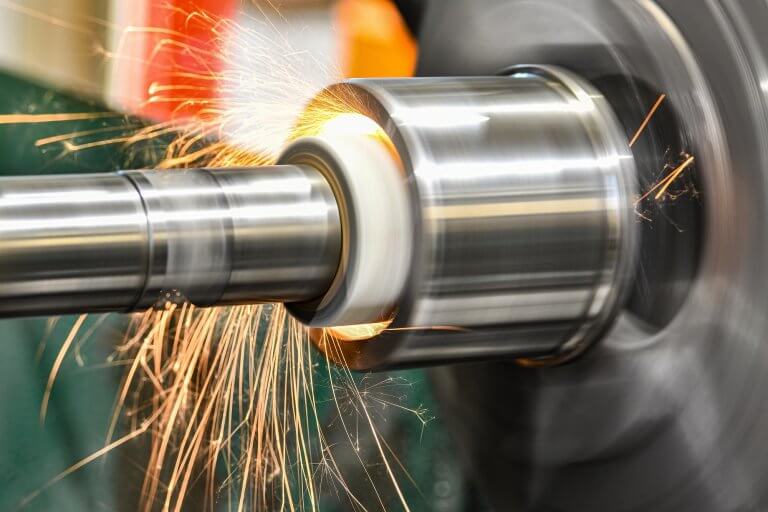
What is Grinding: Definition, Methods & Applications?
The Concept and History of Grinding Technology Introduction Grinding is one of the most critical processes in modern manufacturing, especially for achieving high levels of
With our online custom machining service, you can order custom parts or prototypes with just a few clicks. Grinding: As an essential machining technique for parts, we offer powerful CNC Grinding machine and excellent engineers to provide you with reliable and advanced technical support! All products are ISO 9001:2015, ISO 13485, and AS9100D certified or registered under ITAR.
Home » CNC Machining » CNC Grinding
With our own factory and our robust CNC grining manufacturer networks, we provide high precision grining service for our global clients at the most competitive price possible. Our precision CNC lathes provide low-cost parts for simple and complex cylindrical geometries. We also use Live tooling to create precise, complex geometries for features like axial and radial holes, grooves, slots, and flats. Full automation of these versatile machines allows us to produce hundreds of similar dimensions easier, faster, and cost-effectively.
Item | Indicator Range | Remarks |
Dimensional Tolerance | ±0.001 mm ~ ±0.003 mm | Depends on material and geometry; highly stable for batch operations |
Cylindricity | ≤0.002 mm | Standard accuracy for external and internal cylindrical grinding |
Roundness | ≤0.0015 mm | Achieved via air-bearing spindles and dressing techniques; ideal for demanding parts |
Surface Roughness | Ra 0.2 ~ 0.4 µm | High-quality grinding wheels with automatic dressing can reach Ra 0.1 µm (fine grinding) |
Max Grinding Diameter | Ø 200 mm | Larger diameters may be assessed based on specific equipment configurations |
Max Grinding Length | 400 mm | Suitable for external, internal, and end-face composite grinding |
Hardness Range | HRC 20 ~ HRC 65 | Covers common hardened steels and carbides, ensuring stable grindability |
Yield Rate | ≥98.5% | Inline inspection and auto-compensation enable high stability in continuous production |
Lead Time | 3 ~ 10 days (standard batch) | Expedited processing available depending on complexity; trial runs as fast as 48 hours |
Measurement | Zeiss CMM, MarSurf roughness testers, etc. | Real-time data monitoring with regular calibration of measurement devices |
This data table illustrate the key precision and performance indicators our CNC Grinding Service can reliably achieve in actual production. These figures are based on measurements conducted using our frequently utilized high-end grinding machines (e.g., Studer, Okuma) in combination with high-precision measuring equipment (e.g., Zeiss CMM, MarSurf roughness testers). All data reflects feasible levels under batch production conditions and common materials (alloy steel, stainless steel, cemented carbide, etc.), providing trustworthy references.
1.Primary Machines and Models:
Our CNC Grinding Service features multiple high-end grinding machines from top international brands, such as the Swiss-made Studer S31 and the Japanese OKUMA GA-26T, specialized in both external and internal cylindrical grinding. Equipped with state-of-the-art control systems, these machines consistently achieve sub-micron feed accuracy.
2.High-Efficiency Automation:
To boost efficiency even further, our CNC Grinding Service incorporates automated loading robots and in-line measurement systems, ensuring consistent results in mass production runs. Real-time sensor monitoring allows us to detect any anomalies early, reducing correction and changeover times.
3.Versatile Attachments:
Beyond standard grinding capabilities, our CNC Grinding Service provides an array of wheels and dressers, enabling angled grinding, multi-step operations, and intricate contouring. These versatile attachments broaden our application range to accommodate various customer requirements.
4.Environment Control:
For ultra-precise grinding, room temperature and humidity are crucial. Our CNC Grinding Service workshop is equipped with constant-temperature, humidity-controlled systems that minimize thermal expansion and maintain stable production conditions.
5.Data-Driven Management:
All machinery and process data are managed under our MES system, recording wheel wear, machine load, and vibration in real time. Advanced analytics help us schedule preventive maintenance, allowing our CNC Grinding Service to operate at peak efficiency and quality over the long term.
1.Technical Lead:
Our CNC Grinding Service is led by an engineer with over 20 years of grinding experience in aerospace and precision mold industries. His depth of knowledge in handling challenging materials and complex geometries ensures that we can tackle sophisticated grinding tasks.
2.Cross-Functional Expertise:
Beyond conventional mechanical engineers, our team also includes materials scientists and automation specialists. By working closely, they support each CNC Grinding Service project from material selection through automated integration, offering full-spectrum assistance.
3.Continuous Training:
To stay on the cutting edge, we host regular in-house training and participate in external courses, learning about the latest international grinding innovations. This ensures our CNC Grinding Service engineers remain current with industry best practices.
4.Quality Focus:
Before machining any part, all team members verify drawings and process requirements. During the CNC Grinding Service, they strictly follow inspection protocols to meet or exceed customer standards in every dimension.
5.Efficient Communication:
We encourage direct interaction between our engineers and clients to promptly address any challenges. Through timely communication, our CNC Grinding Service rapidly resolves process bottlenecks, minimizing lead times while maintaining top-notch quality.
1.Initial Assessment:
When receiving customer drawings and requirements, our engineers perform a thorough feasibility study and material analysis to develop the appropriate grinding strategy for our CNC Grinding Service. This phase also covers fixture design and preliminary process planning.
2.Simulation and Trial Runs:
Before full-scale production, we simulate tool paths and potential interferences in CAM software. If needed, a small batch trial grind is conducted to confirm whether our CNC Grinding Service can deliver the required accuracy and surface finish.
3.In-Process Monitoring:
During grinding, we employ inline measuring devices that gauge workpiece dimensions in real time, allowing our CNC Grinding Service to make minor parameter adjustments instantly. If deviations occur, the system triggers an alert or automatically corrects, maintaining part consistency.
4.Intermediate Inspection:
To minimize defects, the CNC Grinding Service performs interim checks at critical production stages using high-precision devices such as CMMs and profilometers. This ensures each process step adheres to the tolerance range specified by the customer.
5.Final Touches:
After grinding, parts may need deburring, cleaning, or anti-rust treatments. We follow the client’s specifications or relevant industry standards for post-processing. A final dimensional check is then carried out, ensuring a flawless delivery.
1.Comprehensive Inspection Facilities:
Our CNC Grinding Service workshop houses advanced measurement tools, including coordinate measuring machines (CMMs), contour gauges, and roughness testers. For instance, a German-made Zeiss CMM achieves up to 0.5μm precision.
2.Quality Management System:
We implement ISO 9001 standards throughout every stage—from drawing reviews and sample approval to final shipment. Each CNC Grinding Service order is assigned an individual quality tracking record for easy reference.
3.Data Monitoring and Statistical Analysis:
Through our MES platform, we track critical data points like wheel wear, spindle load, and temperature patterns in real time. If our CNC Grinding Service detects unexpected variances, we immediately analyze root causes to implement corrective measures.
4.Continuous Improvement Cycle:
Regular quality review meetings address client feedback and internal metrics. Engineers propose and test improvements, following a PDCA cycle. Over time, this systematic approach steadily enhances both our CNC Grinding Service processes and final product quality.
5.Stringent Outbound Inspection:
Once machining is complete, every part must pass either a full dimensional check or sampling test before packing. For projects with extremely tight tolerances or surface finish demands, our CNC Grinding Service can provide third-party inspection reports for additional assurance.
1.Optimized Scheduling:
Our CNC Grinding Service applies an intelligent scheduling system that ranks orders by urgency, complexity, and equipment availability, significantly reducing idle time and boosting overall productivity.
2.Rapid Response:
For urgent orders or prototypes, we launch a priority workflow, allocating essential resources and engineers. This enables our CNC Grinding Service to complete critical projects in the shortest time possible and helps clients stay ahead in a competitive market.
3.Parallel Processing:
To further shorten lead times, we utilize multiple grinding machines working concurrently. Large batches or multi-step components can go through rough grinding, semi-finishing, and finishing operations simultaneously, drastically improving turnaround times.
4.Efficient Logistics:
Our dedication to rapid service extends beyond machining. We manage packaging, dispatch, and shipping methods with strict timelines. Working with multiple logistics partners, we offer various delivery options to ensure on-time arrivals.
5.Order Tracking System:
Customers can monitor their CNC Grinding Service progress online through a dedicated portal. Each process stage updates automatically once finished, allowing clients to plan subsequent assembly steps or additional downstream operations without delay..
Advanced grining capabilities are one of the key technologies that make customers choose us for custom part machining.Choose us for your CNC grining needs and get a quick and accurate CNC grining quote for your grining parts online.
The Concept and History of Grinding Technology Introduction Grinding is one of the most critical processes in modern manufacturing, especially for achieving high levels of
You’re 1-step away from our incredible quote of CNC grining service.
You’re one step from the factory-direct price of part manufacturing services.