What Technical Expertise Should You Look for in a China CNC Machining Service?
When scouting for a CNC machining service in China, the technical expertise of the provider is paramount. This expertise encompasses not only the basic operational knowledge of CNC machines but also a profound understanding of complex machining processes, material behavior, and the latest technological advancements in CNC machining.Now, you can try to submit processing requirements through the Internet and get online cnc machining quote.
Key areas of technical expertise include precision engineering, computer-aided design (CAD) and computer-aided manufacturing (CAM) proficiency, advanced material science knowledge, and expertise in the latest CNC technologies such as 5-axis machining and live tooling. These competencies enable the machining service to handle intricate designs, maintain high precision, and offer innovative solutions.
Data Table: Technical Expertise Evaluation Metrics
Expertise Area | Description | Importance for CNC Projects | Expected Proficiency Level |
---|---|---|---|
CAD/CAM Proficiency | Ability to efficiently use design and manufacturing software. | Crucial for translating complex designs into precise machining instructions. | High |
5-Axis Machining | Capability to perform intricate machining on five axes simultaneously. | Essential for complex geometries and reducing setup times. | Advanced |
Material Science | Understanding of diverse material properties and machining behavior. | Critical for selecting optimal materials and machining parameters. | Expert |
Precision Engineering | Expertise in achieving and maintaining high precision and tolerances. | Directly impacts the quality and functionality of machined parts. | Expert |
Process Optimization | Ability to streamline machining processes for efficiency. | Affects overall production time and cost. | Advanced |
Quality Control | Rigorous quality assurance practices and standards. | Ensures the reliability and consistency of machined parts. | High |
Innovation and Adaptability | Keeping abreast of and incorporating new machining technologies and methods. | Enables tackling novel and challenging projects. | Advanced |
The technical expertise of a CNC machining service is a critical determinant of their capability to deliver high-quality parts that meet your specifications. It influences everything from the feasibility of your project to the efficiency of production and the quality of the final product.
How Does Machine Precision Influence the Efficiency and Quality of Your Products?
Machine precision is a cornerstone of CNC machining, directly influencing both the efficiency of the manufacturing process and the quality of the final products. Precision refers to the machine’s ability to reproduce the dimensions and tolerances of the parts as designed, with minimal deviation.
High-precision CNC machines can achieve tighter tolerances, finer surface finishes, and more consistent part quality. This precision minimizes the need for post-processing, reduces material waste, and enhances the functionality and aesthetic appeal of the parts.
Graph Illustration: Correlation Between Machine Precision and Product Quality
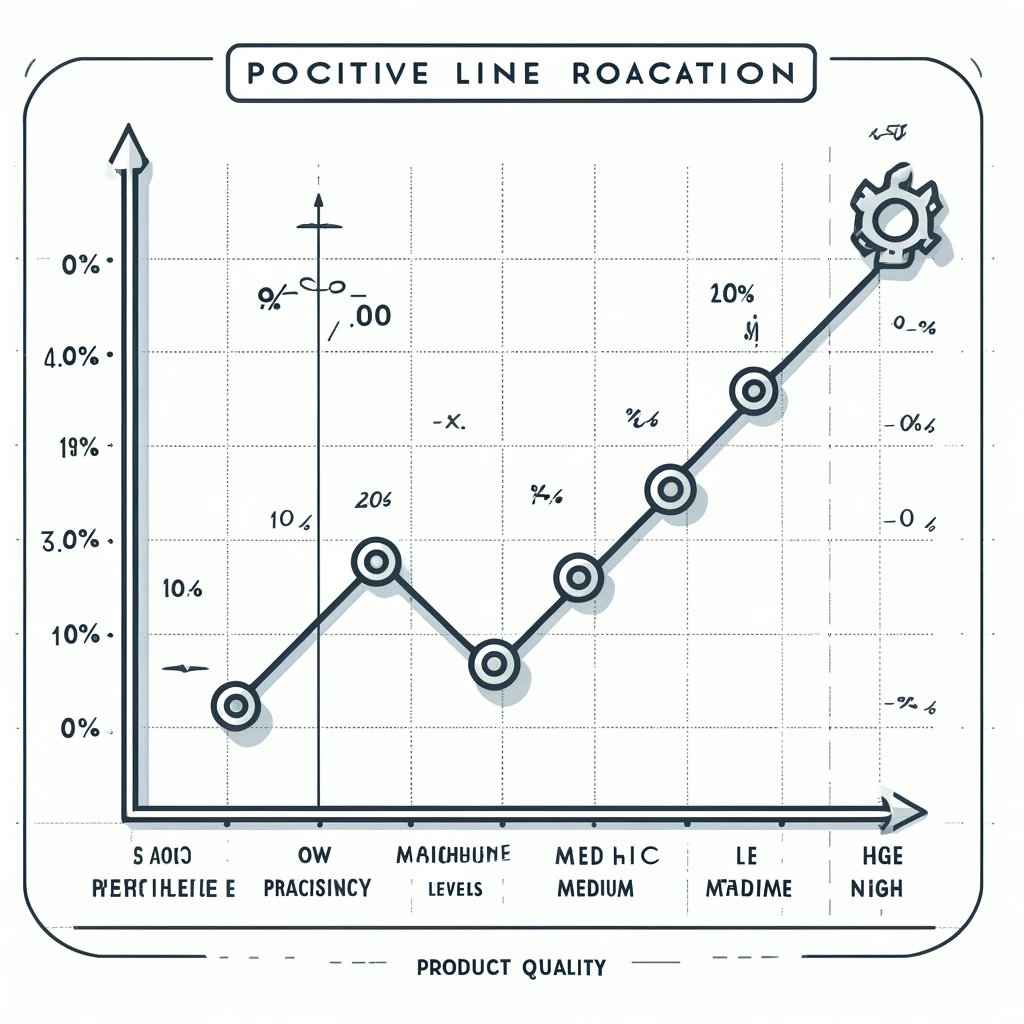
[A graphical representation showing the positive correlation between the level of machine precision and the overall quality of the produced parts. The x-axis represents different levels of machine precision, while the y-axis shows the corresponding product quality rating.]
Assessing the machine precision capabilities of a CNC service is integral to ensuring that the parts produced will meet your project’s specific requirements. High machine precision is particularly vital for industries where the slightest deviation can significantly impact the performance or safety of the final product, such as in aerospace, medical devices, and automotive sectors.
Why Is Efficient Project Management Essential in CNC Machining Services?
Efficient project management in CNC machining services encompasses thorough planning, execution, monitoring, and control of all aspects of the production process. It ensures that projects are completed on time, within budget, and to the specified quality standards. An efficient project management system integrates various functions, including customer communication, design review, material procurement, machining, quality control, and logistics.
The project management life cycle in CNC machining can be broken down into five phases: initiation, planning, execution, monitoring & control, and closure. Each phase plays a crucial role in ensuring the project’s success.
Data Table: Project Management Efficiency Metrics
Metric | Industry Standard | Target for Excellence | Impact on CNC Machining |
---|---|---|---|
Lead Time Reduction (%) | 10-20% | >30% | Reduced turnaround time for projects |
On-time Delivery Rate (%) | 95% | 99% | Higher customer satisfaction and repeat business |
Rework Rate (%) | <5% | <1% | Improved quality and reduced waste |
Customer Satisfaction Score (1-10) | 7-8 | 9-10 | Increased trust and brand loyalty |
Project Cost Variance (%) | ±10% | ±5% | Better budget management and profitability |
Communication Efficiency (Scale 1-5) | 3-4 | 5 | Smoother project flow and fewer misunderstandings |
Error Reporting Time (Hours) | <24 | <12 | Faster resolution of issues, minimizing delays |
Efficient project management in a CNC machining service is indicative of the provider’s ability to handle complex projects and deliver high-quality products on time. It reflects their organizational capabilities and commitment to customer satisfaction, making it a critical factor in your selection process.
What Are the Implications of Advanced CNC Technologies on Your Manufacturing Outcomes?
The adoption of advanced CNC technologies marks a significant leap in manufacturing capabilities, offering unprecedented precision, flexibility, and efficiency. These technologies, ranging from 5-axis machining to adaptive machining, high-speed machining, and automated tool changes, have profound implications for manufacturing outcomes.
Advanced CNC technologies enable the machining of complex geometries that were previously unattainable, significantly reduce setup and machining times, and improve the consistency and quality of the parts produced. They also facilitate the efficient use of materials and optimize tool paths, reducing waste and wear.
Data Table: Advanced CNC Technologies and Their Manufacturing Impacts
Technology | Description | Impact on Efficiency | Impact on Precision | Impact on Flexibility |
---|---|---|---|---|
5-Axis Machining | Machining parts from five sides in a single setup. | Drastically reduces setup times. | Allows for intricate geometries with tight tolerances. | Enables complex shapes without repositioning. |
High-Speed Machining | Utilizing higher spindle speeds and feed rates. | Shortens machining times. | Reduces thermal distortion for higher precision. | Facilitates quick production of parts. |
Adaptive Machining | Adjusting machining parameters in real-time based on sensor feedback. | Optimizes machining efficiency. | Enhances surface quality and consistency. | Adapts to varying material conditions. |
Automated Tool Changes | Switching between tools without manual intervention. | Minimizes non-productive time. | Maintains consistent tool performance. | Allows for multi-operation machining without delays. |
Robotic Automation | Incorporating robots for part loading/unloading and machining. | Maximizes machine utilization. | Ensures consistent part handling. | Enables lights-out manufacturing. |
Real-Time Monitoring | Continuous monitoring of machining parameters. | Allows for immediate optimizations. | Prevents machining errors, improving quality. | Adapts processes to maintain optimal conditions. |
Graph Illustration: Efficiency Gains from Advanced CNC Technologies
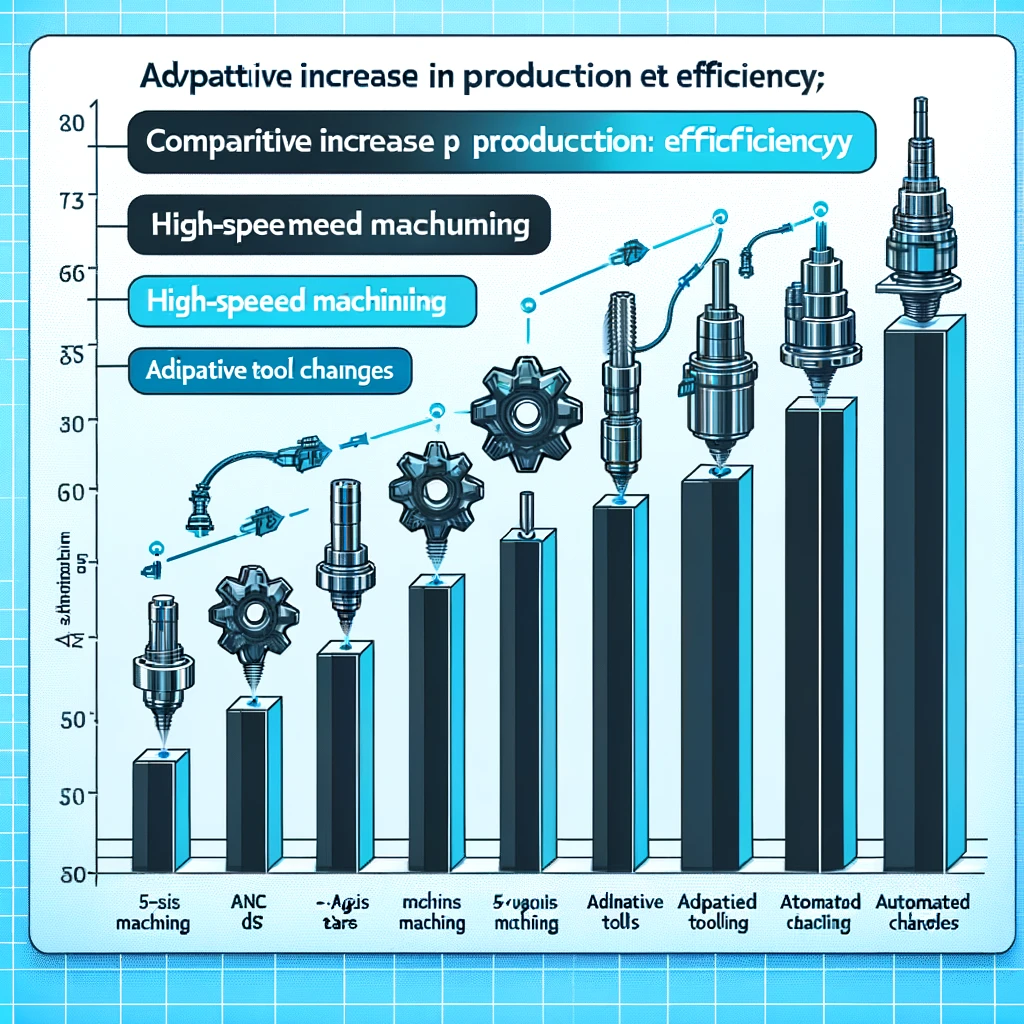
[Graph Here: A bar chart illustrating the efficiency gains achieved through the adoption of various advanced CNC technologies. Each bar represents a different technology, showing a comparative increase in production efficiency relative to traditional machining methods.]
When evaluating potential CNC machining services, it’s crucial to consider their use of advanced technologies. Services that invest in and effectively utilize these technologies are more likely to deliver superior manufacturing outcomes, characterized by higher precision, faster turnaround times, and the ability to handle a broader range of machining tasks. This technological edge can significantly enhance your product’s market competitiveness by improving quality, reducing costs, and shortening development cycles.
How Do Turnaround Time and Scalability Impact Your Decision in Choosing a CNC Service?
In the dynamic landscape of manufacturing, the ability of a CNC service to offer rapid turnaround times and scalable solutions directly influences your project’s success and your company’s agility in responding to market opportunities.
Turnaround time in CNC machining encompasses the entire cycle from receiving a CAD model to delivering the finished parts. It is a critical measure of a service’s operational efficiency and responsiveness. Scalability, on the other hand, refers to the service’s ability to adjust production volumes up or down without compromising quality or lead times, accommodating fluctuating demand and enabling growth.
Data Table: Evaluating Turnaround Time and Scalability
Factor | Description | Impact on Projects | Ideal Service Characteristics |
---|---|---|---|
Turnaround Time | Time from order placement to delivery. | Critical for meeting project deadlines and market launches. | Short, predictable turnaround times with high reliability. |
Production Scalability | Ability to adjust production volume. | Essential for adapting to market demand fluctuations. | Flexible production capacity with minimal lead time changes. |
Batch Flexibility | Capability to handle various batch sizes. | Important for prototyping, testing, and full-scale production. | Efficient handling of both small and large orders. |
Rapid Prototyping | Quick production of prototype parts. | Enables faster design iteration and development. | Expedited services for prototype development. |
Emergency Services | Ability to expedite urgent orders. | Useful for critical project needs or unforeseen demands. | Fast-track options for high-priority projects. |
Capacity Management | Effective allocation of machining resources. | Ensures consistent quality and turnaround regardless of volume. | Robust planning and resource allocation strategies. |
Technology Adaptation | Utilization of tech for efficiency gains. | Improves speed and capacity for handling complex projects. | Adoption of advanced CNC technologies and automation. |
Graph Illustration: Impact of Scalability on Customer Satisfaction
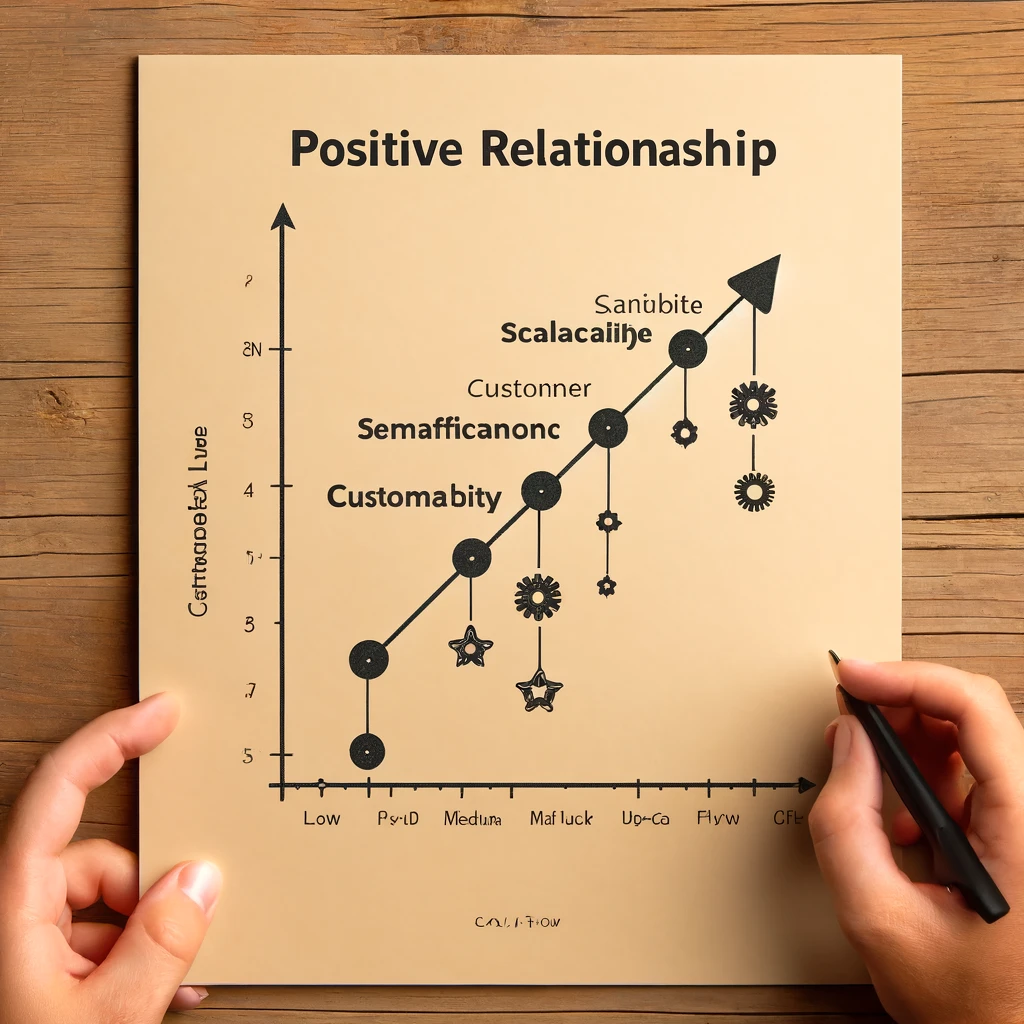
[Graph Here: A line graph showing the relationship between a CNC service’s scalability level and overall customer satisfaction, based on a survey of manufacturers. The graph indicates higher satisfaction levels as scalability increases, reflecting the value of flexible production capabilities.]
The turnaround time and scalability offered by a CNC service are pivotal factors in your selection process. A service that can rapidly produce high-quality parts and adjust to changing demands can significantly enhance your operational flexibility, reduce time-to-market for new products, and better manage inventory levels, ultimately contributing to a stronger market position and improved customer satisfaction.
What Role Does Quality Assurance Play in CNC Machining Services?
Quality Assurance (QA) in CNC machining is a comprehensive process that ensures the manufactured parts meet all specified requirements. It encompasses various stages, from raw material inspection to the final product checking.
QA in CNC machining involves a series of standardized procedures and checks, including dimensional accuracy, material properties, and surface finish, to ensure the final product adheres to the predefined standards and specifications.
Data Table: QA Metrics for CNC Machining
QA Metric | Description | Acceptable Range | Ideal Target | Impact on CNC Projects |
---|---|---|---|---|
Dimensional Accuracy | Measurement of part dimensions against specifications. | ±0.05 mm | ±0.01 mm | Directly affects the fit and function of parts. |
Surface Finish | Measure of the surface quality of machined parts. | RA 3.2 μm | RA 0.8 μm | Influences the aesthetic and performance of parts. |
Material Hardness | Resistance of material to deformation. | Within material spec | As per design requirements | Affects durability and wear resistance. |
Tolerance Adherence | The degree to which parts conform to specified tolerances. | Within ±0.1 mm | Within ±0.02 mm | Ensures compatibility and interoperability of parts. |
Part Flatness | Measure of part flatness over its surface. | 0.1 mm deviation | 0.01 mm deviation | Critical for parts requiring high precision assembly. |
Wall Thickness | Minimum and maximum wall thickness in parts. | As per design spec | +0.00/-0.02 mm | Affects part strength and material usage. |
Tool Marks | Visibility of tool marks on part surfaces. | Minimal acceptable | None | Affects surface finish and part aesthetics. |
Burr Formation | Presence of burrs or sharp edges post-machining. | Non-critical areas acceptable | Complete removal | Impacts part assembly and safety. |
Understanding a service provider’s QA processes is essential in evaluating their capability to produce high-quality parts consistently. It reflects their commitment to precision and reliability, key factors for the success of your CNC machining projects.
How Can Effective Communication and Project Management Enhance CNC Machining Efficiency?
Effective communication and robust project management are crucial in CNC machining services for ensuring that projects are completed as per the client’s requirements, on time, and within budget.
Effective communication encompasses clear articulation of project requirements, regular updates, and open feedback channels, while project management involves planning, execution, monitoring, and closing of projects with efficiency and precision.
Case Study: Consider a complex project involving the production of aerospace components where precise tolerances and strict material specifications were critical. Through effective communication, the CNC service provider was able to clearly understand the project requirements, while adept project management ensured that the project was completed within the tight deadlines, adhering to all quality standards.
Graph Illustration: Impact of Communication on Project Timelines
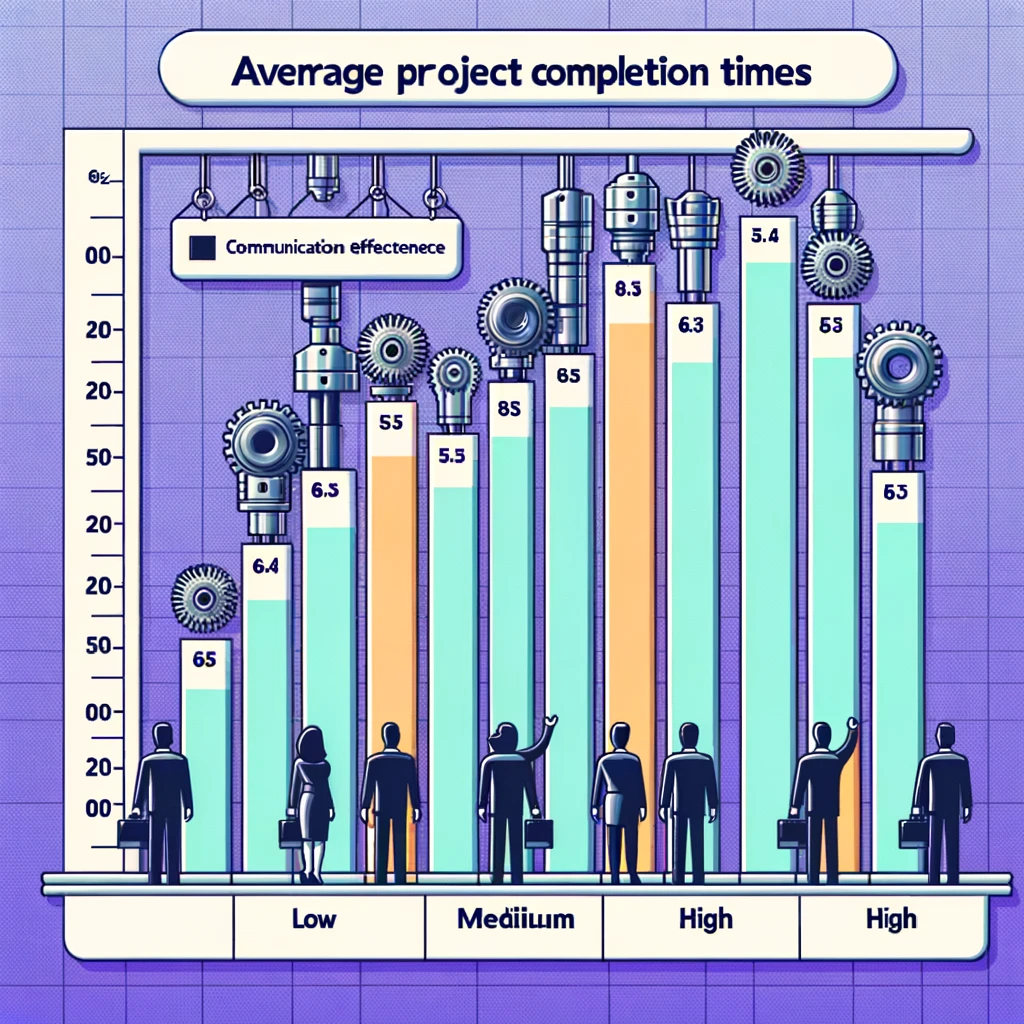
[Graph Here: The graph could show a comparison between projects with high levels of communication and those with lower levels, demonstrating shorter project timelines and higher client satisfaction in projects with more effective communication.]
Assessing a service provider’s communication and project management capabilities is vital. It indicates their ability to understand and meet your project requirements effectively, ensuring the success and efficiency of your CNC machining projects.
Other Articles You Might Enjoy
- Material Versatility in CNC Machining: From Titanium to Thermoplastics
Introduction to CNC Machining CNC machining stands as a cornerstone in the manufacturing sector, enabling the precise creation of parts and components. This process utilizes computer numerical control (CNC) to…
- Precision CNC Machining of Steel: High-Volume Production
Precision CNC Machining and High-Volume Production As an integral part of modern manufacturing processes, Precision Computer Numerical Control (CNC) machining brings about unmatched accuracy and consistency in the production of…
- Precision CNC Machining for High-End Audio Equipment
Precision CNC Machining in High-End Audio Equipment Manufacturing Precision Computer Numerical Control (CNC) machining refers to a highly-advanced technology where computer-generated codes are used to operate factory machinery and tools.…