Cast Iron is a ferrous alloy primarily composed of iron, carbon (typically between 2% and 4%), and silicon (1% to 3%). Its unique properties such as high wear resistance, excellent thermal conductivity, and vibration-damping capacity make it a staple material in manufacturing and construction industries. Cast iron is characterized by its microstructure, with carbon existing in the form of graphite, which influences its mechanical properties. Custom Machining techniques allow manufacturers to tailor cast iron components to precise specifications, ensuring optimal performance in specialized applications. As a widely used metal, cast iron provides a balance of strength, durability, and cost-effectiveness, making it indispensable in many industrial sectors. This material is widely utilized for engine blocks, machine tool components, pipes, and cookware due to its durability and cost-efficiency. Despite its brittleness compared to steel, cast iron offers unparalleled strength in compressive loads, making it ideal for applications involving high-pressure environments. Many CNC machined parts made from cast iron benefit from its excellent stability and resistance to deformation, making it a preferred choice for precision engineering projects. Its machinability, though varied by subtype, is another key reason for its widespread adoption in CNC machining.
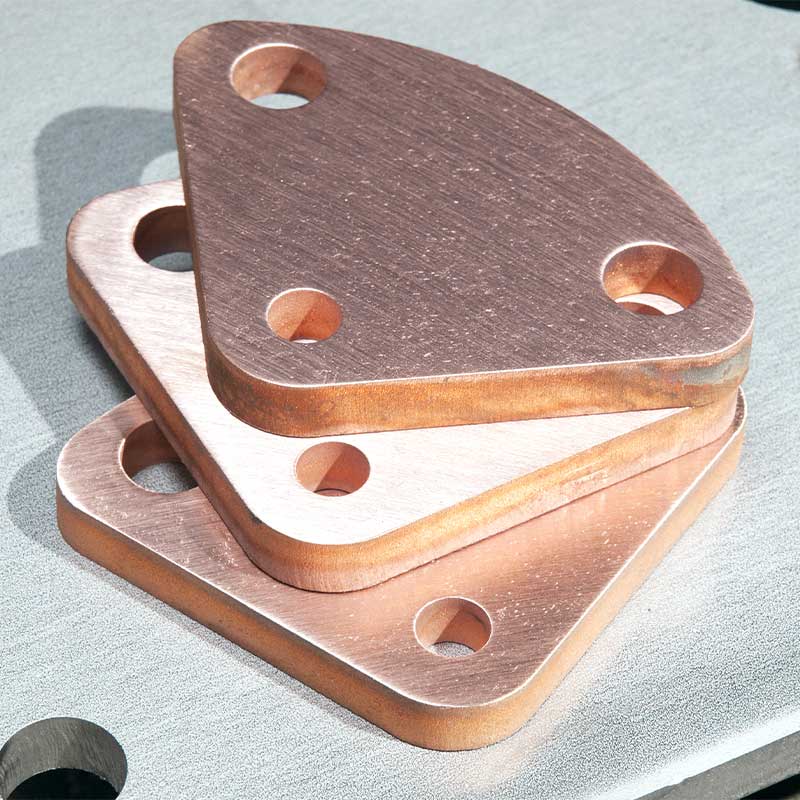