In the field of CNC machining, understanding mechanical properties and stresses in materials is crucial for designing parts that can withstand operational loads without failure. One of the most critical concepts in this context is shear stress, which occurs when forces are applied parallel or tangential to a material’s surface. For engineers and machinists, knowing how to calculate and apply the shear stress formula is essential for designing components that are both strong and reliable.
In this guide, we will explore how to use the shear stress formula effectively in CNC design and production. We will cover the basics of shear stress, how to calculate it, and practical applications of these calculations in selecting materials, designing parts, and optimizing machining processes. Whether you are an experienced engineer or a CNC machinist, understanding shear stress can help you improve the quality and durability of the parts you produce.
What is Shear Stress?
Shear stress is defined as the force per unit area acting parallel to the plane of a material. It measures how much force causes a material to slide or shear along a particular plane. The most common application of shear stress analysis in CNC machining involves understanding how different parts behave under various operational forces, ensuring they do not fail during use.
1.1 Definition and Importance
Shear Stress (τ): It is expressed by the formula:
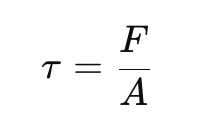
where:
- (τ ) = shear stress (measured in pascals or psi)
- ( F ) = applied force (measured in newtons or pounds-force)
- ( A ) = area over which the force is applied (measured in square meters or square inches)
Shear stress is crucial because many mechanical failures, such as material fractures and joint separations, occur due to shear forces. For CNC-machined components, understanding shear stress helps in designing parts that are resilient and can handle the loads they are exposed to during operation.
1.2 Types of Shear Stress in CNC Parts
- Direct Shear: Occurs when forces are applied directly to cause shearing, such as in rivets, bolts, and welded joints.
- Torsional Shear: Happens when a material is twisted, common in shafts and gears.
- Bending Shear: Results from forces causing a material to bend, which is important for beams and other structural components.
The Shear Stress Formula: Key Equations and Their Derivations
The shear stress formula is a straightforward calculation, but applying it correctly requires understanding the forces involved and the area over which they act. Here’s a detailed breakdown:
2.1 Basic Shear Stress Formula
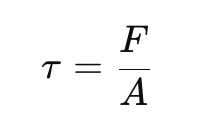
- ( F ): This is the shear force applied parallel to the surface.
- ( A ): The cross-sectional area where the force is acting.
2.2 Derivation and Application
The formula can be derived from the concept that stress is a measure of force distribution over an area. In CNC machining, you might encounter situations where multiple shear planes exist, such as in bolts securing two plates together. For such cases, the shear stress on each plane must be calculated separately.
2.3 Torsional Shear Stress
For components like shafts, the torsional shear stress is given by:
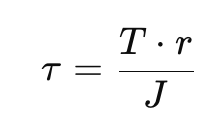
where:
- ( τ ) = shear stress
- ( T ) = applied torque
- ( r ) = radius of the shaft
- ( J ) = polar moment of inertia
This formula helps in determining how much twist a component can endure before failing.
2.4 Practical Calculation Example
Consider a bolt holding two plates together. If the shear force applied is 2000 N and the cross-sectional area of the bolt is 0.005 m², the shear stress would be:
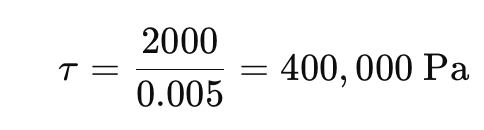
Applying Shear Stress Calculations in CNC Machining
Calculating shear stress is just the first step. Applying these calculations effectively can help in the design and production of CNC parts. Here’s how:
3.1 Material Selection Based on Shear Strength
When designing a part, it’s essential to choose a material that can handle the expected shear stress without failure. The shear strength of a material is the maximum stress it can withstand before failure. Here’s a table comparing the shear strengths of common materials:
Material | Shear Strength (MPa) | Common Applications |
---|---|---|
Aluminum (6061) | 207 | Gears, brackets |
Steel (A36) | 152 | Structural components, fasteners |
Stainless Steel (304) | 290 | High-stress mechanical parts |
Titanium (Grade 5) | 550 | Aerospace components, critical parts |
Brass | 138 | Decorative parts, connectors |
Selecting the right material can help ensure that the part does not fail under shear stress during operation.
3.2 Structural Design Considerations
In CNC design, engineers must consider how shear forces affect different parts. For example:
- Bolts and Fasteners: Must be designed to handle shear without snapping.
- Shafts and Gears: Should be robust enough to resist torsional shear.
- Welded Joints: Must be evaluated for potential shear failure to ensure safety.
3.3 Real-World Example: Designing a Shaft
Suppose you are designing a shaft for a motor. You need to ensure that the shaft can transmit torque without twisting beyond acceptable limits. By calculating torsional shear stress, you can determine the appropriate shaft diameter and material.
Factors Affecting Shear Stress in CNC Machined Parts
Shear stress in CNC parts can be influenced by several factors, and understanding these can help optimize the design and production process.
4.1 Material Type
Different materials have varying levels of shear strength. For example, metals like steel and titanium have higher shear strength than softer materials like aluminum or plastic.
4.2 Cutting Speed and Tool Angle
- High cutting speeds can introduce more shear forces, leading to potential deformation or failure if the part is not properly designed.
- Tool angle can also affect the direction and magnitude of shear forces. Adjusting the angle can help in achieving a smoother cut and reducing stress on the material.
4.3 Temperature and Environmental Conditions
High temperatures can weaken materials, reducing their shear strength. Consideration of operating conditions is essential during the design phase to ensure part longevity.
Factor | Impact on Shear Stress |
---|---|
Material Hardness | Harder materials resist shear better |
Cutting Speed | High speeds increase shear stress |
Tool Geometry | Proper angles reduce stress |
Temperature | High temps can lower shear strength |
Choosing the Right Materials Based on Shear Stress Analysis
5.1 Importance of Material Properties
Selecting the appropriate material is critical in preventing shear failure. Engineers need to consider not only the shear strength but also other properties like ductility, toughness, and resistance to environmental factors.
Material | Shear Strength (MPa) | Ductility | Heat Resistance |
---|---|---|---|
Aluminum (6061) | 207 | High | Moderate |
Stainless Steel (316) | 300 | Moderate | High |
Titanium (Grade 2) | 345 | Low | High |
Polycarbonate | 55 | Very High | Low |
Copper | 70 | Moderate | Moderate |
5.2 Practical Selection Tips
- High-Shear Applications: Use materials like titanium or stainless steel for parts that will be exposed to high shear forces.
- Lightweight Needs: For lighter components where shear is moderate, consider aluminum alloys.
- Cost Considerations: Balance between cost and performance. For instance, stainless steel offers high performance but at a higher cost compared to aluminum.
Shear Stress Analysis Tools for CNC Engineers
Several tools and software can assist engineers in accurately calculating and analyzing shear stress, making it easier to predict part behavior and optimize designs.
6.1 Popular Software for Shear Stress Analysis
- ANSYS: A powerful tool for finite element analysis (FEA) that can simulate stress, including shear forces, on complex geometries.
- SolidWorks Simulation: Useful for basic stress analysis, helping to determine the shear stress distribution across different parts.
- Autodesk Fusion 360: Integrates CAD and stress analysis, allowing real-time simulation and adjustment.
6.2 Benefits of Using Analysis Tools
- Accuracy: Allows precise calculation of shear stress, reducing the risk of part failure.
- Efficiency: Helps in designing parts faster by eliminating guesswork.
- **Cost Reduction**: Prevents overengineering by selecting the right material and geometry from the beginning.
Conclusion
Understanding how to calculate and apply shear stress formulas is fundamental to CNC design and production. It allows engineers to design parts that are durable, safe, and efficient, minimizing the risk of failure during operation. By considering material properties, design parameters, and machining conditions, engineers can optimize part performance, ensuring that components meet all operational requirements while also being cost-effective.
FAQ
- What is the difference between shear stress and tensile stress?
Shear stress occurs when forces are applied parallel to a material’s surface, causing it to slide or shear. Tensile stress, on the other hand, involves forces that pull materials apart, acting perpendicular to the surface. Understanding this difference is crucial because different materials and parts react differently to these types of stress, affecting their design and performance in CNC machining. - How do you use the shear stress formula to calculate the strength of parts with different geometries?
To calculate shear stress for parts with varying shapes, you can still use the basic formula (\tau = \frac{F}{A}), but it is essential to determine the correct cross-sectional area (A) where the force (F) is applied. For cylindrical parts like shafts, consider the area of the circular cross-section. For bolts or rivets, you might need to account for multiple shear planes if the part experiences forces at multiple contact points. - What are the common units used to measure shear stress in CNC machining?
Shear stress is typically measured in pascals (Pa) or megapascals (MPa) in the metric system. In the imperial system, it is commonly measured in pounds per square inch (psi). These units help quantify how much force per unit area a material can withstand before failing. - How do material properties like ductility and hardness affect shear stress calculations?
Ductility and hardness play a significant role in how materials behave under shear stress. Ductile materials, such as aluminum and copper, can absorb more shear deformation before failure, making them suitable for applications that require flexibility. Harder materials, like steel and titanium, can resist higher shear forces without deforming, but they may be more brittle, leading to a sudden failure if the shear limit is exceeded. - How can shear stress be minimized during the CNC machining process?
- To minimize shear stress during machining, engineers can adjust the cutting speed and feed rate, use sharp tools with the proper cutting angles, and employ coolants to reduce heat build-up. These measures help in reducing the stress concentration on the part and prevent potential issues like material deformation, tool breakage, or premature failure.
- What tools or software are best for performing shear stress analysis in CNC design?
Several software tools can help engineers perform accurate shear stress analysis. ANSYS and SolidWorks Simulation are popular for their finite element analysis (FEA) capabilities, which allow engineers to simulate stress, including shear, on complex geometries. Autodesk Fusion 360 also integrates CAD and stress analysis features, making it easier to perform real-time simulations and optimize designs accordingly. - How does cutting speed influence shear stress in CNC-machined parts?
Higher cutting speeds can lead to increased heat generation and potentially higher shear forces on the material being cut. If not managed properly, this can result in material deformation or premature tool wear. Reducing cutting speed or using coolants can help mitigate these effects, allowing for smoother cuts and lower shear stresses on the machined part. - How do you balance shear strength with other mechanical properties when selecting materials?
When selecting materials for CNC parts, it is important to balance shear strength with properties like tensile strength, ductility, corrosion resistance, and thermal stability. Engineers must evaluate the specific requirements of the part’s application, considering factors like operating environment, load types, and expected stress conditions. For instance, titanium might be chosen for its high shear strength and corrosion resistance, while aluminum could be selected for its lighter weight and sufficient shear strength for less demanding applications. - What are the typical failure modes related to shear stress in CNC-machined parts, and how can they be prevented?
Typical failure modes due to shear stress include shearing off (e.g., of bolts or fasteners), torsional failure in shafts, and delamination in composite materials. To prevent these failures, it is essential to ensure proper material selection, adequate cross-sectional area, and correct installation (for fasteners). Additionally, engineers should account for possible multiple shear planes and stress concentration points during design. - In designing CNC parts, what steps can be taken to prevent shear failure under operational loads?
To prevent shear failure, engineers should:- Select appropriate materials that can withstand the expected shear forces.
- Calculate accurate cross-sectional areas to determine proper dimensions for parts like bolts, shafts, and connectors.
- Optimize the design to distribute loads evenly and reduce stress concentrations.
- Use multiple fasteners if necessary to distribute the load and prevent overloading a single point.
- Test designs using simulation software to identify and address potential weak points before production.
Other Articles You Might Enjoy
- Analyzing Residual Stress in Aluminum Alloy CNC Machining Parts
Residual stress is a crucial factor affecting the performance and durability of aluminum alloy components in aerospace applications. These parts are often large, thin-walled, and complex in structure, making them…
- CNC Turning: A Deep Dive into Rivet Production(cnc laser cutting Adolph)
Introduction:Computer numerical control (CNC) represents one of the most crucial inventions in manufacturing technology. It pertains to a method used to control an array of complex machinery using computer programs…
- CNC Turning: A Closer Look at Rivet Production(g code cnc Lester)
Computer Numeric Control (CNC) machining is a manufacturing process that has revolutionized the industrial sector, introducing precision and control in ways never before possible. CNC turning is one element of…
- Breaking Down Design and Production Barriers: A Multidimensional Analysis of CNC Machining Part Drawings
CNC machining is a marvel of modern engineering, enabling the production of intricate parts with high precision. But behind every perfectly crafted piece lies the unsung hero of the process:…
- Flange Production Mastery with China's CNC Services
Exploring the Landscape of Flange Production in China China cnc machining service is developing very rapidly and have become an important force in global CNC processing services. Especially in the…
- Reducing Manufacturing Costs with Multi-Material CNC Machining Strategies
Introduction to Manufacturing Costs and CNC Machining Solutions Manufacturing costs significantly impact businesses, encompassing expenses related to materials, labor, and operations. These costs determine the final price of products, affecting…