Best Custom Sheet Metal Fabrication
Looking for metal fabricators for your custom metal parts or prototypes? Save cost and time with Want.net’s precision sheet metal fabrication service today! Click to get a free quote now!
- Instant Quote
- Fast Turnaround
- Pay After Delivery
- All uploads are secure and confidential
Premium Metal Fabrication Service Trusted by
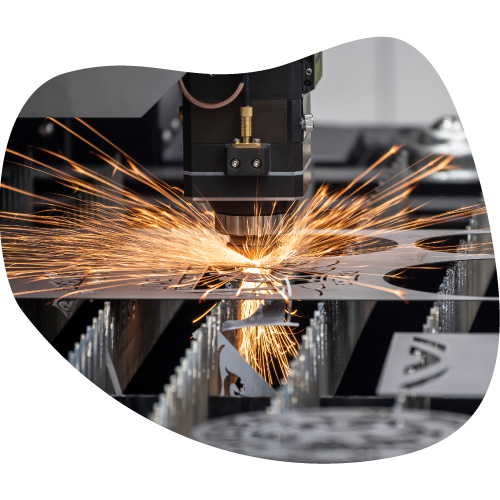
Work with The Best Sheet Metal Fabricators
In the past decade, we have built a network of more than hundreds of sheet metal fabricators in China. We optimize the ordering process from quoting to delivery, stock the materials in huge quantities before our customer orders, and regularly review the quality of the metal fabricators within our network. All of these have been helping us to deliver the most reliable sheet metal fabrication service at the most competitive price. With Want.net, you can rest assured that your order will only be produced by the best sheet metal fabricators. Click the button below to get a quote now!
Get Your Custom Sheet Metal Parts Online Easily
Ordering your custom metal parts is always easy with Want.net. All you need to do is get a free instant quote from us by uploading your 3D files and project requirements. Want.net will take care of all the rest, from fabricating, inspection, to delivery. With our ISO9001:2015 certificated sheet metal fabricator network, you can rest assured that the custom metal parts you get from us will always exceed your expectation.
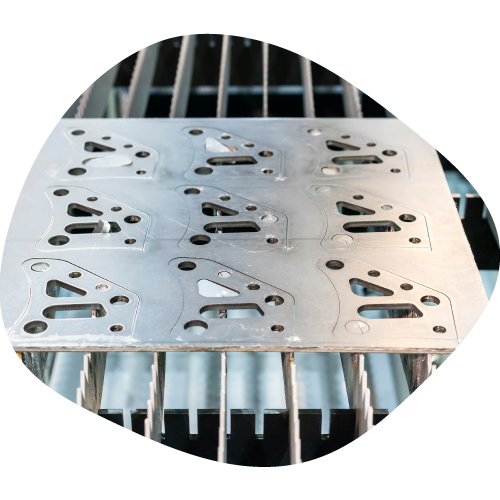
Available Sheet Metal Fabrication Processes
We offer the full range of sheet metal fabrication processes that are necessary to complete your metal parts or prototypes.
Laser Cutting
Utilizing a high-powered laser, Laser cutting can cut all types of metals, from steel to stainless and also non-ferrous metals.
Plasma Cutting
Plasma cutting is a thermal cutting method where ionised gas is used for cutting the metal. It is one of the most widely used techniques to cut thick metal plates and sheet metal.
Waterjet Cutting
Water Jet It is the preferred method when the materials being cut are sensitive to the high temperatures generated by other methods.
Bending
The sheet metal bending process involves applying a force to a sheet metal part to change its geometry.
Standard Tolerances for Sheet Metal Fabricating
The sheet metal fabrication tolerance can be defined as a deviation from original dimensions which may have important results on the performance of the metal parts or prototypes. Over-toleration of particular dimensions may cause the metal part to fail in complying with design and performance needs later in its operational life cycle. To ensure part manufacturability and precision of fabricated prototypes and parts, our custom sheet metal fabrication services are in compliance with the ISO 2768-m.
Discover The Amazing World Of Sheet Metal Fabrication
Sheet metal fabrication is a manufacturing method using cutting and bending sheets of metal, steel, stainless steel or aluminum, to transform them into products for different purposes. It’s widely used to produce boxes, metal cabinets, facade panels, garden containers or even store shelves. Sheet metal fabrication is also suitable for producing prototypes due to it’s low-cost, flexible, and fast lead time. The few application
Why Choose Our Sheet Metal Fabrication Service
Best Custom Sheet Fabrication Services In China
What is Sheet Metal Fabrication?
The process of fabricating flat sheet metal involves using a range of tools and equipment, such as punch presses, brake presses, shearing machines, and lasers, to shape the metal into the desired parts or products.
It requires several procedures including cutting, bending, shaping, and welding to create a finished product.
Sheet metal fabrication is widely utilized in products requiring accurate and consistent parts, such as airplanes, hospital instruments, and industrial equipment.
How Does Sheet Metal Fabrication Work?
The process of molding and shaping a metal sheet into a desired form is known as sheet metal fabrication. This is typically accomplished by shaping the metal through cutting, bending, and assembly. The most popular fabrication techniques include folding, shearing, punching, and welding.
The first step in the procedure is choosing the right kind and thickness of metal sheet for the particular use. The parts are first cut to size and then manually or mechanically molded into the necessary shapes after the metal has been chosen.
The final shape may be created by welding several sections together, based on the complexity of the design. The metal is then painted or coated with a protective finish after the final shape has been attained.
Metal Fabrication Process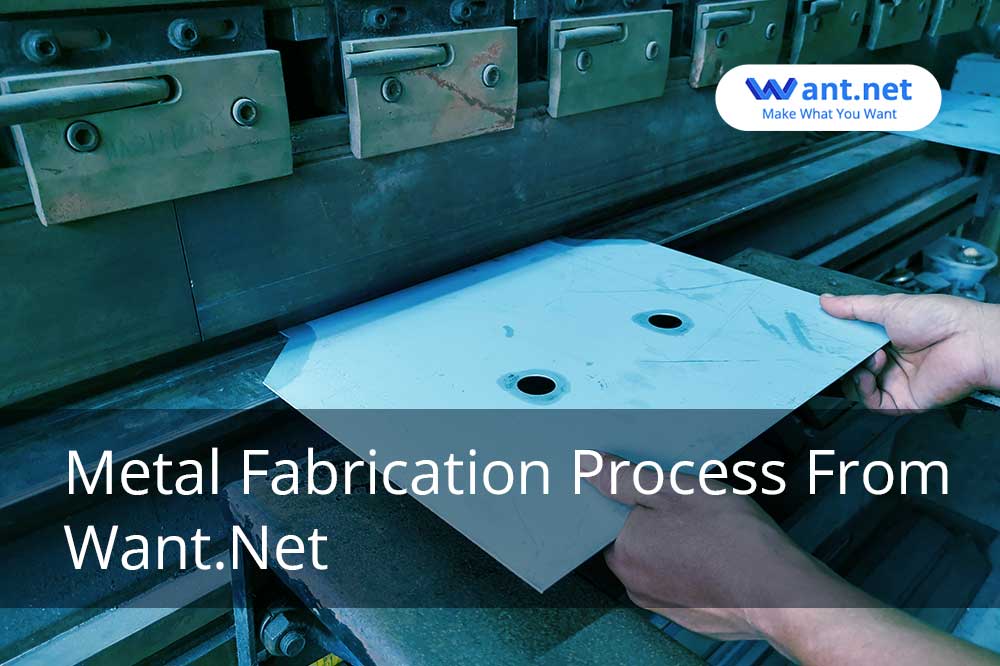
- Cutting: Cutting is performed as the initial stage of sheet metal manufacture. Typically, a cutting tool like a laser, waterjet, or plasma cutter is used for this. The sheet metal can be cut into forms or patterns with this cutting technique.
- Forming: Forming is the next step. A press brake is used to bend the sheet metal into the required shape.
- Welding: The final phase involves welding the sheet metal together to form the final product. You can do this by hand, with a MIG welder, or with a TIG welder.
- Finishing: The final step is completed. To give the sheet metal a finished look, this may entail polishing, painting, or powder coating.
Sheet Metal Surface Finishes
The surface finish of sheet metal plays a decisive role in custom metal manufacturing parts. It has an excellent impact on a range of elements, including the product’s visual appeal and performance in different contexts.
A more textured surface finish can offer better grip, wear resistance, and corrosion resistance, while a smooth surface finish is often preferred for aesthetic reasons.
In this article, we’ll look at the various surface finishes that are used in sheet metal manufacturing and their advantages.
- Anodizing: Anodizing is a technique that coats the top of the sheet metal with a protective oxide layer. This method has the potential to produce a wide range of colors, textures, and finishes. Aluminum parts are frequently anodized because it offers excellent corrosion protection, wear resistance, or aesthetics.
- Powder Coating: The surface of the sheet metal is coated with powdered paint during the dry finishing process known as powder coating. This method is frequently applied to produce a finish that is robust, homogeneous, and aesthetically beautiful. A spray gun can be used to apply the powder, which is then heated to fix it.
- Painting: Painting is a popular finishing technique used to enhance the appearance of sheet metal objects. In this method, liquid paint is put on the sheet metal’s surface and then dried. Painting can be done with a variety of colors and textures and is frequently used to create a smooth finish.
- Polishing: Polishing is a procedure that is performed on sheet metal to achieve a smooth and shiny surface. This method can provide a range of finishes, from high-gloss to matte. The body of the sheet metal can be polished to remove blemishes like scratches and other flaws.
- Sand Blasting: Sandblasting is a technique used to give the sheet metal’s surface a matte appearance. The surface of the sheet metal is removed during this operation using a spray of abrasives, such as sand. Many different textures and finishes can be produced with sandblasting.
- Laser Etching: Laser etching is a technique used to generate an accurate and complex design on the top of sheet metal. In this method, a laser is used to etch or carve a design into the sheet metal’s surface. Laser etching can create writing, logos, or other complicated designs on the surface of sheet metal.
- Plating: A protective layer is applied to the surface of the sheet metal by the plating process. This procedure can be used to increase corrosion resistance, as well as to produce a range of colors and finishes. Plating is frequently used to give sheet metal a shiny, reflecting polish.
Top Sheet Metal Fabrication Advantages
- Cost-Effective: Sheet metal fabrication is a low-cost manufacturing method for producing high-quality products. It is less expensive than other methods since it uses fewer resources and labor.
- Highly Versatile: Sheet metal fabrication is used to fabricate a variety of components and parts like enclosures, boxes, ducts, and other specific parts.
- Durable: Sheet metal parts and components are efficient, robust, and corrosion-resistant, making them perfect for use in applications requiring strength and longevity.
- Quick Turnaround: Sheet metal fabrication is a quick method that allows for quicker turnaround times than some other processes.
- Automation-Ready:
- Automation and sheet metal manufacturing work very well together, resulting in quicker turnaround times and more productivity.
Sheet Metal Applications
Sheet metal is a thin, flat piece of metal. It is a type of metal that is among the most useful and popular. Sheet metal is applied in a wide range of applications, including automotive body panels and airplane wings, as well as medical devices and household appliances.
Additionally, it is used as decoration in items like jewelry and artwork.
- Automotive: Sheet metal is widely used in the automotive sector, from hoods and fenders to body panels and bumpers. Additionally, it is utilized in exhaust systems and fuel tank linings.
- Aerospace: Sheet metal is used to make the fuselage, wings, tail sections, and landing gear of airplanes and spacecraft. Additionally, it is used for rocket engine components and fuel tank linings.
- Architectural: Sheet metal is widely used in the process of building structures, including siding, gutters, and roofing panels. It is also utilized in metal artworks and decorative pieces.
- Industrial: Sheet metal has many industrial uses, including shelving and storage containers as well as pipe fittings and machine parts. Additionally, it is used in commercial ventilation and ductwork systems.
- Marine: Sheet metal is used to build hulls, bulkheads, decking, and furniture for boats and ships. Additionally, it is used in exhaust systems and fuel tank linings.
- Electrical: Sheet metal is used to build everything from electrical enclosures and switches to circuit boards and wiring. Additionally, it is very useful for grounding and shielding.
Sheet Metal Cutting Types
- Punching: Punching is a cutting technique that involves applying a strong enough shearing force to a sheet of metal to remove material from it. To make holes, louvers, and other patterns in sheet metal, punching is used.
- Shearing: Shearing is a straight-line cutting technique that uses two blades to cut sheet metal. Sheet metal is frequently cut using this method into long, straight sections.
- Laser Cutting: A laser beam is used in the laser cutting procedure to cut sheet metal. This method can create intricate shapes and holes.
- Waterjet Cutting: This technique involves cutting the sheet metal with a stream of pressurized water. This method can create intricate shapes and holes and is quite accurate.
- Plasma Cutting: In plasma cutting, the sheet metal is cut using an electric arc. This technique is extremely precise and can create complex patterns and holes.
Frequently Asked Questions
Custom sheet metal fabrication services come with some rigorous processes including bending, cutting, and assembling to make customized metal products.
Sheet metal fabrication can be expensive if you choose an unprofessional company with little experience. By contacting an experienced manufacturer for custom parts, you can reduce the cost of metal parts with professional guidance about material, design, and surface finishes options.
As we have mentioned above, fabrication carries cutting, bending, and assembling materials to create a product. On the other hand, sheet metal is a thin material that is used to process custom metal parts.
Put Your Sheet Metal Parts into Production Today!
You’re one-step away from the most affordable sheet metal fabrication service. Fill the form beside and we will get back to you within 24 hours.
GET QUICK QUOTE
- All uploads are secure and confidential