Nylon is an engineering plastic known for its high strength, wear resistance, and chemical inertness. It possesses excellent mechanical properties and durability, making it widely used in various fields including mechanical parts, automotive components, electronics, and sports equipment.Nylon CNC machining finds extensive applications in automotive parts (e.g., brake system components, transmission parts), mechanical parts (e.g., bearings, gears), electronic enclosures, industrial components, aerospace parts, etc.
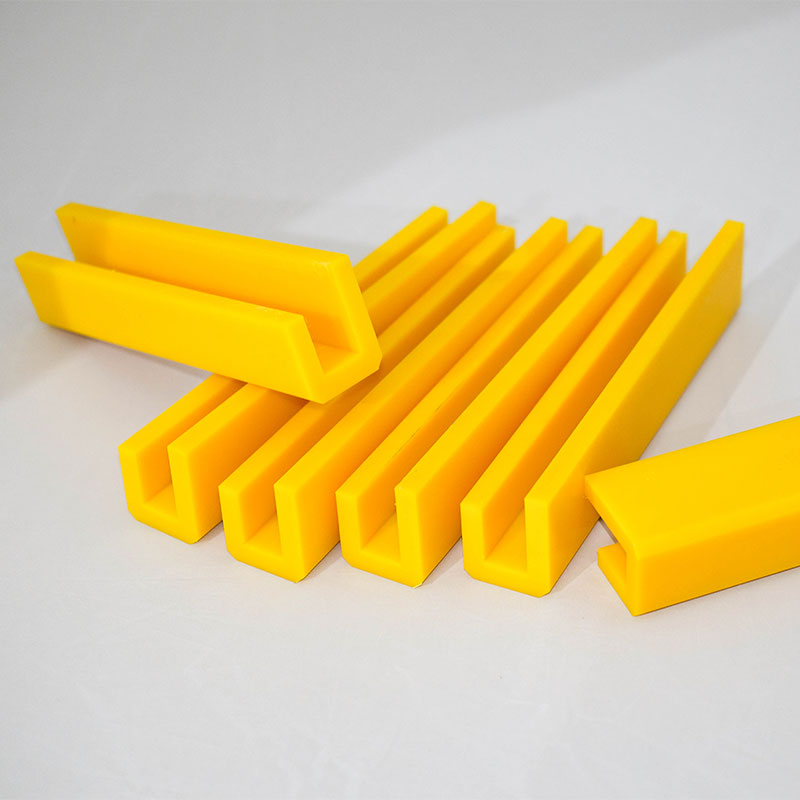
Nylon Advantages and Limitations
Nylon material offers good wear resistance, corrosion resistance, and chemical resistance, making it suitable for use in certain specialized environments. However, compared to metals, nylon exhibits slightly lower strength and stiffness, which may limit its suitability under high loads, temperatures, or pressures.
The methods involved in Nylon CNC machining typically include the following steps:
- Design: Begin by designing the part or component using computer-aided design (CAD) software. This step involves creating a detailed digital model of the part, specifying dimensions, tolerances, and surface finishes.
- Programming: Once the design is complete, the next step is to program the CNC machine. This involves translating the design specifications into machine-readable instructions (G-code). The programmer determines the toolpaths, cutting parameters, tool changes, and other machining parameters based on the part geometry and material properties.
- Material Preparation: Prepare the Nylon material for machining. This may involve securing the material to the CNC machine’s worktable using clamps, vises, or other workholding devices. Ensure that the material is flat, stable, and properly aligned to prevent errors during machining.
- Tool Selection: Select appropriate cutting tools for the machining operation. For Nylon, carbide or high-speed steel (HSS) tools are commonly used due to their ability to withstand the material’s abrasiveness. The tools should be sharp and properly sized for the desired cuts.
- Machining Operations: Execute the programmed toolpaths on the CNC machine. This typically involves a series of cutting, drilling, milling, and other operations to shape the Nylon material according to the design specifications. Monitor the machining process closely to ensure accuracy and quality.
- Quality Control: After machining, inspect the finished parts to ensure they meet the required tolerances, surface finishes, and dimensional accuracy. Use precision measuring tools such as calipers, micrometers, and gauges to verify part dimensions.
- Finishing Operations: Depending on the application and requirements, finishing operations such as deburring, sanding, polishing, or surface treatments may be performed to improve the part’s appearance, functionality, or performance.
Nylon CNC machining Advantages and Limitations
Nylon material offers good wear resistance, corrosion resistance, and chemical resistance, making it suitable for use in certain specialized environments. However, compared to metals, nylon exhibits slightly lower strength and stiffness, which may limit its suitability under high loads, temperatures, or pressures.
Nylon can be machined using CNC processes to produce parts with complex shapes, such as cutting, drilling, milling, etc. During machining, considerations need to be made for the thermal sensitivity of nylon, and appropriate machining parameters and process controls should be implemented to prevent overheating and material damage or deformation.
Common types of nylon that can be used for CNC machining
- Nylon 6: This is one of the most common types of nylon, known for its good strength, stiffness, and wear resistance. It’s suitable for machining many general mechanical parts such as bearings, gears, and washers.
- Nylon 66: Nylon 66 offers higher heat stability and rigidity compared to Nylon 6. It also boasts good wear resistance and chemical resistance, making it suitable for applications requiring higher temperatures and mechanical performance, such as automotive engine parts and industrial components.
- Glass-Filled Nylon: This type of nylon incorporates glass fiber reinforcement, providing it with higher strength and stiffness. It’s commonly used for parts requiring greater strength and wear resistance, such as mechanical and engineering components.
- Carbon-Filled Nylon: Similarly, carbon-filled nylon offers increased strength and stiffness. It also has a lower coefficient of thermal expansion, making it suitable for applications in high-temperature environments, such as aerospace components and automotive engine parts.
- Conductive Nylon: Conductive nylon contains conductive materials, giving it excellent electrical conductivity. It’s suitable for applications requiring electrostatic discharge protection or electrical conductivity, such as electronic product housings and static-sensitive components.
Nylon CNC Machining Service for Custom Parts
Are you in need of precision-engineered custom parts made from Nylon? Look no further! Our Nylon CNC machining service offers high-quality solutions tailored to your exact specifications.
Why Choose Us?
- Precision Machining: Our state-of-the-art CNC machines ensure precise cutting, drilling, and milling of Nylon material, guaranteeing accuracy and consistency in every part we produce.
- Customization: Whether you require complex shapes, intricate designs, or specific dimensions, we have the expertise to bring your ideas to life. Our team works closely with you to understand your requirements and deliver custom solutions that meet your needs.
- Quality Assurance: We adhere to strict quality control measures throughout the machining process to ensure that each part meets the highest standards of quality and performance. You can trust us to deliver reliable and durable custom Nylon parts.
- Fast Turnaround: With our efficient manufacturing processes and dedicated team, we offer fast turnaround times without compromising on quality. Whether you need prototypes or production runs, we can accommodate your timeline requirements.
- Competitive Pricing: We offer competitive pricing for our Nylon CNC machining services, providing cost-effective solutions for your custom part manufacturing needs.
Our Capabilities:
- CNC milling and turning
- Drilling and tapping
- Surface finishing options
- Prototyping and production runs
Applications:
Our Nylon CNC machining services are suitable for various industries and applications, including automotive, aerospace, electronics, medical devices, and more. Whether you need Nylon parts for mechanical components, electrical enclosures, or specialized equipment, we have the expertise to deliver.
Get in Touch:
Ready to discuss your custom Nylon machining needs? Contact us today to learn more about our services and how we can help bring your projects to fruition. Let us be your trusted partner for precision-engineered Nylon parts!
Other Articles You Might Enjoy
- Aluminum CNC Machining Service for Custom Parts
Aluminum CNC machining stands at the forefront of modern manufacturing, epitomizing precision, versatility, and efficiency. With its widespread applications across industries ranging from aerospace to automotive and beyond, aluminum CNC…
- CNC Machining Plastics: Delrin vs. Nylon for High-Precision Parts
Introduction to CNC Machining Plastics The Computer Numerical Control (CNC) machining process plays a vital role in manufacturing various high-precision parts and components. This advanced technology uses pre-programmed computer software…
- 10 Advantages of CNC Machining for Custom Parts
CNC machining services produce high-quality parts with accuracy and efficient production. These CNC machines use computer numerical control machining tools to cut and shape materials precisely. Additionally, CNC machining services…