Tool steels are referred to as an extensive variety of carbon and alloy steels known for their distinctive hardness, abrasion resistance, and ability to…
- From Vision to Reality: CNC Machining for Custom Furniture Design
Introduction to CNC Machining in Custom Furniture Design The advent of computer numerical control (CNC) machining has revolutionized the field of custom furniture design, allowing precise and intricate patterns to…