There are many types of milling cutters used in precision parts machining, but only a few are commonly used.
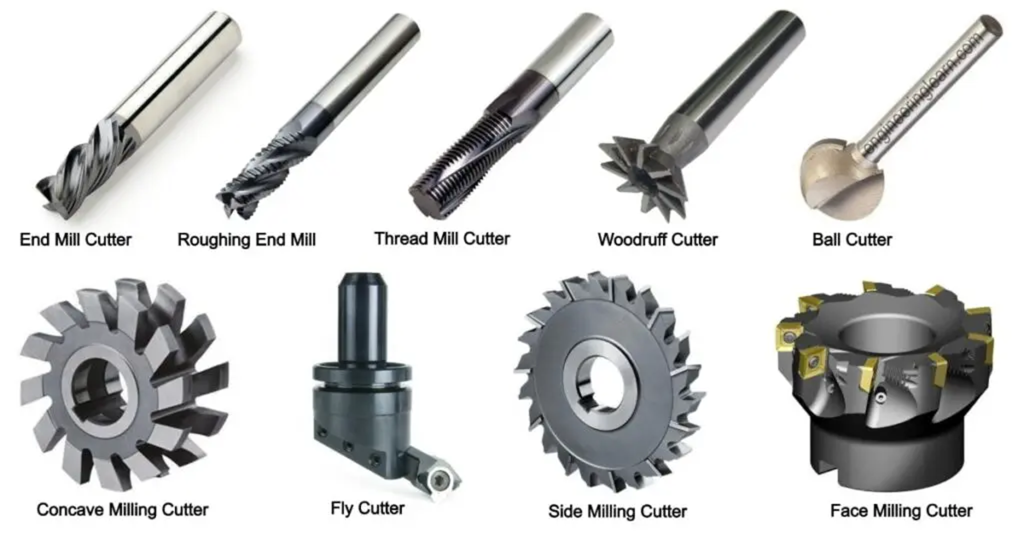
- Face Mill: The face mill has cutting edges on both its circumferential surface and its end face, with the end face cutting edge serving as the auxiliary cutting edge. Face mills are often designed with an insert-tooth structure, with the teeth made of high-speed steel or carbide. Compared to high-speed steel mills, carbide face mills offer faster cutting speeds, higher machining efficiency, and better surface quality.
- End Mill: End mills are the most commonly used type of milling cutter in precision parts machining. They have cutting edges on both the cylindrical surface and the end face, which can cut simultaneously or independently. The cylindrical surface cutting edges are the main cutting edges, while the end face cutting edges are auxiliary. The main cutting edge is helical, which improves cutting stability and machining accuracy.
- Mold Mill: Developed from the end mill, mold mills can be divided into conical end mills, cylindrical ball nose end mills, and conical ball nose end mills. They come with straight shanks, flat shanks, and Morse taper shanks. Their structural feature is that the ball nose or end face is covered with cutting edges, and the circumferential edges are connected to the ball nose edges with an arc, allowing both radial and axial feed. The working part of the mill is made of high-speed steel or carbide.
- Keyway Cutter: The keyway cutter has two teeth, with cutting edges on both the cylindrical and end faces. The end face edge extends to the center, making it resemble both an end mill and a drill bit. During machining, it first feeds axially to the slot depth and then mills along the keyway direction to complete the keyway.
- Form Mill: The form mill has cutting edges distributed on its curved surface, with no cutting edges on the end face. By controlling the tool’s vertical position, the cutting edge position can be changed to cut various angles on the workpiece. Form mills can process a wide range of shapes, but the resulting surface quality is generally poor. These cutters are difficult to sharpen, have unfavorable cutting conditions, and are unsuitable for machining contoured surfaces with a bottom.
- Profile Mill: Profile mills are usually custom-designed and manufactured for specific workpieces or machining tasks, such as angled surfaces, grooves, special-shaped holes, or steps.
China Online CNC Machining Services – Want.net
In addition to the above cutters, precision parts machining can use various general-purpose milling cutters. However, due to the special puller positions in many machine tool spindles or differences in spindle taper holes, transition sleeves and pull studs must be used.
Other Articles You Might Enjoy
- Using the Right Milling Technique: Down Milling vs. Back Milling
In the world of CNC milling, experts employ a myriad of techniques to maximize the capabilities of their CNC machines. These techniques are tailored to the size, shape, features, and…
- CNC Machining Aluminum vs. Brass: A Detailed Comparison for Precision Parts Manufacturing
Introduction to CNC Machining and Material Choices CNC (Computer Numerical Control) machining is a critical process in precision parts manufacturing. Its importance lies in its ability to create intricate and…
- The Art of CNC Precision Machining: Crafting High-Quality Parts
In the modern era, the success of CNC industries hinges on the production of parts that possess tight tolerances, impeccable surface finishes, and unwavering reliability. These meticulously crafted components contribute…
- Revolutionizing Renewable Energy with CNC Machined Components
Introduction: Renewable Energy and CNC Machined Components Renewable energy harnesses power from natural sources such as the sun, wind, and water, making it a sustainable and eco-friendly alternative to traditional…
- Is Copper the Right Choice for Electrical Component CNC Machining? A Detailed Analysis
CNC Machining of Electrical Components Utilizing Copper In the field of electrical engineering, Computer Numerical Control (CNC) machining plays an integral role, particularly in the development and manufacturing of electrical…
- Precision Aluminum Machining for Aerospace: Custom CNC Services
Precision Aluminum Machining for Aerospace: Custom CNC Services In the world of manufacturing, precision aluminum machining plays a pivotal role, particularly in aerospace industries where superior precision is required. As…