5 Axis CNC Machining Service
Our 5-axis CNC machining service, designed to provide excellent custom machining solutions, combines cutting-edge technology with skilled craftsmanship to deliver precise and complex parts for a wide range of industries. All products are certified by ISO 9001:2015, ISO 13485 and AS9100D, or registered in ITAR.
- Free Quote and DfM
- Fast Lead Time
- Pay After Delivery
Home » CNC Machining » 5 Axis Machining
Precision and Complexity Custom Parts Manufacturing
With 5-axis machining technique, we can achieve complex geometries, intricate contours, and tight tolerances with fewer setups. This reduces production time, minimizes errors, and enhances overall productivity, resulting in cost-effective solutions without compromising quality. Our skilled technicians work closely with you to understand your specific requirements, providing customized solutions that perfectly match your project’s needs.
With our 5-axis CNC machining service, you can expect superior surface finishes, precise hole drilling, intricate detailing, and exceptional dimensional accuracy. We have a comprehensive range of materials available, including metals, plastics, composites, and more, allowing us to cater to diverse applications and industries.
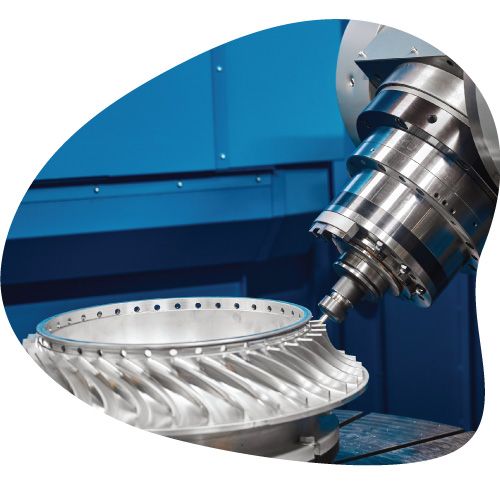
Why Choose Our 5 Axis CNC Machining Service
When you choose our 5-axis CNC machining service, you benefit from our commitment to quality, attention to detail, and efficient turnaround times. We pride ourselves on delivering exceptional craftsmanship, ensuring that every part meets the highest standards of accuracy and functionality.
What is 5 Axis Machining?
5-axis CNC machining revolutionizes the manufacturing process by introducing two additional axes of movement to the cutting tool, enabling unparalleled precision and complexity. While traditional 3-axis machines move the spindle along the X, Y, and Z axes, 5-axis machines offer even greater flexibility and freedom.
In a 3-axis CNC machine, the spindle can move up and down, side to side, and back and forth. However, with a 5-axis machine, the possibilities expand further. There are two main methods employed: either the table can tilt and rotate on two different axes, or the spindle itself can swivel on two axes. Both approaches allow the cutting tool to approach the workpiece from a significantly greater number of angles, opening up a world of design possibilities.
The ability to maneuver the cutting tool from various angles offers several advantages. First and foremost, it enables the creation of highly complex shapes that would be challenging or even impossible to produce with traditional machining methods. Intricate contours, curved surfaces, undercuts, and complex geometries can now be achieved with exceptional precision.
Furthermore, the incorporation of additional axes reduces the need for manual repositioning of the workpiece. Unlike 3-axis machines where the part often needs to be turned over to access different areas, 5-axis machines can reach those areas without manual intervention. This significantly minimizes the number of setups required, leading to increased efficiency, faster production times, and reduced chances of errors.
The speed and accuracy of 5-axis machining make it an ideal choice for industries requiring intricate and high-quality components. From aerospace and automotive to medical and electronics, the advantages of 5-axis machining are evident. It empowers manufacturers to push the boundaries of design and innovation, delivering superior surface finishes, precise hole drilling, and exceptional dimensional accuracy.
5 Axis vs. 3+2 Axis
When it comes to 5-axis CNC machining, there are two main methods employed: simultaneous 5-axis machining and 3+2-axis machining. While both approaches offer the benefits of multi-axis movement, they differ in their capabilities and characteristics.
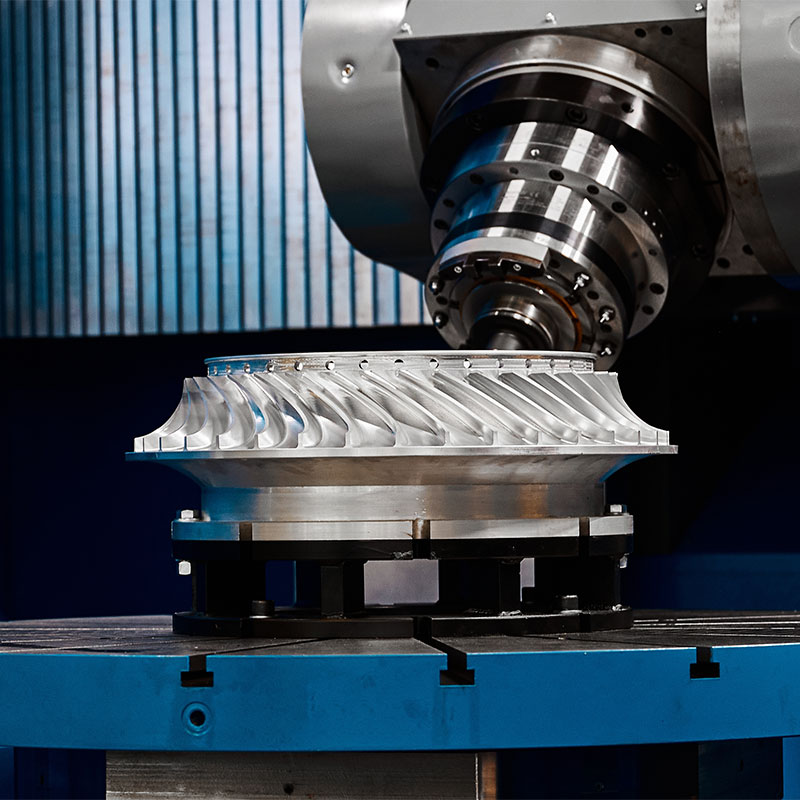
Simultaneous 5-axis machining, also known as continuous 5-axis machining, allows the machine to adjust movement on all five axes simultaneously and continuously. This means that the cutting tool can move along all axes without pauses or interruptions. This method offers high efficiency and speed since there are no breaks between passes of the cutting tool. It enables the machine to approach the workpiece from various angles continuously, resulting in smoother and more efficient machining operations. Simultaneous 5-axis machining is particularly suitable for complex geometries and intricate contours, delivering exceptional precision and surface finishes.
On the other hand, 3+2-axis machining is a form of 5-axis machining where the machine can only move on the 4th and 5th axes (adjusting the angle of the cutting tool) when the cutting tool isn’t moving along the X, Y, and Z axes. In other words, the additional axes are used when the machine is stationary. This approach can result in more rigid parts and longer tool life due to reduced stress and wear on the cutting tool. However, compared to simultaneous 5-axis machining, it may be slower since the machine has to reposition itself to adjust the cutting tool’s angle. 3+2-axis machining is often preferred for applications that require stability, such as machining deep cavities or when working with hard materials.
Get Started with Want.Net Today
Experience the precision and versatility of 5-axis CNC machining today