Metal machining, particularly CNC milling, plays a crucial role in modern prototyping techniques. To enhance efficiency, prototype manufacturers strive to maximize their equipment capabilities by adopting advanced technologies. In recent years, helical milling has gained popularity as a preferred method. In this article, we will delve into the concept of helical milling, discuss its advantages and disadvantages, and explore how you can leverage this knowledge to design cost-effective prototypes.
Understanding Helical Milling
Helical milling offers an alternative approach to hole-making processes. This technique involves utilizing an endmill that follows a helical trajectory, resulting in high-quality bores. In comparison to conventional drilling, helical milling presents several advantages and can even replace the need for boring machines. This aspect is particularly advantageous for prototyping shops seeking to minimize equipment investments. Helical milling enables the creation of bores in various shapes, reduces cutting force and tool wear, and delivers excellent quality results.
Why Choose Milling Over Drilling?
While conventional drilling remains a widely-used method for creating holes, it possesses inherent limitations that justify the adoption of the more intricate milling technique. Let’s explore the drawbacks of drilling:
1. Inconsistent Drilling Speed
Drilling speed varies depending on the diameter, with the highest speed at the outer point and practically zero speed at the center of the drill where the axis is located. As a result, the machining process near the revolution axis involves more plastic deformation than cutting. This leads to increased thrust force and significant tool wear.
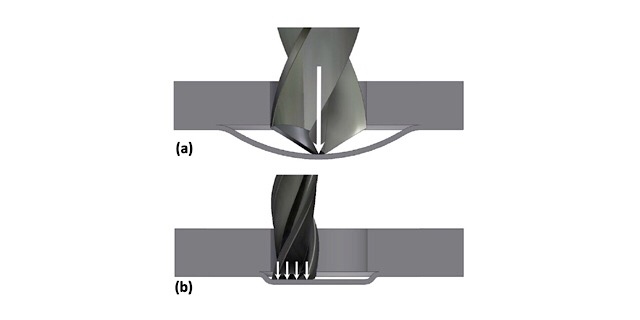
2. Material Protrusion and Manual Finishing
The axial thrust force exerted by the drill, especially a worn one, causes the thin layer of metal to bend as it exits the stock. This results in leftover material protruding around the hole, necessitating manual removal. Employing milling techniques significantly reduces the amount of leftover material.
3. Suboptimal Chip Removal Conditions
Drilling poses challenges for effective chip removal. The processed material can only be removed through the drill flutes, which impacts the surface finish and cutting temperature. As metal chips move from the cutting zone through the flutes to the surface, they scrape the sides of the hole, resulting in lower surface quality. Additionally, these chips carry up to 80% of the cutting warmth, thereby increasing the drill’s temperature and accelerating wear. To enhance chip removal, operators often employ discrete drilling methods, where the drill processes a part of the length before being removed. While this strategy proves effective, it also increases drilling time.
Considering these significant drawbacks, manufacturers increasingly turn to helical milling to enhance machining efficiency in prototyping shops.
Key Aspects of Helical Milling
Let’s now explore some essential aspects of helical milling:
1. Complex NC Programming
Helical milling involves the end mill moving along a helical path, necessitating the combination of vertical (z-axis) and horizontal (x-y axis) movements. Consequently, manually writing the NC program for helical milling can be challenging. However, many CAM systems have incorporated helical milling as one of their strategies, simplifying the programming process.
2. Chip Geometry and Cutting Forces
The chip geometry in helical milling comprises two zones: the blue zone created by the side of the end mill and the red zone created by the face of the mill. The ratio between these zones depends on the tool and bore diameters:
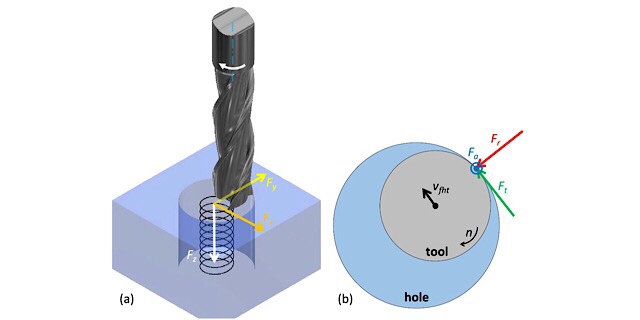
When using larger tools, the blue zone expands, leading to discontinuous milling and poorer surface finish. Additionally, larger tools generate higher radial cutting forces, causing tool deflection inside the hole and reducing tolerance. However, larger tools exhibit greater rigidity, mitigating the negative effects to some extent. On the other hand, smaller tools result in a larger red zone, minimizing radial force and vibration. Yet, the decrease in tool diameter is limited by system rigidity.
To achieve optimal results, it is advisable to begin with a larger tool and switch to a smaller one for the final cut with low depth and feed. This approach ensures excellent surface finish.
Advantages of Helical Milling
Helical milling offers several compelling advantages:
1. Precise Diameter and Surface Quality
With helical milling, you can achieve any desired diameter with exceptional precision and surface quality without changing the tool. Unlike conventional drilling, which often requires multiple tool changes for larger holes, helical milling enables efficient hole creation using a single endmill. Subsequently, a smaller feed can be utilized to achieve the desired tolerance and surface quality. With helical milling, you can achieve tolerances up to IT7 with a surface finish of Ra 1.25, all without the need for tool changes.
2. Lower Cutting Temperature and Improved Chip Removal
The endmill used in helical milling does not occupy the entire bore, offering a distinct advantage. Rather than extracting the tool after plunging a certain depth, as required in drilling, helical milling allows coolant to be sprayed directly into the hole, facilitating chip removal and reducing cutting temperature. This feature contributes to longer tool life and enhanced machining performance.
3. Predictable Tool Wear and Trajectory Modifications
One of the challenges in drilling is detecting tool wear, which is often realized when the drill breaks or gets stuck in the bore, particularly when machining hard materials. In helical milling, the process is akin to milling, enabling the prediction of tool wear using established calculation methods or manufacturer-specified tool life. This valuable insight enables operators to make trajectory modifications to maintain dimensional accuracy during the machining process. Such flexibility is not possible with drilling.
Conclusion
Undoubtedly, helical milling represents an innovative process with its own limitations. While challenges such as chip removal rate and limited research on certain parameters persist, this technique significantly reduces the number of setups, machining operations, and tool changes while maintaining high-quality bores. For prototyping manufacturers aiming to streamline their operations and minimize tooling and equipment requirements, helical milling presents a considerable advantage. By harnessing the potential of helical milling, manufacturers can optimize their metal machining strategies for improved prototyping outcomes.
Recommended Reads:
- 2023 Best CNC Machining Company From China: Machined Parts Guide for Beginners
- Improve the Precision of Your CNC parts
- Everything You Should Know About CNC Machining Titanium
- How to Select The Right Plastic For Your CNC Machined Parts
- What is Heat Treatment in CNC Machining
Other Articles You Might Enjoy
- 3 Effective Strategies for Cost Optimization in CNC Prototyping
When considering the production of CNC prototypes, cost is often a top concern. As designers, we strive to find ways to reduce expenses and enhance production efficiency. In this article,…
- Using CNC Machining to Fabricate Lightweight Metal and Remove Chrome From Metal( cnc machining services china Dana)
CNC (Computer Numerically Controlled) machining is an essential process in the manufacturing domain. With its precision, adaptability, and extensive applications, many industries rely on it for fabricating highly complex parts…
- Efficient CNC Machining of Lightweight Metal and Chrome Removal( cnc machining services china Atwood)
Computer Numerical Control (CNC) machining is a modern manufacturing process used in various industries, frequently dealing with lightweight metals or needing to remove chrome from metal surfaces. This article will…