CNC machining is a popular manufacturing process that utilizes numerical codes to create precise and complex parts. It offers numerous advantages such as increased production speed, reduced manufacturing time for identical parts, and minimized human errors due to computer control. Unlike CNC machining, 3D printing is an additive manufacturing technique more suited for producing parts from plastic and lower-quality materials. When it comes to cutting precise products or manufacturing a large number of identical items, CNC machining surpasses 3D printing.
CNC machines are capable of working with various materials, including metals, alloys, and plastics. However, 3D printing is not cost-effective for mass production. The cost of CNC machining depends on several factors that need to be considered when calculating expenses. In this article, we will discuss the key factors that influence CNC machining costs and provide tips to reduce them effectively.
Factors Affecting CNC Machining Costs
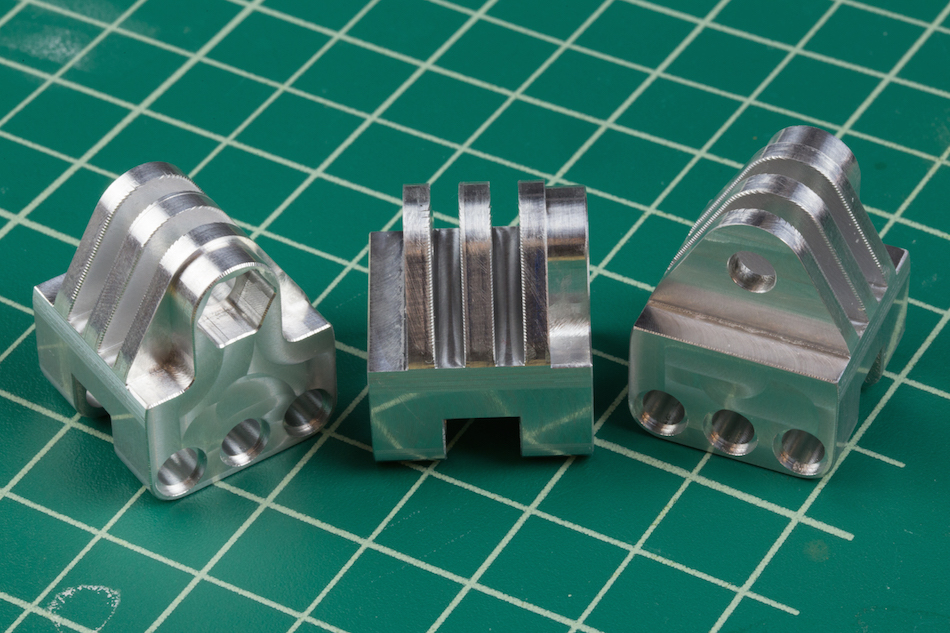
CNC Machine Costs
The choice of machine significantly impacts machining costs. There are mainly two types of machines used in CNC manufacturing: 3-axis and multi-axis machines. Factors such as machine size, weight, speed, power, and configuration affect the machine cost. The machining cost is calculated per hour, with 3-axis CNC machining costing around $40 per hour and CNC turning machines costing approximately $35 per hour. Multi-axis machines have higher hourly rates ranging from $75 to $125 due to their increased complexity. CNC milling, which involves more intricate parts, tends to be more expensive than other machining operations. The number of axes in milling machines affects costs, with 5-axis machining being more expensive than 3-axis machines.
Machining Time
The time required to complete machining a part plays a significant role in cost calculation. Longer machining times result in higher costs, including the basic setup expenses. Software tools like Computer-Aided Manufacturing (CAM) can estimate the time needed to complete a project based on a 3D CAD design model. Complex projects typically require more hours to finish.
Labor
Compared to manual machining, CNC machining reduces the need for manual labor. The primary labor cost involves an expert designer creating the 3D CAD design model, which increases with product complexity. The per-part machining cost remains the same, even when producing a larger quantity of parts, reducing overall costs. Additional labor costs arise from operating the CNC machine, with costs increasing as more hours are required for machining. If manual work is necessary for assembly, finishing, or post-processing, extra labor costs are added. Similarly, costs increase if the finished product needs to be delivered to a different location.
Shape Complexity and Dimensions
The complexity of CNC machined parts affects costs. Parts with higher complexity may require additional process operations, different tools, and increased production time. Features like sharp internal corners, deep cavities, or thin walls tend to increase machining costs. On the other hand, designs with simpler features are easier and quicker to manufacture. Additionally, larger parts require more raw materials and time to produce, resulting in higher costs compared to smaller parts.
Material Costs
Material costs play a crucial role in CNC machining expenses. The final product’s price depends on the materials used, whether plastic or metal. Plastic and aluminum are less expensive and easier to machine compared to stainless steel. In CNC machines, material is removed from solid blocks to create the 3D object, which means the required raw material will be more than the material used in the final product. Machinists purchase materials in the form of solid blocks and calculate the expense per block. Aluminum is commonly used due to its affordability and excellent machinability. Stainless steel and brass are more costly due to their poor machinability relative to aluminum. The machining cost of the titanium alloy is the highest among these metals because it may require special tools to manufacture the parts. When it comes to plastics, the price of bulk material is lower, tools required are less expensive, and less time is required to machine plastics like Nylon, Delrin, and ABS.
Surface Finishing
Certain products require surface finishing, which increases the final product’s cost. Surface finishes such as polishing are necessary to enhance aesthetics and remove machining scratches. Other finishing processes include coating, anodizing, painting, chroming, blacking, galvanizing, brushing, and water transferring. Adding any of these finishes incurs extra costs.
Tooling Cost
In some cases, standard tooling is insufficient, necessitating custom tooling, which increases CNC machining costs.
Tolerances
Tighter tolerances in part manufacturing result in higher costs as fabricating parts with such precision requires complex machinery. Sometimes, holes or cavities with tight tolerances may develop surface burrs, requiring additional time to rectify.
Quantity
The volume of the order tremendously affects the cost of the final product. While the overall cost increases with larger orders, the cost per part decreases. Producing parts in larger quantities reduces machining costs as the cost per unit decreases. Designing an identical part once and repeating the machine setup for each part decreases production costs.
Three Tips to Reduce CNC Machining Costs
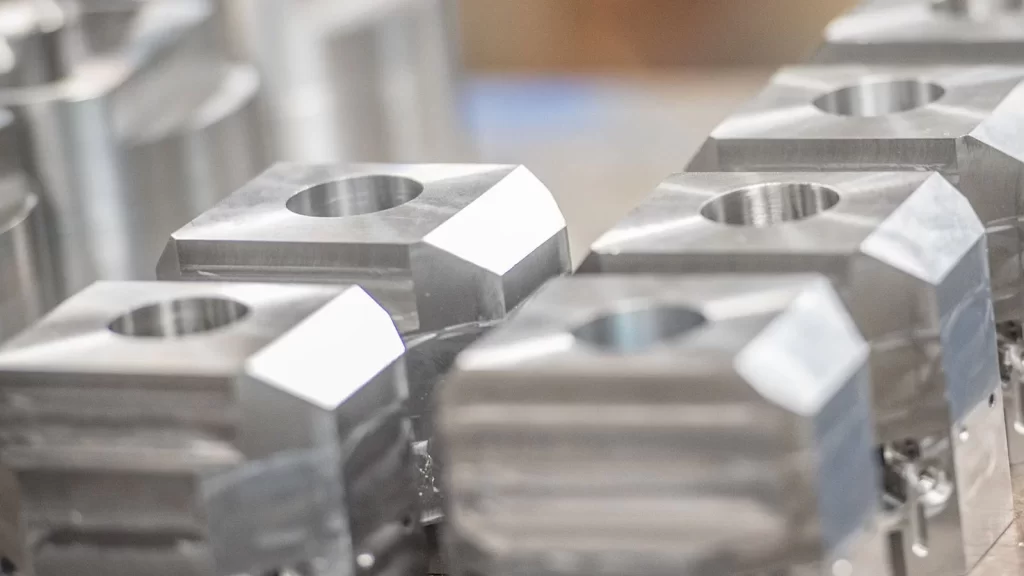
Quantity
A significant portion of machining costs can be saved when producing parts in larger numbers. The cost per unit part decreases as designing the identical part needs to be done only once. In this case, you need to repeat the machine setup for each part, resulting in a decrease in production cost.
Be Wise in Material Selection
Selecting the right materials can significantly reduce the cost of the final product. Choose materials with good mechanical properties that are cost-effective to process. Consider the functional requirements of the product and select the best available material. There is a difference in price between plastic and metal materials. You can align the material selection with the needs of your project and seek advice from your manufacturer for more guidance.
Design Optimization
Optimizing the design without compromising functionality is crucial for reducing production costs.
- Consider Hole Sizes and Profiles: Ensure that part features like holes, contours, slots, and threads can be made using standard toolings commonly available. Custom hole and thread sizes require special tools, which can be quite expensive. You can find many references about standard sizes used in the machining industry available on the internet.
- Avoid Thin Walls and Deep Cavities in Part Design: Thin-walled parts and deep cavities are challenging to achieve through machining and are usually prone to dimensional inaccuracies. These part features tend to cause vibration and may lead to the scrappage of parts.
- Avoid Very Tight Tolerances as Much as Possible: Parts with tighter tolerances are significantly harder to achieve, making them more expensive. Only control a dimension if it is essential to the part’s overall functionality. A helpful piece of advice is to design your part to have one common reference point or datum. This simplifies dimensional controls and inspection, reducing costs.
- Convert Complex Parts into Modular Components: When a part becomes too complex, consider splitting it into multiple components to be assembled. This approach simplifies machining, reduces setup time, minimizes machining operations, and optimizes machining time. Splitting complicated parts into simpler separate parts is a common strategy used by designers to promote manufacturability and reduce fabrication costs.
FAQs
Is CNC machining expensive?
The cost of CNC machining depends on various factors. However, manufacturing a larger number of parts reduces the cost per unit. For example, if the machine setup cost is $500 and the raw material for one product costs $10, the overall machining cost for one part will be $510. But if you need to manufacture 50 identical parts, the cost per part will reduce to $20. As the machine setup costs remain the same, the cost decreases with an increase in the number of required parts.
How can CNC machining costs be effectively reduced?
To minimize CNC machining costs, optimize the design without compromising the product’s functionality. Add radii to internal vertical edges, limit cavity depth, increase wall thickness, and optimize hole sizes and threads. If complexity is unavoidable, convert one complex part into modular components. Additionally, choose essential surface finishes and minimize the number of machine setups for operations.
Conclusion
In the world of manufacturing, various approaches like 3D printing and CNC machining are available. Customers seek cost-effective solutions from manufacturing companies. This article has discussed the factors that influence CNC machining costs and provided tips to minimize expenses.
At Want.Net, we are committed to Design for Manufacturing (DFM) and strive to provide cost-effective CNC machining solutions. Our quotes average 30% lower than those of our competitors. Get an instant quote today and experience our affordable CNC machining services!
Recommended Reads:
- How to Optimize Machining Process Routes
- Bring Your Ideas to Life with Want.Net’s Advanced CNC Machining Services
- 5 Essential Steps for Achieving Perfect Product Delivery in Manufacturing
- Achieving a CNC Model: Tips for Success
- What is High-Speed Machining?
- CNC Cutting vs. Laser Cutting: Which Manufacturing Process is Right for You?
Other Articles You Might Enjoy
- Precision CNC Machining of Steel: High-Volume Production
Precision CNC Machining and High-Volume Production As an integral part of modern manufacturing processes, Precision Computer Numerical Control (CNC) machining brings about unmatched accuracy and consistency in the production of…
- The main factors of workpiece deformation in CNC machining
With the rapid development of science and technology, many fields have already reached a near-saturated state. The market competition in the field of CNC machining is becoming more and more…
- Material Versatility in CNC Machining: From Titanium to Thermoplastics
Introduction to CNC Machining CNC machining stands as a cornerstone in the manufacturing sector, enabling the precise creation of parts and components. This process utilizes computer numerical control (CNC) to…