What is Counterbore and Why Does It Matter in CNC Machining?
Counterbore is a term that frequently comes up in machining and manufacturing, especially in industries that require precision assembly. A counterbore is a cylindrical, flat-bottomed recess cut into a material, typically at the entry point of a hole. It allows screws or bolts to sit flush with or below the surface, ensuring smooth assembly and an improved aesthetic appearance.
Counterbore is not to be confused with countersink, which is cone-shaped and designed for flathead screws. While both techniques provide functional recesses, counterbore is more suited for applications requiring flat-bottomed hardware. This feature is critical in industries like aerospace, automotive, and electronics, where safety and precision are paramount.
When I first started working with counterbore machining, I was amazed by how essential it is for creating clean and functional assemblies. Without counterbore, exposed bolt heads could interfere with operations or make devices look unprofessional.
Here’s a quick comparison between Counterbore and Countersink for clarity:
Feature | Counterbore | Countersink |
---|---|---|
Shape | Cylindrical, flat bottom | Conical, angled |
Purpose | To recess cylindrical bolt heads | To recess flathead screws |
Typical Use | Machinery, heavy equipment | Electronics, light fixtures |
CNC Compatibility | High | High |
Understanding what counterbore is and how it’s different from other techniques sets the foundation for exploring its role in CNC machining. Let’s move on to see why CNC machining is the best tool for the job.
The Role of CNC in Counterbore Machining
Counterbore machining has evolved significantly with the introduction of CNC (Computer Numerical Control) technology. Unlike manual machining, CNC machining enables precise, repeatable, and efficient production of counterbore holes. When working on projects that involve hundreds of counterbore holes—such as large-scale automotive parts—I have found CNC machines indispensable for ensuring consistency.
Why CNC is Ideal for Counterbore:
- Precision: CNC ensures uniform depth and diameter for every counterbore hole, eliminating human error.
- Efficiency: It can process multiple counterbore holes in a single setup, drastically reducing production time.
- Flexibility: CNC machines accommodate various materials, from soft plastics to hard metals, using tailored settings.
The following table highlights the comparison between CNC and manual counterbore machining:
Criteria | CNC Machining | Manual Machining |
---|---|---|
Precision | ±0.001 inches | ±0.01 inches |
Speed | High | Moderate |
Automation | Fully automated | Requires operator input |
Material Compatibility | Extensive | Limited by operator skill |
When machining counterbore holes for aerospace components, CNC allowed me to ensure each bolt recess was identical. This is critical for high-stress environments where even minor inconsistencies could lead to part failure.
How to Machine Counterbore Holes Using CNC
CNC machining simplifies the counterbore process, but there’s still an art to doing it right. The process generally involves:
- Drilling the Pilot Hole: The primary hole for the screw or bolt.
- Counterboring the Recess: Enlarging the top portion with a flat-bottomed end mill or specialized counterbore tool.
Key Steps for CNC Counterbore Machining:
- Step 1: Secure the material on the CNC table using clamps or a vise.
- Step 2: Program the CNC machine with precise dimensions for the pilot hole and counterbore recess.
- Step 3: Select the appropriate tool (e.g., end mill or counterbore bit) based on material and dimensions.
- Step 4: Execute the CNC program, monitoring for tool wear or material inconsistencies.
In one project for a client’s automotive assembly line, I used these steps to create hundreds of identical counterbore holes. CNC allowed for tight tolerances, ensuring every bolt fit perfectly.
Here are optimal cutting parameters for common materials:
Material | Spindle Speed (RPM) | Feed Rate (IPM) | Depth of Cut (inches) |
---|---|---|---|
Aluminum | 3,000–5,000 | 20–30 | 0.1–0.2 |
Steel | 1,500–2,500 | 10–15 | 0.05–0.1 |
Stainless Steel | 800–1,200 | 5–10 | 0.03–0.08 |
Selecting the right parameters ensures a smooth machining process and reduces tool wear.
Tools and Materials for Counterbore in CNC Machining
Using the right tools is critical for achieving precise counterbore holes. Common tools include:
- Flat-Bottomed End Mills: Ideal for general counterbore applications.
- Specialized Counterbore Tools: Designed for specific bolt head dimensions.
- Multi-Purpose Drill Countersink Tools: For projects requiring both countersink and counterbore features.
Choosing Tools Based on Material:
- Soft Materials (e.g., aluminum): High-speed steel (HSS) tools work well.
- Hard Metals (e.g., stainless steel): Carbide tools are recommended for their durability.
- Plastics: Use sharp tools with low RPM to avoid melting.
Tool Type | Material Compatibility | Cost | Durability |
---|---|---|---|
HSS End Mills | Aluminum, plastics | Low | Moderate |
Carbide Tools | Steel, stainless steel | High | High |
Coated Tools (TiN, TiCN) | General | Moderate | Very High |
In my experience, investing in high-quality tools pays off in the long run. They ensure smoother finishes and longer lifespans, particularly when working with abrasive materials like stainless steel.
Programming CNC for Counterbore Operations
Writing a CNC program for counterbore operations is an essential step in ensuring precision and efficiency. With CNC, the programming process involves creating detailed instructions for both the pilot hole and the counterbore recess.
Steps to Program CNC for Counterbore:
- Define Dimensions:
Input the diameter, depth, and positioning of the pilot hole and counterbore. These dimensions are typically derived from part blueprints.
Example: A bolt with a head diameter of 0.75 inches and a depth of 0.5 inches would require a counterbore diameter slightly larger than the bolt head, such as 0.8 inches. - Toolpath Creation:
Use CAM software to generate the toolpath for both the pilot hole and the counterbore.
Ensure the tool retracts between the operations to avoid collisions or tool damage. - Select Appropriate G-Codes:
Use G-codes to control the machining process.
G81: Drilling cycle for the pilot hole.
G85: Boring cycle for the counterbore recess.
Example of a program for one counterbore:
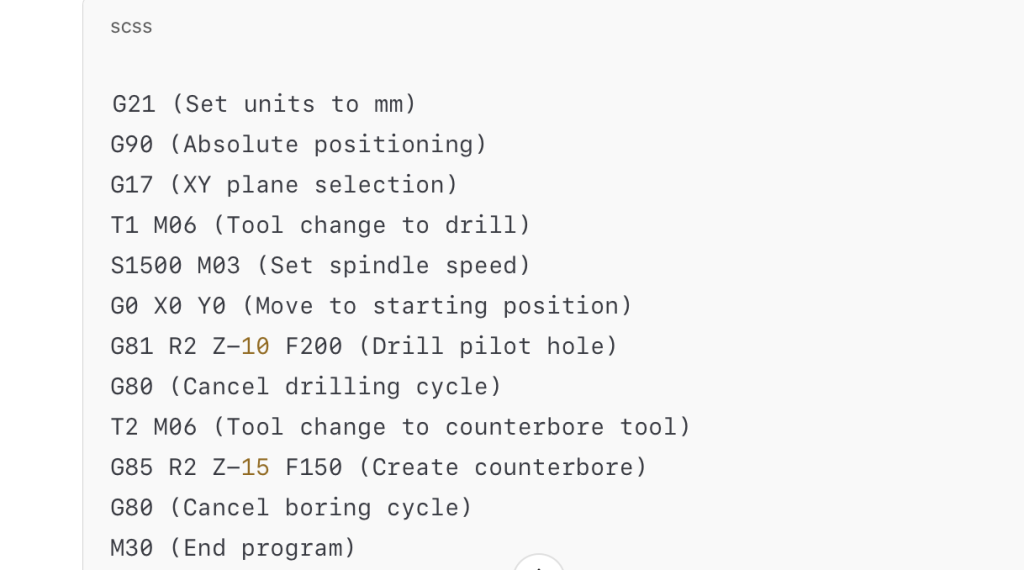
4. Simulate the Program:
Run the program through a CNC simulator to check for errors. Simulations help identify potential tool collisions or incorrect paths.
5. Test and Validate:
Perform a test run on scrap material. Measure the dimensions of the counterbore to ensure accuracy.
Optimizing CNC Programming for Counterbore:
- Toolpath Optimization: Use helical toolpaths for larger counterbore diameters to reduce cutting forces.
- Feed Rate Adjustment: Match the feed rate to the material being machined to prevent tool wear or chatter.
- Batch Processing: For multiple counterbores, program efficient transitions between holes to minimize cycle time.
Feature | Manual Programming | CAM Software |
---|---|---|
Ease of Use | Requires expertise | User-friendly |
Error Potential | Higher | Lower |
Optimization | Limited | Advanced (toolpath, speed) |
In my experience, CAM software has been invaluable for complex projects involving dozens of counterbore holes. It simplifies programming and ensures optimal machining efficiency.
Ensuring Precision and Quality in Counterbore Machining
The success of counterbore machining depends heavily on achieving precision and maintaining quality. Even slight deviations in depth or diameter can lead to assembly issues or mechanical failures.
Critical Factors for Counterbore Quality:
- Dimensional Accuracy:
The diameter and depth of the counterbore must match the bolt or screw specifications. Variations can result in improper seating or structural instability. - Surface Finish:
A smooth surface ensures a snug fit for bolt heads and reduces stress concentrations. Poor finishes can lead to corrosion or loosening over time. - Concentricity:
The counterbore and the pilot hole must be perfectly aligned to prevent misalignment during assembly.
Inspection Techniques:
Inspection Tool | Use Case | Accuracy |
---|---|---|
Dial Caliper | Measuring diameter and depth | ±0.01 mm |
Surface Finish Comparator | Assessing surface quality | Visual/tactile evaluation |
Coordinate Measuring Machine (CMM) | Ensuring concentricity and alignment | High precision |
Common Counterbore Defects and Solutions:
Defect | Cause | Solution |
---|---|---|
Rough surface finish | Tool wear or incorrect feed rate | Use sharp tools; adjust feed and speed |
Incorrect depth | Programming error or tool slippage | Verify program; check tool holder tightness |
Misalignment | Inaccurate setup or machine vibration | Ensure proper setup; stabilize machine |
During a recent aerospace project, I encountered misalignment issues with counterbores on a titanium part. By recalibrating the CNC machine and using a CMM for validation, we ensured all holes met the required tolerances.
Industry Applications of Counterbore and CNC Machining
Counterbore holes play a vital role in numerous industries where precision and functionality are critical. Here are some key applications:
Automotive Industry:
- Applications:
Engine components, such as cylinder heads and crankcases.
Brake systems where bolts need to be recessed for safety and aerodynamics. - Example:
In one project, we machined counterbore holes for a performance car’s suspension system. The CNC ensured each bolt fit perfectly, enhancing the vehicle’s safety and durability.
Aerospace Industry:
- Applications:
Aircraft fuselages, where counterbore holes reduce drag by allowing bolts to sit flush.
Engine mounts, where precision and reliability are paramount. - Example:
For an aerospace client, we machined counterbores in lightweight aluminum parts to minimize weight while ensuring structural integrity.
Electronics and Consumer Goods:
- Applications:
Device enclosures where screws must not protrude to maintain sleek designs.
Assembly of small mechanical parts in gadgets and appliances. - Example:
In producing enclosures for a wearable fitness tracker, counterbore machining allowed us to hide screws, improving aesthetics and user comfort.
Industrial Machinery:
- Applications:
Heavy-duty equipment requiring robust assembly.
Components like flanges and brackets where bolts need secure seating. - Example:
For a construction equipment manufacturer, we used counterbore machining to improve assembly strength and durability in hydraulic systems.
The versatility of counterbore holes, combined with CNC precision, makes them indispensable across these industries. Each application highlights the value of proper tooling, programming, and machining techniques.
Troubleshooting Common Challenges in Counterbore CNC Machining
Even with precise CNC technology, counterbore machining can present challenges. Identifying and addressing these issues ensures efficiency and high-quality results.
Common Counterbore Challenges and Solutions
Challenge | Cause | Solution |
---|---|---|
Tool Wear | Excessive cutting speed or poor-quality tools | Use carbide or coated tools; reduce spindle speed. |
Surface Roughness | Dull tools or improper feed rate | Replace tools regularly; adjust feed rate for material compatibility. |
Incorrect Counterbore Depth | Programming errors or tool holder slippage | Verify CNC program; ensure tool is securely fastened in the holder. |
Material Deformation | Insufficient clamping or excessive force | Use proper clamping techniques; reduce cutting forces. |
Chatter or Vibration | Machine instability or incorrect parameters | Stabilize machine; adjust speed and feed; use dampened tool holders. |
For example, during a project involving stainless steel parts, I noticed chatter marks in counterbore holes. By switching to a dampened tool holder and recalibrating the feed rate, we achieved smoother finishes without damaging the tools.
Preventive Maintenance for Counterbore Machining
- Inspect Tools Regularly: Check for wear and replace tools promptly to avoid defects.
- Monitor Machine Settings: Periodically validate spindle speed, feed rate, and tool alignment.
- Calibrate CNC Machines: Ensure machine axes are properly aligned and calibrated for accuracy.
By taking these preventive measures, counterbore machining can achieve consistent results even in demanding applications.
Future Trends in Counterbore and CNC Machining
The field of CNC machining is constantly evolving, and counterbore machining is no exception. Emerging technologies and trends are poised to enhance precision, efficiency, and sustainability.
1. High-Speed Machining
- Impact on Counterbore:
High-speed machining reduces cycle times for counterbore operations while maintaining accuracy. This is especially beneficial in industries with tight production schedules, like automotive manufacturing.
2. Tooling Innovations
- Example:
Tools with advanced coatings (e.g., diamond-like carbon) offer greater durability and reduced friction, making them ideal for abrasive materials. Multi-functional tools that combine drilling and counterboring capabilities further streamline processes.
3. Artificial Intelligence and Machine Learning
- Role in CNC Machining:
AI algorithms can optimize toolpath planning and predict tool wear, reducing downtime and improving machining quality. For counterbore machining, this means fewer defects and higher efficiency.
4. Automation and Robotics
- Integration:
Automated loading/unloading systems and robotic arms can handle large batches of counterbore machining tasks with minimal human intervention. This reduces labor costs and ensures consistent results.
5. Sustainability Initiatives
- Eco-Friendly Machining:
Techniques like minimum quantity lubrication (MQL) reduce coolant usage, minimizing environmental impact. Recyclable tooling materials are also gaining traction.
The adoption of these technologies will redefine counterbore machining, making it more efficient, sustainable, and adaptable to future industry demands.
Conclusion
Counterbore machining is an indispensable process in modern manufacturing, and CNC technology has revolutionized its precision and efficiency. From understanding the basics to adopting advanced techniques, mastering counterbore machining ensures success in industries demanding high-quality assemblies. By leveraging the right tools, programming skills, and emerging technologies, you can stay ahead in this critical aspect of machining.
FAQ
- What is the primary purpose of counterbore holes?
Counterbore holes are designed to allow bolts or screws to sit flush with or below the surface of a material. This enhances the assembly’s aesthetics, safety, and functionality. For example, in automotive applications, counterbore holes ensure that fasteners don’t interfere with other components or pose safety risks. - How does CNC improve counterbore machining?
CNC provides unmatched precision and repeatability, making it ideal for counterbore machining. It automates the process, ensuring consistent diameter, depth, and alignment. In high-volume production, CNC significantly reduces labor and time costs while maintaining accuracy. - What materials are suitable for counterbore machining?
Almost all materials can be counterbored using CNC, including aluminum, steel, stainless steel, titanium, and plastics. Tool selection and machining parameters must be adjusted based on the material’s hardness and machinability. - What are the common defects in counterbore machining and how to avoid them?
Common defects include rough surfaces, incorrect depth, and misalignment. Using sharp tools, verifying CNC programs, and ensuring proper machine calibration are essential to avoid these issues. - What is the difference between counterbore and countersink?
A counterbore creates a flat-bottomed recess for cylindrical bolt heads, while a countersink creates a conical recess for flathead screws. Counterbore is used in heavy-duty applications, whereas countersink is common in electronics and decorative assemblies. - Can counterbore and pilot holes be machined in one setup?
Yes, CNC machines can perform both operations in a single setup by using multi-functional tools or sequential programming. This reduces cycle time and improves alignment. - How do I choose the right counterbore tool?
Tool selection depends on the material being machined and the dimensions of the counterbore. For hard metals like stainless steel, carbide tools are ideal, while HSS tools work well for softer materials like aluminum. - What are the best practices for counterbore depth control?
Use precise CNC programming and regularly calibrate the machine to maintain depth accuracy. Monitoring tool wear is also critical to avoid inconsistencies. - Is counterbore machining cost-effective for small batches?
CNC machining can be cost-effective even for small batches, especially when high precision is required. However, the setup cost may be higher compared to manual methods. - What industries benefit most from counterbore machining?
Industries such as automotive, aerospace, electronics, and heavy machinery rely heavily on counterbore machining for precise assembly and functionality. - Can CNC machines handle large-diameter counterbores?
Yes, CNC machines equipped with appropriate tooling can machine large-diameter counterbores. However, the machine’s power and rigidity must be sufficient to handle the increased cutting forces. - How can I improve surface finish in counterbore machining?
Ensure sharp tools, optimize feed rates and speeds, and use appropriate coolant. Polishing or secondary finishing processes can further enhance the surface quality. - What are the latest advancements in counterbore tooling?
Recent innovations include multi-functional tools, advanced coatings for durability, and adaptive tooling that reduces vibration during machining. - How does counterbore machining differ for hard-to-machine materials?
Hard materials like titanium require slower feed rates, lower spindle speeds, and advanced tooling to prevent tool wear and maintain accuracy. - How do I ensure concentricity in counterbore holes?
Use a CNC machine with a well-calibrated spindle and high-precision work holding. Regular inspection with tools like a CMM can verify concentricity.
Other Articles You Might Enjoy
- The Future of Biomedical CNC Machining: Innovations in Material Compatibility and Functionality
Introduction to Biomedical CNC Machining Biomedical CNC (Computer Numerical Control) machining stands as a cornerstone in the development of medical devices, enabling the precise fabrication of complex parts essential for…
- Countersink Bit in CNC Machining: Tips, Techniques, and Tools
The Unsung Hero of CNC Machining In CNC machining, precision is everything. Whether you're crafting aerospace components, automotive parts, or custom furniture, a tiny misalignment can compromise the entire project.…
- How to Choose the Best Metric Drill Bits for CNC Projects
Why Metric Drill Bits Are Essential in CNC Machining When it comes to CNC machining, precision isn’t just a goal—it’s a requirement. The quality of your project often depends on…
- Countersink in CNC Machining: A Complete Guide
Understanding Countersink in CNC Machining In CNC machining, precision isn't just a feature—it's a requirement. One critical process that often gets overlooked is the countersink. A small, conical recess at the…
- Applications and Advantages of Bronze CNC Machining
1. Introduction: The Enduring Allure of Bronze in CNC Machining In this opening section, we explore the timeless appeal of bronze as a material for CNC machining. From its rich…
- CNC Aluminum Machining Services: Advanced Techniques for Perfect Parts
CNC Aluminum Machining Services In the current manufacturing landscape, CNC aluminum machining services play a pivotal role. CNC which simply translates to 'Computer Numerical Control', is an advanced technique used…