CNC Drilling Services
- Free Quote and DfM
- Fast Lead Time
- Pay After Delivery
Home » CNC Machining » CNC Drilling
High-Quality CNC Drilling Services for Precision Parts
We take pride in providing the best CNC drilling services for the fabrication of parts of any complexity, whether in small or large series. With our state-of-the-art equipment and expertise, we ensure exceptional results for all your drilling needs.
At Want.Net, we utilize a range of advanced CNC drilling machines, including upright, bench, and radial models. This diverse selection enables us to drill holes of simple and complex patterns, with diameters reaching up to 7 cm. Whether you require precision drilling in metals and alloys such as aluminium, steel, copper, or various polymers, our services cover a wide range of materials.
We maintain strict control over the entire drilling process, ensuring that our exacting quality standards are met every time. Our integration of advanced CNC drilling equipment with our machining centers allows us to execute precise and efficient drilling operations for your parts.
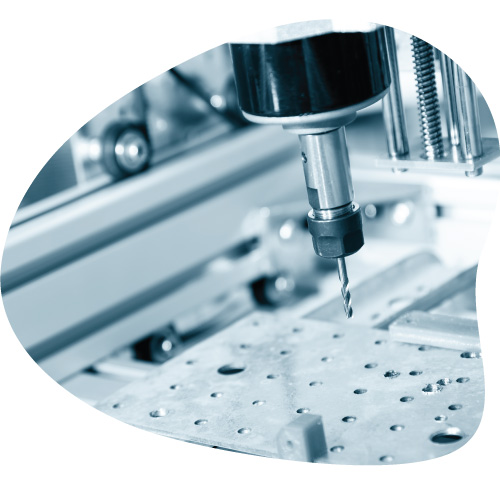

Equipment and Technical Strength
Our CNC Drilling Service is powered by multiple advanced drilling and tapping centers, including FANUC α-T14iF and Brother S500X1 machines. With spindle speeds up to 10,000 rpm and tool magazines of over 20 slots, these units allow rapid tool changes while maintaining stable productivity.
By employing automated chip-removal systems and real-time monitoring software, our CNC Drilling Service ensures ideal tool temperatures and reduced wear, maximizing operational uptime.
The production lines use a PLC-based control system to finely adjust spindle speeds and feed rates. Coupled with high-speed, high-precision servo motors, CNC Drilling Service consistently achieves precise results across various materials and hole sizes.
For deep or blind holes, we utilize specialized long drills and internal coolant systems to ensure our CNC Drilling Service maintains both high quality and efficiency, even with high aspect ratios.
Additionally, tool presetting and on-machine probing optimize tool paths, enabling faster setups and line changes in our CNC Drilling Service while reducing manual intervention.
Drilling Precision and Hole Surface Quality
Within our CNC Drilling Service workflows, we achieve hole diameter tolerances of ±0.01 mm and maintain excellent positioning and concentricity, suitable for precision fits on critical components.
By carefully selecting tool geometry, feed rates, and cooling strategies, our CNC Drilling Service delivers hole surface roughness down to Ra1.6 or better across multiple materials, minimizing burrs and chip buildup.
To guarantee consistent surface quality, CNC Drilling Service operates in a temperature- and humidity-controlled environment, supported by dedicated dust extraction and cooling setups to remove swarf effectively.
We use in-process measurement techniques to track hole depth and diameter in real time, enabling immediate correction if deviations arise. This proactive approach ensures stable CNC Drilling Service quality.
Regular fixture and gauge calibrations eliminate potential cumulative errors in CNC Drilling Service, safeguarding the accuracy of every drilling operation.
Whether working with metals or plastics, our compound tooling and adaptive feed strategies enable the CNC Drilling Service to achieve top-notch hole integrity, ensuring reliable product performance in assembly and end-use scenarios.
Below is a sample table that outlines the core performance data for our CNC Drilling Service. The table includes key parameters from our actual production experience and machine specifications, providing potential clients with an insight into our robust capabilities. Please note that while material properties and specific process requirements may introduce slight variations, the data below reliably reflects our strong performance in CNC Drilling Service.
Machine Model | Drill Hole Diameter Range (mm) | Maximum Drilling Depth (mm) | Hole Position Accuracy (mm) | Surface Roughness (Ra, μm) | Additional Information |
FANUC α-T14iF | 1.0 – 20.0 | ≤50 | ±0.01 | 0.8 – 1.6 | High-speed spindle up to 10,000 rpm; ideal for high-precision small-diameter holes in aluminum alloys, stainless steel, and carbon steel. |
Brother S500X1 | 0.8 – 22.0 | ≤60 | ±0.012 | 1.0 – 1.6 | Features a 21-tool magazine for rapid tool changes; well-suited for multi-process drilling and tapping applications in small-hole and composite drilling scenarios. |
TBT Gun Drilling T19 | 2.0 – 25.0 | ≤300 | ±0.02 | 0.4 – 1.6 | Specially designed for deep-hole processing with internal coolant and chip removal; used for titanium and steel deep-hole applications such as aerospace parts. |
Brother TC-S2D (Multi-Spindle) | 1.5 – 18.0 | ≤45 | ±0.015 | 0.8 – 1.6 | Multi-spindle synchronized drilling that significantly boosts productivity; commonly used in electronics and telecommunications for heat dissipation arrays. |
Multi-Material and Diverse Part Capabilities
Our CNC Drilling Service accommodates a wide range of materials, including aluminum alloys (6061, 7075), stainless steel, carbon steel, brass, copper alloys, titanium, and engineering plastics. We tailor tool selection and cutting parameters to each material’s hardness and toughness.
For high-hardness materials like Inconel or titanium alloys, we adopt coated cutting tools and high-pressure coolant systems, allowing the CNC Drilling Service to sustain efficient chip evacuation and tool life in demanding conditions.
Thin-walled, irregularly shaped, or large-format plates benefit from specialized fixturing or vacuum clamping to enhance rigidity and minimize deformation during CNC Drilling Service.
Extended-length or deep-hole requirements are addressed via internal coolant drills and segmented chip removal protocols, ensuring the CNC Drilling Service delivers accurate tolerances and optimal surface finishes.
Multiple processes, including combined drilling and milling or tapping, can be performed on the same CNC Drilling Service setup, reducing part transfers between different machines.
Backed by extensive experience in material behavior and versatile fixturing approaches, our CNC Drilling Service covers everything from rapid prototyping and small-batch runs to large-scale mass production for various industries.
Quality Management and Certifications
To guarantee reliable outcomes in our CNC Drilling Service, we fully adhere to the ISO 9001 quality management system, recording and tracking every step from incoming materials to final inspections.
Statistical Process Control (SPC) is utilized throughout our CNC Drilling Service, continuously monitoring key hole diameters and distances so we can promptly adjust cutting parameters if deviations occur.
We invest in core inspection equipment—coordinate measuring machines, optical projectors, and roughness testers—to thoroughly verify every hole feature in our CNC Drilling Service.
Regular quality trainings ensure that operators and engineers alike maintain keen awareness of the crucial factors influencing CNC Drilling Service, strengthening overall execution and consistency.
Through ongoing PDCA cycles and continuous enhancement, we steadily reduce scrap rates within CNC Drilling Service operations and improve product uniformity, ultimately delivering dependable drilling solutions for our clients.
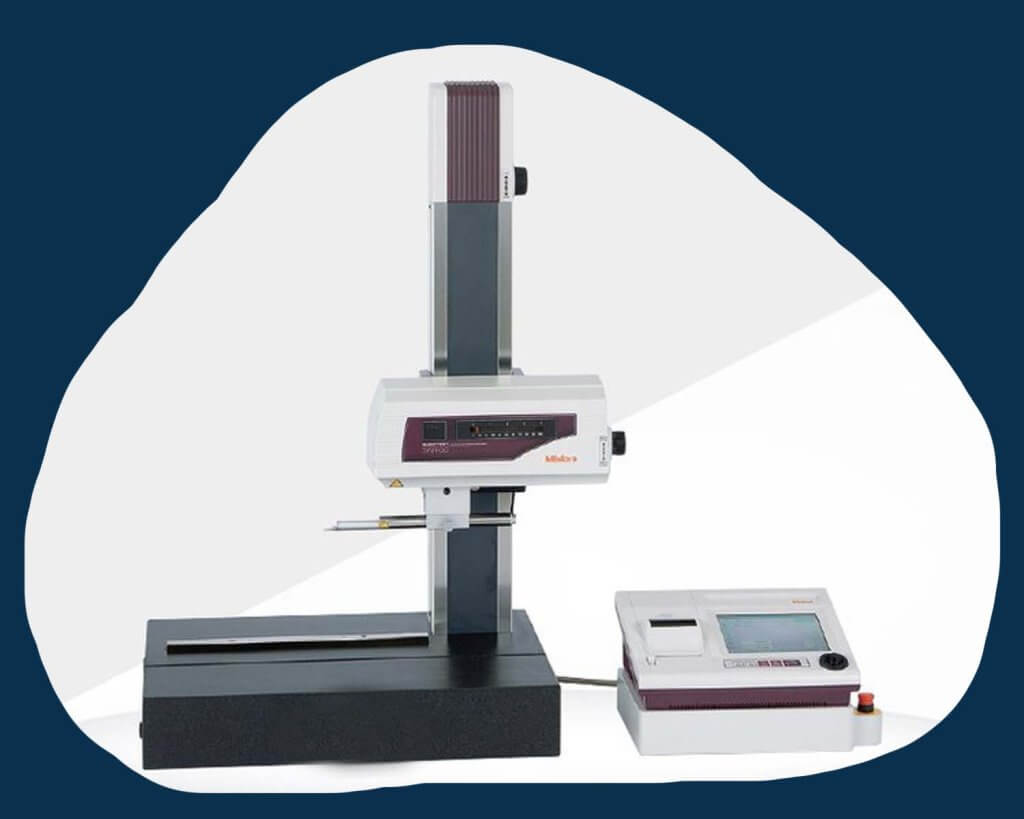
Efficiency and Delivery Speed
We implement high-speed spindles and multi-spindle configurations in our CNC Drilling Service, such as Brother TC-S2D models, allowing multiple holes to be processed simultaneously and drastically cutting production time per piece.
Supported by an advanced production management system, we swiftly schedule CNC Drilling Service tasks once orders are placed, leveraging automated loading and tool presetting to minimize downtime.
Larger-scale orders benefit from parallel machining and staggered production shifts, maximizing facility usage and ensuring that our CNC Drilling Service delivers substantial quantities promptly without compromising quality.
We provide end-to-end logistics coordination, shipping finished workpieces directly from our CNC Drilling Service lines to the customer’s location, cutting out intermediate handling.
Emphasizing lean manufacturing principles and continuous improvement, our CNC Drilling Service maintains high quality while reducing lead times and labor inputs, helping customers gain faster market entry.
Engineering and Service Team
Our seasoned engineering team has extensive hands-on and R&D expertise in CNC Drilling Service, offering end-to-end support from tool selection and drilling path design to fixture development.
Upon receiving a project, engineers assess feasibility based on drawings and requirements, using CAM software to simulate CNC Drilling Service processes and identify potential risks or areas for improvement.
Close collaboration with our customers is a hallmark of our CNC Drilling Service approach—any questions regarding material properties, hole tolerances, or structural design can be swiftly addressed by our drilling experts.
For highly specialized or challenging hole-processing tasks, we form dedicated teams that collaborate with tool suppliers and customize coolant strategies, ensuring the CNC Drilling Service meets unique project demands.
We also assist with post-processing steps, such as surface treatment, tapping, or assembly tests, minimizing the need for multiple external vendors.
Regular in-house workshops and knowledge-sharing sessions keep our CNC Drilling Service team updated on the latest techniques and equipment, enabling them to deliver pioneering drilling solutions across numerous industries.
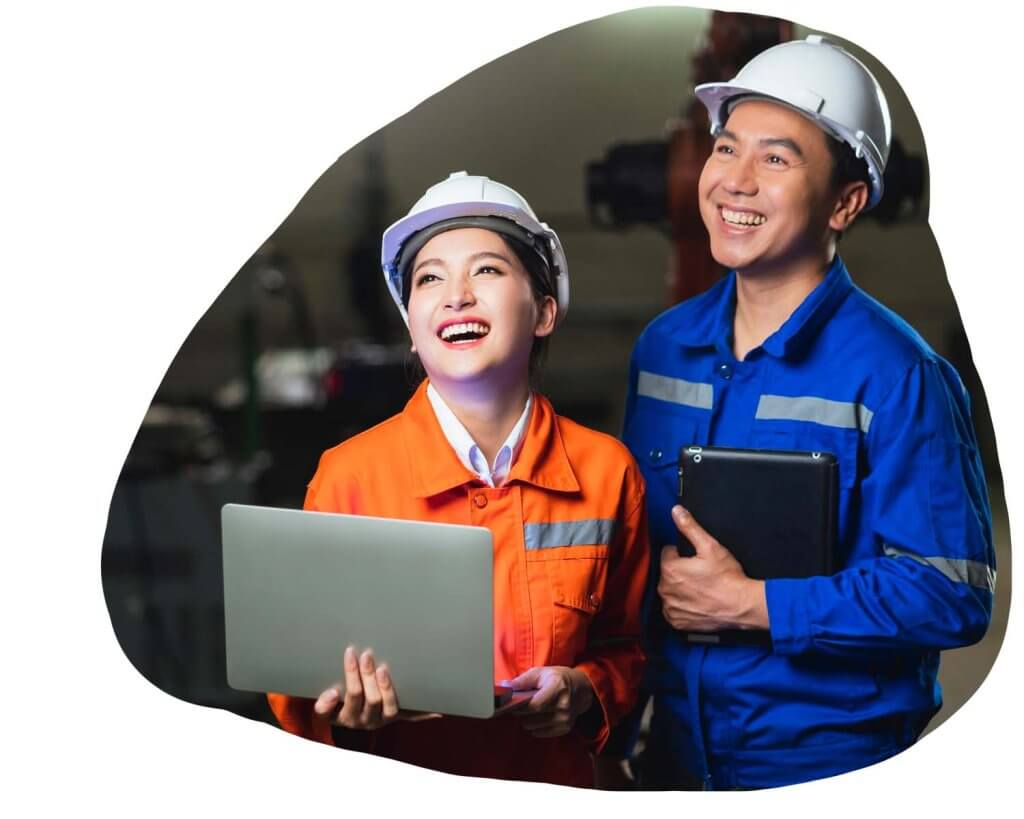
Typical Cases and Application Fields
Our CNC Drilling Service is widely employed in the automotive sector, producing critical parts like engine cylinder heads and crankshaft holes. We excel at high-strength materials and deep-hole demands.
In aerospace, we have supported a key supplier by drilling deep holes in titanium components, utilizing internal coolant drills and high-pressure chip removal. Our CNC Drilling Service achieved stable precision even with challenging length-to-diameter ratios.
For electronics and telecommunications, common applications include heat dissipation arrays and connector panels, which our CNC Drilling Service completes with speed and smooth bore finishes, ensuring efficient assembly and reliable through-holes.
Medical device manufacturing demands extreme cleanliness and precision; by combining CNC Drilling Service with in-process measurement, we ensure minimal positional deviation and reduce scrap rates.
Large-scale machinery and heavy equipment also benefit from our CNC Drilling Service—board-like and structural components can be processed in parallel to significantly shorten production time.
Through collaborations with leading companies across multiple industries, we continually refine our expertise, bolstering our CNC Drilling Service offerings to deliver dependable, high-throughput drilling solutions.
Why Choose Our CNC Drilling Service
Choose Want.Net for top-quality CNC drilling services. With our expertise, cutting-edge equipment, and commitment to excellence, we guarantee exceptional results for all your drilling needs.
What is CNC Drilling and How does it Works?
CNC drilling is a precise cutting process that involves the movement of the cutter while keeping the workpiece stationary. By aligning the cutter’s center with the hole’s center and inducing rotation, CNC drilling machines create round holes, commonly used for machine screws and bolts. This versatile technique is primarily performed on CNC milling machines and lathes, providing efficient and accurate results.
The CNC drilling service caters to a wide range of materials, including metals, hard plastics, wood, and other rigid substances. This makes it a suitable choice for various industries and applications, from automotive and aerospace to electronics and construction.
Different types of drilling machines are available for CNC operations, including upright, bench, and radial drill presses. Each type offers unique advantages, allowing operators to select the most suitable machine for their specific requirements.
The CNC drilling process follows a systematic approach to ensure precision and consistency:
The operator begins by uploading the CAD or CAM file. This digital representation serves as the blueprint for the drilling operation.
The operator selects the appropriate drill bit and secures the designated material firmly on the machine’s table or work surface. This ensures stability during the drilling process.
Through the control panel or interface, the operator initiates the drilling operation. The CNC machine’s software interprets the instructions from the uploaded file and executes the drilling program accordingly.
The spindle, equipped with the selected drill bit, begins its descent. As it penetrates the material, it precisely creates holes of the required sizes and diameters, following the programmed specifications.
CNC drilling combines the accuracy of computer-controlled automation with the reliability of drilling machinery, delivering consistent results with minimal errors. This efficient process streamlines production and saves time, making it an ideal choice for projects that demand precision and high-volume drilling.
When you choose CNC drilling, you can expect precise hole drilling, increased productivity, and enhanced repeatability. Trust this advanced technique to achieve your drilling needs with superior quality and efficiency.
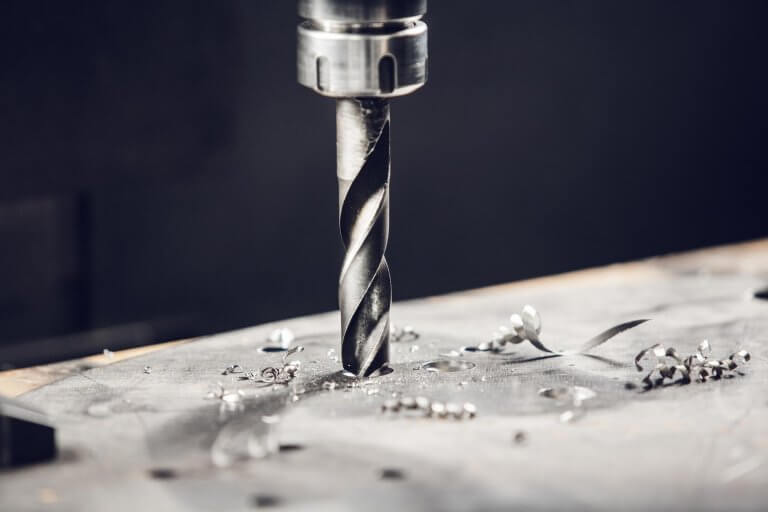
What is CNC Drilling: Types, Process & Key Techniques?
What is CNC Drilling Technology? CNC (Computer Numerical Control) drilling is a precise and automated manufacturing process used to create holes in various materials with
Get a Quick Quote Now
You’re 1-step away from our incredible quote of CNC turning service.
- All uploads are secure and confidential