Many individuals believe that the key to completing a CNC project lies in having a skilled machinist. While this holds some truth, it is not the whole picture. While an adept engineer with expertise in CNC machining is vital, they might simply proceed with assembling parts as listed in the datasheet, addressing issues one by one. While this is a viable strategy, it can be time-consuming and potentially more expensive than a systematic approach that anticipates potential issues. This approach is known as project management.
Understanding Project Management
At its core, project management entails utilizing resources and time efficiently while approaching each project systematically. This practice can be applied to nearly any industry or business sector, as saving resources, reducing costs, and increasing efficiency are universal goals. While this idea seems straightforward, how can we achieve these objectives? What are some project management examples specific to CNC prototyping projects? And how can project management help reduce CNC prototype costs? Let’s delve into these questions.
Implementing Project Management Techniques to Cut Costs
Project management relies on specialized techniques and approaches that enable project managers to decrease production time, improve quality, or reduce overall CNC machining costs. Let’s explore some key strategies:
Managing Manufacturing Workflow and Logistics
Project managers must have a clear understanding of how raw materials move through the production area, ultimately transforming into a final CNC prototype. It is particularly crucial to monitor individual parts or batches of parts in manufacturing systems. For instance, low-volume production shops often face multiple orders for different parts.
One project management example in this scenario involves determining the transfer batch. Let’s consider a specific manufacturing situation with two orders. Rather than manufacturing each order separately, it may be more efficient to focus on one order first and then proceed to the second order. However, what if there are three or more orders, some of which comprise single parts? Additionally, what if there is a bottleneck in the system, such as having only one grinding machine tool? Project managers utilize specialized diagrams to calculate transfer batches, identify critical paths (projects that cannot be postponed), and determine available time.
Logistics is another crucial consideration. For larger enterprises with limited electric carts, project managers aim to group batches according to CNC machining stages, optimizing cart loads and transportation efficiency.
By implementing these strategies, costs can be minimized, and project managers gain detailed time maps of ongoing projects, ensuring deadlines are met. Parts no longer sit idle, waiting to be transported for subsequent operations, resulting in reduced machining costs and time.
Effective Personnel Management and Outsourcing
Personnel management plays a pivotal role in lean production. Nowadays, personnel extends beyond the office or machine tools, thanks to digital technologies that allow for global hiring. The personnel of a company encompasses a diverse network of individuals accessible through the web. Lean project management necessitates considering these additional personnel. Identifying the most suitable person for a task is challenging and often requires an extensive network of suppliers and employees.
To save costs, project management services curate a list of individuals capable of performing tasks for the company. They identify suppliers who can provide the best service within the shortest timeframe. This streamlined approach ensures that the right people are assigned to each task, reducing errors and increasing overall efficiency.
Leveraging Enterprise Resource Planning (ERP) Systems
Enterprises, regardless of size, grapple with managing various resources. Tracking these resources poses a significant challenge. However, ERP systems, software tools designed for production management, offer a solution. These systems monitor the availability of materials, such as steels and stock diameters, in CNC machining production facilities. Consequently, production downtime caused by material or equipment shortages is minimized. Additionally, ERP systems provide insights into equipment utilization, distinguishing between idle and overloaded machinery.
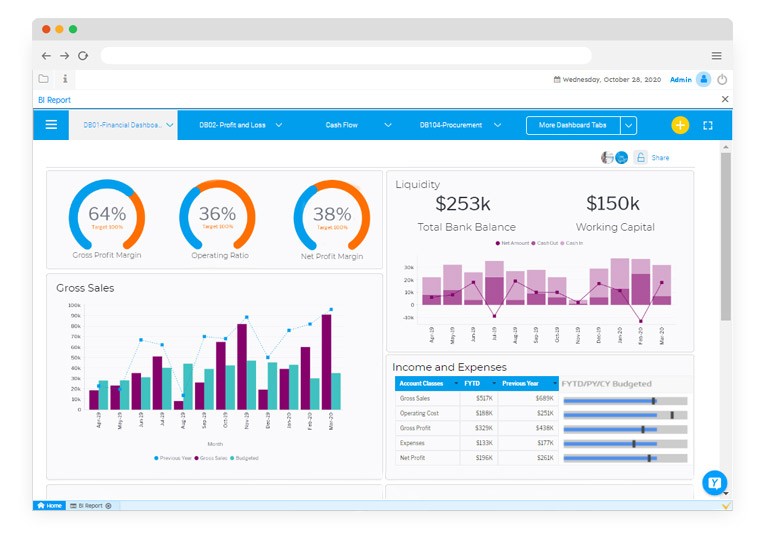
To save costs, projectmanagers can estimate the materials, cutting tools, and other supplies required for future projects. By planning orders in batches, they can minimize shipping expenses. Moreover, projects no longer need to wait for additional materials or tools to arrive before commencing production, resulting in increased efficiency and reduced costs.
Applying Product Lifecycle Management (PLM) for Project Development
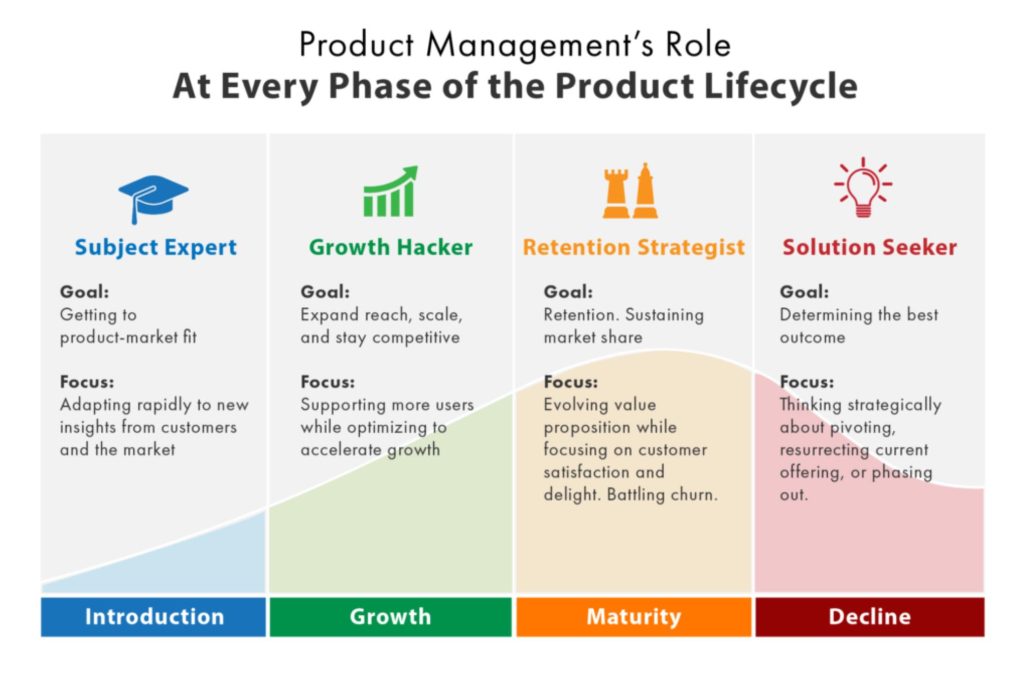
One highly effective approach to industrial project management is the implementation of PLM techniques. With the advent of digitalization, numerous software tools for design, manufacturing, and production planning have emerged. Traditionally, these tools and project development stages (such as R&D, engineering analysis, manufacturing, repairing, and recycling) were viewed as separate entities. However, PLM integrates all project stages, enabling early resolution of potential issues. For example, once the CAD model is developed, materials can be ordered even before the blueprints are finalized. Furthermore, PLM incorporates an integrated workflow that eliminates paper-based communication between departments, ensuring that project changes are instantly accessible to all involved.
To save costs, an integrated approach minimizes errors resulting from information transfer between departments. Automation streamlines menial tasks like creating bills of materials. Additionally, real-time monitoring enables project managers to track progress at any given moment.
Embracing Project Management for Cost Savings
By implementing project management techniques in CNC machining project development, companies can achieve significant cost savings. Optimizing manufacturing workflows, efficiently managing logistics, leveraging personnel resources, utilizing ERP systems, and integrating PLM methodologies all contribute to reducing production costs, improving efficiency, and meeting project deadlines. With careful planning and a systematic approach, project management becomes a powerful tool in maximizing resources and cutting expenses in CNC machining. By adopting these strategies, companies can gain a competitive edge in the industry while delivering high-quality CNC machining prototypes in a cost-effective manner.
Recommended Reads:
- 10 Tips and Tricks to Master CNC Mill Operation
- 7 Amazing Projects You Can Create with CNC Mills
- Top 5 Materials Best Suited for CNC Milling
- 10 Key Features of CNC Mills You Should Know
- Understanding CNC Software: 8 Must-Know Tools for Success
Other Articles You Might Enjoy
- CNC Turning: A Deep Dive into Rivet Production(cnc laser cutting Adolph)
Introduction:Computer numerical control (CNC) represents one of the most crucial inventions in manufacturing technology. It pertains to a method used to control an array of complex machinery using computer programs…
- CNC Turning: A Closer Look at Rivet Production(g code cnc Lester)
Computer Numeric Control (CNC) machining is a manufacturing process that has revolutionized the industrial sector, introducing precision and control in ways never before possible. CNC turning is one element of…
- Bronze Rivet Technology in CNC Machining
Bronze type that can process Rivet Phosphor Bronze Characteristics: High strength, excellent wear resistance, good elasticity. Applications: Springs, bearings, and parts requiring high wear resistance and elasticity. Tin Bronze Characteristics:…