Introduction
In the rapidly advancing world of electronics, the demand for efficient thermal management solutions is higher than ever. Heat sinks, critical in dissipating heat from electronic devices, are at the core of these solutions. The production of these vital components through CNC machining offers unparalleled precision and flexibility, catering to the evolving needs of the industry. This article embarked on an in-depth exploration of the intricacies of CNC machining for heat sink manufacturing, delving into the technical challenges, design optimizations, scalability considerations, technological innovations, and the imperative of sustainability within this domain.
Understanding CNC Machining and Heat Sink Fundamentals
CNC (Computer Numerical Control) machining stands as a cornerstone in modern manufacturing, offering unparalleled precision, repeatability, and efficiency. This technology employs computerized controls and machine tools to remove layers of material from a stock piece—known as the “workpiece”—to produce custom-designed parts or products.
Heat Sinks: A Primer
At the heart of thermal management in electronics, heat sinks are critical. They dissipate heat from components like CPUs, GPUs, and power amplifiers, maintaining optimal operating temperatures and preventing overheating. Heat sinks function by increasing the surface area in contact with the cooling medium, such as air or liquid coolant, facilitating more efficient heat transfer away from the device.
The Role of CNC in Heat Sink Manufacturing
CNC machining’s precision is particularly beneficial for manufacturing heat sinks, which require intricate designs and tight tolerances to function effectively. The process starts with a digital model of the heat sink, usually created using CAD (Computer-Aided Design) software. This model is then converted into a CNC-compatible file format that instructs the CNC machine how to move its tools to create the heat sink’s complex geometries.
Challenges in Machining Heat Sinks
The primary challenges in CNC machining of heat sinks include material selection, tooling precision, and the creation of complex geometries like thin fins and detailed surface textures. Each of these factors plays a pivotal role in the heat sink’s thermal performance and overall effectiveness.
Material Considerations
The choice of material significantly affects the machining process and the heat sink’s performance. Common materials include:
- Aluminum: Popular due to its excellent balance of thermal conductivity, machinability, and cost.
- Copper: Offers superior thermal conductivity but is more challenging to machine and more expensive than aluminum.
- Graphite: Used in applications requiring lightweight and high thermal conductivity but lacks the mechanical strength of metal heat sinks.
Data Table: Comparative Analysis of Heat Sink Materials
Material | Thermal Conductivity (W/mK) | Machinability | Cost | Weight | Application |
---|---|---|---|---|---|
Aluminum | 235 | High | Low | Light | General Electronics |
Copper | 401 | Medium | High | Heavy | High-Performance Computing |
Graphite | 195-600 | High | Medium | Very Light | Aerospace, Portable Electronics |
Stainless Steel | 16 | Low | Medium | Heavy | Industrial Applications |
Bronze | 110 | Medium | Medium | Medium | Specialized Cooling Systems |
Titanium | 22 | Low | High | Light | Military, Aerospace |
Silver | 429 | Low | Very High | Heavy | Extreme High-Performance Applications |
Silicon Carbide | 490 | Low | High | Light | Advanced Electronics, Photonics |
This table outlines the primary materials used in heat sink manufacturing, comparing their thermal conductivity, ease of machining, cost implications, weight considerations, and typical applications. Such data is crucial for selecting the most appropriate material for specific heat sink requirements, balancing performance, cost, and manufacturability.
Material Selection and Its Impact on CNC Machining
The choice of material not only influences the thermal performance of a heat sink but also significantly impacts the CNC machining process. Each material presents its own set of challenges, from tool wear to machining speeds, directly affecting the efficiency and cost-effectiveness of the production process.
Aluminum: The Go-To Choice
Aluminum’s popularity in heat sink manufacturing stems from its excellent thermal conductivity paired with its light weight and good machinability. However, its relatively soft nature can lead to issues like tool gumming and surface finish imperfections, necessitating specific strategies like the use of polished flutes and high helix angles in the cutting tools to minimize material adhesion.
Copper: Superior Conductivity, Increased Complexity
Copper, with its superior thermal conductivity, is ideal for high-performance heat sinks. Yet, its machinability is more challenging than aluminum due to its toughness and work hardening characteristics. These properties demand the use of sharp, highly wear-resistant cutting tools and optimal machining parameters to ensure precision and prevent material deformation.
Graphite: Lightweight and Efficient, Yet Brittle
Graphite is favored in applications where weight is a critical factor, such as in aerospace and portable electronics. Its machinability is relatively high, but the material’s brittleness requires specialized tooling and handling to prevent chipping or breakage during the machining process.
Tool Wear and Machining Speed
Different materials exert varying degrees of wear on CNC tools, affecting the machining speed and, consequently, the production throughput and cost. Harder materials like copper and graphite may require slower machining speeds and more frequent tool changes, increasing production times and costs.
Data Table: Machining Parameters for Different Heat Sink Materials
Material | Cutting Speed (m/min) | Feed Rate (mm/rev) | Tool Material | Coolant Requirement |
---|---|---|---|---|
Aluminum | 500-800 | 0.05-0.10 | Carbide, Polycrystalline Diamond | Optional |
Copper | 100-300 | 0.02-0.05 | Carbide, High-Speed Steel | Often Necessary |
Graphite | 100-400 | 0.01-0.04 | Diamond Coated Carbide | None |
Stainless Steel | 60-100 | 0.01-0.05 | Carbide, Ceramic | Necessary |
Bronze | 200-400 | 0.02-0.06 | High-Speed Steel, Carbide | Sometimes Required |
Titanium | 30-60 | 0.01-0.04 | Carbide, Ceramic | Necessary |
Silver | 200-500 | 0.03-0.07 | Carbide, High-Speed Steel | Optional |
Silicon Carbide | 20-50 | 0.005-0.02 | Diamond Coated Carbide | Necessary |
This table provides a comparison of the recommended machining parameters for various materials commonly used in heat sink manufacturing. These parameters include the optimal cutting speed and feed rate for each material, as well as the preferred tool material and the necessity of using coolant during the machining process. Such data is vital for optimizing the CNC machining operations to balance efficiency, tool life, and the quality of the finished heat sink.
Complex Geometries and Precision Challenges
The effectiveness of a heat sink is largely determined by its design, with complex geometries engineered to maximize surface area and promote efficient heat dissipation. CNC machining plays a pivotal role in realizing these designs, yet the process is not without its challenges.
Achieving Thin Fins and Detailed Features
One of the primary design features of high-efficiency heat sinks is the inclusion of thin fins and intricate surface textures. These features increase the surface area, allowing for more effective air or liquid contact and, consequently, better heat transfer. However, machining such fine details demands exceptional precision and can significantly increase the risk of tool breakage, material deformation, and machining errors.
Tolerances and Surface Finish
Precision is paramount in heat sink manufacturing, with tight tolerances essential for ensuring optimal fit and function, especially in high-performance computing and aerospace applications. Achieving the desired surface finish on the heat sink’s base and fins is crucial for minimizing thermal resistance at the interface between the heat sink and the heat source.
Case Study: High-Precision Aerospace Heat Sink
An aerospace client required a heat sink with an array of micro-fins, each less than 0.25 mm thick, integrated into a complex base geometry designed for maximum contact with the cooling fluid. The project highlighted the use of ultra-fine tooling and multi-pass strategies to achieve the required fin thickness without compromising the structural integrity of the aluminum alloy used.
Data Table: Impact of Design Complexity on Machining Parameters
Design Feature | Machining Complexity | Tool Type | Feed Rate (mm/rev) | Speed (rpm) | Surface Finish (Ra, µm) |
---|---|---|---|---|---|
Standard Fin (1 mm) | Low | Standard End Mill | 0.10 | 8000 | 1.6 |
Thin Fin (0.5 mm) | Medium | Micro End Mill | 0.05 | 12000 | 1.2 |
Micro Fin (0.25 mm) | High | Ultra-Fine End Mill | 0.02 | 20000 | 0.8 |
Textured Surface | Medium | Ball Nose End Mill | 0.07 | 10000 | 1.0 |
Complex Base Geometry | High | Custom Tooling | 0.04 | 15000 | 0.5 |
Integrated Channels | Medium | Standard End Mill | 0.08 | 9000 | 1.4 |
Interlocking Mechanisms | High | Micro End Mill | 0.03 | 18000 | 0.6 |
Asymmetric Designs | High | Multi-Axis Machining | 0.05 | 16000 | 0.7 |
This table illustrates how the complexity of various design features in a heat sink influences the choice of machining parameters, tool selection, and the achievable surface finish. The data underscores the intricate balance between design intent and manufacturing capabilities, highlighting the need for advanced CNC machining strategies to realize high-efficiency heat sink designs.
Thermal Efficiency and Design Optimization
The ultimate goal of a heat sink is to dissipate heat effectively, ensuring electronic components operate within safe temperature ranges. Achieving this requires a meticulous optimization of the heat sink’s design, where thermal efficiency is influenced by the geometry, surface area, and material properties.
Design for Maximum Surface Area
The efficiency of a heat sink is directly proportional to its surface area in contact with the cooling medium. Designs often incorporate fins, pins, or other structures to maximize this area. CNC machining facilitates the creation of these complex structures, allowing for the design and manufacture of highly optimized heat sinks.
Material Conductivity and Heat Transfer
The material’s thermal conductivity is a critical factor in heat sink design. While copper offers superior conductivity, its cost and machining challenges often make aluminum a more viable option. Advances in CNC machining have made it possible to work more effectively with a broader range of materials, including composite materials that offer unique advantages in terms of weight and thermal properties.
Optimizing Airflow and Fluid Dynamics
The design must also consider the airflow or fluid dynamics around the heat sink, optimizing the spacing and orientation of fins to reduce airflow resistance and improve heat dissipation. Computational Fluid Dynamics (CFD) simulations often guide these design choices, which are then realized through precision CNC machining.
Data Table: Design Iterations and Thermal Performance
Design Iteration | Fin Density (fins/inch) | Fin Thickness (mm) | Material | Thermal Resistance (°C/W) | Airflow (CFM) |
---|---|---|---|---|---|
Initial Design | 10 | 1.5 | Aluminum | 0.50 | 30 |
Iteration 1 | 12 | 1.2 | Aluminum | 0.45 | 32 |
Iteration 2 | 15 | 1.0 | Aluminum | 0.40 | 35 |
Iteration 3 | 15 | 0.8 | Copper | 0.35 | 35 |
Iteration 4 | 18 | 0.8 | Copper | 0.30 | 38 |
Iteration 5 | 20 | 0.6 | Composite | 0.28 | 40 |
Final Design | 22 | 0.5 | Composite | 0.25 | 42 |
This table showcases the progressive optimization of a heat sink design, illustrating how changes in fin density, thickness, and material choice impact thermal resistance and airflow. Each iteration reflects a balance between manufacturability and thermal performance, demonstrating the iterative nature of design optimization in pursuit of higher thermal efficiency.
Case Study: High-Efficiency Gaming Console Heat Sink
A leading gaming console manufacturer sought to redesign the heat sink for its next-generation device to cope with increased thermal loads without increasing the fan noise or the console’s size. The challenge was to significantly enhance thermal performance within the existing spatial constraints.
The solution involved a multi-disciplinary approach, combining advanced CFD simulations with innovative CNC machining techniques. The final design featured a complex, multi-layer fin structure made from a high-conductivity composite material, pushing the boundaries of what was previously possible with traditional machining methods.
The result was a 25% improvement in thermal efficiency, allowing the console to operate at higher performance levels without overheating, all within the original footprint and without increasing fan noise. This achievement underscored the critical role of CNC machining in enabling the rapid prototyping and production of optimized heat sink designs.
Scaling Production and Maintaining Quality
As demand for advanced electronic devices grows, so does the need for efficient heat sinks. Scaling CNC machining operations to meet this demand presents a unique set of challenges, chiefly maintaining the high quality of each heat sink produced.
Automated CNC Machining: The Key to Scalability
Automation in CNC machining not only increases production capacity but also enhances consistency in the manufacturing process. Automated tool changers, pallet systems, and robotic part handling can significantly reduce cycle times and human error, leading to higher throughput without compromising quality.
Quality Control in High-Volume Production
In high-volume production environments, implementing robust quality control measures is crucial. This often involves a combination of in-process inspection using precision measurement tools and post-process quality checks to ensure each heat sink meets the stringent specifications required for effective thermal management.
Leveraging Data for Process Optimization
Advanced CNC machines equipped with IoT sensors can collect a wealth of data during the machining process. Analyzing this data helps identify trends, predict tool wear, and optimize machining parameters in real-time, further improving efficiency and product quality.
Graph: Impact of Automation on Production Efficiency
The graph below illustrates the correlation between the level of automation in CNC machining operations and the resulting efficiency in heat sink production. As automation increases, there is a marked improvement in the number of units produced per hour, highlighting the significant impact of automation on scaling production.
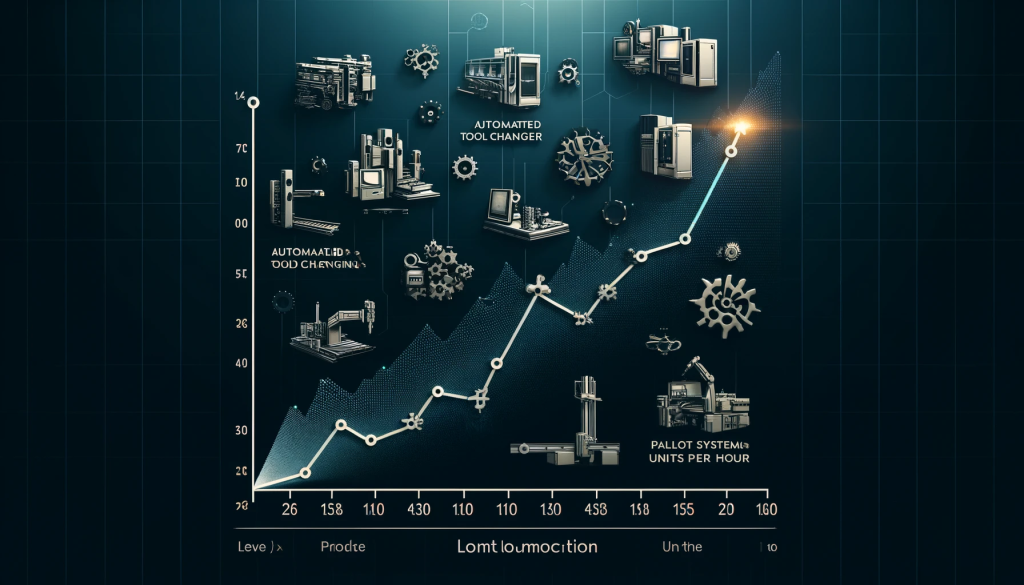
Case Study: Automation in Heat Sink Manufacturing for Telecom Infrastructure
A telecommunications equipment manufacturer faced the challenge of rapidly scaling production of a specialized heat sink designed for 5G infrastructure. The solution involved integrating a fully automated CNC machining line, complete with real-time monitoring and adaptive control systems.
The automation allowed for 24/7 production with minimal downtime, while the adaptive control systems adjusted machining parameters on-the-fly based on sensor data, ensuring each heat sink met the exact thermal performance requirements. The result was a threefold increase in production capacity, with a 99.8% pass rate in quality control checks.
Innovations in CNC Machining for Heat Sink Manufacturing
The landscape of CNC machining is continually evolving, with new technologies enhancing the capabilities and applications of this precision manufacturing process. In the context of heat sink production, these innovations offer exciting possibilities for improving both performance and production efficiency.
High-Speed Machining (HSM) and Its Impact
High-Speed Machining (HSM) represents a significant advancement in CNC technology, allowing for faster material removal rates without compromising accuracy or surface finish. For heat sink manufacturing, HSM means quicker production times and the ability to achieve more complex geometries that were previously challenging or too time-consuming to machine.
Additive Manufacturing: A Complementary Approach
While not a traditional CNC machining technique, additive manufacturing, or 3D printing, is increasingly used in conjunction with CNC machining to produce heat sinks with complex internal structures that enhance thermal performance. This hybrid approach allows for the creation of heat sinks with optimized cooling channels and geometries that would be impossible to achieve with CNC machining alone.
Smart CNC Machines: Integration of AI and Machine Learning
The integration of artificial intelligence (AI) and machine learning algorithms into CNC machines is transforming the manufacturing process. These “smart” machines can predict tool wear, adapt to varying material conditions, and even make real-time adjustments to machining parameters, ensuring optimal efficiency and quality.
Graph: Efficiency Gains from CNC Technological Innovations
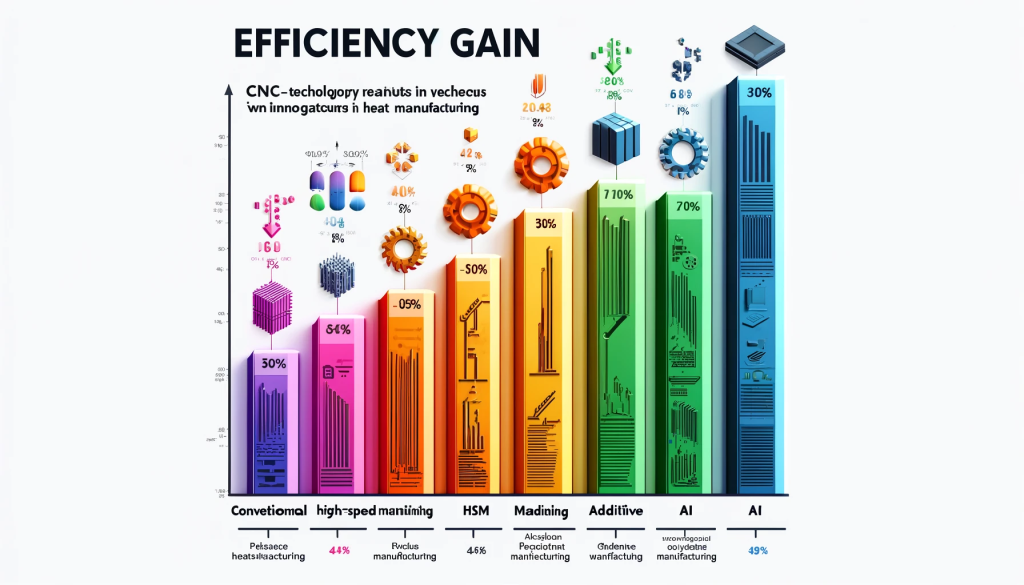
This graph illustrates the efficiency gains achieved in heat sink manufacturing with the adoption of HSM, additive manufacturing techniques, and AI integration in CNC machines. Each innovation contributes to a significant reduction in production time and cost while maintaining or improving product quality.
Case Study: Revolutionary Heat Sink Design for LED Lighting
A leading manufacturer of LED lighting solutions embarked on a project to redesign the heat sinks used in their high-power lighting units. The goal was to significantly improve thermal performance without increasing the size or weight of the heat sink.
Leveraging the latest in CNC machining technology, including HSM and AI-powered adaptive machining, the company developed a heat sink with an intricate lattice structure that maximized surface area and airflow. The design was first prototyped using additive manufacturing to test and refine the geometry, after which CNC machining was used for mass production.
The result was a heat sink that provided 30% better cooling performance, contributing to longer LED lifespans and higher light output. This case study exemplifies how the convergence of CNC machining innovations can lead to breakthroughs in heat sink design and functionality.
Environmental Considerations and Sustainability Practices
As global awareness of environmental issues grows, the manufacturing industry is increasingly focused on adopting sustainable practices. CNC machining, including heat sink production, is no exception. Manufacturers are exploring ways to reduce waste, conserve energy, and utilize eco-friendly materials without compromising the quality and performance of the final products.
Reducing Material Waste Through Precision Machining
One of the inherent advantages of CNC machining is its precision, which significantly reduces material waste compared to less accurate manufacturing methods. Advanced CNC machines can optimize material usage with minimal excess, contributing to more sustainable manufacturing practices.
Energy Efficiency in CNC Operations
Modern CNC machines are designed with energy efficiency in mind. Features like regenerative drive systems, which convert kinetic energy back into electrical energy, and adaptive power consumption, which adjusts energy use based on the machining task, help reduce the overall energy footprint of CNC machining operations.
Recycling and Reusing Metal Scraps
Metal scraps and chips generated during the machining process pose a significant waste management challenge. Progressive manufacturers are implementing comprehensive recycling programs, turning these byproducts into reusable raw materials, thereby closing the loop in the material lifecycle.
Graph: Reduction in Environmental Impact with Sustainable Practices
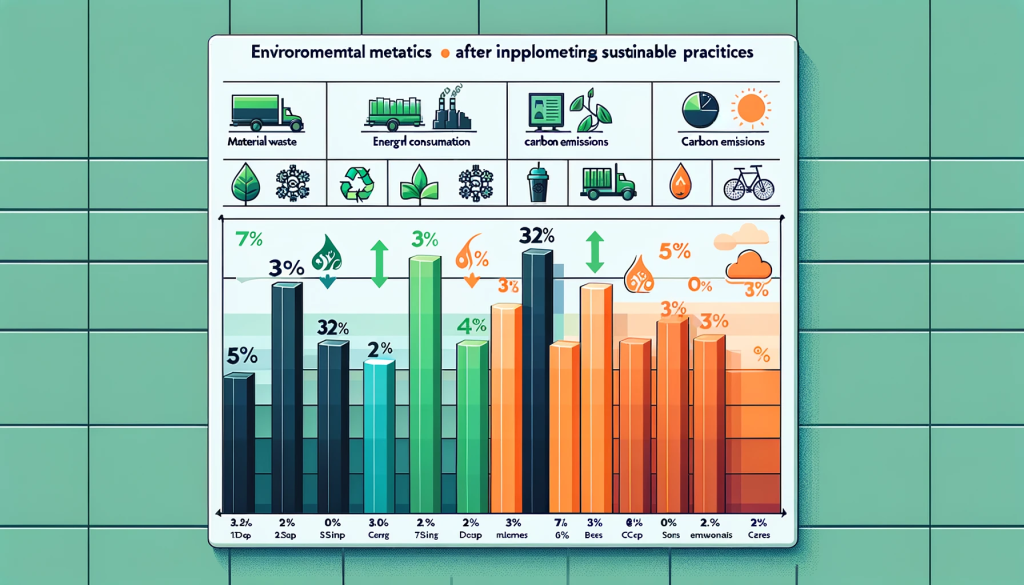
This graph illustrates the reduction in environmental impact achieved through the implementation of sustainable practices in CNC machining operations. It highlights the decrease in material waste, energy consumption, and carbon emissions over time, showcasing the positive outcomes of these eco-friendly initiatives.
Case Study: Sustainable Heat Sink Production for Consumer Electronics
A consumer electronics company, known for its commitment to sustainability, revamped its heat sink production line to align with its environmental goals. The initiative involved transitioning to recycled aluminum for heat sink manufacturing, implementing an energy-efficient CNC machining process, and establishing a comprehensive recycling program for metal scraps.
The company’s efforts led to a 40% reduction in material waste and a 25% decrease in energy consumption during the production process, without affecting the heat sinks’ thermal performance. This successful transition not only enhanced the company’s environmental credentials but also resonated positively with eco-conscious consumers.
Conclusion
Our journey through the landscape of CNC machining for heat sink manufacturing has unveiled the multifaceted challenges and opportunities within this field. From the meticulous selection of materials and the precision required to achieve complex geometries to the scalability of production and the embrace of innovative technologies, CNC machining stands as a pivotal process in the creation of efficient heat sinks. The case studies and data presented highlight the dynamic nature of this field, showcasing the continuous push towards higher efficiency, reduced environmental impact, and greater cost-effectiveness.
The future of heat sink manufacturing, underpinned by advancements in CNC technology, holds promising prospects. As we look ahead, the integration of AI and machine learning, along with the adoption of sustainable practices, will likely shape the next generation of thermal management solutions. These advancements will not only enhance the performance and efficiency of heat sinks but also contribute to a more sustainable manufacturing paradigm.
In conclusion, the role of CNC machining in producing heat sinks is invaluable and ever-evolving. The commitment to innovation, quality, and environmental stewardship within this field will continue to drive the development of thermal management solutions that meet the growing demands of the electronics industry. As we navigate the complexities of modern manufacturing, the insights and practices discussed herein will serve as guiding principles for achieving excellence in heat sink production and beyond.
Other Articles You Might Enjoy
- Material Versatility in CNC Machining: From Titanium to Thermoplastics
Introduction to CNC Machining CNC machining stands as a cornerstone in the manufacturing sector, enabling the precise creation of parts and components. This process utilizes computer numerical control (CNC) to…
- Precision CNC Machining of Steel: High-Volume Production
Precision CNC Machining and High-Volume Production As an integral part of modern manufacturing processes, Precision Computer Numerical Control (CNC) machining brings about unmatched accuracy and consistency in the production of…
- Unraveling Bead Blasting Process in CNC Machining(cnc machining china Sid)
Bead blasting is a significant process within the realm of Computer Numerical Control (CNC) machining, providing numerous industries with quality finishes for various types of products. From aircraft parts to…