CNC machines have revolutionized the manufacturing industry with their ability to perform a wide range of CNC machining procedures accurately and efficiently. One of the key factors that contribute to their versatility is the availability of various types of CNC machine tools. These tools possess unique properties that make them suitable for different operations while reducing the need for manual intervention. In this comprehensive guide, we will explore the different types of CNC machine tools, their functions, the materials used in their construction, common tool coatings, and factors to consider when selecting the right tool for your machining needs.
CNC Turning Tools
Turning, an ancient machining procedure dating back to the Egyptian empire, remains an integral part of CNC machining. CNC turning tools are used in conjunction with a lathe, a turning machine that rotates the workpiece at high speeds while the turning tool shapes it according to the programmed specifications. The type of turning procedure and tool employed determines the final shape of the workpiece. Let’s take a closer look at some common types of turning tools:
Boring Tools
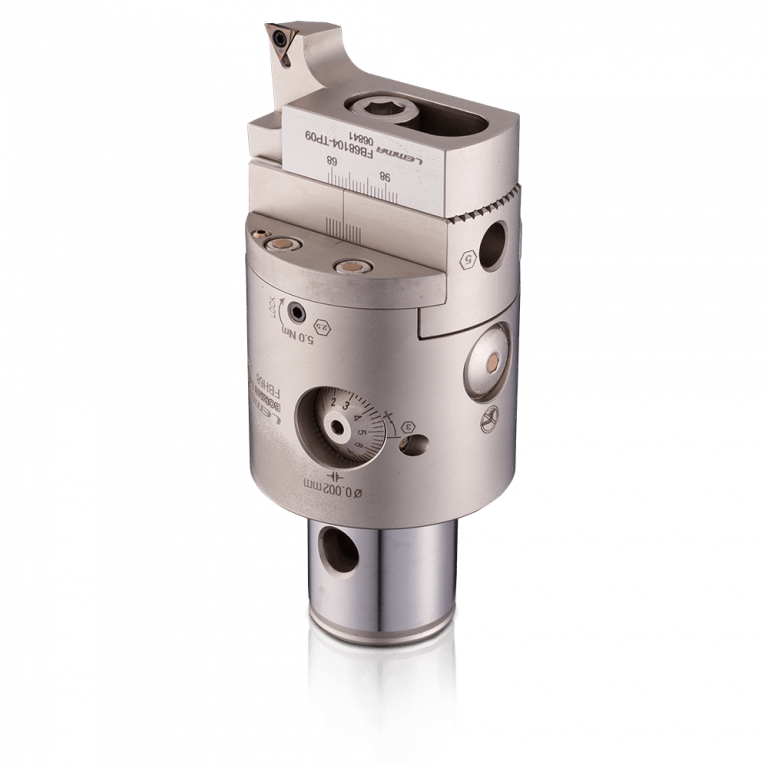
Boring tools work in collaboration with the lathe to enlarge existing straight or tapered holes in the workpiece. They are crucial for achieving precise dimensions and smooth finishes.
Chamfering Tools
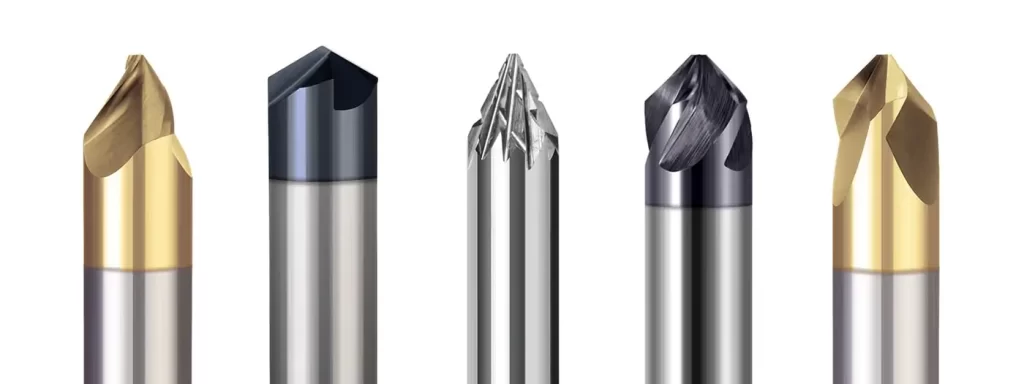
Machinists employ chamfering tools for various applications, such as deburring, removing sharp edges, and beveling workpieces. Chamfering tools create angled surfaces or beveled edges, enhancing the aesthetic appeal and functionality of the workpiece.
Knurling Tools
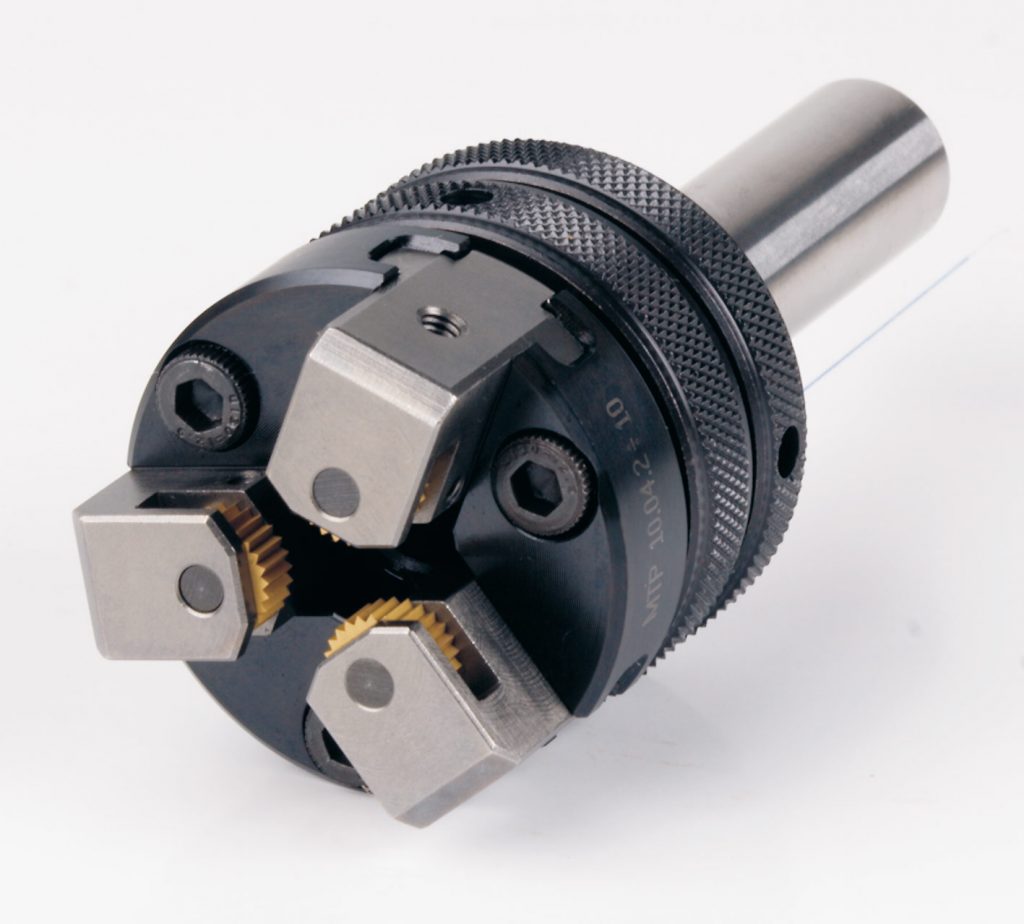
Knurling tools create patterns (diagonal, straight, or diamond) on the surface of workpieces. These patterns serve as a source of better grip and improved functionality for the finished part. Knurling tools are commonly used in applications where a firm grip is essential.
Parting Tools
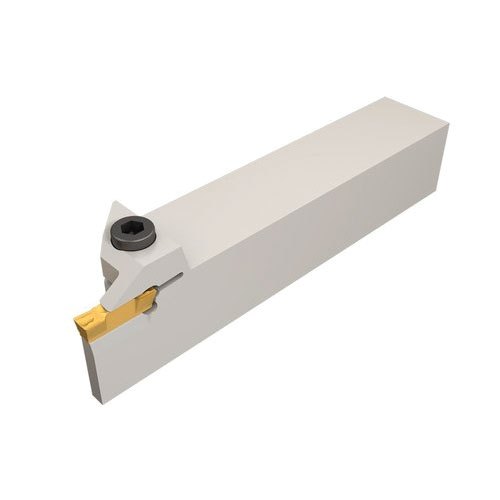
Parting tools have a blade-like edge that cuts materials away from the workpiece. They are used to separate the finished part from the rest of the workpiece, enabling efficient production and reducing material wastage.
CNC Cutting Tools (CNC Milling Tools)
Among the different types of CNC machine tools, cutting tools take the center stage due to their extensive usage in the CNC industry. Although referred to as cutting tools, they are primarily used for the CNC milling procedure, which involves removing material from fixed workpieces using CNC cutters. Let’s delve into the various types of cutting tools:
End Mills
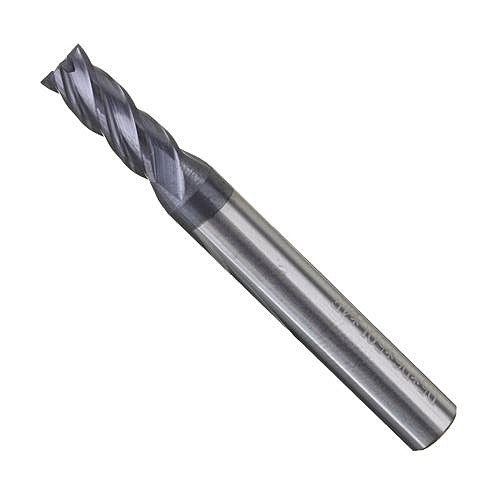
End mills, akin to drill bits but more versatile, are employed to create holes in materials even without a pre-drilled spot. They come in various types, distinguished by the number of flutes (spiraling cutting edges) and the shape of their noses. End mills are essential tools for achieving precise dimensions and complex shapes.
Slab Mills
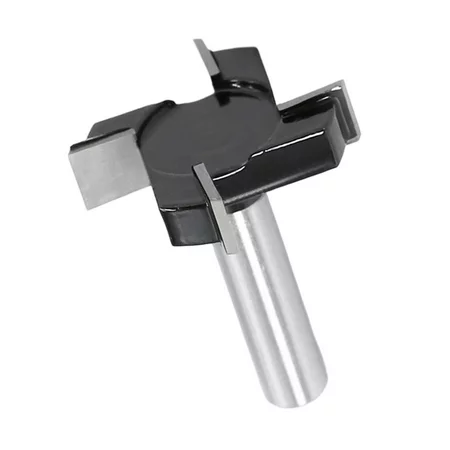
Slab mills are designed for heavy-duty operations and are ideal for milling flat surfaces. The workpiece must be positioned parallel to the CNC mill table for effective use. Slab mills excel in removing large amounts of material quickly and efficiently.
Face Mills
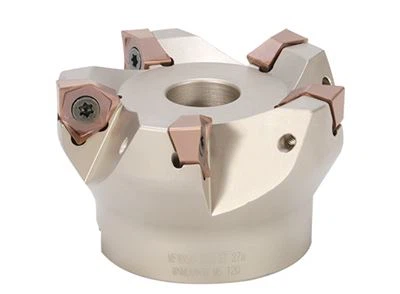
Face mills have flat faces with replaceable cutting edges made of carbide. These cutting edges are positioned on the side of the tool, enabling face mills to make flat sections on workpieces. One significant advantage of using face mills is the ability to replace their cutting edges, resulting in longer tool life and reduced costs.
Fly Cutters
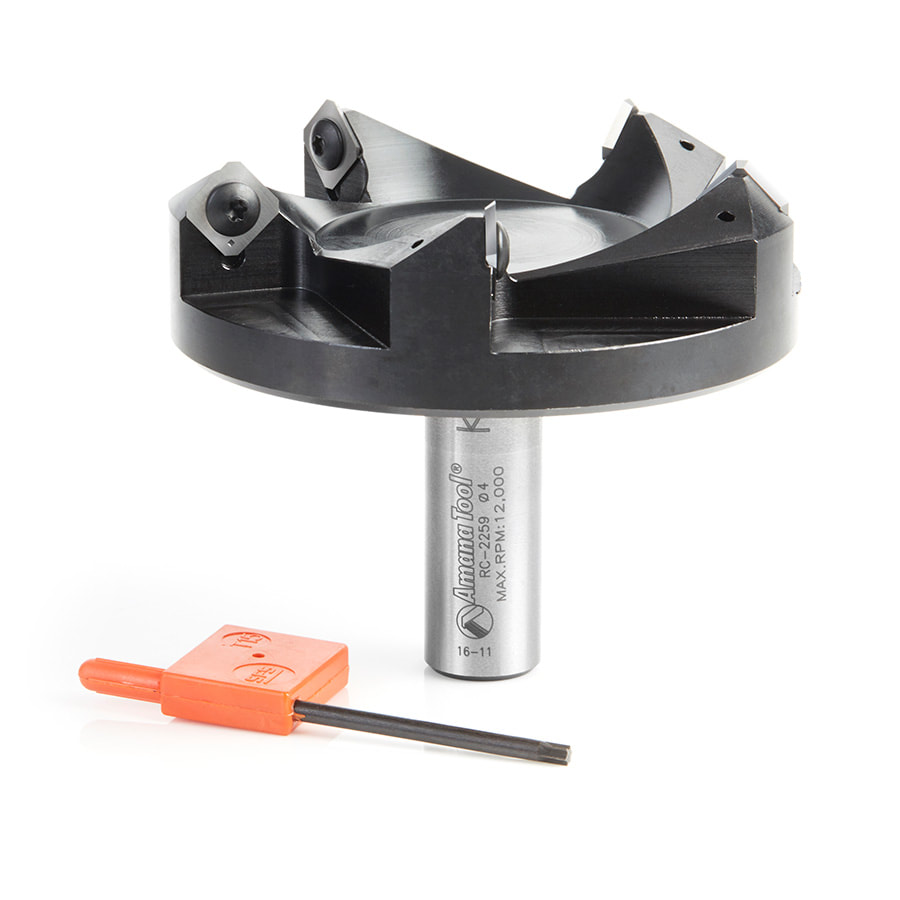
Fly cutters consist of a tool body and cutting bits. They are used to make shallow or broad cuts on workpieces. Fly cutters can have one or two cutting bits, and they cover larger sections of the workpiece compared to other cutting tools. They are a cost-effective option for achieving smooth finishes.
Hollow Mills
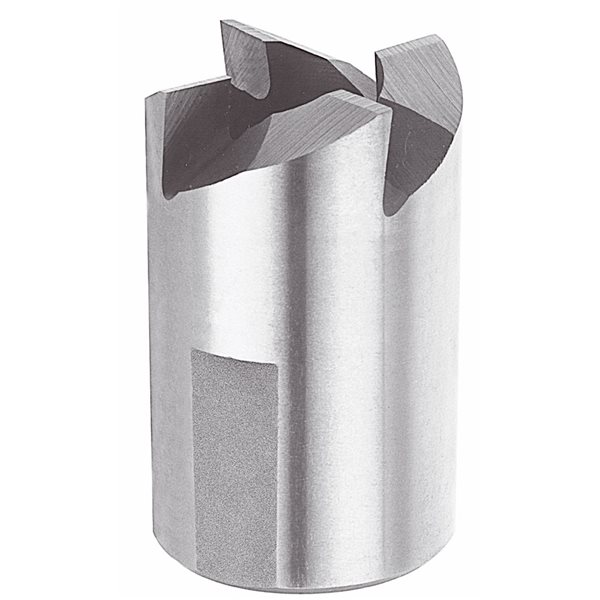
Hollow mills have a pipe-like structure and resemble inverted end mills. They are commonly used to create form radii and full points on workpieces. Hollow mills are ideal for achieving precise and intricate shapes in various materials.
Drilling Tools
CNC Drilling tools, also known as drill bits, are indispensable for creating holes in workpieces. They are utilized in conjunction with twist drills or CNC mills, employing their flutes and tapered cutting points to achieve precise drilling. Let’s explore some common drilling tools:
Center Drills
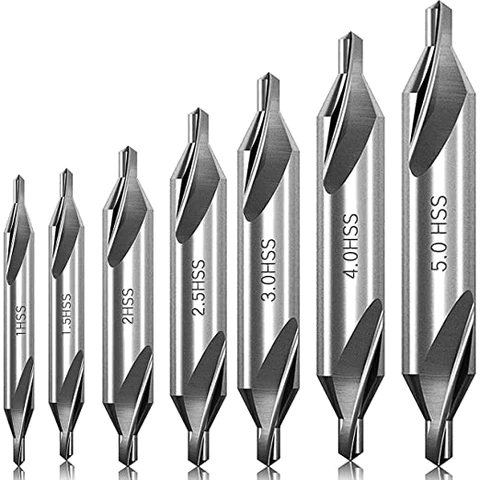
Center drills are used to create precise holes on the workpiece before enlarging them with other drill bits. They ensure accurate hole placement and help prevent drill bit wandering.
Ejector Drills
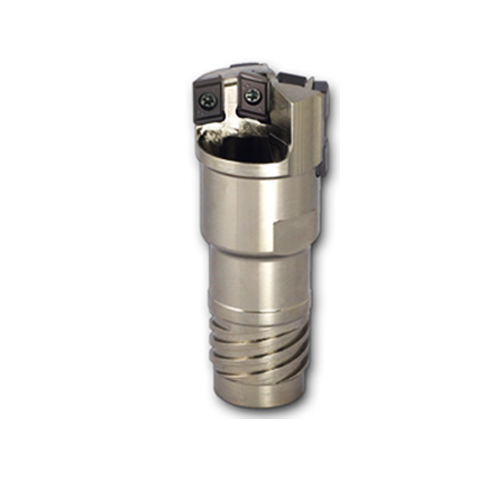
Ejector drills are employed after center drills to create larger and deeper holes on the workpiece. They enable the creation of holes with precise dimensions and depths.
Twist Drills
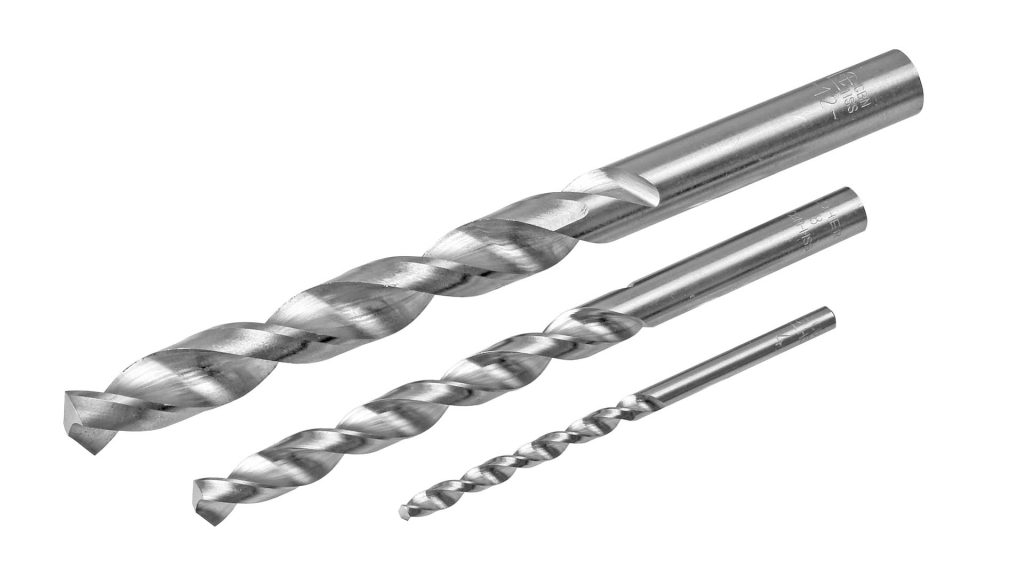
Twist drills are versatile tools used for drilling holes that do not require specific specifications. They are commonly used for general drilling applications and come in various sizes and designs.
Materials Used in CNC Machine Tools
The choice of raw material for CNC machine tools significantly influences the machining procedure, including feed rate, cutting speed, and overall effectiveness. It is essential to select a material harder than the workpiece material to ensure optimal performance. Let’s explore some common materials used for machining tools:
Carbon Steel
Carbon steel, containing a mixture of silicon, carbon, and manganese, is the most affordable material used in making CNC machine tools. However, its low durability limits its usage to lightweight materials like foam or plastic. Carbon steel tools are not suitable for heavy-duty operations.
High-Speed Steel
High-speed steel is a more durable material for making CNC machine tools. It contains metals like tungsten, molybdenum, and chromium, which enhance its hardness and heat resistance. High-speed steel tools can withstand high temperatures and are suitable for heavy-duty operations.
Cemented Carbides
Cemented carbides consist of carbides and metals like titanium. They offer excellent heat resistance compared to high-speed steel. However, their durability is lower, and they are mainly used for finishing tools that require precision and fine finishes.
Cutting Ceramics
Cutting ceramics are the hardest material used in CNC machine tools. They are resistant to corrosion and heat, making them suitable for cutting through the toughest workpieces. However, they are prone to cracks and chips, limiting their usage in machining tools.
Tool Coatings in CNC Machining Tools
Coatings play a crucial role in improving the properties of CNC machine tools, including hardness, thermal stability, and resistance to high temperatures. Several coatings are commonly used in CNC machining tools:
Titanium Nitride
Titanium nitride is one of the earliest and most common coatings used to increase the hardness of cutting tools. It also improves other properties such as thermal stability and wear resistance. However, variations of this coating with better properties have reduced its widespread usage.
Chromium Nitride
Chromium nitride coatings increase the hardness of machine tools and make them corrosion-resistant. They also enhance thermal strength, making them suitable for high-heat applications where other coatings may not suffice.
Aluminum Titanium Nitride (AlTiN) / Super-Life Titanium Nitride
Aluminum titanium nitride (AlTiN) coatings, containing a higher percentage of aluminum compared to titanium aluminum nitride (TiAlN), enhance the resistance of CNC machine tools to heat. They provide improved performance and extended tool life.
Titanium Carbo Nitride
Titanium carbo nitride is a variation of the titanium nitride coating that contains carbon. It enhances the hardness and surface lubrication of CNC cutting tools. However, its relatively low operating temperature limits its usage in high-temperature environments.
Factors to Consider When Selecting CNC Machine Tools
Selecting the right CNC machine tool is crucial for achieving successful machining operations. Consider the following factors when choosing the appropriate tool:
- Workpiece Material: The material being worked on should be softer than the tool material. Understanding the workpiece’s toughness helps determine the suitable tool materials.
- Tool Material: Consider the properties required, such as tool lifespan and heat resistance, to select the most appropriate tool material for the machining procedure.
- Number of Flutes: The number of flutes on the tool impacts the feed rate. Choosing the optimal number of flutes ensures efficient machining while avoiding workpiece bit jamming.
- Machining Operation: Different machining procedures require specific tools. However, some tools designed for a particular machining procedure can be used for other applications as well.
- Tool Coating: Coatings improve tool properties but are not mandatory. Consider the coating requirements based on cost, hardness, and specific machining needs.
Conclusion
CNC machine tools are essential for modern machining operations, providing precision, efficiency, and versatility. Understanding the different types of tools, their functions, the materials used, common tool coatings, and factors to consider when selecting the right tool empowers manufacturers to make informed decisions. Whether you need turning tools, cutting tools, drilling tools, or grinding tools, each tool type serves a specific purpose and contributes to the overall success of your machining projects. By carefully selecting the appropriate CNC machine tools, you can achieve accurate, high-quality results and optimize your manufacturing processes.
Recommended Reads:
- The Future of Smart CNC Prototyping
- Advanced Techniques for Machining Holes: Unveiling CNC Services’ Expertise
- How to Manage Production Anomalies of CNC Prototypes
- What is Micro Milling?
- Ensuring Efficient CNC Machining in the Aerospace Industry
Other Articles You Might Enjoy
- Custom Precision CNC Machining Services for Bronze Parts
Introduction to CNC machining and Bronze Parts Manufacturing Custom precision Computer Numerical Control (CNC) machining is a unique technology that employs computerized controls and machine tools to eradicate layers of…
- Plastic vs. Metal CNC Machining: A Detailed Comparison?
CNC Machining: An Essential Process Across Industries Computer Numerical Control (CNC) machining is a digital manufacturing technology that makes use of pre-programmed computer software to dictate the movement of various…
- Bead Blasting: The Secret to Quality CNC Machining(cnc machining tools Mavis)
The world of manufacturing has witnessed revolutionary changes with the advent of Computer Numerical Control (CNC) machining. It is a process used in the manufacturing sector that involves the use…