In today’s fast-paced manufacturing industry, Computer-Aided Manufacturing (CAM) acts as a bridge between design and production, enabling manufacturers to translate their digital designs into precise and efficient machine instructions. One of the key advantages of CAM software is its ability to achieve exceptional precision in CNC machining. The software utilizes sophisticated algorithms to calculate tool paths, taking into account factors such as material properties, cutting tools, and machine capabilities. This precision-driven approach minimizes errors, eliminates guesswork, and ensures the accurate reproduction of complex designs with utmost detail and quality. This article explores the significance of CAM software in CNC machining and how it enhances productivity and precision.
#1: Intuitive User Interface
An intuitive user interface allows operators to navigate through the software effortlessly. With easy access to tools, menus, and commands, operators can quickly define machining parameters and perform tasks efficiently. This streamlined workflow leads to increased productivity and faster turnaround times.
CAM software with a user-friendly interface also helps minimize errors caused by operator confusion or misunderstanding. Clear and logical menu structures, intuitive icons, and tooltips provide operators with the necessary guidance, reducing the likelihood of mistakes during the programming and machining process.
Recommended Read: 4 Must-Know CAM Software for CNC Machining
#2: Powerful Toolpath Generation
Toolpath generation refers to the process of generating a sequence of instructions that guide the CNC machine’s cutting tool along the desired path to create a part. The toolpath includes information about the cutting tool’s position, speed, feed rate, and other relevant parameters. It is an essential step in the CNC machining workflow, as it determines how efficiently and accurately the machine can produce the desired part.
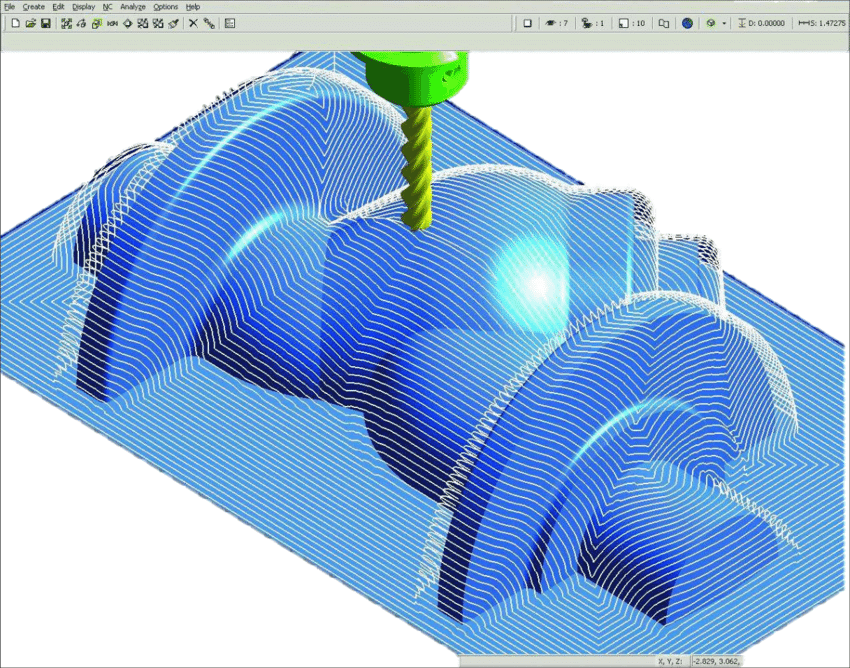
An efficient toolpath ensures optimal material removal, minimizing machining time and reducing tool wear. By intelligently planning the tool’s movements, unnecessary retractions, sharp corners, and redundant tool paths can be avoided, resulting in smoother and more consistent cutting operations. A well-optimized toolpath can also enhance the surface finish of the machined part. By minimizing abrupt changes in cutting direction and strategically planning tool entry and exit points, tool marks, surface imperfections, and vibrations can be minimized, leading to higher-quality finished parts.
Recommended Read: The 5-Step Guide to Mastering CAM in CNC Machining
# 3: Comprehensive Tool Library
A tool library is a digital repository within CAM software that stores information about various cutting tools, including their geometries, dimensions, materials, and performance characteristics. It serves as a centralized database where users can access and manage information about the tools they use for specific machining operations.
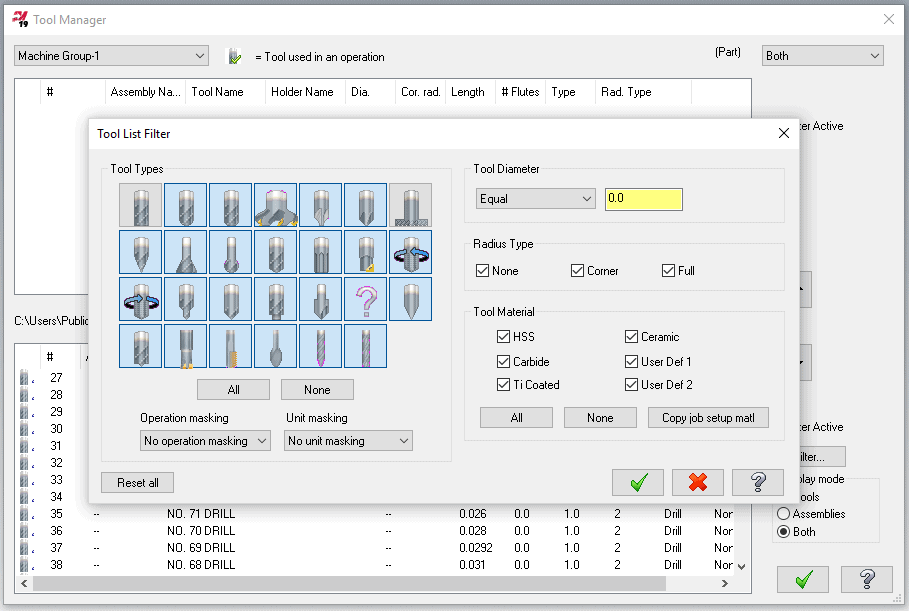
By providing a centralized repository, tool libraries facilitate standardization and consistency in tool selection and usage. This ensures that operators across different machining processes and projects can access the same set of tools, leading to uniformity in manufacturing practices. A tool library allows users to quickly search and select appropriate tools for specific machining operations. Instead of manually inputting tool data each time, operators can choose from a pre-defined list of tools, saving time and reducing the chance of errors.
Tool libraries also enable efficient management and organization of tools. You can categorize tools based on types, manufacturers, and parameters, making it easier to locate and track the lifecycle of each tool, including usage history, maintenance schedules, and tool life expectancy.
# 4: Simulation and Visualization
Simulation in CAM refers to the virtual representation of the machining process, where the tool path, material removal, and other machining parameters are digitally simulated. Visualization, on the other hand, involves presenting the simulated machining process in a graphical or interactive manner, allowing users to see and understand the sequence of operations and potential outcomes.
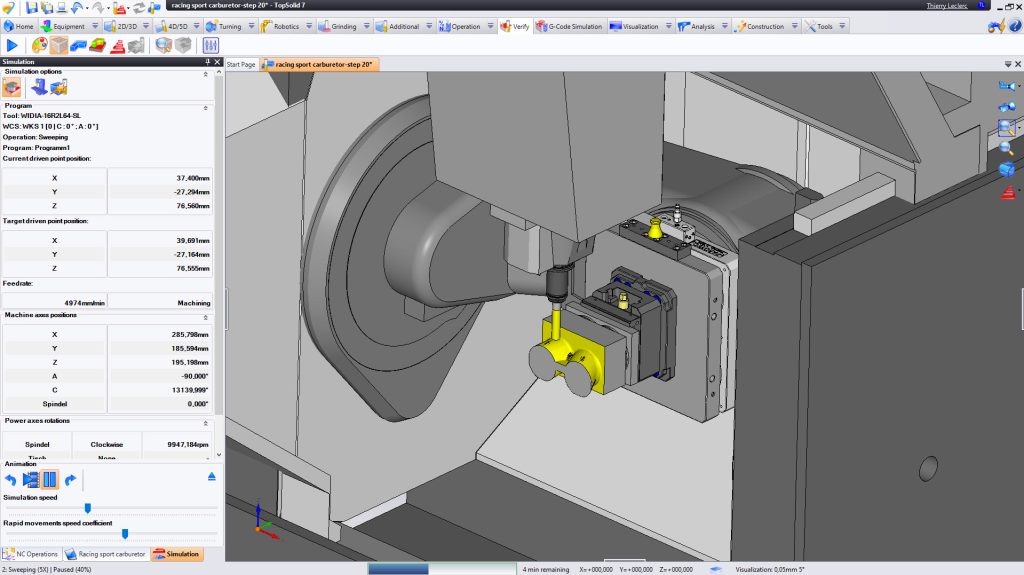
Simulation helps identify potential errors or collisions that may occur during the machining process. By simulating the tool movements and interactions with the workpiece, users can detect and resolve any issues before executing the program on the actual machine. This minimizes the risk of machine damage, tool breakage, and scrap parts. Simulation allows users to test and optimize machining parameters such as feed rates, spindle speeds, and tool engagement. By evaluating different scenarios virtually, operators can fine-tune the parameters to achieve the desired results in terms of surface finish, material removal rate, and tool life.
# 5: Multi-Axis Machining Support
Traditional CNC machining is often limited to three primary axes: X, Y, and Z. However, many complex parts and geometries require movements along additional rotational or tilting axes to achieve the desired shapes and contours. Multi-axis machining offers the flexibility to create intricate and sophisticated components that cannot be easily produced with conventional three-axis machining.
Certain parts, such as impellers, turbine blades, and molds, feature complex shapes that require simultaneous movement along multiple axes to achieve the desired contours and surface finishes. Multi-axis machining enables the creation of intricate details and complex geometries with higher precision. With multi-axis support, CAM software allows for the machining of highly complex geometries that would be challenging or impossible to produce with traditional three-axis machining. The additional axes enable the tool to approach the workpiece from various angles, facilitating the creation of intricate shapes and features.
Multi-axis machining support enables smoother and more consistent tool paths, resulting in improved surface finish on the machined parts. By continuously adjusting the tool orientation during the machining process, CAM software ensures that the tool engages with the workpiece optimally, minimizing tool marks and surface imperfections.
# 6: Adaptive Machining Technology
Adaptive machining is a proactive approach that adapts the machining process to the specific conditions encountered during operation. Traditional machining strategies rely on pre-determined parameters, such as cutting speeds and feeds, that are set before the machining begins. In contrast, adaptive machining uses sensor feedback, real-time data, and advanced algorithms to continuously monitor and adjust machining parameters during the process.
CAM software with adaptive capabilities can make precise adjustments to the cutting parameters based on factors such as tool wear, material variances, workpiece deformation, and cutting forces. By continuously monitoring and analyzing these variables, the software can optimize the machining process, ensuring optimal tool performance, improved surface finish, and reduced cycle times.
# 7: Post-Processing Capabilities
Post-processing plays a crucial role in CNC machining, as it bridges the gap between the virtual programming environment and the physical machining process. CAM software with robust post-processing capabilities offers a range of tools and options to convert the generated toolpaths into machine-specific instructions. After generating the toolpaths, the CAM software needs to translate them into a format that the specific CNC machine can understand. This process is known as post-processing. Post-processing takes into account the machine’s kinematics, controller capabilities, tooling, and other machine-specific parameters to generate the appropriate G-code or machine instructions.
Accurate post-processing ensures that the machine follows the intended toolpath, properly interprets the cutting parameters, and handles any machine-specific nuances or requirements. Proper post-processing minimizes errors, reduces the risk of collisions, and maximizes the machine’s performance.
# 8: Integration with CAD Systems
CAM software that seamlessly integrates with CAD systems allows for a smooth and efficient transition from the design phase to the manufacturing phase. The integration ensures that the manufacturing data, such as part geometry, dimensions, and features, is accurately transferred from the CAD model to the CAM software. This eliminates the need for manual re-entry of data, reducing errors and saving valuable time.
Furthermore, seamless integration enables real-time collaboration and information exchange between designers and machinists. Machinists can easily access the CAD models and associated data, allowing them to make informed decisions during the programming and machining stages. This integration fosters a more cohesive and streamlined workflow, improving overall productivity and reducing potential communication gaps between design and manufacturing teams.
Other Articles You Might Enjoy
- 4 Must-Know CAM Software for CNC Machining
CAM, which stands for Computer-Aided Manufacturing, is a special kind of software that helps bridge the gap between design and the actual production of physical objects. It works hand in…
- Precision CNC Machining of Steel: High-Volume Production
Precision CNC Machining and High-Volume Production As an integral part of modern manufacturing processes, Precision Computer Numerical Control (CNC) machining brings about unmatched accuracy and consistency in the production of…
- Revolutionizing CNC Machining for the Future of Smart Wearables
Introduction: CNC Machining and Smart Wearables CNC (Computer Numerical Control) machining is a manufacturing process that utilizes computerized controls to operate and manipulate machine tools, converting raw materials into finished…