When producing CNC machining parts, it’s not just about hitting the right dimensions and achieving the desired surface roughness. The shape and the relative positions of different elements of a part can also present challenges. Let’s dive into the world of shape and position tolerances, which are crucial for ensuring that parts fit and function correctly.
Shape and Position Errors
During production, parts can exhibit shape errors, as shown in Figures (a) and (b), and position errors, as depicted in Figures (c) and (d). Shape errors refer to deviations from the ideal shape, while position errors involve deviations from the ideal location.
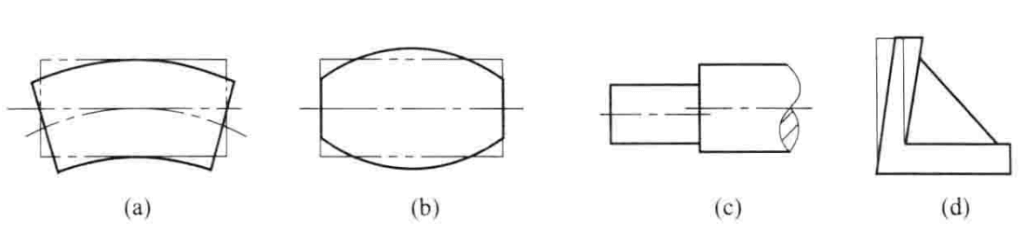
These errors can significantly affect the interchangeability of parts and the overall performance and lifespan of machines. Hence, controlling these errors is crucial for quality assurance.
Key Terminologies
- Element: These are the points, lines, and surfaces that make up the geometric features of a part. Points include center points of spheres and axes of cylinders; lines include center lines and axis lines; surfaces include planes and curved surfaces.
- Ideal Element: This is the theoretically perfect geometric shape used as a reference during design.
- Actual Element: The element that actually exists on the part, which may have deviations due to manufacturing processes.
- Measured Element: The element on which shape or position tolerance is specified.
- Datum Element: The element used as a reference for determining the direction or position of the measured element.
Shape and Position Tolerances
Shape tolerance refers to the allowable variation in the shape of an element, while position tolerance refers to the allowable variation in the location of an element relative to a datum. These tolerances are critical for ensuring that parts can be assembled and function correctly.
Examples:
- Straightness: For a shaft, the straightness tolerance might be specified to ensure the shaft’s surface does not deviate beyond a certain limit.
- Flatness: For a part’s surface, flatness tolerance ensures the surface remains within two parallel planes a specific distance apart.
Here are some symbols used for different types of shape and position tolerances:
Tolerance Type | Symbol | Example Description |
---|---|---|
Straightness | ———— | A shaft’s straightness must be within 0.02mm. |
Flatness | □ | A surface’s flatness must be within 0.1mm. |
Roundness | ⃝ | The roundness of a hole must be within 0.05mm. |
Cylindricity | ⦿ | The cylindricity of a cylinder must be within 0.1mm. |
Parallelism | ∥ | A surface must be parallel to a datum within 0.05mm. |
Perpendicularity | ⊥ | A hole must be perpendicular to a surface within 0.05mm. |
Position | ○ | The position of a hole relative to a datum within 0.1mm. |
Practical Application
In practical terms, managing these tolerances involves careful planning and precise measurement. For example, ensuring that the flatness of a surface is within the specified tolerance might require specific machining techniques and the use of precise measuring tools.
Example Table of Achievable Tolerances:
To provide a comprehensive understanding of the achievable tolerances across various machining processes, here is an table that includes a broader range of processes and the typical tolerances they can achieve.
Machining Process | Straightness | Flatness | Roundness | Cylindricity | Parallelism | Perpendicularity | Position | Concentricity | Surface Roughness (Ra) |
---|---|---|---|---|---|---|---|---|---|
Grinding | 0.001 – 0.005 mm | 0.002 mm | 0.002 mm | 0.003 mm | 0.002 mm | 0.003 mm | 0.003 mm | 0.003 mm | 0.1 – 0.2 µm |
Milling | 0.01 – 0.03 mm | 0.02 mm | 0.02 mm | 0.03 mm | 0.02 mm | 0.03 mm | 0.03 mm | 0.03 mm | 0.4 – 1.6 µm |
Turning | 0.01 – 0.02 mm | 0.02 mm | 0.01 mm | 0.02 mm | 0.02 mm | 0.02 mm | 0.02 mm | 0.02 mm | 0.8 – 1.6 µm |
Drilling | 0.02 – 0.05 mm | 0.03 mm | 0.03 mm | 0.04 mm | 0.03 mm | 0.04 mm | 0.04 mm | 0.04 mm | 1.6 – 3.2 µm |
Boring | 0.005 – 0.02 mm | 0.01 mm | 0.005 mm | 0.01 mm | 0.01 mm | 0.015 mm | 0.015 mm | 0.015 mm | 0.4 – 1.6 µm |
Honing | 0.002 – 0.005 mm | 0.002 mm | 0.001 mm | 0.003 mm | 0.002 mm | 0.002 mm | 0.003 mm | 0.003 mm | 0.1 – 0.4 µm |
Lapping | 0.001 – 0.003 mm | 0.001 mm | 0.001 mm | 0.002 mm | 0.001 mm | 0.0015 mm | 0.002 mm | 0.002 mm | 0.05 – 0.2 µm |
Electrical Discharge Machining (EDM) | 0.01 – 0.02 mm | 0.01 mm | 0.01 mm | 0.02 mm | 0.01 mm | 0.015 mm | 0.015 mm | 0.015 mm | 0.8 – 1.6 µm |
Laser Cutting | 0.02 – 0.05 mm | 0.03 mm | 0.03 mm | 0.04 mm | 0.03 mm | 0.04 mm | 0.04 mm | 0.04 mm | 1.6 – 3.2 µm |
Water Jet Cutting | 0.05 – 0.1 mm | 0.07 mm | 0.07 mm | 0.08 mm | 0.07 mm | 0.08 mm | 0.08 mm | 0.08 mm | 3.2 – 6.3 µm |
Additive Manufacturing (3D Printing) | 0.1 – 0.2 mm | 0.1 mm | 0.1 mm | 0.15 mm | 0.1 mm | 0.15 mm | 0.15 mm | 0.15 mm | 6.3 – 12.5 µm |
This table provides a more detailed overview of the achievable tolerances across various machining processes, offering a comprehensive reference for designers and machinists to understand the capabilities and limitations of different methods.
Understanding and applying these tolerances is essential for producing high-quality CNC machined parts that meet design specifications and perform reliably in their intended applications.
Other Articles You Might Enjoy
- Requirements for CNC Machining Parts
Preparation Work Complete the necessary preparation before machining, including process analysis, process route design, tool and fixture selection, and program compilation. online cnc machining service Operating Steps and Contents Start…
- What are the requirements for CNC machining of bearing parts?
Bearings are common and important parts in the automotive industry, which can support transmission components and transmit torque. Generally, CNC machining centers are used to process bearing parts. So what…
- Evolution of Mills and Machining Centers: The Future of CNC Machining Parts
Stepping into the world of CNC machining, you quickly realize how pivotal mills and machining centers are in crafting precise parts. Over time, these machines have evolved significantly, transforming from…
- Precision CNC Machining of Steel: High-Volume Production
Precision CNC Machining and High-Volume Production As an integral part of modern manufacturing processes, Precision Computer Numerical Control (CNC) machining brings about unmatched accuracy and consistency in the production of…
- Smart Choice for CNC Machining Parts: Comprehensive Analysis of Horizontal Machining Centers
When it comes to CNC machining parts, the type of machining center you choose can significantly impact the efficiency and quality of your work. Horizontal CNC machining centers (HMCs) are…
- Mastering Corner Control in CNC Machining Parts
CNC machining is all about precision and efficiency, especially when it comes to navigating sharp corners and changing directions. When machining complex contours, the feed rate and movement control are…