The Importance of the Stress-Strain Curve in CNC Machining
In the world of CNC machining, understanding the stress-strain curve isn’t just a technical necessity—it’s a strategic advantage. When I first dove into the intricacies of material science and machining, I quickly realized how often CNC projects succeed or fail based on choosing the right materials. The stress-strain curve is a fundamental tool that helps us understand how materials respond to forces, and, more importantly, it guides us in selecting and working with materials that fit the exact needs of a project.
So, why does the stress-strain curve matter so much in CNC machining? At its core, the curve illustrates how a material behaves under stress—essentially, how it stretches, bends, or even fractures. For any project, this data helps determine if the material can handle the applied forces, survive the machining process, and maintain its integrity in the final application. When I work on CNC projects, knowing a material’s response to stress helps me tailor machining parameters like feed rate, cutting speed, and tool choice, which ultimately influence the part’s quality and lifespan.
In this article, we’ll dive into the core principles of the stress-strain curve and explore how these principles apply directly to CNC machining. We’ll walk through the essential concepts, examine how different materials react under stress, and discuss real-world applications. By the end, I hope you’ll feel confident about using stress-strain data to make informed choices in CNC machining, whether you’re working with metals, plastics, or specialized alloys. And if you’re looking to optimize your material choices for both performance and cost, this is where it all starts.
Fundamentals of the Stress-Strain Curve
To understand why the stress-strain curve is essential in CNC machining, let’s first dive into the fundamentals of what this curve represents. The stress-strain curve is a graphical representation of a material’s response to applied stress—essentially a “roadmap” of how a material will behave under increasing levels of force. Knowing how to interpret this roadmap is crucial for anyone working in CNC machining, as it directly influences the success of machining processes and the durability of final products.
2.1 What Are Stress and Strain?
Stress and strain are key mechanical properties that tell us how a material reacts under force. Let’s break down each:
Stress (σ) is defined as the force applied per unit area within a material. We calculate stress as:
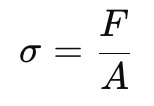
where ( F ) is the force applied and ( A ) is the cross-sectional area of the material.
Strain (ε) is the deformation or change in length that the material experiences relative to its original length, calculated as:
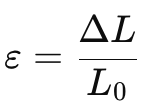
where ( /\L ) is the change in length and ( L_0 ) is the original length.
2.2 Key Regions of the Stress-Strain Curve
When we plot stress against strain, several distinct regions emerge on the graph, each representing a different phase of material behavior:
- Elastic Region: In this initial phase, the material deforms but returns to its original shape once the stress is removed. This region is critical for CNC machining, especially when designing parts that will experience reversible loads.
- Yield Point: This point marks the end of elastic behavior and the beginning of permanent deformation. Knowing the yield point is essential in CNC as it tells us the stress level beyond which the material will not recover its shape.
- Plastic Region: Beyond the yield point, the material undergoes plastic deformation, meaning it won’t return to its original shape even if the stress is removed. Parts machined for this stage often require high precision, as any further stress can result in irreversible changes in dimensions.
- Ultimate Tensile Strength (UTS): The peak point of the curve represents the maximum stress the material can withstand. CNC operators must be cautious when approaching this threshold, as it indicates the material’s maximum load capacity.
- Fracture Point: The endpoint of the curve is where the material ultimately breaks. Knowing this point is crucial for applications involving high-stress environments, as parts need to be machined to stay well below this limit for safety and durability.
2.3 Parameters Derived from the Curve
The stress-strain curve gives us several essential parameters for CNC machining:
- Elastic Modulus (Young’s Modulus): This measures the stiffness of a material, indicating how much it will deform elastically under a given stress. For CNC, a higher modulus often means the material can handle higher loads without deforming.
- Toughness: This measures the area under the curve, representing the material’s ability to absorb energy up to fracture. Tougher materials are often more resistant to cracking under the stress of CNC machining.
- Ductility: This is the material’s capacity to deform plastically before breaking, which is valuable in CNC as it indicates how “forgiving” the material will be to various stresses during machining.
Characteristics of Common Materials on the Stress-Strain Curve
In CNC machining, understanding the stress-strain characteristics of different materials is essential for selecting the right one for the job. Each material’s curve is unique, offering insights into how it will behave under machining stresses. Here, I’ll share an overview of the stress-strain characteristics for common materials like steel, aluminum, and titanium, and explain how these properties impact CNC machining decisions.
3.1 Steel
Steel is one of the most commonly used metals in CNC machining due to its strength and versatility. Its stress-strain curve typically features a clear yield point, followed by a long plastic region, making it relatively easy to predict and control under various loads.
Property | Value Range | CNC Machining Impact |
---|---|---|
Elastic Modulus | 190-210 GPa | High rigidity allows for precise machining with minimal deformation. |
Yield Strength | 250-550 MPa | Steels with high yield strength are suitable for heavy-duty parts. |
Ultimate Strength | 400-700 MPa | Provides high tensile strength for load-bearing applications. |
Ductility | Moderate | Allows for some plastic deformation before fracture, aiding in complex shapes. |
Toughness | High | Absorbs impact energy well, making it resistant to cracking. |
Steel’s high strength and moderate ductility make it ideal for structural and load-bearing CNC machined parts. It holds up well under stress, and with a clearly defined yield point, machinists can push it to high stress levels without risking failure.
3.2 Aluminum
Aluminum is popular in CNC machining due to its lightweight and excellent machinability. Its stress-strain curve typically lacks a clear yield point, but it shows a good balance between strength and ductility.
Property | Value Range | CNC Machining Impact |
---|---|---|
Elastic Modulus | 68-70 GPa | Low modulus makes it more prone to deformation but easier to cut. |
Yield Strength | 50-400 MPa | Offers versatility for parts that need lightweight strength. |
Ultimate Strength | 90-550 MPa | Suitable for lightweight applications requiring moderate strength. |
Ductility | High | High ductility makes it ideal for complex, bendable shapes. |
Toughness | Moderate | Less tough than steel, but suitable for low-impact applications. |
Aluminum’s machinability and high ductility mean it can handle intricate shapes without fracturing, which is beneficial in CNC for parts requiring light but strong material. Its low modulus, however, requires careful parameter control to prevent bending or excessive deformation.
3.3 Titanium
Titanium is prized for its high strength-to-weight ratio and corrosion resistance, but its stress-strain curve reveals a challenging material for CNC machining. It has high strength and low ductility, making it prone to work hardening and tool wear.
Property | Value Range | CNC Machining Impact |
---|---|---|
Elastic Modulus | 110-120 GPa | Moderately stiff, can handle stress but needs controlled feed rates. |
Yield Strength | 550-900 MPa | High yield strength allows for high-stress applications. |
Ultimate Strength | 800-950 MPa | Excellent tensile strength suitable for critical parts. |
Ductility | Low | Low ductility makes it prone to cracking if stressed too much. |
Toughness | High | Good toughness, suitable for impact-prone applications. |
Titanium’s high strength and toughness are ideal for aerospace and medical applications where reliability under stress is essential. However, CNC machining titanium requires specialized tooling and techniques to prevent deformation, overheating, and premature tool wear.
3.4 Other Common CNC Materials
Other materials like brass, copper, and various plastics each have unique stress-strain characteristics, making them suitable for different CNC applications:
Material | Yield Strength (MPa) | Ductility | Toughness | CNC Machining Suitability |
---|---|---|---|---|
Brass | 100-300 | Moderate | Moderate | Good for decorative and precision parts. |
Copper | 70-210 | High | Moderate | Excellent thermal/electrical conductivity, easy to machine. |
Nylon | 35-90 | High | Low | Ideal for lightweight, non-metallic parts. |
POM (Delrin) | 60-80 | Moderate | Low | Great for precise plastic components. |
Each material’s unique stress-strain characteristics help us understand its limits and strengths in CNC machining. For example, brass’s moderate yield strength and ductility make it easy to shape, while POM’s precision allows for fine-tuned plastic parts.
Relationship Between the Stress-Strain Curve and CNC Machining Parameters
The stress-strain curve doesn’t just help us choose materials—it guides us in selecting the optimal CNC machining parameters for each material. Understanding how a material responds to stress allows us to make informed decisions on cutting speed, feed rate, and depth of cut, which directly impact the efficiency, quality, and durability of the final product.
4.1 Importance of Selecting Machining Parameters Based on the Stress-Strain Curve
When I first began working with stress-strain curves in machining, I was surprised by how much machining efficiency and product quality depended on selecting the right parameters. By understanding where a material’s elastic and plastic limits are, we can tailor machining conditions to avoid pushing a material beyond its safe limits. Here’s why each key parameter matters:
- Cutting Speed: Faster speeds can lead to higher temperatures and greater stress, especially in materials with low ductility. High cutting speeds may exceed a material’s yield point, causing unwanted plastic deformation or even fracturing.
- Feed Rate: Adjusting the rate at which material is fed to the cutter helps control stress. Lower feed rates generally reduce the force applied per pass, which is essential for materials with low toughness.
- Depth of Cut: Deeper cuts introduce more stress. For tough, brittle materials, even a slight increase in cut depth can cause cracking or tool wear. The depth of cut should remain within the elastic region of the stress-strain curve to prevent permanent deformation.
4.2 How the Stress-Strain Curve Affects Cutting Speed, Feed Rate, and Depth of Cut
To better illustrate how these parameters are adjusted based on material properties, I’ve created a table outlining general recommendations for common materials.
Material | Cutting Speed | Feed Rate | Depth of Cut | Stress-Strain Considerations |
---|---|---|---|---|
Steel | Moderate to High | Moderate | Shallow to Moderate | Good toughness, but caution with high speeds to avoid overheating. |
Aluminum | High | High | Moderate | Low modulus allows higher speeds, but care with feed rate to prevent bending. |
Titanium | Low to Moderate | Low | Shallow | Prone to work hardening; keep speeds low to prevent tool wear. |
Brass | High | High | Moderate | Highly machinable; responds well to high speeds. |
Copper | Moderate | Low to Moderate | Shallow to Moderate | Conductive; avoid high speeds to reduce heat buildup. |
POM (Delrin) | Moderate to High | Moderate | Moderate | Plasticity allows flexibility with feed rates and speeds. |
This table is a starting point, but precise adjustments often depend on the material batch, CNC machine, and tooling. When machining high-toughness materials like titanium, I find that low cutting speeds and shallow depths extend tool life and prevent unwanted stress accumulation. In contrast, for materials like aluminum, high cutting speeds work well as long as feed rates are balanced to avoid excessive deflection.
4.3 Minimizing Deformation and Breakage Using Stress-Strain Data
Materials with low ductility, such as titanium, are at higher risk of cracking during machining if the stress-strain limits are exceeded. Here are some tips based on the stress-strain curve to minimize deformation and prevent breakage:
- Stay Below the Yield Point: For materials prone to plastic deformation, keeping stress within the elastic region prevents permanent changes in shape. CNC operators can refer to the yield strength on the stress-strain curve to set conservative feed rates and depth of cut.
- Control Temperature: Higher temperatures can increase material ductility but may reduce strength. For materials with steep stress-strain curves, such as brass, maintaining lower machining temperatures preserves material integrity.
- Reduce Vibrations: Vibrations can induce unnecessary stress, especially in low-toughness materials like POM. Precision setups and stabilized fixtures are essential to keep the material within its elastic range on the stress-strain curve.
By leveraging the stress-strain curve, I’ve found that I can precisely tailor machining processes to the material’s strengths and weaknesses, resulting in improved part quality, reduced waste, and lower tool wear.
Case Studies Across Industries
Understanding how different industries apply the stress-strain curve in CNC machining helps us see its real-world impact. Each industry has unique demands, and the material choice, as well as the machining parameters, are often driven by stress-strain data. Here, I’ll share examples from automotive, aerospace, medical equipment, and research/education sectors to illustrate these applications.
5.1 Automotive and Aerospace Industry
In the automotive and aerospace industries, materials are chosen to meet specific requirements for strength, weight, and durability. The stress-strain curve plays a critical role in helping engineers and CNC machinists determine if a material can withstand high-stress environments while remaining lightweight.
- Case Example: Aircraft Structural Components
In aerospace, parts such as landing gear and wing spars are made from high-strength, lightweight materials like titanium and aluminum alloys. Using the stress-strain curve, engineers can evaluate each material’s elastic and plastic regions to set appropriate machining parameters, ensuring the components can handle heavy loads without deforming. - Case Example: Car Engine Parts
Automotive engine components, such as pistons and connecting rods, require high toughness to withstand extreme temperatures and cyclic loading. By analyzing the stress-strain curve, machinists can fine-tune parameters to avoid inducing stress that could lead to fatigue and cracking over time. For example, titanium alloys might be chosen for their high yield strength and moderate ductility, providing the right balance of strength and flexibility.
Material | Application | Key Stress-Strain Properties | Machining Considerations |
---|---|---|---|
Titanium Alloy | Aircraft landing gear | High strength, low ductility | Low speeds, shallow cuts to prevent tool wear |
Aluminum Alloy | Aerospace structural parts | Moderate strength, high ductility | High speeds with balanced feed rates to reduce deflection |
Cast Iron | Engine blocks (automotive) | High strength, low toughness | Moderate speeds; care to avoid sudden stress |
5.2 Medical Equipment Industry
Medical devices require precise, biocompatible materials, often with unique stress-strain properties. Materials like stainless steel, titanium, and certain polymers are popular in this sector due to their specific mechanical characteristics.
- Case Example: Titanium Implants
Titanium’s high strength-to-weight ratio and excellent corrosion resistance make it ideal for implants. CNC machinists rely on the stress-strain curve to avoid exceeding the yield strength, as implants must maintain precise dimensions and surface finish. The material’s low ductility means operators need to use low cutting speeds and shallow depths to prevent cracking. - Case Example: Surgical Instruments Made from Stainless Steel
Stainless steel is favored for surgical instruments due to its durability and corrosion resistance. Using stress-strain data, machinists can determine optimal cutting parameters to maintain edge sharpness and avoid micro-cracking, which can compromise performance during surgery.
Material | Application | Key Stress-Strain Properties | Machining Considerations |
---|---|---|---|
Titanium | Implants | High strength, low ductility | Shallow cuts to prevent cracking |
Stainless Steel | Surgical tools | High toughness, moderate ductility | High feed rates to maintain sharpness and reduce wear |
PEEK (polymer) | Spinal cages | Moderate strength, high ductility | Moderate speeds, shallow cuts for precision |
5.3 Research and Education
The stress-strain curve is a fundamental concept taught in engineering and material science programs. For CNC machining, this data allows students and researchers to understand how materials respond to stress and adjust their techniques accordingly.
- Case Example: Testing Material Performance in Labs
In educational labs, materials like steel and aluminum are often tested for strength and elasticity using CNC machines. The stress-strain curve helps students learn how different materials respond under controlled conditions, providing a practical foundation for real-world applications. - Case Example: Experimental CNC Machining of New Alloys
Research institutes often work with experimental alloys that offer unique stress-strain characteristics. CNC operators use this data to set machining parameters carefully, as these materials may exhibit unexpected behaviors under stress.
Material | Application | Key Stress-Strain Properties | Machining Considerations |
---|---|---|---|
Experimental Alloy | Research in advanced materials | Varies by alloy; often unpredictable | Conservative speeds and feed rates |
Aluminum | Educational material testing | High ductility, low strength | High speeds to observe plastic deformation |
Stainless Steel | Experimental surgical tools | High strength, high toughness | Low speeds to minimize stress during fine-tuning |
These case studies illustrate how the stress-strain curve is applied across various industries to ensure that CNC-machined parts meet both performance and safety standards. From aerospace components to medical implants, stress-strain data provides machinists with critical insights to achieve optimal results.
Role of the Stress-Strain Curve in Material Development
The stress-strain curve isn’t only essential for machining existing materials; it’s also invaluable in the development of new materials. Whether developing advanced alloys for high-stress applications or biocompatible polymers for medical devices, understanding the stress-strain behavior helps material scientists and engineers assess if a material will perform as expected in real-world conditions. In CNC machining, this is crucial because any new material must be compatible with the machining process to ensure a stable, efficient workflow.
6.1 Using the Stress-Strain Curve to Test New Materials
When testing new materials, scientists and engineers use the stress-strain curve to determine core properties like yield strength, elasticity, and toughness. This initial testing phase gives a clear indication of whether a material can handle the machining process without failure or excessive wear.
For example, let’s say a research team is developing a new titanium-aluminum alloy for lightweight automotive components. The team can use the stress-strain curve to:
- Assess the alloy’s yield strength and elastic modulus to determine if it can handle the operational stresses expected in vehicle parts.
- Evaluate the toughness to ensure that the material can withstand potential impacts during machining without cracking.
- Analyze the ductility to predict whether the material will be machinable or if it risks fracturing.
6.2 Challenges in New Material Selection for CNC Machining
Working with new materials can be challenging because their properties are often unpredictable, which makes choosing suitable machining parameters difficult. In my experience, using stress-strain data helps to mitigate these challenges by providing a roadmap for parameter adjustments. Here are some common challenges in CNC machining with new materials:
- Tool Wear and Breakage: New materials often have unknown hardness and toughness, which can quickly wear down or even break tools. By referring to the material’s stress-strain curve, machinists can adjust feed rates and cutting depths to minimize these risks.
- Thermal Instability: Some experimental materials may behave unpredictably under heat, leading to deformations or phase changes. Stress-strain data at different temperatures can help CNC machinists understand if the material will hold up under heat or if additional cooling measures are required.
- Surface Finish Quality: The stress-strain curve can also guide operators in achieving a consistent surface finish. Materials that exhibit significant plastic deformation are more likely to produce smoother finishes, while harder, brittle materials require precision control to avoid rough or uneven surfaces.
Material Type | Key Stress-Strain Challenges | CNC Machining Strategy |
---|---|---|
New Metal Alloys | Unknown toughness and hardness | Conservative cutting speeds, frequent tool inspection |
Advanced Polymers | Thermal instability | Controlled temperatures, potentially modified cooling systems |
Biocompatible Materials | Sensitive to stress and heat | Use of gentle feed rates, shallow cuts to preserve integrity |
6.3 Benefits of Incorporating the Stress-Strain Curve in Material Development
Incorporating the stress-strain curve into material development has numerous benefits, particularly for CNC applications:
- Predictive Machining Parameters: By analyzing stress-strain data, CNC machinists can anticipate the best parameters for a new material, minimizing trial and error and reducing wastage.
- Enhanced Product Performance: Knowing a material’s limits allows manufacturers to create parts that perform well under stress without risking structural integrity.
- Lower Production Costs: When we understand the stress-strain behavior of a material, it’s easier to choose efficient machining processes that reduce tool wear and avoid unnecessary expenses.
By leveraging the stress-strain curve during the material development phase, CNC operators and engineers can more effectively integrate new materials into their production workflows, paving the way for innovations without compromising on efficiency or safety.
Methods to Improve Material Machinability
Improving a material’s machinability is often essential to achieving high-quality results in CNC machining, particularly when working with materials that exhibit challenging stress-strain characteristics, such as low ductility or high hardness. Several methods can be employed to enhance machinability, allowing us to achieve smoother cuts, reduce tool wear, and maintain the material’s integrity throughout the machining process.
7.1 Heat Treatment to Enhance Stress-Strain Response
Heat treatment is a commonly used method to modify a material’s mechanical properties, including its stress-strain behavior. By adjusting the material’s hardness, ductility, and strength, we can improve its response to machining stresses and make it more workable. Here’s how different types of heat treatment affect machinability:
- Annealing: This process involves heating a material to a specific temperature and then cooling it slowly. Annealing softens the material, increases ductility, and relieves internal stresses. For metals like steel, annealing can make them easier to machine by reducing brittleness and enhancing the plastic region on the stress-strain curve.
- Tempering: Tempering is commonly used for hardened steels to decrease brittleness while retaining strength. This process lowers the hardness slightly, which can prevent cracking during machining. CNC machinists often find that tempered materials produce smoother finishes with less risk of fracture.
- Case Hardening: This process hardens only the outer surface of the material, leaving the core softer. For components requiring wear resistance on the surface and flexibility at the core, case hardening is ideal. By altering the stress-strain behavior at the surface, machinists can maintain a durable, machinable core for critical parts.
Heat Treatment Type | Effect on Stress-Strain Curve | Benefits for CNC Machining |
---|---|---|
Annealing | Increases ductility, lowers strength | Reduces brittleness, easier cutting, minimizes cracking |
Tempering | Decreases brittleness | Improves toughness, reduces risk of tool wear |
Case Hardening | Hard outer surface, soft core | Ideal for wear-resistant surfaces with machinable core |
7.2 Surface Treatment to Enhance Durability and Toughness
Surface treatments can improve a material’s durability and toughness, making it more resistant to wear and environmental factors. While these treatments may not change the overall stress-strain characteristics significantly, they can protect against surface stresses that arise during CNC machining.
- Shot Peening: This process bombards the material surface with small particles, inducing compressive stresses that enhance surface toughness. Shot peening is particularly useful for materials that might crack or deform easily under stress.
- Polishing: Polishing smoothens the surface, reducing friction between the tool and material. It’s often applied to softer metals and plastics, which may otherwise exhibit rough finishes. A polished surface can improve the overall machining experience by reducing material drag and enhancing tool performance.
Surface Treatment | Effect on Machinability | Application Examples |
---|---|---|
Coating | Reduces friction, enhances wear resistance | Suitable for high-speed cutting with reduced tool wear |
Shot Peening | Increases surface toughness | Ideal for aerospace and automotive parts |
Polishing | Smoothens surface, lowers friction | Useful for precise components with high surface finish |
7.3 Adjusting Machining Parameters Based on Stress-Strain Data
Aside from modifying the material, adjusting CNC parameters based on the material’s stress-strain curve is a practical way to improve machinability. Here are key parameter adjustments to consider:
- Lower Cutting Speed: For materials prone to deformation, reducing the cutting speed helps keep stress levels within the elastic region, minimizing the risk of cracking or excessive wear.
- Optimized Feed Rate: Materials with low toughness require careful feed rate adjustments to prevent abrupt stress increases. A slower feed rate can reduce the force on the tool and prevent deformation.
- Shallow Depth of Cut: When working with brittle materials, using a shallow depth of cut prevents sudden stress spikes, keeping the material within its safe load limits.
By using heat treatment, surface treatment, and parameter adjustments based on the stress-strain curve, CNC machinists can optimize the material’s response under machining conditions. This combination of techniques ultimately enhances productivity, minimizes waste, and ensures a smooth workflow.
FAQ
The stress-strain curve provides critical insights for CNC machinists, engineers, and material scientists, helping them optimize machining processes and material selection. Here are some of the most frequently asked questions regarding the application of the stress-strain curve in CNC machining:
Q1: How does the stress-strain curve help in assessing machinability?
The stress-strain curve helps us understand a material’s elasticity, plasticity, and ultimate strength, which are crucial for selecting appropriate machining parameters. By identifying a material’s yield point, we can ensure that machining processes don’t exceed the elastic limit, preventing permanent deformation or cracking.
Q2: Can the stress-strain curve help in determining cutting speed and feed rate?
Yes, absolutely. By examining a material’s toughness and ductility on the stress-strain curve, machinists can set cutting speeds and feed rates that minimize stress and maintain the material’s structural integrity. For example, materials with low toughness benefit from lower cutting speeds and feed rates to avoid excessive stress.
Q3: How do I determine if a material will withstand high-stress environments based on its stress-strain curve?
The ultimate tensile strength (UTS) on the stress-strain curve indicates the maximum stress a material can withstand before breaking. Materials with high UTS are more suitable for high-stress applications. Additionally, materials with a significant plastic region (high ductility) can absorb stress and strain without fracturing, making them more resilient under high-stress conditions.
Q4: How does heat treatment affect a material’s stress-strain characteristics?
Heat treatment can alter the material’s hardness, ductility, and strength, which are directly represented on the stress-strain curve. For instance, annealing softens the material, increasing its ductility and allowing for easier machining. Hardening, on the other hand, increases strength but reduces ductility, making it more challenging to machine.
Q5: Why is it important to keep machining stresses within the elastic region of the stress-strain curve?
Operating within the elastic region prevents permanent deformation, ensuring the material returns to its original shape once the stress is removed. If the stress exceeds the elastic limit, the material enters the plastic region, where deformations become irreversible, potentially leading to defects in the machined part.
Q6: Can the stress-strain curve guide surface finishing techniques in CNC machining?
Yes. The stress-strain curve can indicate if a material is prone to cracking or stress accumulation during finishing. For materials with low ductility, polishing or shot peening may be necessary to reduce surface stress and improve durability, whereas materials with higher toughness may tolerate more aggressive surface treatments.
Q7: How does the curve help in choosing materials for high-precision parts?
For high-precision parts, materials with a high modulus of elasticity (indicating stiffness) and moderate ductility are often preferred. The stress-strain curve allows us to identify materials that maintain dimensional accuracy under stress, reducing the risk of deformation in high-precision components.
Q8: What role does the fracture point on the stress-strain curve play in material selection?
The fracture point shows the maximum stress the material can endure before breaking, which is critical for safety. In applications where parts undergo cyclic or extreme loading, knowing the fracture point helps ensure that the material can handle the expected stress levels without risk of sudden failure.
Q9: How can CNC machinists use the stress-strain curve to reduce tool wear?
Materials with high toughness and low ductility typically require low cutting speeds and shallow depths of cut to reduce tool wear. The stress-strain curve provides machinists with insights into these material properties, allowing them to adjust machining parameters to prolong tool life.
Q10: How does temperature impact the stress-strain behavior of materials during CNC machining?
Temperature can alter a material’s yield strength, ductility, and elasticity. Higher temperatures often increase ductility, which may ease machining but reduce overall strength. By analyzing temperature-dependent stress-strain data, machinists can adjust cooling methods and parameters to optimize performance.
Q11: How does ductility on the stress-strain curve affect machining complexity?
High ductility allows for more plastic deformation, making materials easier to machine into complex shapes. Materials with low ductility, however, are prone to cracking and require careful handling with lower speeds and feed rates.
Q12: Can the stress-strain curve help in predicting material fatigue?
Yes, the stress-strain curve provides data on how a material behaves under repeated stress, helping predict potential fatigue failures. Materials with low plastic deformation are less forgiving under cyclic stress, while ductile materials may absorb more energy before failing.
Q13: How do I identify the elastic modulus on the stress-strain curve, and why is it important for CNC machining?
The elastic modulus is the slope of the initial linear part of the curve, representing the material’s stiffness. In CNC machining, materials with a higher elastic modulus resist deformation better, which is crucial for parts that require precise dimensional stability.
Q14: What does a “steep” or “shallow” stress-strain curve mean for CNC machining?
A steep curve in the elastic region indicates high stiffness, while a shallow curve suggests lower stiffness. Stiffer materials (steep curve) are less prone to deflection and more suitable for precise machining, while materials with a shallow curve may require adjusted machining parameters to avoid bending.
Q15: Why might a machinist need to adjust parameters based on a material’s toughness?
Toughness, represented by the area under the stress-strain curve, indicates how much energy a material can absorb before failure. Machinists may use lower feed rates and cutting depths for materials with low toughness to prevent excessive stress accumulation and avoid failure during machining.
Other Articles You Might Enjoy
- Can Precision CNC Machining Compensate for Material Weaknesses in High-Stress Applications?
The Role of CNC Machining in Material Enhancement In engineering applications where materials are subjected to high stress, the choice and treatment of materials are crucial for the integrity and…
- Analyzing Residual Stress in Aluminum Alloy CNC Machining Parts
Residual stress is a crucial factor affecting the performance and durability of aluminum alloy components in aerospace applications. These parts are often large, thin-walled, and complex in structure, making them…
- How Yield Stress Impacts CNC Machining and Material Performance
Introduction to Yield Stress and Its Importance in CNC Machining When we think about machining and materials, yield stress is one of the most crucial properties to understand. Yield stress…
- Precision CNC Machining of Steel: High-Volume Production
Precision CNC Machining and High-Volume Production As an integral part of modern manufacturing processes, Precision Computer Numerical Control (CNC) machining brings about unmatched accuracy and consistency in the production of…
- CNC Machining for Consumer Electronics: Material Selection for Heat Dissipation
Introduction to CNC Machining in Consumer Electronics CNC machining stands as a pivotal technology in the manufacturing of consumer electronics, offering precision and efficiency in producing components. This process involves…
- Understanding Material Machinability in CNC Machining: What Every Engineer Should Know
Introduction When it comes to CNC machining, the material you choose can make or break your project. Whether you're working on a high-precision component or a bulk order of simple…