CNC machining is a versatile process that can produce custom parts in various materials, including metals, plastics, and composites. If you need to manufacture custom CNC parts, the following steps can guide you through the CNC machining process.
Material selection for Custom Machined Parts
The material selection depends on the requirements of the metal part, such as its:
- Strength
- Durability
- and resistance to wear
Some common materials used in CNC machining include:
- Aluminium
- brass,
- steel
- Titanium
- and plastics such as polycarbonate and nylon.
Design considerations
When designing a custom-machined part, it is important to consider the capabilities of the CNC machine shop near you. By designing the part with these factors in mind, you can ensure that the part can be produced with the required accuracy and precision.
Programming the CNC machine for excellent surface finish
Programming the CNC machine involves creating a set of instructions for the machine to follow to create the part.
The programming process is typically done using CAM. The program will include information such as the cutting tools, the cutting speed, and the path the tool will follow.
Quality control
After the custom metal part is manufactured, it is important to perform quality control checks to ensure it meets the required specifications. It involves measuring the part to ensure it is the correct size and shape and checking for defects or imperfections.
Finishing the Metal Part
After the custom metal part has been produced, the final step is to finish the part. It may involve CNC machining processes such as:
- Polishing
- Anodizing the part to give it the desired appearance and surface finish.
CNC Machining for Custom Machined Parts – Want.net
Want.net is an online CNC machining service for custom-machined parts. It offers various machining services, including milling, turning, and EDM. They use state-of-the-art machines and equipment to ensure high-quality parts that meet your specifications.
What is Tool geometry in Custom CNC machining?
Tool geometry refers to the cutting tool’s physical shape, angles, and features used in custom CNC machining services. The geometry of a cutting tool is designed to optimize its cutting performance, efficiency, and accuracy for a specific machining application.
Design Guidelines for CNC Machining Rapid Prototyping
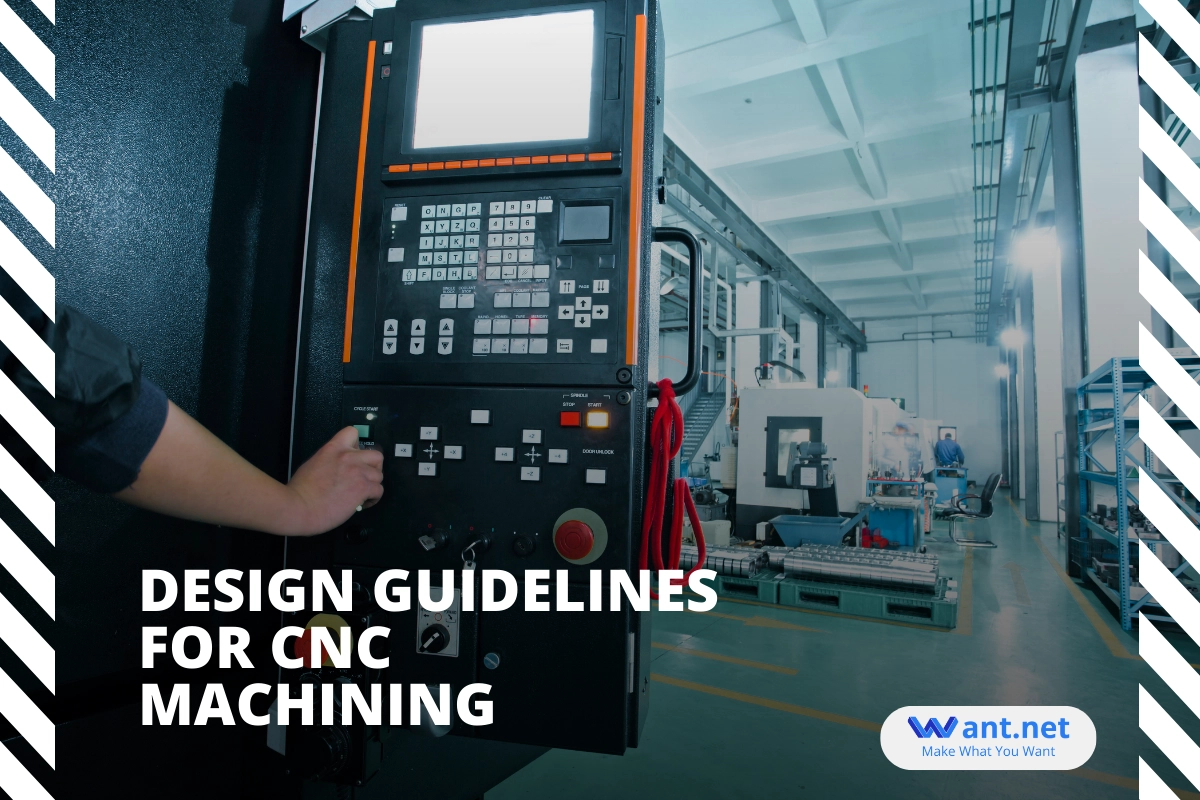
Design for manufacturability
Before you start designing, consider the process and design the part to minimize the complexity of machining. Avoid designing parts with undercuts, sharp corners, and thin walls, as they can be challenging to machine.
Choose appropriate materials
Select the right material that suits the application of the part. Different materials have varying machining properties, such as hardness, toughness, and brittleness. Machining aluminium is different from machining steel or titanium.
Use Right tolerances
CNC machining can achieve tight tolerances, but they come at a cost. Tighter tolerances increase machining time, which increases the cost. Consider the application and specify the necessary tolerance for the part.
Design for stability
During machining, parts must be securely placed to avoid movement or vibration. Design features such as flat surfaces and parallel edges can help stabilize the part during machining.
Simplify part geometry
Simple part geometries are easier to machine and have shorter cycle times to reduce CNC machining costs. Avoid designing parts with complex geometries, as they require more setup time and specialized tooling.
Provide sufficient draft angles
Provide draft angles on features such as ribs, bosses, and walls to allow for easy ejection of the part from the mould. It reduces the risk of damage to the part and ensures the proper surface finish.
Consider surface finish requirements for Custom Machined Parts
CNC machining can achieve a wide range of surface finishes, but the finish quality depends on several factors, such as:
- The type of material and machining parameters
- Specify the required surface finish for the part
- work with your machining service shop.
By following these guidelines, you can design parts optimized for CNC machining, which can help you save on CNC machining costs, reduce lead times, and achieve high-quality parts with tight tolerances.
Custom Machining for Low-volume Production
Custom machining is creating custom metal parts according to specific requirements and designs. It involves using various tools and machines to cut, shape, and form materials such as metals, plastics, and composites.
Prototype Machining for Design Verification and Engineering Testing
Prototype machining is the process of creating a physical model or prototype of a product using machining techniques such as milling, drilling, turning, or grinding.
It is an essential step in the product design and development process, as it allows designers and engineers to test the functionality and feasibility of their designs before moving to mass production.
Design verification and engineering testing are two critical aspects of rapid prototype machining. Design verification involves testing the product prototype to ensure it meets the intended design specifications and functions as expected.
It may involve checking dimensions, tolerances, materials, and other factors critical to the product’s performance.
Engineering testing involves subjecting the product prototype to various stresses, loads, and environmental conditions to evaluate its performance and durability. These tests may include fatigue testing, vibration testing, temperature testing, and more.
The results of these tests help designers and engineers identify potential design flaws and make necessary improvements to the product.
The Ordering Process for CNC Machining Quotes
The ordering process for CNC machining quotes typically involves the following steps:
Request for Quote (RFQ): The first step is to send an RFQ to the provider. It should include a detailed description of the part or component to be machined, including dimensions, material specifications, and any special requirements or tolerances.
Quote Preparation: Based on the RFQ, the provider will prepare a quote that outlines the estimated cost and lead time for the project. The quote should include a breakdown of the materials, labor, and other associated costs.
Review of Quote: The customer should carefully review the quote to ensure it meets their requirements and budget. If necessary, they can request revisions or clarification from the service provider.
Order Confirmation: Once the customer is satisfied with the quote, they can confirm it by providing a purchase order or other formal documentation. The provider will then initiate the production process.
CNC Machining Tolerances
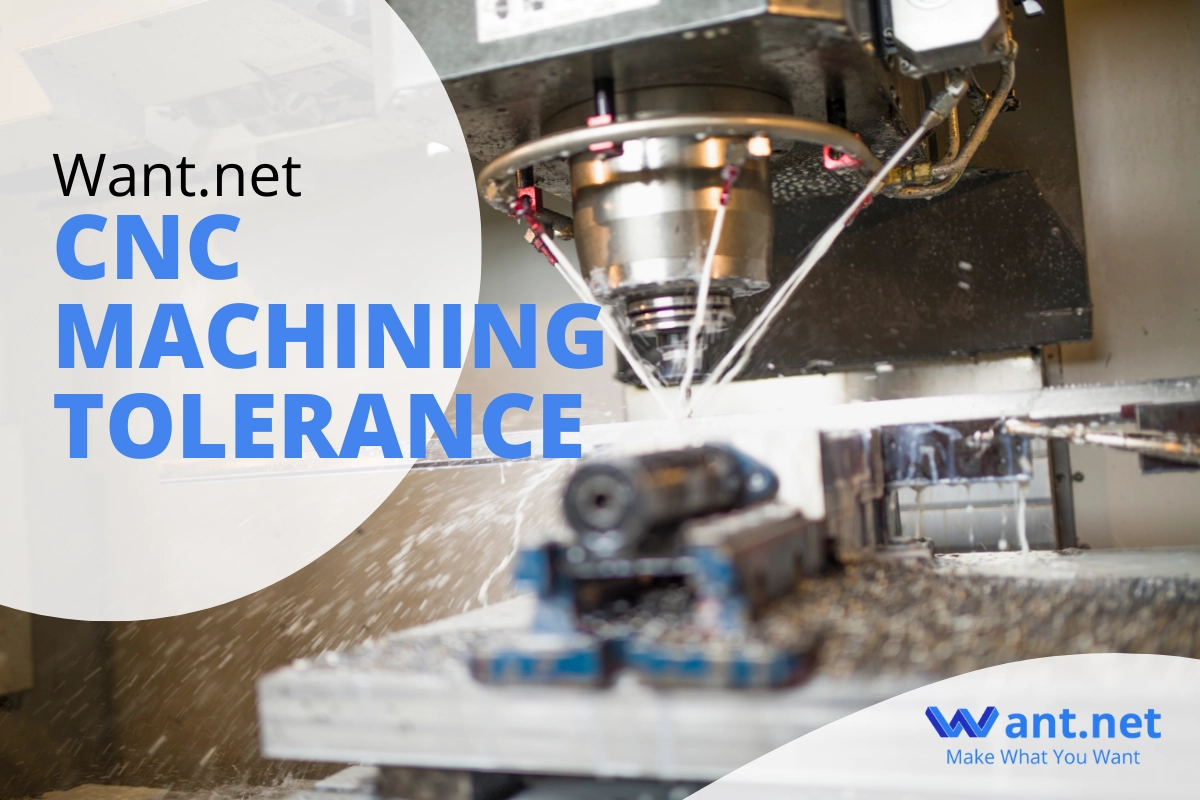
CNC machining tolerances refer to the allowable range of deviation from a specified dimension or measurement in a part or component process. In other words, it is the degree of accuracy to which the final product must adhere to the design specifications.
Typically, the tolerance for CNC machining depends on the part’s complexity, size, material, and manufacturing process used. The common tolerances for CNC machining range from +/- 0.005 to +/- 0.0005 inches, depending on the application and design requirements.
What is the typical cost of a CNC machined part?
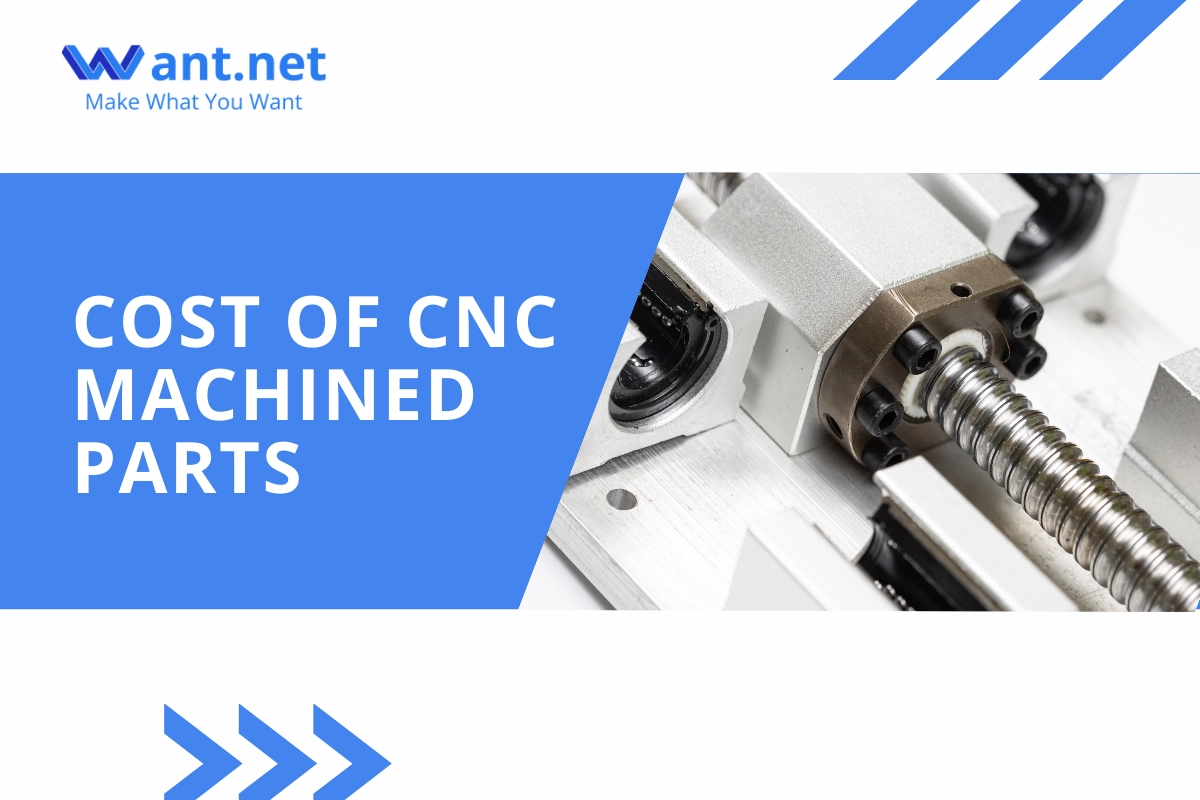
The cost of CNC machining per hour can vary widely depending on several factors, such as the type of machine being used, the complexity of the part being produced, the material being machined, the location of the machine shop, and other factors.
In general, the hourly rate for CNC machining price ranges from around $50 per hour to over $100 per hour. However, some machine shops may charge significantly more or less than this depending on their location, expertise, and other factors.
CNC Machining Materials
CNC (Computer Numerical Control) machining is a process that involves the use of computer-controlled machines to remove material from a workpiece to create a final product.
Some common materials used for CNC machining include metals like aluminium, brass, copper, titanium, and steel and plastics such as acrylic, nylon, and polycarbonate. Additionally, certain composites, ceramics, and wood can be used in CNC machining.
What is design for manufacturability (DFM)?
Design for manufacturability (DFM) is a set of guidelines and principles used in the design process to optimize the process’s ease, efficiency, and cost-effectiveness. DFM aims to ensure that the product can be manufactured quickly, reliably, and economically, with minimal waste and rework.
7 Steps for a technical drawing for CNC machining
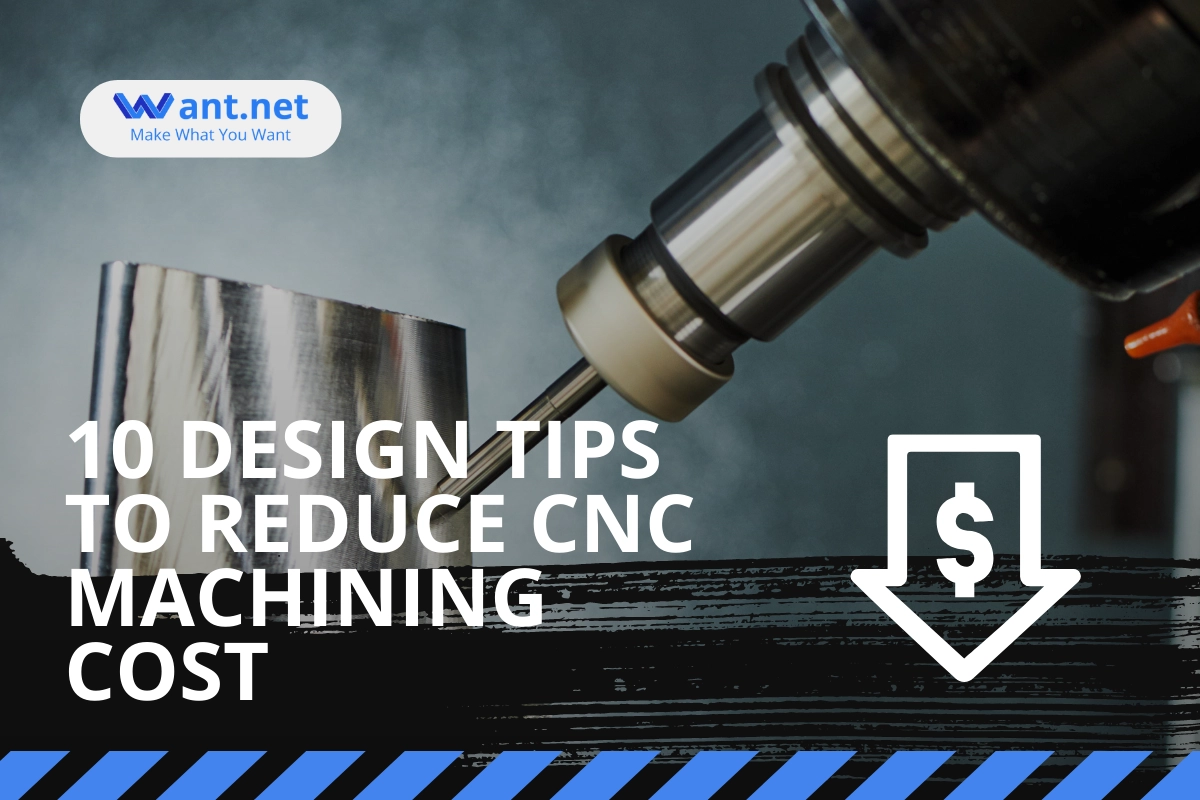
Following these simple guidelines will help ensure that your drawings are as good as possible.
Step 1: Provide enough space between orthographic views to add dimensions.
Step 2: Are there any complicated features or other parts on your part? If so, include section views or detail views.
Step 3: At this point, add construction lines to each view.
Step 4: After adding construction lines, your drawing is ready to receive dimensions.
Step 5: Detail where, how long, and how big each thread is.
Step 6: Provide additional tolerance information for any features requiring a higher level of accuracy than the default tolerances.
Step 7: Fill the title block with the necessary details.
Why Choose Want.net CNC Machining Services?
Want.net is a CNC machining service that provides high-quality precision parts to businesses and individuals worldwide.
Quality: Want.net takes pride in delivering high-quality precision parts that meet or exceed customer expectations. The company uses state-of-the-art CNC machines and the latest software to produce accurate and reliable parts.
Our company has experience working with various materials, including metals, plastics, and composites. This versatility allows them to produce parts for the medical, automotive and aerospace industries.
Other Articles You Might Enjoy
- Aluminum CNC Machining Service for Custom Parts
Aluminum CNC machining stands at the forefront of modern manufacturing, epitomizing precision, versatility, and efficiency. With its widespread applications across industries ranging from aerospace to automotive and beyond, aluminum CNC…
- Unraveling the World of CNC Machined Plastic Parts(CNC machined plastic parts Mabel)
Modern innovations have taken traditional manufacturing methods to new heights. One such innovation that stands out is Computer Numerical Control (CNC) machining, a process used extensively in various industries from…
- CNC Machined Plastic Parts: An In-depth Overview(CNC machined plastic parts Norman)
Computer Numeric Control (CNC) machining is an advanced manufacturing process where pre-programmed software dictates the movement of factory machinery and tools. These applications can carry out complicated manufacturing tasks with…