CNC plasma cutters have revolutionized the world of precision cutting and fabrication. With their remarkable versatility and precision, these machines have become an integral part of numerous industries. In this article, we will uncover three hidden secrets that only the experts know. Whether you’re new to CNC machining or simply curious about the inner workings of these remarkable machines, this article will provide you with valuable insights. So, let’s dive in and explore the wonders of CNC plasma cutters!
CNC plasma cutters are cutting-edge machines that use a high-velocity jet of ionized gas to cut through various types of materials with exceptional precision. They have become indispensable in industries such as automotive, aerospace, metal fabrication, and many others. From intricate designs to large-scale projects, CNC plasma cutters have the capability to handle a wide range of cutting tasks.
Secret #1: Optimizing Cut Quality
Cut quality refers to the overall precision, smoothness, and cleanliness of the cut edges. Achieving superior cut quality is essential as it directly affects the fit, finish, and functionality of the final product. Experts in the field understand the significance of cut quality and employ advanced techniques to ensure exceptional results.
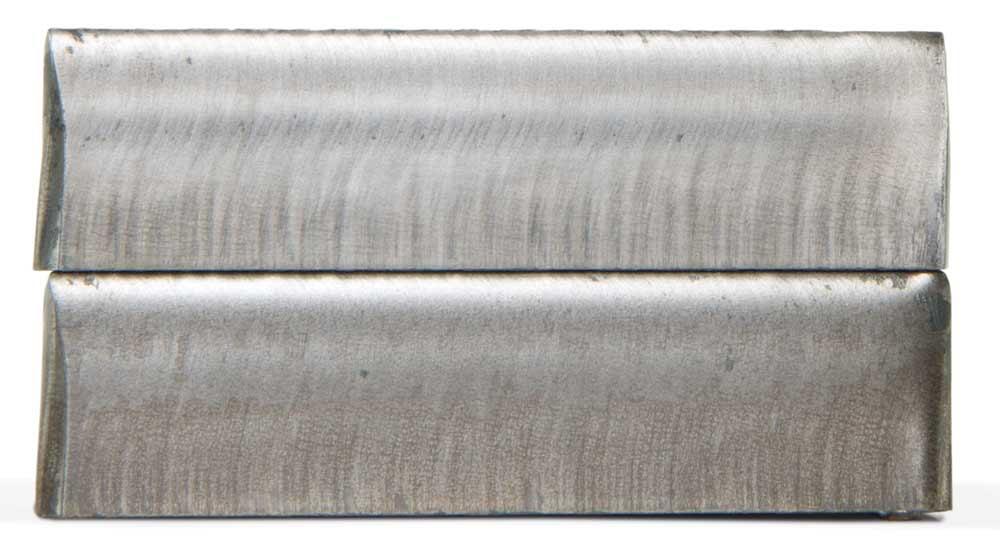
One of the key ways experts achieve superior cut quality is through the proper selection of consumables and gas types. Different materials require specific consumables, such as nozzles and electrodes, to achieve optimal results. Experts meticulously choose the appropriate consumables based on factors like material type, thickness, and desired cut quality. Additionally, selecting the right gas type, such as oxygen or nitrogen, can significantly impact the quality of the cut.
Another technique used by experts is the optimization of cutting parameters. Parameters like cutting speed, amperage, and torch height are carefully adjusted to achieve the desired cut quality. Experts understand the delicate balance between these parameters and fine-tune them to perfection. Adjusting the cutting speed can prevent excessive heat buildup, while optimizing the amperage ensures efficient material removal. Maintaining the correct torch height throughout the cutting process guarantees consistent and precise cuts.
Furthermore, experts make use of advanced software features to exercise precise control over the cutting process. CNC plasma cutters are equipped with sophisticated software that allows experts to adjust and monitor various parameters in real-time. This enables them to make on-the-fly modifications, compensate for material irregularities, and achieve exceptional cut quality. These software features include features like kerf compensation, corner slowdown, and pierce delay, which contribute to the overall precision and smoothness of the cut.
Recommended Read: 4 Remarkable Uses of CNC Plasma Cutters
Secret #2: Effective Material Handling
Efficient material handling is crucial in CNC plasma cutting as it directly impacts productivity, material utilization, and overall workflow. Experts totally get how crucial it is to handle materials effectively, so they use smart strategies to make the process smooth and efficient. This boosts productivity and saves some serious cash along the way.
One way experts enhance material handling is by implementing automated loading and unloading systems. These systems eliminate the need for manual material handling, reducing the risk of errors and increasing overall efficiency. By integrating robotic arms or conveyor systems, experts can seamlessly load raw materials onto the cutting table and remove finished parts, allowing for uninterrupted production. Automated material handling not only saves time but also enhances worker safety and ensures consistent material positioning for precise cuts.
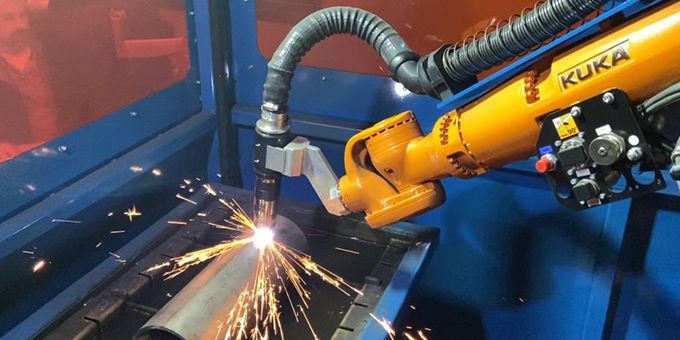
Another technique experts employ is the use of nesting software. Nesting software optimizes the arrangement of parts on the material sheet, minimizing waste and maximizing material usage. By intelligently nesting parts together, experts can reduce scrap material and increase the number of parts obtained from a single sheet. This not only saves on material costs but also reduces cutting time and improves overall productivity.
Additionally, experts apply effective clamping and fixturing techniques to enhance material handling. Properly securing the material during the cutting process prevents unwanted movement and vibrations, leading to cleaner and more accurate cuts. Experts utilize various clamping and fixturing devices tailored to the specific material and geometry of the parts being cut. This ensures stability and precision throughout the cutting process, resulting in improved quality and reduced rework.
Secret #3: Maintaining Machine Longevity
Proper maintenance helps you ensure the longevity and optimal performance of CNC plasma cutters. Experts understand the significance of regular upkeep and follow specific practices to extend the lifespan of these machines, avoiding unnecessary downtime and costly repairs.
One hidden secret experts employ is implementing regular cleaning and inspection routines. They know that keeping the machine clean from debris, dust, and accumulated metal shavings is essential for its smooth operation. By performing routine cleaning and inspections, experts can identify potential issues early on, such as worn-out components or loose connections, preventing them from escalating into major problems.
Another secret to maximizing machine longevity is maintaining the lubrication and cooling systems. Experts are diligent in keeping these systems well-maintained and functioning optimally. They ensure that the appropriate lubricants are used and regularly check and replace filters, if necessary. Proper lubrication reduces friction and wear on moving parts, while an efficiently functioning cooling system helps prevent overheating, preserving the machine’s overall health.
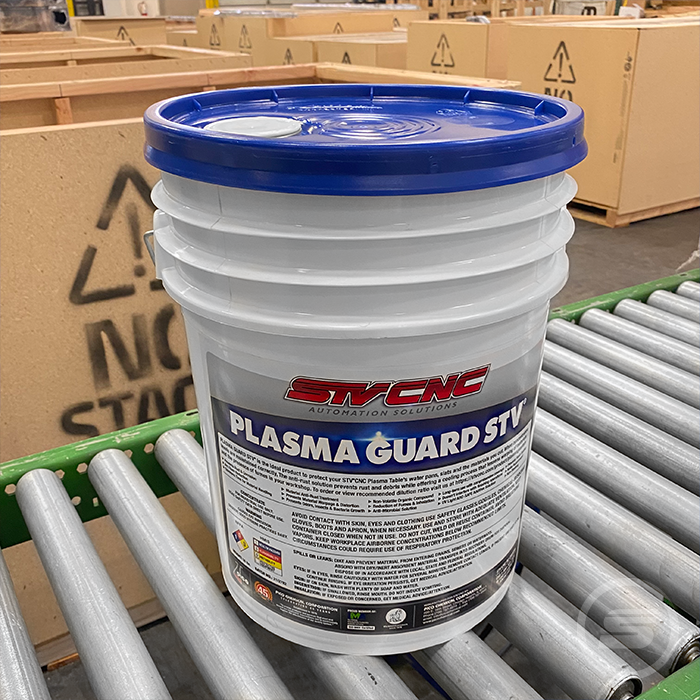
Timely consumable replacements are also a hidden secret to maintaining CNC plasma cutter longevity. Experts understand the importance of replacing consumable parts, such as nozzles, electrodes, and shields, at recommended intervals. These parts wear out over time and can affect cut quality and machine performance. By staying on top of consumable replacements, experts ensure consistent and precise cuts while minimizing unnecessary strain on the machine.
By adhering to regular cleaning and inspection routines, maintaining lubrication and cooling systems, and performing timely consumable replacements, experts ensure that their CNC plasma cutters stay in top-notch condition. These hidden secrets not only extend the machine’s longevity but also contribute to consistent, high-quality cuts and overall productivity.
The Bottom Line
As you embark on your CNC machining journey, keep these hidden secrets in mind. By incorporating these expert strategies into your practice, you’ll be well on your way to achieving exceptional cut quality, improving material handling efficiency, and maximizing the lifespan of your CNC plasma cutter.
Remember, the world of CNC machining is filled with endless possibilities, and with dedication and continuous learning, you can become a true expert in the field. Keep exploring, experimenting, and shining brightly as you create remarkable pieces with your CNC plasma cutter.
Other Articles You Might Enjoy
- 4 Remarkable Uses of CNC Plasma Cutters
CNC plasma cutters may sound like something out of a science fiction movie, but they are actually incredible machines that can do some pretty amazing things! CNC stands for Computer…
- What is a CNC Plasma Cutter?
In the fast-paced world of CNC machining, where precision and efficiency reign supreme, the CNC Plasma Cutter emerges as a groundbreaking tool. If you're new to the realm of CNC…
- The Role of Precision in CNC Machining: How Tight Tolerances Impact Cost and Quality?
Introduction: Understanding Precision in CNC Machining In manufacturing contexts, precision is epitomized by Computer Numerical Control (CNC) machining. In essence, CNC machining is a process utilized widely within the manufacturing…