The Concept and History of Grinding Technology
Introduction
Grinding is one of the most critical processes in modern manufacturing, especially for achieving high levels of dimensional precision and surface quality. Unlike other machining methods, such as milling or turning, grinding is primarily used when the desired outcome requires an exceptionally smooth finish or when dealing with materials that are too hard or brittle to cut easily through conventional means.
What is Grinding Technology?
At its core, grinding is an abrasive machining process that involves removing small amounts of material from a workpiece surface using abrasive grains bonded into a grinding wheel or other abrasive tools. These abrasive particles, or “grits,” are extremely hard materials that are sharper and harder than the material they are grinding. Each grit functions as a tiny cutting tool that shears away tiny fragments of the material.
The primary distinction between grinding and other cutting processes lies in the size of the material removed. Whereas turning or milling removes large chunks of material to shape a part, grinding removes much smaller pieces. This results in better dimensional control and much finer surface finishes, often required for precision components in industries such as aerospace, automotive, medical devices, and tooling.
Grinding is unique because it allows for high material removal rates while maintaining very tight tolerances. It is often used as a finishing process after other machining techniques have brought the part close to its final dimensions. In many cases, grinding can be the only viable option for materials like hardened steel, ceramics, and glass.
Abrasive Materials in Grinding Technology
Abrasives are the backbone of grinding technology. Without the development of advanced abrasive materials, the effectiveness of grinding would be extremely limited. The two primary categories of abrasive materials used in grinding are conventional abrasives and superabrasives:
- Conventional abrasives: These include materials like aluminum oxide (Al₂O₃) and silicon carbide (SiC). Aluminum oxide is commonly used for grinding materials like steel, whereas silicon carbide is more suited for non-metallics, such as glass or ceramics.
- Superabrasives: These are extremely hard materials, including cubic boron nitride (CBN) and synthetic diamonds. Both CBN and diamond offer far greater hardness than conventional abrasives, making them ideal for grinding extremely hard materials. CBN is often used for hardened steel, while diamonds are preferred for non-ferrous metals and composites.
A critical property of abrasive materials is their friability, which is the ability of the abrasive particles to break down into smaller fragments during the grinding process. This self-sharpening characteristic is important because it ensures that the grinding wheel maintains its cutting ability over time.
Grinding vs. Other Machining Techniques
Grinding distinguishes itself from other machining techniques in several ways. Most importantly, the forces involved in grinding are much smaller than those in processes like turning or milling, which enables more delicate operations. This is particularly important for high-precision applications where minute errors in dimensional accuracy can lead to performance issues in the final product.
In addition, grinding often provides superior surface finishes. The surface roughness achieved through grinding can be significantly lower than that of other processes, making it ideal for parts that must fit precisely or require smooth contact surfaces, such as bearings or gears.
The versatility of grinding also sets it apart. Unlike milling or turning, which rely on specific cutting tools for different materials, a single grinding wheel can be used for various applications by simply changing the abrasive material or adjusting operational parameters.
Historical Evolution of Grinding Technology
The origins of grinding technology can be traced back to the earliest days of human civilization when abrasive stones were used to shape and sharpen tools. Early humans recognized that certain materials, such as flint and sandstone, could be used to grind down or sharpen objects, and this knowledge evolved over millennia into more sophisticated grinding techniques.
- Ancient Techniques and Early Applications: The earliest grinding techniques involved hand tools made of natural stones. These were used to grind down hard materials like flint for use in tools and weapons. The Egyptians and Greeks advanced the craft by using grinding stones to shape harder materials such as granite and marble. The Greeks even developed early grinding machines, resembling the modern-day lathe, for sharpening tools like chisels.
- Middle Ages to Early Industrial Revolution: During the Middle Ages, the use of grinding stones became more widespread, especially in tool-making. Wind and water mills were employed to rotate grinding wheels, significantly improving productivity. By the 17th century, manual grinding had evolved into a more mechanized process. With the dawn of the Industrial Revolution in the 18th and 19th centuries, the demand for more precise and durable parts led to the invention of machines specifically designed for grinding. Grinding wheels made of bonded abrasive grains were introduced, providing a more efficient means of material removal.
- The Birth of Modern Grinding Technology (19th Century): Grinding technology saw a major leap forward in the 19th century. In 1873, for example, Brown & Sharpe introduced the cylindrical grinder, which allowed for more accurate and efficient grinding of round parts. The development of new grinding machines allowed manufacturers to achieve tighter tolerances and improve surface finishes.
The invention of synthetic abrasives in the late 19th century revolutionized grinding. Natural abrasives, such as quartz and emery, had been used for centuries, but synthetic abrasives like aluminum oxide and silicon carbide brought a new level of hardness and consistency to the process. The availability of these materials expanded the use of grinding across multiple industries.
- The Emergence of Superabrasives (20th Century): The 20th century brought about the development of superabrasives like cubic boron nitride (CBN) and synthetic diamonds, which have made grinding of even the hardest materials possible. CBN, for example, is the second hardest material known to man, making it ideal for grinding hardened steels and nickel-based superalloys. These materials paved the way for high-performance grinding applications in industries such as aerospace, where the ability to grind ultra-hard materials with precision is critical.
Advances in machine tools during this period also played a significant role in the evolution of grinding technology. The introduction of numerically controlled (NC) and computer numerically controlled (CNC) machines allowed for much greater control over the grinding process, enabling manufacturers to grind complex geometries with unprecedented accuracy. CNC technology, in particular, allowed for the automation of grinding processes, making it possible to produce high-precision parts in large volumes with minimal human intervention.
Applications of Grinding Technology in Modern Manufacturing
The development of advanced grinding technologies has expanded its applications across various industries. Today, grinding is used in the production of everything from precision medical instruments to automotive and aerospace components. Key applications include:
- Precision parts: Grinding is commonly used to achieve extremely tight tolerances on parts that require high levels of precision. Components such as bearings, pistons, and gears often require grinding to achieve the necessary surface finish and dimensional accuracy.
- Material finishing: Grinding is used as a finishing process in many manufacturing workflows. After parts are machined to near-net shape, grinding can be employed to improve surface quality and achieve the desired dimensions.
- Hard materials: One of the main reasons grinding is used is its ability to machine extremely hard materials that would otherwise be impossible to cut using conventional techniques. Materials like hardened steel, ceramics, glass, and even advanced composites can be ground to precise tolerances.
Impact of Grinding Technology on Modern Industry
Grinding has significantly impacted the ability to manufacture high-performance products, especially in industries where precision and material properties are paramount. In the aerospace industry, for example, grinding is used extensively for turbine blades and other critical engine components. These parts must withstand extreme temperatures and pressures, making high-precision grinding an essential process.
Similarly, the automotive industry relies heavily on grinding for manufacturing parts like camshafts, crankshafts, and gears, where dimensional accuracy and surface finish are crucial for ensuring the long-term performance and reliability of vehicles.
The development of automation in grinding technology has led to more efficient production lines, allowing companies to reduce labor costs while increasing output. The advent of CNC grinding machines has further enhanced productivity by providing greater consistency and accuracy than manual processes.
Conclusion
Grinding technology has evolved from a simple, hand-operated process to a highly sophisticated and automated one, capable of producing parts with extremely tight tolerances and superior surface finishes. The development of new abrasive materials, the invention of advanced grinding machines, and the integration of automation and CNC control have all contributed to the essential role grinding plays in modern manufacturing.
While grinding is not always the first step in the manufacturing process, it is often the final and most crucial one, especially for industries that demand precision and quality. Understanding the concept and history of grinding technology provides insight into how it has become an indispensable tool in today’s highly technical manufacturing landscape.
How Does Grinding Compare to Other Machining Techniques?
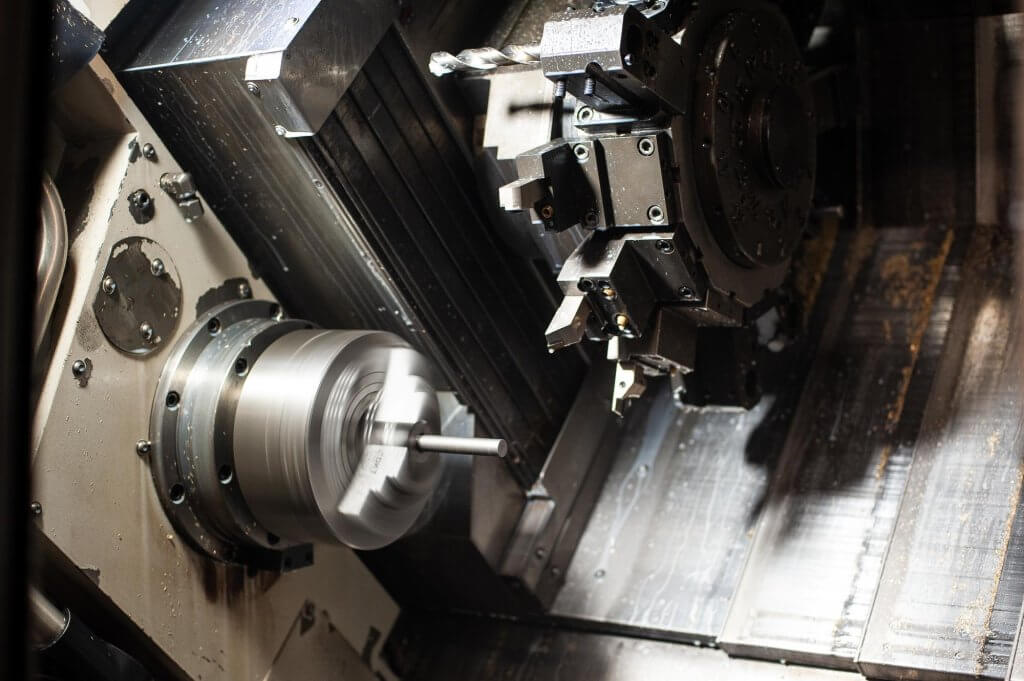
Introduction
Grinding technology plays a critical role in modern manufacturing, particularly when high precision, surface quality, and material hardness become limiting factors for other machining processes. Compared to milling, turning, or drilling, grinding offers unique advantages in terms of dimensional control, surface smoothness, and material flexibility. This chapter will explore how grinding stands out from other machining techniques by examining the differences in processes, applications, material compatibility, and performance capabilities.
While other machining methods like turning and milling are often employed for larger-scale material removal and shaping operations, grinding shines when it comes to achieving the final finish with extreme precision. To understand these differences in depth, we will evaluate grinding alongside other key machining techniques.
Material Removal Mechanism
One of the primary distinctions between grinding and other machining processes is how material is removed. In grinding, a grinding wheel with numerous abrasive particles is used to shear off tiny fragments from a workpiece. Each of these abrasive grains acts as an individual cutting tool, similar to the single-point or multi-point tools used in other processes like turning or milling. However, the size of the material removed in grinding is typically much smaller, often on the order of microns.
This difference in material removal rate is significant. Processes like turning or milling can remove large volumes of material rapidly, making them ideal for rough shaping or pre-machining. However, grinding is utilized for finishing operations where extremely tight tolerances and surface smoothness are critical. This makes grinding a slower but far more accurate method than processes like turning, which tend to leave behind rougher surfaces that require additional finishing operations.
For example, in high-precision applications such as manufacturing medical implants or aerospace components, where dimensional accuracy of less than 10 microns is essential, grinding is often the only viable option. Conventional machining methods might not offer the required level of precision or could distort the material due to the higher forces involved in cutting.
Surface Quality and Tolerance Achievements
A key advantage of grinding over other machining techniques is its ability to achieve superior surface quality. Grinding is known for producing ultra-smooth surfaces with very low roughness values, typically measured in microns or even submicron levels. This level of surface finish is not commonly achievable through milling or turning, which often leave behind rougher surfaces due to the nature of their cutting tools and higher feed rates.
Surface roughness values in turning and milling operations typically range from 0.8 to 6.3 micrometers (Ra), whereas grinding can achieve surface finishes as fine as 0.025 micrometers (Ra). This makes grinding essential in industries such as automotive, aerospace, and medical devices, where component surfaces must be smooth to avoid issues like friction, wear, or improper fits.
An example of grinding’s superior surface finish is seen in the production of ball bearings, where grinding ensures the bearing races have ultra-smooth surfaces, critical for reducing friction and extending the component’s lifespan. Similarly, in the optics industry, grinding is essential for producing smooth and precise lenses.
In addition to surface finish, grinding can maintain extremely tight tolerances that other processes struggle to achieve. Milling and turning processes typically maintain tolerances within the range of ±25 to ±125 microns, whereas grinding can consistently achieve tolerances of ±1 micron or tighter. This level of precision makes grinding the go-to process for high-accuracy components such as those used in fuel injectors, turbine engines, and precision molds.
Application of Forces in Machining
The forces involved in grinding are generally much lower than those applied in milling or turning. This is primarily due to the smaller depth of cut and the minute size of the chips removed during grinding. Lower forces mean less stress on the workpiece, reducing the likelihood of distortion, especially in thin or delicate parts.
In turning and milling, higher forces are required due to the larger cutting tools and deeper cuts, which can sometimes cause unwanted deformation or even chatter, a vibration-induced surface irregularity. In contrast, the fine abrasive grains in grinding continuously shear off small amounts of material, creating a more controlled and smoother operation.
This reduced force application in grinding is particularly important when working with brittle or hard materials such as ceramics, glass, or hardened steels. These materials are prone to cracking or chipping under the higher forces generated by milling or turning. Grinding, with its lower cutting forces, minimizes the risk of such damage and ensures that the final component meets the required specifications without defects.
A typical example is grinding of hardened tool steels or tungsten carbide. While these materials are difficult to machine using traditional cutting tools, grinding can handle them with ease due to the lower forces applied and the higher hardness of abrasive materials like cubic boron nitride (CBN) or diamond.
Suitability for Hard-to-Cut Materials
One of the standout features of grinding is its ability to machine extremely hard or abrasive materials that other machining techniques struggle with. Materials like ceramics, hardened steels, titanium alloys, and superalloys pose significant challenges for conventional processes like milling or turning, which often result in rapid tool wear, poor surface quality, or even material failure.
Grinding, on the other hand, utilizes abrasive particles that are much harder than the workpiece material, such as diamond or cubic boron nitride, making it an ideal choice for machining hard-to-cut materials. For example:
- Ceramics and Glass: These materials are extremely brittle, and traditional cutting processes can easily cause fractures or chipping. Grinding provides a much gentler, controlled material removal process, which reduces the risk of cracking or surface defects.
- Hardened Steels: After heat treatment, steels used in tooling and die-making become too hard for conventional machining methods. Grinding offers an efficient solution for finishing these materials, maintaining the necessary hardness without compromising on surface finish or precision.
- Superalloys: In industries like aerospace, where nickel-based superalloys are commonly used for turbine blades and other high-temperature applications, grinding is essential. These materials are difficult to machine due to their toughness and resistance to heat, which can cause rapid tool wear in conventional machining. Grinding, particularly with CBN or diamond abrasives, allows for the efficient machining of these hard, temperature-resistant materials.
Tool Wear and Durability
One of the drawbacks of conventional machining methods like turning and milling is tool wear, which is particularly problematic when working with hard or abrasive materials. In these processes, the cutting tool is subjected to high stresses, temperatures, and friction, all of which contribute to rapid wear. This not only shortens tool life but also compromises the accuracy and surface finish of the machined parts.
Grinding tools, such as diamond or CBN wheels, tend to have a much longer lifespan compared to conventional cutting tools. This is because the abrasive particles are much harder than the workpiece material and are capable of self-sharpening. As the abrasive particles wear down, new sharp edges are continuously exposed, maintaining the grinding wheel’s cutting ability. This self-sharpening characteristic significantly extends the tool life, especially in high-production environments.
For instance, in mass production settings like automotive engine component manufacturing, grinding is preferred for finishing critical parts such as camshafts and crankshafts, which require consistent surface quality and tight tolerances over long production runs. The longevity of grinding wheels, compared to traditional cutting tools, reduces downtime due to tool changes and ensures more consistent part quality.
Process Flexibility and Automation
Another major advantage grinding has over other machining processes is its adaptability to automation. With the advent of CNC (Computer Numerical Control) grinding machines, it has become possible to fully automate the grinding process for a wide range of applications, from cylindrical grinding of shafts to the surface grinding of precision flat parts.
CNC grinding machines provide greater precision and consistency compared to manually controlled processes, especially for complex geometries. Furthermore, CNC machines allow for multi-axis movement, enabling the grinding of intricate shapes and profiles that would be difficult or impossible to achieve with conventional cutting tools.
For example, industries that require the production of complex parts with precise geometries, such as aerospace and medical devices, benefit significantly from CNC grinding. These industries often require high repeatability, which is difficult to achieve with manual operations. CNC grinding ensures that each part produced is identical, regardless of batch size, with minimal operator intervention.
Compared to milling or turning, which also benefit from CNC automation, grinding’s ability to achieve higher precision and better surface finishes while maintaining consistency over large production runs gives it an edge in high-volume and high-precision manufacturing environments.
Energy Consumption and Environmental Considerations
Grinding is generally more energy-intensive compared to other machining techniques like turning or milling. This is due to the high rotational speeds of grinding wheels and the energy required to overcome the hardness of the abrasive grains. However, advancements in grinding machine technology have led to more efficient systems that reduce energy consumption.
For instance, high-efficiency grinding machines now utilize advanced control systems to optimize the grinding process, reducing unnecessary energy usage and improving the sustainability of the operation. Additionally, modern grinding machines often incorporate coolant systems that help dissipate heat generated during the process, reducing the energy required to maintain workpiece temperature and improving surface quality.
From an environmental perspective, grinding is increasingly becoming more sustainable due to the use of synthetic abrasives, which can be tailored for specific applications, minimizing waste and reducing environmental impact. Moreover, the development of coolant filtration systems allows for the recycling of cutting fluids, further reducing the ecological footprint of grinding operations.
While milling or turning typically consume less energy per unit of material removed, grinding’s higher precision and superior surface finish often justify the increased energy use, especially in industries where these characteristics are critical to product performance.
Use Cases: When Grinding is the Preferred Method
The choice of grinding over other machining processes often depends on the specific requirements of the job. Here are some use cases where grinding is the preferred method:
- Precision Molds and Dies: Grinding is essential in producing molds and dies with highly accurate dimensions and smooth surface finishes. This is particularly important in industries like plastics and injection molding, where any imperfections in the mold directly affect the quality of the finished product.
- Aerospace Components: In the aerospace industry, where turbine blades, engine components, and landing gear parts are made from hard-to-machine materials like titanium and nickel-based superalloys, grinding is crucial. These components must withstand extreme temperatures and stresses, making the precision and durability offered by grinding a necessity.
- Medical Instruments: Grinding is frequently used in the production of surgical tools and medical implants, where both material biocompatibility and surface quality are paramount. For example, artificial hip joints and dental implants require mirror-like finishes and must adhere to strict dimensional tolerances to function properly.
- Automotive Parts: In the automotive industry, grinding is essential for manufacturing components such as crankshafts, camshafts, and gears. These parts require extremely high precision and smooth surfaces to ensure proper engine performance and longevity.
What are the Basic Principles of Grinding?
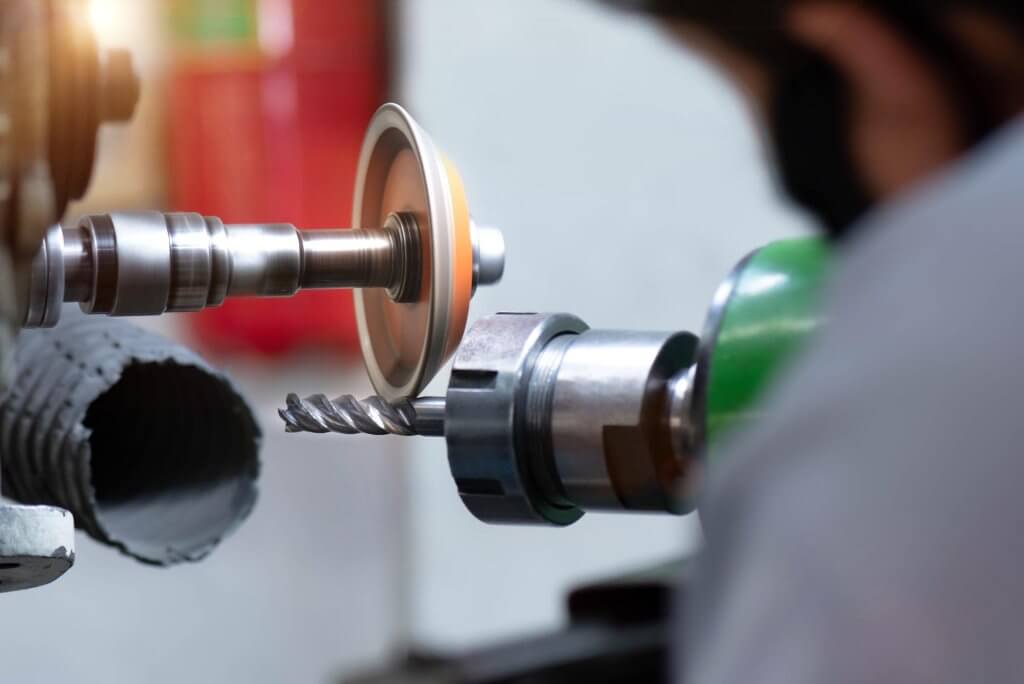
Introduction
Grinding is a machining process that uses abrasive particles bonded to a wheel or another surface to remove material from a workpiece. It is an essential method for achieving precise dimensions and superior surface finishes, especially when dealing with hard or brittle materials. This chapter explores the fundamental principles of grinding, covering topics like abrasive materials, grinding force dynamics, wheel dressing, and the factors that influence the effectiveness of the grinding process.
Understanding the principles behind grinding is essential for manufacturers to optimize the process, ensuring that the final products meet stringent quality requirements.
Abrasive Cutting Action
The grinding process is essentially a form of multi-point cutting, where numerous abrasive particles are engaged in the removal of material. Unlike single-point tools (like in turning) or multi-point tools (like in milling), a grinding wheel has thousands of tiny cutting edges that shear away small chips from the workpiece.
Each abrasive grain on the wheel surface acts as a cutting tool, creating tiny grooves on the surface of the material. The shape, size, and orientation of these grains determine the overall cutting action. As the wheel rotates, the abrasive particles interact with the workpiece material, removing small chips, which are called “swarf.” This process continues until the desired shape or surface finish is achieved.
A key difference between grinding and other forms of machining is the negative rake angle of the abrasive particles, which ranges from -45° to -60°. This means that the abrasive grains cut the material under greater resistance, leading to higher levels of friction and heat generation. While the heat generated during grinding can be controlled using coolants and lubrication, the negative rake angle makes grinding more challenging to manage than conventional machining processes. However, it also allows grinding to achieve finer surface finishes.
Grinding Wheels and Abrasive Materials
Grinding wheels are made from abrasive grains held together by a bonding material. The abrasive grains are typically very hard, capable of cutting through materials that conventional cutting tools cannot. There are two primary categories of abrasive materials:
- Conventional Abrasives: These include materials like aluminum oxide (Al₂O₃) and silicon carbide (SiC). Aluminum oxide is widely used for grinding metals such as steel, while silicon carbide is preferred for non-metals like ceramics, glass, and certain metals such as titanium.
- Superabrasives: These consist of materials like cubic boron nitride (CBN) and synthetic diamond. Superabrasives are used to grind extremely hard materials like hardened steels, superalloys, and ceramics. For example, CBN is commonly used for grinding hardened steels, while synthetic diamonds are used for cutting and grinding non-ferrous metals and materials like ceramics and glass.
The choice of abrasive material depends largely on the properties of the workpiece material. For example, grinding hardened steel requires a different abrasive than grinding softer metals like aluminum. Table 1 below shows the typical usage of abrasive materials based on the workpiece material.
Abrasive Material | Workpiece Material |
---|---|
Aluminum Oxide (Al₂O₃) | Steel, Cast Iron, Malleable Iron |
Silicon Carbide (SiC) | Ceramics, Glass, Titanium, Carbides |
Cubic Boron Nitride (CBN) | Hardened Steel, Superalloys |
Synthetic Diamond | Ceramics, Glass, Non-ferrous Metals |
In addition to the abrasive material, the bonding agent plays a crucial role in holding the grains together and influencing the wheel’s performance. The common types of bonds are:
- Vitrified Bond: Made from clay or glass, vitrified bonds are strong and rigid, providing excellent cutting action but are prone to breakage under shock.
- Resinoid Bond: This is a softer and more flexible bond than vitrified. It is more resistant to shock and used in grinding applications that require high material removal rates.
- Metal Bond: Metal bonds are used in wheels containing superabrasives like diamond or CBN. These bonds offer high strength and durability, making them suitable for precision grinding operations.
Wheel Dressing and Conditioning
One of the most critical principles in grinding is wheel dressing. As grinding progresses, the abrasive grains on the wheel gradually wear down and become less effective. They may also become clogged with material (a condition called “loading”). To restore the wheel’s cutting ability, it must be dressed and conditioned.
Dressing refers to the process of removing worn abrasive grains and contaminants from the wheel surface to expose fresh, sharp grains. It can also restore the wheel’s original shape if it becomes deformed during the grinding process.
Conditioning, on the other hand, involves improving the wheel’s surface structure, ensuring the grains are properly aligned and ready for optimal cutting performance. For superabrasive wheels, like those containing CBN or diamond, truing is often used. Truing reshapes the wheel to its original form and is essential for precision grinding applications.
Dressing tools vary depending on the type of wheel and grinding operation. Single-point diamond dressers are commonly used for fine dressing applications, while multi-point dressers and rotary diamond dressers are employed for coarser applications. Additionally, abrasive sticks can be used for manual dressing in small-scale grinding operations.
A well-dressed and conditioned grinding wheel results in improved surface quality, reduced heat generation, and more consistent material removal rates. Frequent dressing also ensures that the grinding process remains stable over long production runs, which is essential in high-precision manufacturing environments.
Grinding Force Dynamics
The forces involved in grinding are a fundamental aspect of the process. Understanding how these forces act on both the grinding wheel and the workpiece is key to optimizing performance.
There are three primary forces involved in grinding:
- Normal Force: This force acts perpendicular to the workpiece surface and is responsible for creating depth of cut. It is often the largest force component in grinding.
- Tangential Force: This force acts in the direction of the wheel’s rotation and is responsible for removing material from the workpiece. It directly influences material removal rates and tool wear.
- Axial Force: This force acts parallel to the workpiece surface and is typically smaller than the normal and tangential forces. It affects the stability of the grinding process and the surface finish.
These forces interact with one another and can be measured using sensors installed on the grinding machine. The force ratio, defined as the ratio between the tangential and normal forces, is an important parameter used to evaluate the grinding process. A higher force ratio indicates more efficient material removal, while a lower force ratio suggests that the grinding wheel is becoming dull and needs to be dressed.
The specific grinding energy (also known as grinding power) is another important factor. It is the energy required to remove a unit volume of material and is calculated using the following equation:
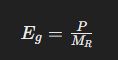
Where:
- Eg is the specific grinding energy,
- P is the power consumed during grinding,
- MR is the material removal rate.
Grinding typically requires more energy than other machining processes, such as turning or milling, because of the large number of cutting points and the small chip sizes involved.
Heat Generation and Control
Grinding generates significant heat due to the high friction and cutting forces between the wheel and the workpiece. This heat can cause thermal damage to both the grinding wheel and the workpiece. Overheating the workpiece can lead to surface burns, changes in microstructure, and residual stresses, all of which negatively affect part performance.
To manage heat generation, grinding operations make use of coolants and cutting fluids. These fluids serve several functions:
- Cooling: The primary role is to remove heat from the grinding zone and prevent thermal damage.
- Lubrication: Cutting fluids reduce friction between the abrasive grains and the workpiece, enhancing the efficiency of material removal.
- Chip Removal: Coolants help to flush away swarf from the grinding zone, preventing clogging of the wheel.
Different coolants are used based on the grinding operation and the material being ground. For example, water-based coolants are commonly used in surface grinding, while oil-based coolants are preferred in operations where high lubrication is needed.
The application method of the coolant is also important. For efficient heat control, the coolant must be directed precisely at the contact point between the wheel and the workpiece. High-pressure jets or specially designed nozzles are often used to ensure that the coolant penetrates the grinding zone effectively.
Material Removal Rate (MRR)
The material removal rate in grinding is significantly smaller than in other machining processes like milling or turning. However, it is a critical parameter for determining process efficiency. The MRR depends on several factors, including the grinding wheel’s speed, the feed rate, and the depth of cut.
The formula for calculating material removal rate is:
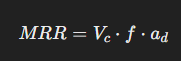
Where:
- Vc is the cutting speed (the speed at which the grinding wheel rotates),
- f is the feed rate (how fast the workpiece moves relative to the wheel),
- ad is the depth of cut (how deep the abrasive grains penetrate the workpiece).
Achieving a balance between these variables is essential for optimizing the grinding process. A higher MRR increases productivity but may compromise surface finish or lead to excessive heat generation. Conversely, a lower MRR results in slower production rates but yields finer surface finishes and better control over heat generation.
The following table outlines the typical ranges for grinding parameters depending on the type of grinding process.
Grinding Process | Cutting Speed (m/s) | Feed Rate (mm/min) | Depth of Cut (mm) |
---|---|---|---|
Surface Grinding | 20 – 40 | 50 – 500 | 0.01 – 0.05 |
Cylindrical Grinding | 20 – 45 | 20 – 400 | 0.02 – 0.10 |
Creep-Feed Grinding | 1 – 15 | 1 – 10 | 0.5 – 6.0 |
Centerless Grinding | 20 – 45 | 10 – 200 | 0.01 – 0.05 |
Factors Affecting Grinding Efficiency
Several factors influence the effectiveness of the grinding process, ranging from the type of abrasive used to machine settings. Key factors include:
- Abrasive Grain Size: Smaller grains produce a finer surface finish but remove material more slowly. Coarser grains remove material faster but leave a rougher finish.
- Wheel Speed: Higher wheel speeds increase the material removal rate but generate more heat, which can affect surface quality.
- Feed Rate: Faster feed rates increase material removal but can degrade surface finish and lead to overheating.
- Depth of Cut: A deeper cut allows for more material removal but increases the risk of thermal damage and tool wear.
- Coolant Application: Effective coolant application is essential for controlling heat and ensuring a smooth grinding process.
What are the Main Grinding Methods?
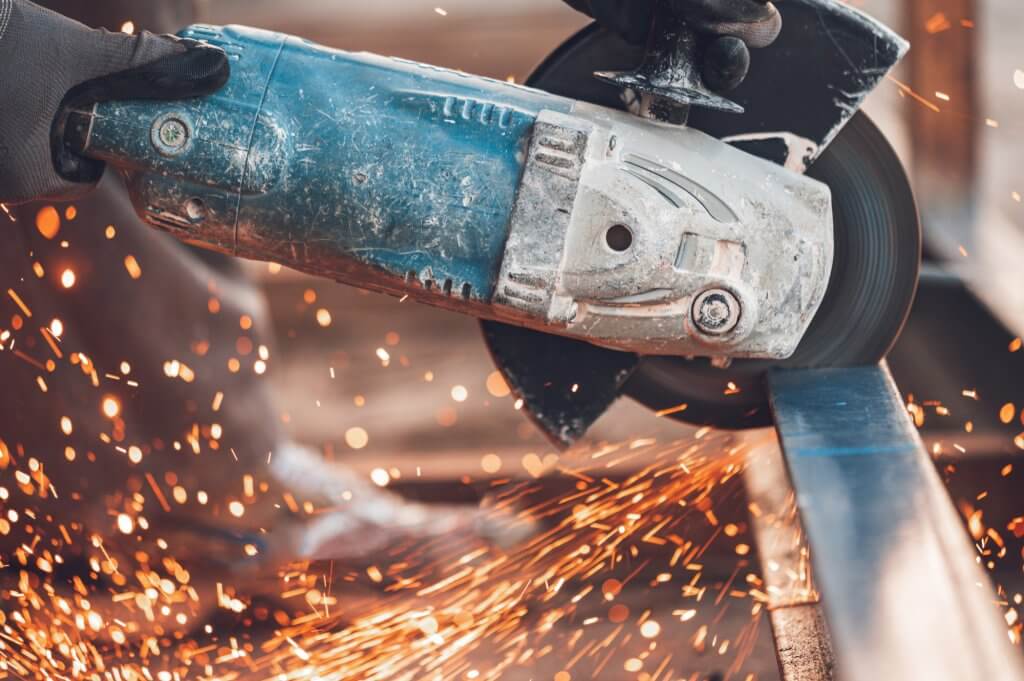
Introduction
Grinding is a versatile machining process that offers a wide range of applications for different industries. The three primary methods of grinding—surface grinding, cylindrical grinding, and centerless grinding—are each designed to achieve distinct goals and are used to address specific types of geometries and precision requirements. These grinding techniques are integral to achieving high-precision parts, ensuring tight tolerances, and creating fine surface finishes for various components used in industries such as aerospace, automotive, medical devices, and tooling manufacturing.
In this section, we will discuss the key grinding methods, outline their operational principles, and explain their distinctive features. We will also provide insights into the types of workpieces for which each method is best suited. By understanding the differences between surface grinding, cylindrical grinding, and centerless grinding, manufacturers can select the most appropriate method for their needs, optimizing both the quality of their products and their manufacturing efficiency.
Surface Grinding: Definition, Process, and Applications
Surface grinding is one of the most common grinding methods, and it involves the removal of material from a workpiece’s flat surface to produce a smooth finish. In surface grinding, a rotating abrasive wheel cuts across the surface of a workpiece, removing material at a very shallow depth to achieve the required flatness, parallelism, or angularity.
The grinding wheel’s abrasive grains act like tiny cutting tools, producing microchips by removing a thin layer of material from the workpiece. The process is highly controlled to ensure precision and smoothness, making it ideal for applications where surface finish and dimensional accuracy are critical.
Process Overview
- Machine Setup: Surface grinding machines consist of a flat or slightly concave grinding wheel mounted on a horizontal or vertical spindle. The workpiece is typically clamped onto a magnetic chuck (for ferrous materials) or a mechanical fixture. The grinding wheel is then fed slowly across the workpiece in multiple passes, removing small amounts of material with each pass.
- Material Removal: The amount of material removed is very small, typically in the range of microns. This allows surface grinding to achieve extremely tight tolerances, often down to ±1 micron, depending on the machine setup and the type of material.
- Coolant Application: Coolants are critical in surface grinding to reduce friction, prevent overheating, and flush away swarf. The use of coolants also improves the wheel’s cutting action by reducing loading (the clogging of the grinding wheel with debris).
Advantages of Surface Grinding
- High Precision: Surface grinding is known for its ability to achieve tight tolerances and highly precise dimensions. It is often used for parts that require extremely smooth surfaces and flatness, such as machine tool components, die plates, and precision bearings.
- Excellent Surface Finish: Surface grinding can produce finishes as smooth as 0.1–0.5 microns Ra, making it suitable for polishing applications and finishing tasks where surface quality is critical.
- Versatility: Surface grinding can be performed on a variety of materials, including ferrous and non-ferrous metals, ceramics, and even certain plastics. This versatility makes it a staple in a wide range of industries.
Applications
Surface grinding is commonly used for applications that require precision flat surfaces or tight dimensional tolerances. Typical examples include:
- Mold and Die Manufacturing: The flat surfaces of molds and dies must meet strict dimensional tolerances to ensure that the parts produced from them are accurate and consistent.
- Precision Tooling: Surface grinding is essential for manufacturing machine tools, jigs, and fixtures, which must maintain high levels of accuracy for their functions.
- Automotive and Aerospace Components: Critical components such as engine blocks, transmission housings, and turbine blades are surface ground to meet the exacting specifications required in these industries.
Cylindrical Grinding: Definition, Process, and Applications
Cylindrical grinding is a grinding method used to achieve precise tolerances and surface finishes on cylindrical or rounded workpieces. Unlike surface grinding, which focuses on flat surfaces, cylindrical grinding is used for round objects like shafts, rods, and bearing races.
Cylindrical grinding can be further divided into external cylindrical grinding and internal cylindrical grinding, depending on the part of the workpiece being ground.
External Cylindrical Grinding
In external cylindrical grinding, the workpiece is mounted between centers or in a chuck and rotated while the grinding wheel is applied to its outer surface. This method is used to achieve precise diameters, circularity, and surface finishes on cylindrical parts.
- Process Overview: The grinding wheel rotates in the same direction as the workpiece, with grinding occurring at the point where the wheel contacts the workpiece’s surface. The workpiece is usually fed axially through the grinding wheel.
- Types of Grinders: There are several types of cylindrical grinding machines, including center-type and chucking-type machines. Center-type grinders hold the workpiece between two rotating centers, while chucking-type machines use a chuck to hold one end of the workpiece in place.
- Precision and Surface Finish: Cylindrical grinding machines can achieve dimensional tolerances as tight as ±2 microns and surface finishes as fine as 0.2 microns Ra. It is often used in precision machining for critical components.
Internal Cylindrical Grinding
In internal cylindrical grinding, the inside of the workpiece is ground. This process is similar to external cylindrical grinding but is used to finish the inside of hollow parts like bushings, tubes, and bearing rings.
- Process Overview: A small grinding wheel, often mounted on a spindle, is fed into the bore of the workpiece, removing material from the inside surface. As with external grinding, the workpiece is rotated while the grinding wheel engages it.
- Applications: Internal cylindrical grinding is commonly used in the manufacturing of engine cylinders, hydraulic cylinders, and precision bushings. It is also frequently used to produce precision holes and bores in components like bearings, bushings, and valve seats.
Advantages of Cylindrical Grinding
- High Precision for Round Parts: Cylindrical grinding is unmatched in its ability to produce highly precise round parts. It ensures that components like shafts and bearings are perfectly cylindrical and conform to their dimensional specifications.
- Improved Surface Quality: The surface finish produced by cylindrical grinding is excellent, often achieving values as low as 0.2 microns Ra, which is crucial for components that require smooth surfaces, such as bearing races and hydraulic components.
- Versatility: Cylindrical grinding is used across various industries for parts that need to meet strict tolerance and surface finish requirements. It is commonly used in automotive, aerospace, defense, and medical equipment manufacturing.
Applications
Cylindrical grinding is widely used in industries where precision and accuracy are critical. Some common applications include:
- Shaft Manufacturing: Shafts used in motors, pumps, and compressors must meet tight dimensional tolerances and require fine surface finishes to reduce wear and ensure efficient operation.
- Bearing Production: Bearings are one of the most common components produced using cylindrical grinding. They require precise roundness and smooth surface finishes to reduce friction and enhance performance.
- Hydraulic Systems: Cylindrical grinding is used to manufacture hydraulic pistons, which need to fit precisely within their cylinders to maintain proper pressure and performance.
Centerless Grinding: Definition, Process, and Applications
Centerless grinding is a high-efficiency grinding method used to process cylindrical workpieces without the need for supporting the workpiece between centers or using a chuck. It is especially suited for mass production and is used extensively in the manufacturing of small, precise components.
Unlike surface or cylindrical grinding, centerless grinding eliminates the need for the workpiece to be mounted or fixed, providing a more flexible and efficient grinding solution.
Process Overview
- Machine Setup: In centerless grinding, the workpiece is supported between a rotating grinding wheel and a stationary regulating wheel. The workpiece is fed axially between the two wheels, with the grinding wheel removing material from its surface while the regulating wheel controls the workpiece’s rotational speed and axial feed rate.
- Types of Centerless Grinding: There are two primary types of centerless grinding: through-feed and in-feed. In through-feed grinding, the workpiece is fed axially through the machine, continuously moving past the grinding wheel. In in-feed grinding, the workpiece is fixed in place, and the grinding wheel moves in and out, removing material from specific areas.
- Coolant Application: As with other grinding methods, coolants are crucial for reducing friction, preventing overheating, and flushing away swarf during centerless grinding. The high surface speeds involved in centerless grinding can generate significant heat, making coolant application especially important.
Advantages of Centerless Grinding
- High Efficiency: Centerless grinding is one of the most efficient grinding methods, particularly for mass production. Since the workpiece does not need to be mounted, loading and unloading are quick, making it an ideal choice for high-volume production lines.
- Consistency: This grinding method ensures excellent consistency between parts. The lack of centers or chucks means that the process is less dependent on operator skill, leading to more uniform results across production batches.
- Cost-Effective: Centerless grinding eliminates the need for expensive fixtures and complex setups, reducing production costs. The process is also highly automated, minimizing labor costs.
Applications
Centerless grinding is widely used in industries that require mass production of small cylindrical parts. Some typical applications include:
- Precision Bearings: Centerless grinding is essential for producing the small, high-precision bearings used in automotive and aerospace applications.
- Pins and Shafts: Small pins, shafts, and fasteners used in mechanical assemblies often require centerless grinding to ensure their dimensional accuracy and smooth finishes.
- Medical Devices: The production of small, cylindrical medical components, such as guide wires and catheter tubes, often involves centerless grinding due to its ability to handle delicate parts and maintain precise tolerances.
Comparing Surface, Cylindrical, and Centerless Grinding
While surface, cylindrical, and centerless grinding methods each have their distinct advantages and applications, they also differ in their fundamental approach to material removal, workpiece handling, and process efficiency. The following table summarizes the key differences between these three grinding methods:
Aspect | Surface Grinding | Cylindrical Grinding | Centerless Grinding |
---|---|---|---|
Workpiece Type | Flat surfaces | Cylindrical parts (internal or external) | Small, cylindrical parts |
Workpiece Holding Method | Magnetic chuck or fixture | Held between centers or in a chuck | Supported between grinding and regulating wheels |
Typical Tolerances | ±1 to ±5 microns | ±2 to ±5 microns | ±1 to ±5 microns |
Surface Finish | 0.1 to 0.5 microns Ra | 0.2 to 0.4 microns Ra | 0.1 to 0.5 microns Ra |
Material Removal Rate | Low | Medium | High |
Applications | Precision flat surfaces, tooling | Shafts, bearings, hydraulic components | Mass production of small cylindrical parts |
What Types of Grinding Machines Are There?
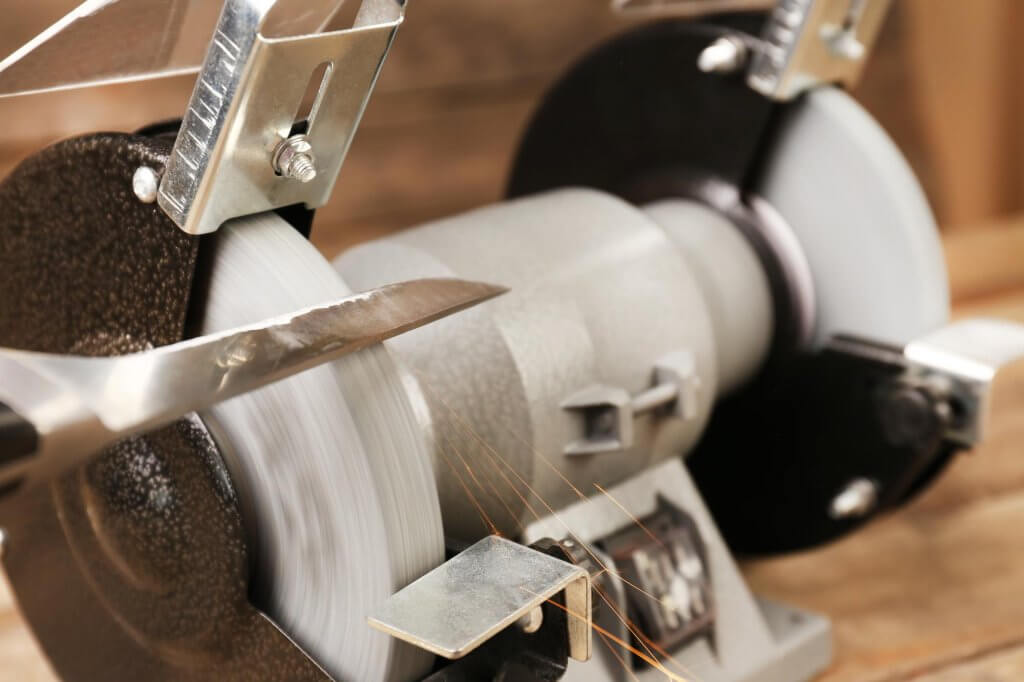
Introduction
Grinding machines are essential to many manufacturing processes, offering the precision, surface finish, and dimensional accuracy required in modern production. As technology has advanced, so have grinding machines, evolving from basic manual devices to fully automated systems. Different types of grinding machines exist to meet the varied needs of industries like aerospace, automotive, medical devices, and tool-making. Each type of grinding machine is designed for a specific purpose, whether it’s achieving ultra-precise tolerances, finishing delicate surfaces, or removing material efficiently in high-volume production environments.
This chapter will explore the main types of grinding machines available today, ranging from manual to automated systems. We will discuss their capabilities, key features, and applications, helping manufacturers understand which machine type is most suitable for their specific requirements.
Manual Grinding Machines
Manual grinding machines represent the earliest form of grinding technology, where operators manually control the machine and apply grinding wheels to the workpiece. Although these machines have largely been replaced by automated systems in many industries, they are still widely used for smaller jobs and in environments where extreme precision is not required. Manual grinding machines typically include bench grinders and hand-held grinding tools.
Bench Grinders
Bench grinders are the simplest form of manual grinding machines, typically used for light-duty grinding tasks, such as sharpening tools or removing burrs and rough edges from workpieces. Bench grinders consist of a rotating abrasive wheel mounted on a stationary motorized bench. The operator manually holds the workpiece against the rotating wheel to remove material.
- Key Features: Bench grinders are equipped with a coarse grinding wheel and sometimes a finer wheel for finishing tasks. The grinding process is controlled entirely by the operator, making it highly dependent on the skill and experience of the user.
- Applications: Bench grinders are commonly used in small workshops for tool sharpening, deburring metal edges, and cleaning surfaces. They are also used for minor repair jobs and maintenance tasks.
Hand-Held Grinders
Hand-held grinders, or angle grinders, are versatile manual tools used for cutting, grinding, and polishing in a variety of industries. These portable tools use abrasive discs and can handle various materials such as metals, ceramics, and masonry. Operators manually guide the tool along the workpiece, adjusting speed and pressure as needed.
- Key Features: Hand-held grinders are powered by electricity, battery, or air pressure and allow operators greater flexibility in grinding complex shapes or hard-to-reach areas. They are highly versatile but can require significant operator skill for precise work.
- Applications: Hand-held grinders are used in construction, metalworking, and automotive repair for cutting and grinding metal, cleaning welds, and smoothing rough surfaces. They are also useful in fabrication shops for finishing welds and prepping metal surfaces for painting.
Pros of Manual Grinding Machines
- Affordability: Manual grinding machines are typically less expensive than automated systems, making them accessible to small businesses or individual operators.
- Flexibility: Manual grinders offer more control and flexibility in terms of grinding angles, pressure, and speed. This makes them ideal for jobs where precision isn’t the top priority but versatility is needed.
- Simplicity: Manual grinding machines are easier to maintain and operate, requiring minimal training for operators to start using them effectively.
CNC Grinding Machines
CNC (Computer Numerical Control) grinding machines represent a major advancement in the grinding industry, offering the ability to automate complex grinding processes with precision and repeatability. CNC machines are programmed through specialized software to perform multiple grinding operations without the need for human intervention. This automation results in increased accuracy, productivity, and consistency, particularly for large-scale production or high-precision work.
CNC Surface Grinders
CNC surface grinders are designed to produce extremely flat surfaces on workpieces, often with precision down to a few microns. These machines use a rotating abrasive wheel to grind away material from the flat surface of a workpiece, with movements precisely controlled by a computer.
- Key Features: CNC surface grinders feature programmable control systems that allow operators to input complex geometries and grinding patterns. The machine can then automatically adjust the grinding wheel’s speed, position, and depth of cut according to the programmed parameters.
- Applications: CNC surface grinders are widely used in industries such as aerospace, automotive, and tool-making for producing flat surfaces on parts like molds, dies, and machine components. They are essential for applications requiring tight dimensional tolerances and high surface quality.
CNC Cylindrical Grinders
CNC cylindrical grinders are used for grinding the external or internal surfaces of cylindrical workpieces, such as shafts, rods, and sleeves. These machines are highly versatile and capable of grinding complex shapes, including tapered and contoured surfaces.
- Key Features: CNC cylindrical grinders have multiple axes of movement that are programmed to follow precise patterns around the workpiece. These machines use either a rotating grinding wheel for external grinding or a smaller wheel for internal grinding, depending on the specific operation.
- Applications: CNC cylindrical grinders are used to produce high-precision parts for industries like automotive and hydraulic systems. They are commonly used for grinding engine parts, bearings, and gears, where precise roundness and surface finish are critical.
CNC Centerless Grinders
CNC centerless grinders are high-productivity machines designed for mass-producing small cylindrical parts, such as bearings, pins, and fasteners. In contrast to cylindrical grinders, centerless grinders do not require the workpiece to be mounted between centers. Instead, the workpiece is supported by a regulating wheel while the grinding wheel removes material.
- Key Features: CNC centerless grinders feature advanced automation and allow for high-speed production of small parts. These machines eliminate the need for chucks or workpiece fixtures, which speeds up the production process and increases output.
- Applications: CNC centerless grinders are ideal for applications requiring high-volume production of small, precise parts. Industries such as automotive, medical devices, and aerospace rely on these machines to manufacture components with tight dimensional tolerances.
Pros of CNC Grinding Machines
- Precision: CNC grinders can achieve extremely high levels of precision, often down to a few microns. This makes them ideal for industries requiring exact tolerances, such as aerospace and medical device manufacturing.
- Consistency: The automation provided by CNC systems ensures consistent results across multiple production runs, reducing the potential for human error and improving overall quality control.
- Productivity: CNC grinding machines can operate continuously with minimal supervision, increasing production efficiency. They are especially beneficial in large-scale manufacturing environments where high output is required.
Automated Grinding Machines
Automated grinding machines represent the most advanced level of grinding technology, where automation plays a key role in achieving maximum efficiency and precision. These machines often incorporate robotic arms, sensors, and artificial intelligence (AI) to manage the entire grinding process, from loading and unloading workpieces to adjusting grinding parameters in real time.
Robotic Grinding Machines
Robotic grinding systems combine CNC grinding machines with robotic arms to perform complex grinding operations without human intervention. These systems can handle a wide range of grinding tasks, including polishing, deburring, and finishing.
- Key Features: Robotic grinders are equipped with advanced sensors and AI systems that allow them to adapt to changing conditions, such as tool wear or variations in workpiece geometry. They can automatically adjust feed rates, speeds, and pressure to maintain optimal grinding conditions.
- Applications: Robotic grinding machines are used in industries that require high levels of automation and precision, such as aerospace, automotive, and medical device manufacturing. They are especially useful for producing complex shapes and contours on parts like turbine blades, prosthetic devices, and custom engine components.
Automated Infeed Grinding Machines
Automated infeed grinding machines are used to grind large batches of identical parts. These machines automatically feed the workpieces into the grinding area, perform the grinding operation, and then discharge the finished parts without human intervention. This process is highly efficient for mass production.
- Key Features: Infeed grinding machines are designed to handle workpieces of varying shapes and sizes, with fully programmable control over grinding parameters. They often feature automatic workpiece loading and unloading systems, further reducing the need for manual labor.
- Applications: These machines are widely used in industries such as automotive and manufacturing for mass production of parts like gears, shafts, and fasteners. They are ideal for grinding large quantities of identical parts with high precision and repeatability.
Fully Integrated Grinding Systems
Fully integrated grinding systems combine multiple machines and robotic elements into a seamless production line. These systems automate the entire grinding process from raw material handling to finished part inspection. Such systems are highly customizable, designed to meet the specific needs of manufacturers producing complex or high-precision components.
- Key Features: Fully integrated grinding systems often feature real-time monitoring and feedback systems that adjust grinding parameters based on sensor input. They can automatically switch between different tools or grinding wheels, optimizing the process for different parts without downtime.
- Applications: Fully integrated grinding systems are used in high-tech industries such as semiconductor manufacturing, precision engineering, and aerospace. These systems are ideal for applications requiring complex geometries, high production volumes, and stringent quality control.
Pros of Automated Grinding Machines
- Increased Throughput: Automated grinding machines can operate continuously, reducing cycle times and increasing production rates. This is especially valuable in high-volume manufacturing environments.
- Reduced Labor Costs: The automation of loading, unloading, and grinding processes minimizes the need for manual labor, reducing labor costs and human error.
- Adaptability: Automated systems can handle a wide variety of workpieces and automatically adjust parameters to optimize the grinding process, making them highly adaptable to changing production needs.
Comparing Grinding Machine Types
The following table summarizes the key differences between manual, CNC, and fully automated grinding machines:
Aspect | Manual Grinding Machines | CNC Grinding Machines | Automated Grinding Machines |
---|---|---|---|
Precision | Moderate | High | Very High |
Operator Involvement | High | Low | Minimal |
Cost | Low | Medium to High | High |
Flexibility | High | High | Medium to High |
Applications | Small-scale tasks, tool sharpening | High-precision parts, mass production | Complex, high-volume manufacturing |
Automation Level | None | Partial | Full |
How to Choose the Right Grinding Wheel Materials?

Introduction
Choosing the right grinding wheel material is essential for achieving optimal performance, efficiency, and quality in grinding operations. Grinding wheels consist of abrasive grains and bonding agents that are specifically designed for particular applications. Each material has unique properties that make it suitable for specific tasks, such as cutting, finishing, or polishing different types of metals, ceramics, or composites. Selecting the right material depends on factors like workpiece hardness, desired surface finish, and the type of grinding process being used.
This chapter will delve into the various types of grinding wheel materials, explain their properties and applications, and provide guidance on selecting the best material for a given operation. We will also explore the key considerations in choosing grinding wheels, such as hardness, friability, grain size, and bonding type.
Key Considerations When Choosing Grinding Wheel Materials
Before selecting a grinding wheel material, it’s important to understand the various factors that affect grinding performance. Each grinding application has its own requirements, and the grinding wheel material must be chosen based on the specific needs of the task. Below are some of the key considerations to keep in mind:
- Workpiece Material: The material being ground significantly impacts the choice of grinding wheel. Softer materials require abrasives with higher hardness, while harder materials often benefit from abrasives with better wear resistance and toughness.
- Grinding Process: Different types of grinding processes—such as surface grinding, cylindrical grinding, or centerless grinding—place different demands on the wheel material. High-speed processes may require more durable materials, while precision grinding processes may call for finer abrasives.
- Required Surface Finish: The desired surface finish can dictate the type of grinding wheel material. Fine surface finishes require smaller grain sizes, while coarse materials can be used for fast material removal in rough grinding.
- Hardness and Toughness of the Abrasive: Abrasives need to be harder than the material being ground. The toughness of the abrasive also plays a role in its performance. Tough abrasives can withstand higher grinding forces, while more friable (brittle) abrasives can fracture and expose new sharp cutting edges, improving cutting performance.
- Coolant and Lubrication: The presence of a grinding coolant or lubricant can influence the choice of abrasive material. Some abrasives work better in dry grinding, while others perform optimally with coolants to reduce friction and heat buildup.
Types of Grinding Wheel Materials
There are several different types of grinding wheel materials, each suited for specific applications. The most commonly used materials include aluminum oxide, silicon carbide, cubic boron nitride (CBN), and diamond. These materials vary in terms of hardness, friability, and cutting performance, allowing them to be used for a wide range of grinding tasks.
1. Aluminum Oxide (Al2O3)
Aluminum oxide is one of the most commonly used abrasive materials in grinding wheels. It is ideal for grinding a variety of metals, including carbon steel, alloy steel, wrought iron, and annealed cast iron.
- Properties: Aluminum oxide is tough and durable, which allows it to retain its cutting edge for longer periods. It is also friable, meaning it fractures under pressure, exposing new sharp cutting edges. This self-sharpening property is beneficial for maintaining performance over extended periods.
- Applications: Aluminum oxide grinding wheels are best suited for grinding ferrous metals such as steel and cast iron. It is commonly used in surface grinding, cylindrical grinding, and tool sharpening applications. Because of its durability, aluminum oxide is a good choice for high-speed and heavy-duty grinding processes.
- Advantages:
- Tough and long-lasting
- Good for grinding a wide range of metals
- Suitable for both precision and high-speed grinding
Property | Aluminum Oxide |
---|---|
Hardness | Moderate |
Friability | Medium |
Applications | Ferrous metals (steel, iron) |
Best for | General-purpose grinding |
2. Silicon Carbide (SiC)
Silicon carbide is another popular abrasive used in grinding wheels. It is much harder than aluminum oxide but is less durable due to its high friability. Silicon carbide excels in grinding harder materials like ceramics, glass, and non-ferrous metals.
- Properties: Silicon carbide has a high hardness level, making it ideal for grinding extremely hard materials. However, because of its friability, it tends to wear down quickly compared to aluminum oxide. This characteristic makes it better suited for applications where frequent wheel dressing is acceptable.
- Applications: Silicon carbide wheels are typically used in grinding non-ferrous metals (e.g., aluminum, brass, copper), ceramics, and glass. It is also useful for cutting and grinding stone, concrete, and masonry materials.
- Advantages:
- Extremely hard and sharp
- Excellent for grinding brittle materials
- Effective for cutting non-ferrous metals
Property | Silicon Carbide |
---|---|
Hardness | Very high |
Friability | High |
Applications | Non-ferrous metals, ceramics, glass |
Best for | Hard, brittle materials |
3. Cubic Boron Nitride (CBN)
Cubic boron nitride (CBN) is an advanced abrasive material used primarily for grinding ferrous metals. It is second only to diamond in hardness and is highly resistant to heat, making it ideal for high-speed grinding.
- Properties: CBN is highly durable and heat-resistant, making it suitable for grinding materials that generate a lot of heat, such as hardened steel. Unlike aluminum oxide or silicon carbide, CBN is much more resistant to wear and provides superior cutting performance over extended periods.
- Applications: CBN grinding wheels are commonly used in high-precision grinding applications, such as sharpening tools, grinding gears, and processing hardened steel parts. CBN is also used in high-speed grinding operations, where traditional abrasives would fail due to excessive heat and wear.
- Advantages:
- Extremely durable and heat-resistant
- Excellent for grinding hardened steels and alloys
- Maintains performance over long production runs
Property | Cubic Boron Nitride (CBN) |
---|---|
Hardness | Very high |
Friability | Low |
Applications | Hardened steel, ferrous metals |
Best for | High-speed, high-precision grinding |
4. Diamond
Diamond is the hardest known abrasive material, making it ideal for precision grinding of hard, brittle materials. Diamond wheels are known for their exceptional wear resistance and cutting ability.
- Properties: Diamond wheels are extremely hard, sharp, and wear-resistant. These properties make diamond an ideal choice for grinding materials such as ceramics, carbide, and stone. However, it should not be used for grinding ferrous metals, as the high temperatures generated during grinding can cause the diamond to decompose.
- Applications: Diamond grinding wheels are commonly used for grinding non-metallic materials like ceramics, glass, and carbide. They are also used in precision grinding applications that require fine surface finishes and tight tolerances.
- Advantages:
- The hardest abrasive available
- Excellent wear resistance
- Ideal for grinding hard, brittle materials
Property | Diamond |
---|---|
Hardness | Highest |
Friability | Very low |
Applications | Ceramics, glass, carbide |
Best for | High-precision grinding of brittle materials |
Choosing the Right Abrasive for Specific Applications
Selecting the right grinding wheel material for a particular application depends on the type of material being ground and the desired results. Below is a summary of how to choose the best abrasive based on the type of workpiece:
- Ferrous Metals (Steel, Iron): For grinding ferrous metals, aluminum oxide and CBN are generally the best options. Aluminum oxide is suitable for softer steels and general-purpose grinding, while CBN is ideal for hardened steels and high-precision work.
- Non-Ferrous Metals (Aluminum, Copper, Brass): Silicon carbide is the preferred abrasive for non-ferrous metals, as it provides efficient material removal without loading up the wheel.
- Ceramics and Glass: Both silicon carbide and diamond are effective for grinding ceramics and glass. For high-precision applications, diamond wheels are often preferred due to their hardness and wear resistance.
- Carbide and Tool Steels: Diamond wheels are the best choice for grinding carbide materials, while CBN wheels excel in grinding tool steels.
Grain Size and Grinding Wheel Performance
In addition to choosing the right abrasive material, selecting the correct grain size is crucial for achieving the desired performance. Grain size affects the cutting action, surface finish, and material removal rate. Coarse grains (lower grit numbers) are typically used for rapid material removal, while finer grains (higher grit numbers) are used for achieving smooth surface finishes.
- Coarse Grains (16–24 Grit): Coarse-grit wheels are used for rough grinding applications where large amounts of material need to be removed quickly. These wheels are ideal for removing welds, preparing surfaces for painting, or grinding down rough edges.
- Medium Grains (36–60 Grit): Medium-grit wheels are used for general-purpose grinding tasks that require a balance between material removal and surface finish. These wheels are commonly used for grinding metal components or sharpening tools.
- Fine Grains (80–120 Grit): Fine-grit wheels are used for finishing operations where a smooth surface is required. They are often used in precision grinding applications to achieve tight dimensional tolerances and polished surfaces.
- Very Fine Grains (150 Grit and Above): Very fine-grit wheels are used for ultra-precise grinding operations, such as grinding carbide tools or producing mirror-like finishes on hardened steel parts.
Bonding Materials and Their Role in Grinding Wheel Performance
The bonding material that holds the abrasive grains together plays a critical role in the performance of the grinding wheel. Different types of bonding materials are used depending on the grinding application:
- Vitrified Bonds: Vitrified bonds are made from clay or ceramic materials and are known for their strength and rigidity. These bonds are ideal for precision grinding operations and can withstand high grinding pressures and speeds.
- Resin Bonds: Resin bonds are more flexible and less brittle than vitrified bonds. They are commonly used in high-speed grinding applications where shock absorption is necessary.
- Metal Bonds: Metal bonds are used for grinding wheels that require extreme durability and wear resistance, such as diamond or CBN wheels. Metal bonds provide excellent heat resistance and are commonly used in high-precision applications.
What is the Role of Coolants in Grinding? How to Optimize Their Use?
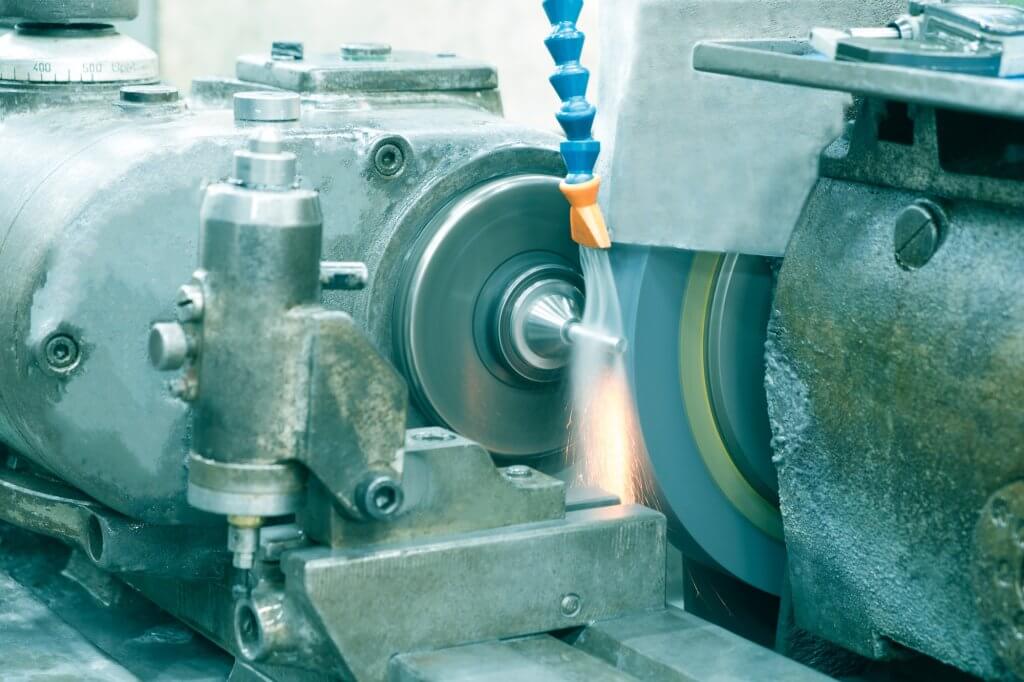
Introduction
In grinding operations, heat is an inevitable byproduct due to the friction generated between the abrasive grains and the workpiece. Excessive heat can cause a variety of issues, such as reduced tool life, poor surface finish, and even thermal damage to the workpiece. To address these problems, coolants or cutting fluids play a crucial role in controlling heat, reducing friction, and improving the overall efficiency and quality of the grinding process.
Coolants are not just about cooling. Their function extends to lubrication, chip removal, and preventing chemical reactions between the tool and the workpiece material. Different coolants are optimized for different grinding applications, and their effectiveness depends on factors such as coolant type, flow rate, nozzle design, and maintenance.
This chapter will explore the multiple roles of coolants in grinding, discuss the different types of coolants, and provide strategies for optimizing their use to improve performance and productivity.
The Role of Coolants in Grinding
Coolants serve several critical functions in grinding operations. While their primary role is to reduce the heat generated during the grinding process, their benefits extend much further:
- Heat Dissipation
- One of the most important functions of a coolant in grinding is to reduce the heat generated at the point of contact between the grinding wheel and the workpiece. Without proper cooling, the excessive heat can damage both the workpiece and the grinding wheel.
- The grinding process involves significant amounts of energy being converted into heat. This heat can cause thermal expansion in the workpiece, leading to dimensional inaccuracies and poor surface quality. Moreover, high temperatures can alter the metallurgical properties of the workpiece, leading to thermal cracks, burns, and phase changes.
- Coolants reduce these risks by absorbing and dissipating heat, keeping the temperature in check and ensuring that both the grinding wheel and the workpiece maintain their integrity.
- Lubrication
- In addition to cooling, coolants also act as lubricants in the grinding process. By reducing friction between the abrasive grains and the workpiece, coolants help improve grinding efficiency and extend the life of the grinding wheel.
- Proper lubrication reduces wear on the abrasive grains, helping to preserve their cutting edges and maintain consistent material removal rates. In some grinding processes, the choice of coolant can significantly affect the cutting performance and overall efficiency.
- Chip Removal
- Coolants help in flushing away chips, debris, and metal fines generated during grinding. This prevents the grinding wheel from becoming clogged, a condition known as “loading,” which can reduce grinding efficiency and damage the workpiece.
- By ensuring that the grinding wheel remains free of debris, coolants contribute to a smoother grinding process and help maintain the sharpness of the abrasive grains.
- Preventing Chemical Reactions
- Coolants also help prevent undesirable chemical reactions between the grinding wheel and the workpiece material. In dry grinding, the high temperatures generated can cause oxidation and other reactions that degrade the quality of the workpiece.
- Coolants prevent these reactions by creating a barrier between the tool and the material, reducing the likelihood of chemical interaction at high temperatures.
- Improving Surface Finish
- The use of coolants can significantly improve the surface finish of the workpiece. Coolants help to minimize wheel wear and maintain the sharpness of the abrasive grains, resulting in a finer and more consistent surface texture.
- Additionally, by reducing thermal expansion and heat-related distortions, coolants help maintain the dimensional accuracy and surface integrity of the workpiece.
Types of Coolants Used in Grinding
There are several types of coolants used in grinding, each suited for different materials, grinding operations, and environmental considerations. The most common coolants include water-based coolants, oil-based coolants, synthetic coolants, and semi-synthetic coolants. Each has unique characteristics, advantages, and drawbacks.
- Water-Based Coolants
- Water-based coolants are widely used in grinding due to their excellent cooling properties. Water has a high thermal capacity, which makes it effective at absorbing and dissipating heat. However, water on its own lacks the lubricating properties needed for effective grinding, so it is often mixed with additives such as oils, surfactants, and corrosion inhibitors.
- These coolants are ideal for operations where heat control is critical, such as surface grinding and high-speed grinding. However, because water-based coolants have poor lubricating properties compared to oil-based coolants, they may not be suitable for all types of grinding.
- Oil-Based Coolants
- Oil-based coolants provide excellent lubrication but are less effective at dissipating heat compared to water-based coolants. They are typically used in grinding applications that require more lubrication, such as cylindrical grinding and tool grinding.
- Oil-based coolants help reduce friction and wear, making them particularly useful for grinding hard materials like hardened steels and alloys. However, because oil-based coolants are less efficient at cooling, they may not be the best choice for operations where heat management is a top priority.
- One of the downsides of oil-based coolants is that they are more prone to fire hazards and are generally more expensive than water-based coolants. Additionally, their use can require more stringent environmental and safety protocols.
- Synthetic Coolants
- Synthetic coolants are water-based fluids that contain chemical additives but no oil. These coolants are designed to provide both cooling and lubrication, making them versatile for a variety of grinding applications.
- Synthetic coolants offer excellent heat dissipation and are often used in high-speed grinding operations where temperature control is critical. They are also formulated to reduce corrosion, provide long-term stability, and minimize bacterial growth in the coolant system.
- While synthetic coolants offer good performance, they can sometimes be more expensive than other types of coolants, and their chemical composition may raise environmental or disposal concerns.
- Semi-Synthetic Coolants
- Semi-synthetic coolants combine the properties of both water-based and oil-based coolants. They contain a small amount of oil, usually less than 30%, along with chemical additives that enhance both cooling and lubricating properties.
- Semi-synthetic coolants are designed to provide a balance between cooling and lubrication, making them suitable for a wide range of grinding operations. They are commonly used in general-purpose grinding applications where both cooling and lubrication are important but not extreme.
- Semi-synthetic coolants offer the advantages of both water and oil-based coolants, but their performance is typically not as specialized as either. They are often chosen for their cost-effectiveness and versatility.
How to Optimize Coolant Use in Grinding
Optimizing the use of coolants in grinding requires a combination of selecting the right coolant, maintaining the proper flow rate, using the correct nozzle positioning, and ensuring regular coolant maintenance. Proper optimization can lead to improved grinding performance, reduced tool wear, and better surface quality.
- Selecting the Right Coolant
- Choosing the right coolant depends on the type of grinding operation, the material being ground, and the desired surface finish. For operations that require high heat dissipation, water-based coolants with added lubricants may be the best choice. For harder materials that require more lubrication, oil-based coolants may be more appropriate.
- It’s important to consider the compatibility of the coolant with both the workpiece material and the grinding wheel. Some coolants can cause chemical reactions or corrosion in certain materials, so it’s critical to match the coolant properties to the materials being used.
- Optimizing Coolant Flow Rate
- Coolant flow rate is crucial in achieving effective cooling and lubrication during grinding. Too little coolant can result in overheating and tool wear, while too much coolant can cause waste and increase operational costs.
- The coolant flow rate should be optimized based on the speed of the grinding wheel, the material removal rate, and the size of the workpiece. In general, the coolant should flow at a rate that ensures complete coverage of the grinding zone and prevents heat buildup.
- Research suggests that an optimal coolant flow rate can reduce grinding temperatures by up to 20%, which can extend tool life and improve surface finish. However, excessive flow rates may result in splashing and coolant waste without additional benefits to the grinding process.
- Nozzle Positioning
- The positioning of coolant nozzles plays a significant role in directing the coolant precisely to the grinding zone. Nozzles that are poorly positioned may lead to ineffective cooling and lubrication, causing overheating and tool damage.
- Proper nozzle positioning ensures that the coolant reaches the point of contact between the grinding wheel and the workpiece. It should also be directed to areas where chips and debris are generated to aid in flushing them away. Advanced nozzle systems, such as coherent jet nozzles, help deliver coolant with high precision and reduce coolant consumption.
- Studies show that proper nozzle alignment can reduce coolant consumption by up to 30% while maintaining effective cooling, improving energy efficiency, and lowering operating costs.
- Maintaining Coolant Quality
- Over time, coolants can degrade due to contamination from metal fines, bacteria, and oil separation. Coolant maintenance is critical for ensuring that the fluid remains effective in cooling, lubricating, and flushing away debris.
- Regular coolant filtration and monitoring help remove contaminants and maintain fluid performance. Periodic checks for pH levels, concentration, and microbial growth are necessary to ensure the coolant is performing at its best.
- Many modern grinding machines come with integrated filtration systems that automatically clean the coolant, reducing the need for manual intervention and extending the life of the coolant.
- Using Coolant Condition Monitoring Systems
- Advanced coolant condition monitoring systems are becoming increasingly popular in high-precision grinding applications. These systems monitor key parameters such as coolant temperature, flow rate, pH levels, and contamination levels in real-time.
- By continuously tracking coolant conditions, these systems can alert operators to any changes that may affect grinding performance. For example, if the coolant temperature rises above a certain threshold, the system can automatically adjust the flow rate or notify the operator to take corrective action.
- Coolant monitoring systems help optimize coolant performance, reduce downtime, and prevent costly damage to both the grinding machine and the workpiece.
- Minimizing Coolant Waste
- Reducing coolant waste is not only important for environmental sustainability but also for cost savings. By optimizing coolant usage and implementing efficient filtration and recycling systems, manufacturers can minimize coolant consumption without compromising performance.
- Closed-loop coolant recycling systems can filter, clean, and reuse coolant, reducing the need for fresh coolant and minimizing disposal costs. This approach helps to reduce the environmental impact of grinding operations while maintaining optimal coolant performance.
Environmental and Health Considerations
While coolants offer numerous benefits, their use comes with certain environmental and health risks that must be carefully managed. Many coolants contain chemical additives that can be harmful to the environment if not disposed of properly. Additionally, the mist generated from coolants can pose respiratory risks to machine operators.
- Environmental Impact
- Improper disposal of coolants can lead to environmental contamination, particularly if the fluids contain harmful chemicals such as heavy metals or petroleum-based oils. It is essential to follow local regulations for coolant disposal and to use environmentally friendly alternatives where possible.
- Water-based synthetic coolants tend to have a lower environmental impact compared to oil-based coolants, but they still require proper management to prevent contamination.
- Health Risks
- Coolant mists generated during high-speed grinding can pose health risks to workers, especially if inhaled over long periods. Prolonged exposure to certain coolant additives, such as biocides and corrosion inhibitors, can lead to respiratory issues and skin irritation.
- To mitigate these risks, it is important to use proper ventilation systems in grinding environments and provide workers with appropriate personal protective equipment (PPE). Coolant mist collectors can also be installed to capture and remove mist from the air, improving workplace safety.
What Common Issues are Encountered During Grinding?
Introduction
Grinding is an essential process in manufacturing, used to achieve high surface finish and tight tolerances for various materials, especially metals. Despite its significance, grinding is often accompanied by various challenges that can affect productivity, surface quality, and tool life. Understanding these common issues and how to address them is critical to optimizing the grinding process and avoiding costly errors.
This section will explore the most frequently encountered issues in grinding, such as heat generation, wheel wear, vibration, and poor surface finish, among others. Each issue will be discussed in terms of its causes, consequences, and potential solutions, with practical examples and insights drawn from industry knowledge and case studies.
1. Heat Generation and Thermal Damage
One of the most common problems in grinding is excessive heat generation. Grinding is a high-energy process where most of the energy is converted into heat. If this heat is not properly managed, it can lead to several issues:
- Causes of Heat Generation: Heat is generated primarily due to friction between the abrasive grains and the workpiece. The higher the grinding speed and depth of cut, the more heat is produced. Additionally, improper coolant application or insufficient coolant flow can exacerbate the problem by failing to dissipate the heat effectively.
- Consequences of Excessive Heat: High temperatures can lead to thermal damage in the workpiece, such as burning, microstructural changes, and warping. Thermal damage can affect the mechanical properties of the workpiece, making it brittle or altering its hardness. Heat can also cause expansion in the workpiece, leading to dimensional inaccuracies.
- Solution: Effective cooling strategies, such as proper coolant selection, nozzle positioning, and flow rate, are essential to managing heat during grinding. Lowering the grinding speed and using a softer wheel can also help reduce heat buildup. Monitoring grinding temperatures and using temperature sensors or infrared cameras can provide real-time feedback to prevent thermal damage.
2. Wheel Wear and Glazing
Grinding wheels, like any cutting tool, wear out over time. Wheel wear can take several forms, including attritious wear, grain fracture, and bond fracture. Additionally, the grinding wheel may become glazed, losing its cutting ability.
- Types of Wheel Wear:
- Attritious Wear: This occurs when the abrasive grains wear down and become dull, leading to a decrease in material removal rate and an increase in grinding forces.
- Grain Fracture: When abrasive grains break prematurely, it can cause uneven wear on the grinding wheel.
- Bond Fracture: This occurs when the bond holding the abrasive grains together breaks down, leading to wheel failure.
- Glazing: Glazing happens when the abrasive grains become too dull to cut effectively, but they remain embedded in the wheel. The wheel surface becomes smooth and shiny, and grinding efficiency decreases significantly.
- Consequences of Wheel Wear and Glazing: Worn or glazed wheels result in higher grinding forces, increased heat generation, poor surface finish, and reduced material removal rates. They can also lead to increased power consumption and premature wheel failure.
- Solution: Regular dressing of the grinding wheel is critical to maintaining its cutting efficiency. Dressing removes dull grains and exposes new, sharp cutting edges, restoring the wheel’s ability to cut effectively. Selecting the appropriate wheel material and bond type for the specific grinding application can also reduce the frequency of wheel wear and glazing.
Type of Wear | Cause | Solution |
---|---|---|
Attritious Wear | Grains become dull due to prolonged use | Regular dressing to expose sharp grains |
Grain Fracture | Premature grain breakage | Use a tougher grinding wheel |
Bond Fracture | Bond holding grains breaks down | Ensure correct wheel selection and bond type |
Glazing | Dull grains remain embedded in the wheel | Frequent dressing and selection of softer wheel |
3. Vibration and Chatter
Vibration, often referred to as chatter in the grinding process, is another prevalent issue. It can result in poor surface finish, increased tool wear, and even damage to the machine itself.
- Causes of Vibration and Chatter:
- Unbalanced Grinding Wheel: An unbalanced wheel can introduce vibration into the grinding process. This imbalance is often due to improper mounting or wear on the wheel.
- Machine Stiffness: Machines that lack sufficient stiffness or rigidity can vibrate during high-force operations like grinding.
- Resonance: The natural frequency of the machine or workpiece can interact with the grinding wheel’s frequency, leading to resonance and chatter.
- Improper Workholding: If the workpiece is not securely held in place, it may vibrate, especially under heavy grinding loads.
- Consequences of Vibration and Chatter: Vibration can lead to uneven material removal, poor surface finish, and increased wheel wear. Over time, it can damage the spindle and other machine components.
- Solution: Balancing the grinding wheel before operation is critical to minimizing vibration. Using precision balancing equipment can help ensure that the wheel rotates smoothly. Additionally, increasing machine stiffness, using vibration-damping materials, and ensuring proper workholding can help reduce vibration. Modifying grinding parameters such as wheel speed, feed rate, or depth of cut can also help mitigate chatter.
4. Poor Surface Finish
Achieving a smooth surface finish is often one of the primary goals in grinding, but several factors can negatively affect the surface quality of the workpiece.
- Causes of Poor Surface Finish:
- Incorrect Wheel Selection: Using a wheel with an inappropriate grain size or bond type can lead to rough surfaces.
- High Grinding Speed or Feed Rate: Excessive speed or feed rate can cause the grinding wheel to leave a rough or uneven surface on the workpiece.
- Vibration and Chatter: As previously mentioned, vibration can leave visible marks and imperfections on the surface of the workpiece.
- Wheel Glazing: A glazed wheel loses its cutting ability, resulting in a burnished rather than ground surface.
- Consequences of Poor Surface Finish: Poor surface finish can affect the functionality of the part, particularly if it requires precision fitting with other components. A rough surface can also negatively impact wear resistance and corrosion protection, leading to premature failure in service.
- Solution: To improve surface finish, ensure the correct grinding wheel is selected for the specific material and application. Optimizing grinding parameters like speed, feed rate, and depth of cut can also improve surface finish. Regular wheel dressing can prevent glazing and maintain cutting efficiency, resulting in a smoother finish.
5. Wheel Loading and Clogging
Wheel loading occurs when workpiece material gets embedded into the pores of the grinding wheel, clogging it. This can significantly reduce the wheel’s ability to cut and leads to increased grinding forces.
- Causes of Wheel Loading:
- Soft Materials: Grinding soft, ductile materials like aluminum or copper can cause material to adhere to the wheel, leading to loading.
- Improper Coolant Application: Insufficient coolant or incorrect coolant type can lead to inadequate chip removal, causing the material to stick to the wheel.
- Consequences of Wheel Loading: A loaded wheel increases the friction between the wheel and the workpiece, generating more heat and reducing the efficiency of the grinding process. It can also lead to surface damage and dimensional inaccuracies in the workpiece.
- Solution: To prevent wheel loading, use a grinding wheel specifically designed for the material being processed. For example, using a wheel with more open pores or a sharper grain structure can help reduce loading. Applying sufficient coolant and selecting the appropriate coolant for the material can also help flush away chips and prevent loading.
6. Burr Formation
Burrs are raised edges or small projections left on the workpiece after grinding. While burrs are more commonly associated with machining processes like milling or turning, they can also occur during grinding.
- Causes of Burr Formation:
- Excessive Cutting Force: High grinding forces, often due to aggressive material removal rates, can lead to burr formation at the edges of the workpiece.
- Tool Wear: A dull or worn grinding wheel can create more friction, leading to burrs.
- Consequences of Burr Formation: Burrs may need to be removed in a separate deburring process, which adds time and cost to the manufacturing cycle. If not properly removed, burrs can affect the functionality and appearance of the finished part.
- Solution: To minimize burr formation, reduce grinding forces by optimizing cutting parameters and using a sharp, properly dressed wheel. Using a finer grit size can also help reduce burrs by producing a smoother cut. Additionally, applying the correct coolant and ensuring proper lubrication during grinding can help reduce the risk of burr formation.
7. Cracking and Distortion
Cracking and distortion are significant issues that can occur during or after grinding, particularly when grinding hard or brittle materials such as hardened steel or ceramics.
- Causes of Cracking and Distortion:
- Thermal Stress: Excessive heat generated during grinding can lead to thermal stresses, which can cause cracking in hard or brittle materials.
- Residual Stress: High grinding forces can induce residual stresses in the workpiece, leading to distortion after the grinding process is completed.
- Improper Coolant Application: Insufficient cooling can exacerbate thermal stress, increasing the likelihood of cracking or distortion.
- Consequences of Cracking and Distortion: Cracked or distorted parts are often unusable and must be scrapped, leading to increased material and production costs. Additionally, cracks may be difficult to detect initially, potentially leading to failures during use.
- Solution: Controlling heat through proper coolant application and reducing grinding forces can help minimize the risk of cracking and distortion. Using a grinding wheel with a softer bond can reduce the forces applied to the workpiece. Regular inspection of parts after grinding can help identify any cracks or distortions before they become problematic.
Issue | Cause | Solution |
---|---|---|
Cracking | Excessive heat and thermal stress | Use proper coolant, reduce grinding forces |
Distortion | Residual stresses from grinding forces | Reduce grinding depth, improve coolant application |
Burr Formation | High grinding forces, tool wear | Optimize grinding parameters, use sharp wheel |
Can Grinding Be Used for High-Hardness Materials?
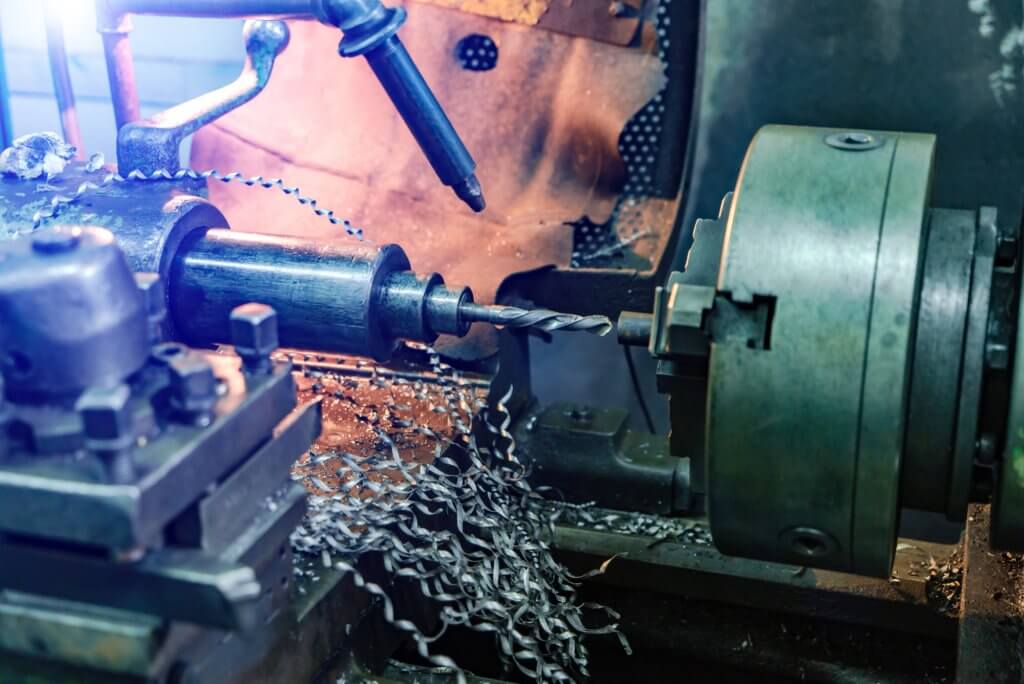
Introduction
Grinding is a critical process in modern manufacturing, widely used for achieving high surface quality, tight tolerances, and precision shaping of materials. It is often associated with metals of moderate hardness, but grinding has also proven to be highly effective for processing high-hardness materials. These materials include ceramics, hardened steels, tungsten carbide, and even superalloys, which are crucial in industries such as aerospace, automotive, and medical devices. The ability to grind these materials efficiently is essential for manufacturing components that require exceptional wear resistance, heat resistance, and mechanical strength.
This section explores the capability of grinding in processing high-hardness materials, the challenges it presents, and how technological advancements in tools, techniques, and machinery have enabled successful outcomes. We will also discuss the types of grinding wheels and coolants best suited for these demanding applications.
Why Use Grinding for High-Hardness Materials?
Grinding is one of the few machining processes that can be used on materials with extremely high hardness levels. This is due to the abrasive nature of grinding tools, which employ materials like diamond, cubic boron nitride (CBN), and silicon carbide to cut through hard surfaces that would be difficult to machine using other processes like turning or milling.
High-hardness materials are typically chosen for applications where durability and resistance to wear, heat, and deformation are essential. For example, in the automotive industry, hardened steel is often used for gears and bearings, while ceramics are favored for components in aerospace due to their high-temperature stability. Grinding allows for the precise shaping and finishing of these materials, providing the high accuracy and surface quality needed for such critical applications.
Grinding offers several advantages when machining high-hardness materials:
- Precision: Grinding can achieve micron-level precision and extremely tight tolerances, which are often required when working with high-hardness materials that will be used in mechanical assemblies or precision tools.
- Surface Finish: High-hardness materials generally require a high-quality surface finish to ensure proper functionality. Grinding can achieve surface finishes that are smoother than those possible with most other machining methods.
- Versatility: Grinding can be applied to various shapes and geometries, including flat surfaces, cylindrical parts, and complex profiles.
- Minimal Tool Wear: With the use of advanced grinding wheels made from superabrasive materials like diamond and CBN, tool wear is significantly minimized, making grinding cost-effective for hard materials.
Challenges in Grinding High-Hardness Materials
While grinding offers numerous advantages for high-hardness materials, it also presents several challenges. These challenges stem from the material properties themselves, as well as the grinding process’s inherent characteristics:
- Heat Generation and Thermal Damage: High-hardness materials, particularly metals like hardened steel and superalloys, tend to generate significant heat during grinding. The excessive heat can lead to thermal damage, including surface burns, microstructural changes, and warping. Thermal cracks may also occur, especially in ceramics, due to their low thermal conductivity and high brittleness.
- High Grinding Forces: High-hardness materials are resistant to plastic deformation, which means that grinding forces tend to be higher than in softer materials. This increases the likelihood of excessive wear on the grinding wheel, as well as the potential for machine and tool damage if the forces are not properly managed.
- Wheel Wear and Glazing: Grinding wheels wear out faster when processing high-hardness materials. In particular, the grains in the grinding wheel may dull quickly, leading to glazing, where the wheel surface becomes smooth and ineffective at cutting. This can result in poor material removal rates and degraded surface quality.
- Material Removal Rate: The removal rate when grinding high-hardness materials is generally slower than when machining softer materials. This is due to the resistance of hard materials to being cut or abraded. Achieving the desired material removal without compromising surface quality or causing thermal damage can be challenging.
Advances in Grinding Technology for High-Hardness Materials
Despite these challenges, technological advancements have significantly improved the grinding process for high-hardness materials. These advancements include new grinding wheel materials, improved machine designs, and better coolant systems.
- Superabrasive Grinding Wheels:
- Diamond Wheels: Diamond grinding wheels are the hardest available and are ideal for grinding ceramics, glass, and other non-metallic hard materials. They offer excellent wear resistance, and their ability to maintain sharp cutting edges over long periods makes them a preferred choice for high-precision applications.
- CBN Wheels: Cubic boron nitride (CBN) grinding wheels are the second hardest abrasive after diamond. CBN is particularly well-suited for grinding hardened steels and nickel-based superalloys, as it retains its hardness and cutting ability at high temperatures, unlike diamond, which can react with ferrous materials.
- Silicon Carbide Wheels: Silicon carbide is another common abrasive for grinding hard materials, particularly ceramics and glass. While not as hard as diamond or CBN, it is often more cost-effective and can be used for less critical applications.
- Improved Coolant Systems:
- Coolants play a vital role in preventing thermal damage when grinding high-hardness materials. Modern coolant delivery systems are designed to ensure that the grinding zone is continuously and efficiently cooled. High-pressure, high-flow coolant systems are especially effective at removing heat and maintaining stable grinding conditions.
- Advanced coolants with chemical additives help reduce friction and heat generation, improving the material removal rate and reducing the risk of thermal damage.
- High-Precision Grinding Machines:
- Today’s grinding machines are designed with increased stiffness and damping to withstand the higher forces generated when grinding hard materials. These machines are also equipped with advanced controls and monitoring systems that can detect and correct any process abnormalities in real time.
- For example, multi-axis CNC grinding machines allow for the precise control of complex geometries while maintaining tight tolerances, even when working with high-hardness materials.
Applications of Grinding High-Hardness Materials
Grinding is used across multiple industries to shape and finish high-hardness materials. Some key applications include:
- Aerospace:
- In the aerospace industry, grinding is commonly used for manufacturing turbine blades, jet engine components, and ceramic matrix composites (CMCs). These materials require exceptional heat resistance and strength, and grinding allows manufacturers to achieve the necessary surface finishes and tight tolerances.
- Automotive:
- Grinding is critical in the automotive industry, particularly for producing hardened gears, camshafts, and crankshafts. These components are often made from hardened steel and require precision grinding to ensure optimal performance and longevity.
- Tool and Die:
- Tool and die makers rely on grinding to achieve the precision and surface finish required for cutting tools, molds, and dies made from hardened steel or carbide. These tools must maintain sharp edges and withstand extreme wear, making grinding an ideal finishing process.
- Medical Devices:
- In the medical device industry, grinding is used to manufacture precision components such as surgical tools and implants made from titanium, stainless steel, or cobalt-chrome alloys. These materials must be ground to exact specifications to ensure compatibility and performance in medical applications.
Case Study: Grinding Tungsten Carbide for Cutting Tools
Tungsten carbide, a high-hardness material, is commonly used for cutting tools due to its extreme wear resistance. However, grinding tungsten carbide presents challenges such as high heat generation, wheel wear, and slower material removal rates.
In one case, a tool manufacturer used diamond grinding wheels to grind tungsten carbide cutting tools. The use of a diamond wheel allowed for a significant reduction in wheel wear and improved material removal rates compared to conventional abrasives. The addition of high-pressure coolant systems further reduced heat generation, preventing thermal damage to the carbide and improving surface finish.
This example highlights how advancements in grinding technology, such as the use of diamond wheels and modern coolant systems, can overcome the challenges of grinding high-hardness materials like tungsten carbide.
How Accurate Can Grinding Achieve in Precision Machining?
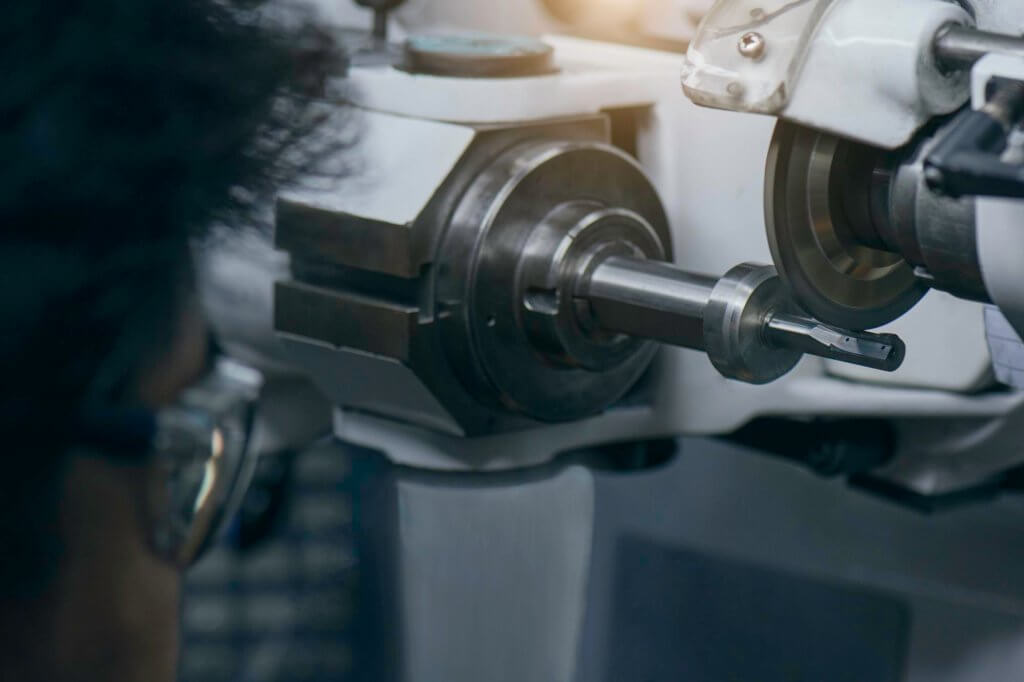
Introduction
Precision machining is the backbone of many industries, where the ability to achieve tight tolerances and highly accurate dimensions is paramount. Among the various machining methods, grinding stands out for its capability to deliver extremely high precision and surface finishes that are difficult to match with other processes. In precision engineering, grinding can achieve tolerances in the range of microns, making it an indispensable process in industries like aerospace, automotive, medical devices, and tooling.
In this section, we will explore the factors that influence the accuracy of grinding in precision machining, examine the achievable tolerances, and understand the technological advancements that have enhanced the precision of grinding over the years. We will also discuss case studies and applications that demonstrate how grinding can meet the stringent accuracy requirements of modern manufacturing.
Factors Influencing Grinding Accuracy
Achieving high accuracy in grinding depends on several factors, including the type of grinding process, the material being ground, the grinding wheel, the machine’s rigidity, and the skill of the operator. Understanding and controlling these factors is crucial for maximizing the precision of grinding operations.
- Type of Grinding Process: Different grinding processes, such as surface grinding, cylindrical grinding, and centerless grinding, offer varying levels of precision. Surface grinding is typically used for flat surfaces and can achieve high levels of dimensional accuracy and surface finish. Cylindrical grinding is more suited for round components, such as shafts or rollers, while centerless grinding is ideal for mass production of small cylindrical parts like pins and bearings. Each process has its unique advantages, and the choice depends on the specific application.
- Material Properties: The material being ground plays a significant role in determining the achievable accuracy. Materials with high hardness, such as hardened steel, ceramics, and superalloys, can be more challenging to grind due to increased heat generation and wear on the grinding wheel. However, advances in grinding wheel technology, such as the use of diamond or CBN wheels, have made it possible to grind even the hardest materials with micron-level precision.
- Grinding Wheel: The selection of the grinding wheel is critical to achieving precision. The grain size, bond type, and wheel hardness all influence the material removal rate, surface finish, and dimensional accuracy. Fine-grit wheels, for example, are better suited for finishing operations where a high-quality surface is required. Coarse-grit wheels, on the other hand, remove material more quickly but may result in a rougher surface finish. Wheel wear and dressing frequency also impact precision, as a dull or clogged wheel will decrease accuracy over time.
- Machine Rigidity: The rigidity of the grinding machine is another key factor in determining the precision of the process. Any flexing or vibration in the machine can lead to inaccuracies in the workpiece. Modern grinding machines are designed with high stiffness and damping to minimize vibrations and ensure consistent precision. CNC grinding machines, in particular, offer enhanced accuracy through precise control of the grinding wheel’s movement, allowing for the grinding of complex geometries with tight tolerances.
- Operator Skill: Although automated systems and CNC technology have reduced the dependency on manual intervention, the skill of the operator still plays a role in ensuring precision in grinding. A knowledgeable operator can optimize grinding parameters, such as speed, feed rate, and depth of cut, to achieve the best results while avoiding issues like burn marks, excessive wheel wear, or surface defects.
Achievable Tolerances in Precision Grinding
One of the defining characteristics of grinding is its ability to achieve extremely tight tolerances. Depending on the specific grinding process, material, and application, tolerances as tight as 1-2 microns (0.001-0.002 mm) can be achieved consistently. In some cases, even sub-micron accuracy is possible, particularly in ultra-precision grinding applications used in industries such as optics and semiconductor manufacturing.
Grinding Process | Typical Achievable Tolerance | Applications |
---|---|---|
Surface Grinding | ± 0.001 mm (1 micron) | Tooling, molds, precision flat surfaces |
Cylindrical Grinding | ± 0.002 mm (2 microns) | Shafts, bearings, spindles |
Centerless Grinding | ± 0.002 mm (2 microns) | Pins, dowels, rollers |
Creep Feed Grinding | ± 0.003 mm (3 microns) | Turbine blades, precision components |
Ultra-Precision Grinding | Sub-micron accuracy (< 1 micron) | Optics, semiconductors |
In precision applications, such as those found in the aerospace or medical industries, even minor dimensional deviations can lead to performance issues or part failure. For instance, in the aerospace industry, the clearance between moving parts in jet engines must be maintained within microns to ensure both safety and efficiency. Grinding is often the go-to process for achieving these critical tolerances.
Surface Finish and Dimensional Accuracy
In addition to dimensional accuracy, surface finish is another critical aspect of precision grinding. The surface finish achieved through grinding is often superior to that of other machining processes, with Ra (roughness average) values as low as 0.025 microns possible in ultra-precision grinding.
Surface finish is important for several reasons:
- Wear Resistance: A smooth surface reduces friction between mating parts, improving wear resistance and extending the component’s lifespan.
- Fatigue Resistance: Surface imperfections, such as roughness or scratches, can act as stress concentrators, reducing the fatigue life of a component. A high-quality surface finish achieved through grinding minimizes the risk of fatigue failure.
- Aesthetic and Functional Requirements: In industries such as medical devices and consumer electronics, the appearance of a component is as important as its function. Grinding allows manufacturers to achieve both.
The following table shows typical surface finishes achievable through different grinding processes:
Grinding Process | Surface Finish (Ra) | Applications |
---|---|---|
Surface Grinding | 0.1-0.5 microns | Flat surfaces, molds |
Cylindrical Grinding | 0.1-0.4 microns | Shafts, rollers |
Centerless Grinding | 0.2-0.6 microns | Small cylindrical parts |
Ultra-Precision Grinding | 0.01-0.025 microns | Optics, semiconductors |
These fine surface finishes are crucial in applications like bearings, where a smooth surface reduces rolling resistance, or in dies and molds, where a high-quality surface ensures the accurate replication of shapes during production.
Technological Advances in Precision Grinding
The ability of grinding to achieve such high levels of precision and surface finish has been significantly enhanced by technological advancements in both grinding tools and machinery. Some key developments include:
- CNC Grinding: CNC technology has revolutionized grinding by enabling precise control over the movement of the grinding wheel. Multi-axis CNC grinders can perform complex grinding operations on parts with intricate geometries, ensuring high precision and repeatability. CNC control also allows for the automation of dressing cycles, which ensures the grinding wheel maintains its sharpness and accuracy throughout long production runs.
- In-Process Measurement Systems: In-process measurement systems are now commonly integrated into high-precision grinding machines. These systems use sensors to monitor the dimensions of the workpiece during grinding, allowing for real-time adjustments to ensure that the final part meets the desired tolerances. This capability is especially valuable in high-volume production environments where consistency and quality control are paramount.
- Superabrasive Grinding Wheels: The use of superabrasive materials like cubic boron nitride (CBN) and diamond in grinding wheels has greatly improved the precision of grinding operations. These materials maintain their hardness and sharpness over long periods, reducing the frequency of dressing and ensuring consistent accuracy even when grinding hard materials like ceramics or hardened steel.
- Adaptive Control Systems: Advanced grinding machines are equipped with adaptive control systems that adjust grinding parameters in response to changes in the material or process conditions. For example, if the system detects an increase in grinding force due to wheel wear, it can automatically reduce the feed rate or increase the flow of coolant to prevent errors and maintain accuracy.
Case Study: Precision Grinding in the Aerospace Industry
In the aerospace industry, precision grinding is critical for manufacturing high-performance components such as turbine blades, gears, and bearings. These parts must withstand extreme temperatures, high pressures, and mechanical stresses while maintaining tight dimensional tolerances.
One notable example is the grinding of nickel-based superalloys used in turbine blades. These materials are difficult to machine due to their high strength and temperature resistance. However, through the use of creep feed grinding and advanced superabrasive wheels, manufacturers can achieve tolerances as tight as 2 microns while producing complex geometries.
Creep feed grinding, which uses a slow feed rate and a deep depth of cut, allows for the efficient removal of material while maintaining precision. This method, combined with high-pressure coolant systems to minimize heat buildup, has proven highly effective in producing the intricate shapes required for aerospace components.
How Does Grinding Improve Surface Quality?
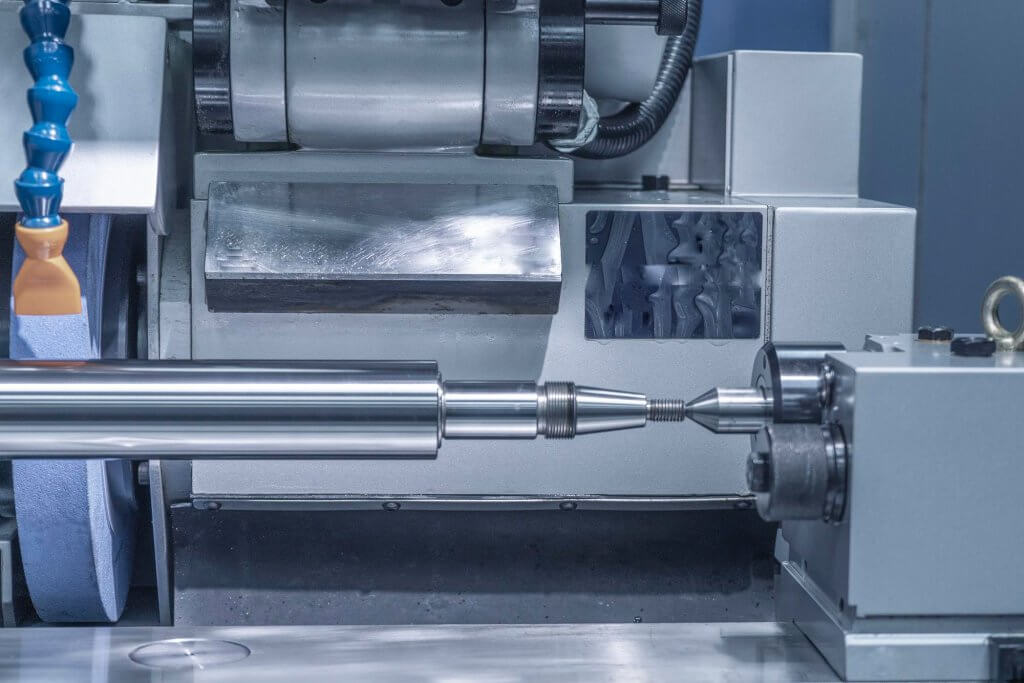
Introduction
Surface quality plays a critical role in the performance, durability, and aesthetic appeal of machined components. In industries such as aerospace, automotive, medical devices, and tooling, the surface finish of parts can impact everything from wear resistance to fatigue strength. Grinding, as one of the most precise machining processes, is widely recognized for its ability to significantly enhance surface quality.
This chapter will explore the factors that influence surface quality during grinding, the role of grinding in improving surface finish compared to other machining methods, and how advancements in grinding technology have contributed to further optimizing surface quality. We will also present data on the achievable surface roughness through different grinding processes and discuss key case studies demonstrating the importance of surface finish in various industrial applications.
The Importance of Surface Quality
Surface quality encompasses several parameters, such as surface roughness, waviness, and the presence of surface defects, which together determine the functionality and longevity of a part. A smooth, high-quality surface can:
- Improve wear resistance: Reducing surface roughness minimizes friction between components, reducing wear and extending the part’s life.
- Enhance fatigue resistance: Surface defects, such as micro-cracks and scratches, can serve as stress concentrators, reducing the fatigue life of a component. A high-quality surface finish helps distribute stress more evenly and prevents the initiation of cracks.
- Improve corrosion resistance: A smoother surface reduces the surface area where corrosive substances can accumulate, thus improving a part’s resistance to environmental degradation.
- Increase aesthetic appeal: In consumer products, medical devices, and other industries where visual appearance is important, a polished surface conveys quality and precision.
In many cases, components that are subjected to heavy loads, high speeds, or corrosive environments require both precision machining and an exceptionally smooth surface. Grinding is commonly employed in these cases to meet demanding surface quality standards.
Key Factors That Affect Surface Quality in Grinding
The surface quality achieved through grinding depends on several factors, including the choice of grinding process, the material being machined, the characteristics of the grinding wheel, and process variables such as speed, feed rate, and coolant application. Understanding these factors is crucial to optimizing surface finish and avoiding common issues like burn marks, scratches, or excessive roughness.
- Grinding Process: Each grinding process offers different levels of precision and surface quality. For example:
- Surface grinding is used to achieve flat surfaces with high precision and smooth finishes.
- Cylindrical grinding is suited for producing high-quality finishes on cylindrical parts, such as shafts and bearings.
- Centerless grinding is ideal for high-throughput production of small cylindrical parts, ensuring both dimensional accuracy and a smooth surface.
- Creep feed grinding enables deep cuts while maintaining a fine surface finish, making it ideal for high-precision components with complex geometries.
- Material Properties: The material being ground can significantly influence the achievable surface quality. Harder materials, such as hardened steel or ceramics, can lead to higher surface roughness if not properly managed. However, with the right combination of grinding wheel and process parameters, even these materials can be ground to very smooth finishes. Softer materials, like aluminum and plastics, are prone to clogging the grinding wheel, which can deteriorate surface finish if the wheel is not regularly dressed.
- Grinding Wheel Characteristics: The choice of grinding wheel plays a central role in determining surface finish. Key factors include:
- Grain size: Finer grains produce smoother surfaces but remove material more slowly, while coarser grains are more aggressive but may leave a rougher surface.
- Bond type: Different bonding agents, such as vitrified or resin bonds, affect the wheel’s behavior during grinding and its ability to maintain sharp cutting edges.
- Wheel hardness: A harder wheel resists wear and maintains precision longer but may result in a rougher finish. Softer wheels, though prone to more frequent wear, can produce better surface finishes in certain applications.
- Dressing frequency: Regular dressing is required to expose new, sharp grains on the wheel, ensuring consistent surface quality throughout the grinding process.
- Grinding Variables: Several key parameters need to be controlled to optimize surface finish:
- Grinding speed: Higher speeds generally improve surface finish but increase heat generation, which can lead to thermal damage and burn marks.
- Feed rate: A slower feed rate can produce a smoother finish by allowing the abrasive grains to cut more evenly.
- Depth of cut: Shallower cuts reduce the load on each abrasive grain, resulting in finer surface finishes.
- Coolant application: Adequate cooling reduces heat build-up, preventing thermal damage and ensuring a more consistent surface finish.
Surface Roughness in Grinding Processes
Surface roughness, often measured as Ra (roughness average), is the most common parameter used to quantify surface quality. The surface roughness values achievable through grinding depend on the grinding process, wheel type, and material properties.
The following table summarizes typical surface roughness values (Ra) achievable through various grinding processes:
Grinding Process | Surface Roughness (Ra) | Application |
---|---|---|
Surface Grinding | 0.1 – 0.5 microns | Tooling, molds, precision flat surfaces |
Cylindrical Grinding | 0.1 – 0.4 microns | Shafts, bearings, spindles |
Centerless Grinding | 0.2 – 0.6 microns | Pins, dowels, rollers |
Creep Feed Grinding | 0.3 – 0.8 microns | Turbine blades, precision components |
Ultra-Precision Grinding | 0.01 – 0.025 microns | Optics, semiconductors, medical devices |
These values show how grinding can deliver superior surface finishes, making it the preferred choice for components that require high precision and durability.
How Grinding Compares to Other Machining Methods
While other machining processes like turning, milling, and electrical discharge machining (EDM) can produce parts with good surface quality, grinding offers significant advantages in terms of precision and smoothness. For example, while turning and milling can achieve surface roughness values between 0.8 and 1.6 microns, grinding can reduce surface roughness to sub-micron levels, as low as 0.01 microns in ultra-precision applications.
- Turning vs. Grinding:
- Turning is typically used for roughing out cylindrical parts, but it cannot match the surface quality achieved by cylindrical grinding. Even with the use of high-precision lathes, turning generally leaves tool marks and surface imperfections that require post-processing. Grinding, on the other hand, can produce a smoother, more uniform surface with fewer imperfections.
- Milling vs. Grinding:
- Milling is excellent for removing large amounts of material quickly and shaping complex geometries. However, the surface finish left by milling operations is typically rougher than that of grinding. When components require both material removal and fine surface finish, milling is often followed by grinding as a secondary process to achieve the desired surface quality.
- EDM vs. Grinding:
- Electrical discharge machining (EDM) is commonly used for cutting hard materials and creating complex shapes that are difficult to machine with conventional methods. While EDM can achieve a relatively fine surface finish, it is limited by the formation of surface imperfections, such as recast layers or micro-cracks, which can negatively impact the part’s performance. Grinding is often used to remove these imperfections and improve the surface quality.
Technological Advancements in Grinding for Surface Quality
Advances in grinding technology have significantly enhanced the ability to improve surface quality. Key innovations include:
- CNC Grinding Machines: CNC technology has allowed for tighter control over the grinding process, enabling manufacturers to achieve higher levels of precision and surface quality. Multi-axis CNC grinders are capable of performing complex grinding operations, ensuring uniform surface finishes on intricate geometries.
- Superabrasive Wheels: The development of superabrasive grinding wheels made from materials such as cubic boron nitride (CBN) and diamond has further improved surface finish. These wheels maintain their sharpness longer than conventional abrasives, enabling more consistent grinding performance and finer surface finishes. For high-hardness materials, superabrasive wheels are essential for achieving both dimensional accuracy and high surface quality.
- In-Process Monitoring Systems: Modern grinding machines are equipped with in-process monitoring systems that allow for real-time adjustments to the grinding parameters. These systems use sensors to detect changes in force, temperature, or vibration, which could affect surface quality. By continuously monitoring and adjusting the process, these systems help ensure that the desired surface finish is consistently achieved.
- Coolant Delivery Systems: Coolant plays a critical role in maintaining surface quality by reducing heat and friction during grinding. Advanced coolant delivery systems use high-pressure jets to precisely target the grinding zone, ensuring optimal cooling and minimizing the risk of thermal damage. This not only improves surface quality but also extends the life of the grinding wheel.
Case Study: Surface Quality in Medical Devices
In the medical device industry, surface quality is critical for both functionality and patient safety. For example, the surface finish of surgical instruments and implants must be smooth to prevent tissue irritation, reduce bacterial growth, and ensure biocompatibility. Grinding is widely used to achieve the necessary surface quality in medical components, particularly for materials like stainless steel, titanium, and cobalt-chrome alloys.
A case study of hip replacement implants shows the importance of grinding in achieving the required surface finish. Hip implants are made from cobalt-chrome alloys, which are difficult to machine using conventional methods. By using high-precision grinding with diamond wheels, manufacturers were able to achieve a surface roughness (Ra) of less than 0.1 microns. This ultra-smooth finish not only ensures proper joint function but also minimizes wear and extends the implant’s lifespan.
How to Control Heat Effects in the Grinding Process?
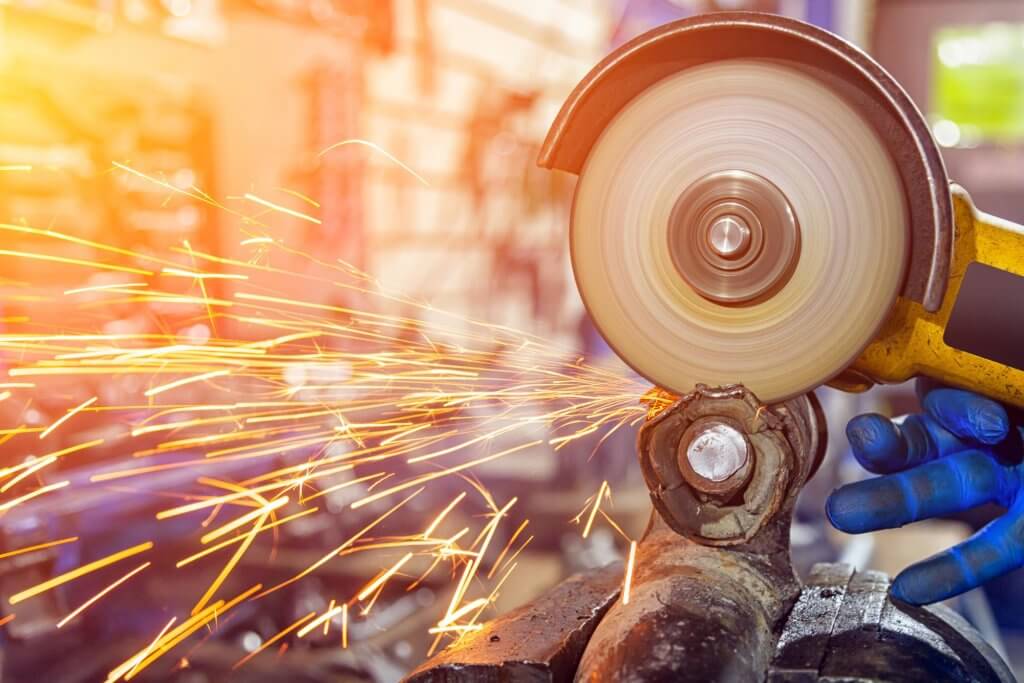
Introduction
One of the most significant challenges in the grinding process is managing the heat generated during machining. Excessive heat can lead to a range of negative effects, including thermal damage to the workpiece, altered material properties, surface burning, and premature wear of grinding tools. As manufacturing industries demand higher precision and greater efficiency, controlling heat in grinding processes has become increasingly critical.
This chapter will explore the sources of heat during grinding, the effects of uncontrolled heat on both the workpiece and the grinding wheel, and the strategies used to manage and minimize these heat effects. Additionally, we will provide insight into advanced cooling methods and technologies that have been developed to tackle thermal issues in grinding.
Heat Generation in the Grinding Process
Heat is generated in the grinding process through a combination of friction between the grinding wheel and the workpiece, plastic deformation, and the cutting action of individual abrasive grains. These mechanisms, while essential to material removal, can also lead to significant heat accumulation at the interface of the grinding wheel and the workpiece.
Several key factors influence the amount of heat generated during grinding:
- Grinding Wheel Speed: As the wheel speed increases, the friction and deformation rates also increase, leading to more heat generation. Higher speeds typically improve material removal rates but often result in higher temperatures.
- Feed Rate and Depth of Cut: Deeper cuts and faster feed rates increase the amount of material removed per pass. While this boosts productivity, it also intensifies heat production, as more abrasive grains are involved in cutting and more energy is consumed.
- Material Properties: The material being ground significantly affects heat generation. Harder materials, such as hardened steel, ceramics, and superalloys, generally generate more heat due to higher friction and resistance to cutting. Softer materials, such as aluminum and plastics, can also generate excessive heat if not properly managed, often leading to workpiece deformation or clogging of the grinding wheel.
- Abrasive Grain Characteristics: The size, shape, and hardness of the abrasive grains impact how heat is distributed during grinding. Fine-grained wheels produce more friction but remove less material per pass, potentially increasing heat concentration. Conversely, coarser grains reduce friction but may leave a rougher surface.
- Coolant Use: The role of coolants in mitigating heat generation cannot be overstated. Without proper coolant application, the grinding process can lead to excessive heat buildup, resulting in surface burns, thermal cracks, and even metallurgical changes in the workpiece.
The Impact of Excessive Heat
Excessive heat in grinding can cause a range of detrimental effects on both the workpiece and the grinding wheel. The following sections outline some of the key issues related to heat:
- Thermal Damage to the Workpiece:
- Surface Burns: One of the most visible signs of excessive heat is surface burning. These burns can weaken the structural integrity of the workpiece and lead to further issues during part usage. Burns often appear as discolored regions on the surface and can be caused by localized overheating due to poor coolant application or an aggressive grinding process.
- Metallurgical Changes: Grinding can induce phase changes in the workpiece material, especially in high-carbon steels. Excessive heat can lead to the formation of martensite, a hard and brittle phase, which compromises the toughness of the material. In some cases, these metallurgical changes reduce the overall strength and fatigue life of the part.
- Thermal Expansion and Distortion: High temperatures during grinding can cause thermal expansion of the workpiece, leading to distortion or dimensional inaccuracies. As the workpiece cools, uneven thermal contraction may occur, resulting in warping or residual stresses.
- Impact on Surface Integrity:
- Cracks and Microcracks: Thermal stress can cause surface cracks, both visible and microscopic. These cracks can weaken the part’s structural integrity, making it more susceptible to failure under load or during service.
- Surface Roughness Degradation: Excessive heat can lead to changes in surface roughness, affecting the final quality of the part. Higher roughness values lead to increased friction and wear in the final application.
- Wear and Tear on the Grinding Wheel:
- Grinding Wheel Glazing: When excessive heat causes the abrasive grains on the grinding wheel to smooth over without breaking away, it results in “glazing.” This reduces the cutting ability of the wheel and increases friction, further exacerbating heat generation.
- Premature Wheel Wear: Overheating can lead to rapid wear of the grinding wheel, shortening its life. When the wheel wears too quickly, it must be dressed or replaced more frequently, increasing production costs.
Methods to Control Heat in Grinding
Controlling heat in the grinding process is essential for maintaining workpiece integrity, prolonging tool life, and achieving consistent surface quality. There are several strategies and methods that can be employed to mitigate heat effects:
- Optimizing Grinding Parameters:
- Reducing Wheel Speed: Lowering the grinding wheel speed can significantly reduce heat generation, though this often comes at the cost of slower material removal rates. The optimal balance between speed and heat control is critical to maximizing productivity while minimizing thermal damage.
- Adjusting Feed Rate and Depth of Cut: Reducing the depth of cut and feed rate can help distribute heat more evenly across the workpiece. This minimizes localized hot spots, which are prone to thermal damage. Shallow cuts and slower feeds are particularly useful for precision grinding applications where surface quality is paramount.
- Selecting the Right Wheel for the Job: The choice of abrasive material and grain size can impact heat generation. Harder abrasives, such as CBN or diamond, offer superior heat resistance and are ideal for grinding hard materials like ceramics or superalloys. Coarse grains generally result in lower temperatures by reducing friction, but a compromise between surface finish and heat control is often necessary.
- Using Advanced Grinding Wheel Technology: Modern grinding wheels are engineered to minimize heat buildup during machining. Some advancements in wheel technology include:
- Porous Grinding Wheels: These wheels have increased porosity, allowing for better coolant flow through the grinding zone and reducing the heat generated by friction.
- Hybrid Bond Wheels: These combine the toughness of resin bonds with the strength of vitrified bonds, creating wheels that are resistant to heat-induced wear while still capable of maintaining cutting efficiency.
- Self-Sharpening Wheels: Certain wheel materials are designed to break away in controlled patterns during grinding, exposing fresh cutting edges that help to reduce heat buildup.
- Effective Coolant Application: Coolants are crucial in the grinding process to dissipate heat, lubricate the workpiece, and prevent surface burns or thermal cracking. However, simply applying coolant is not enough—proper application techniques are essential for maximizing its effectiveness. Key considerations include:
- Coolant Flow Rate: Increasing the flow rate of the coolant helps remove heat more effectively. However, it is important to match the flow rate to the grinding wheel speed to prevent splashing or coolant starvation.
- Targeted Delivery: Coolant must be delivered directly into the grinding zone where the wheel contacts the workpiece. Advanced nozzle designs that direct high-pressure coolant streams to the exact point of contact can dramatically improve cooling efficiency.
- Coolant Type: The choice of coolant also plays a vital role in controlling heat. Water-based coolants are commonly used for general grinding applications, but oil-based coolants or synthetic coolants may be more effective in high-heat situations, particularly when grinding hard materials.
- Dressing the Grinding Wheel: Regular dressing of the grinding wheel is important for maintaining its cutting efficiency and preventing excessive heat generation. By removing clogged debris and exposing fresh abrasive grains, dressing helps reduce friction and improve coolant penetration, ultimately leading to cooler grinding conditions.
- Adaptive Control Systems: Advances in machine control technology have led to the development of adaptive control systems that monitor grinding conditions in real time and adjust process parameters accordingly. These systems use sensors to detect changes in temperature, vibration, or force and can automatically modify wheel speed, feed rate, or coolant flow to prevent overheating. Adaptive control systems are especially valuable in high-precision or high-volume production environments, where consistent quality and minimal downtime are critical.
- Minimizing Spark Generation: Sparks are an indicator of excessive heat in grinding and should be minimized whenever possible. Adjusting grinding parameters, such as reducing wheel speed or optimizing coolant application, can help reduce spark generation and keep temperatures within an acceptable range.
Advanced Cooling Techniques in Grinding
While traditional cooling methods, such as flood coolant systems, are effective in many grinding applications, some advanced cooling techniques offer superior heat management for high-precision or high-heat processes.
- Cryogenic Cooling: Cryogenic cooling involves using liquid nitrogen (LN2) or carbon dioxide (CO2) to cool the grinding zone. These coolants are applied at extremely low temperatures and offer excellent heat dissipation. Cryogenic cooling is particularly useful for grinding difficult materials, such as titanium or superalloys, which generate significant heat during machining. By reducing the temperature of the grinding zone, cryogenic cooling can prevent thermal damage, improve surface finish, and extend tool life.
- Minimum Quantity Lubrication (MQL): Minimum quantity lubrication is an eco-friendly cooling method that involves applying a small amount of high-performance lubricant directly to the grinding zone. MQL significantly reduces heat generation while minimizing the amount of coolant used. This method is particularly advantageous in applications where excessive coolant use could cause contamination or where coolant disposal is costly.
- High-Pressure Coolant Delivery: High-pressure coolant delivery systems use precisely directed, high-velocity streams of coolant to penetrate the grinding zone. These systems are highly effective at reducing heat in high-speed grinding applications, especially when machining hard metals or ceramics. High-pressure delivery ensures that the coolant reaches the grinding interface, preventing the formation of thermal hot spots and improving overall cooling efficiency.
Case Study: Heat Control in Aerospace Grinding
In the aerospace industry, precision components made from high-temperature alloys, such as Inconel and titanium, require careful heat management during grinding. These materials are known for their poor machinability and tendency to generate excessive heat, which can lead to thermal damage and metallurgical changes.
One case study involved the grinding of turbine blades made from Inconel 718. Due to the heat-sensitive nature of the material, cryogenic cooling was implemented using liquid nitrogen to reduce the temperature of the grinding zone. By applying cryogenic cooling, the manufacturer was able to achieve a 40% reduction in surface roughness and extend the life of the grinding wheel by 60%, while also preventing the formation of surface cracks or burns.
Another study focused on the grinding of titanium parts for aircraft engines. High-pressure coolant delivery was used to minimize heat accumulation, resulting in improved surface finish and reduced tool wear. The high-pressure system was able to direct coolant precisely into the grinding zone, lowering temperatures and ensuring the integrity of the workpiece.
How is Vibration Generated During Grinding, and How Can It Be Resolved?
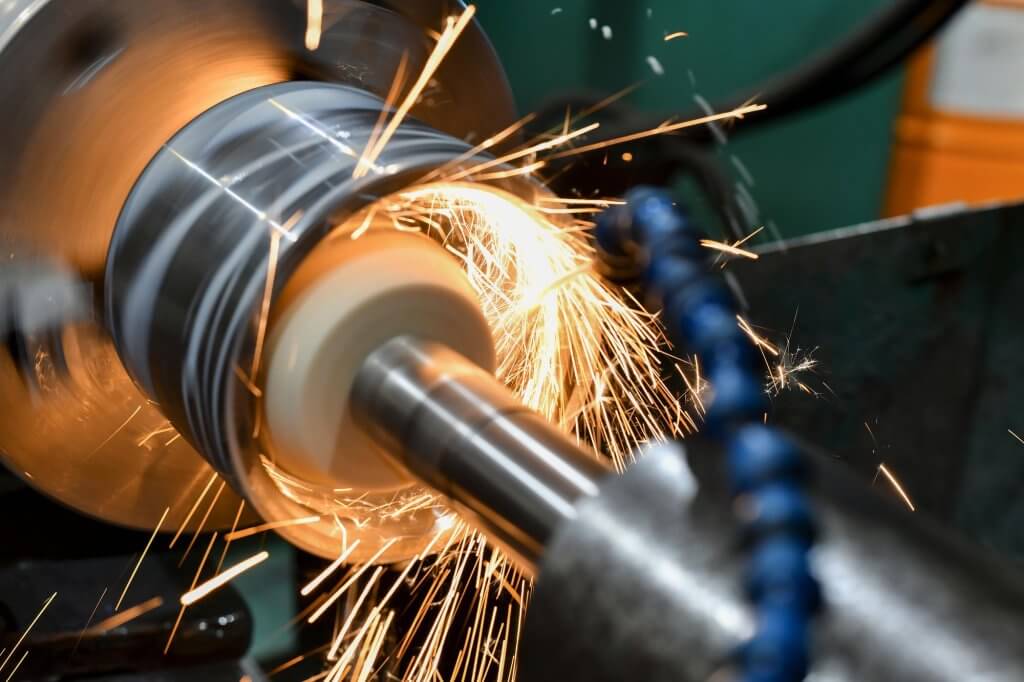
Introduction
Vibration during the grinding process is a common challenge that can affect the quality of the finished product, reduce the life of the grinding wheel, and impact the overall efficiency of the operation. Understanding how vibrations are generated and developing methods to resolve them is critical to achieving optimal grinding results. This chapter delves into the causes of vibration in grinding, its effects on surface finish and precision, and strategies to mitigate or eliminate vibrations.
Causes of Vibration in Grinding
Vibrations during grinding are caused by various factors related to the machine, the workpiece, the grinding wheel, and environmental conditions. These vibrations can be broadly categorized into two main types: forced vibrations and self-excited (regenerative) vibrations.
- Machine-Related Factors:
- Imbalance in Grinding Wheel: One of the most common sources of vibration is an imbalance in the grinding wheel. When the wheel is not uniformly dense or is improperly mounted, it rotates unevenly, leading to vibration. Even minor imbalances can amplify over time, creating significant operational issues.
- Misalignment: If the machine components, such as the spindle or workpiece holder, are not properly aligned, it can introduce oscillations. Misalignment causes variations in the force applied during grinding, resulting in uneven material removal and vibration.
- Worn Bearings or Spindle: Over time, the bearings in the grinding machine’s spindle can wear out, leading to increased play or looseness in the system. This mechanical wear introduces vibration as the spindle is no longer able to rotate smoothly. The same applies to a spindle that has become unbalanced or damaged.
- Machine Rigidity: Insufficient machine rigidity is a major contributor to vibrations. If the frame, bed, or components of the grinding machine flex or deform under load, vibrations will be generated. Machines with insufficient stiffness or damping capacity are particularly prone to this issue.
- Workpiece-Related Factors:
- Workpiece Clamping: If the workpiece is not clamped securely, it can shift or vibrate during grinding. This instability leads to vibrations that not only affect the surface finish but also damage the grinding wheel. Clamping pressure that is too low or unevenly distributed can amplify this effect.
- Workpiece Geometry: The shape and mass of the workpiece can influence the vibration characteristics. Long, slender workpieces are more prone to vibrations due to their lower stiffness. Similarly, workpieces with thin walls or delicate structures can vibrate easily, particularly when subjected to high cutting forces.
- Grinding Wheel and Abrasive Factors:
- Wheel Imbalance: As mentioned earlier, improper mounting, uneven distribution of abrasive grains, or wear patterns on the grinding wheel can cause imbalance, leading to vibration.
- Wheel Dressing: Over time, the grinding wheel wears down and becomes less efficient at cutting, which leads to increased friction and heat. This wear can cause the wheel to lose its sharpness and lead to chatter (a form of vibration). Regular dressing of the grinding wheel is essential to maintain balance and reduce vibration.
- Abrasive Grain Characteristics: The size, shape, and type of abrasive grains used in the grinding wheel can also contribute to vibration. Abrasives that are too coarse or irregularly shaped may not cut smoothly, leading to uneven forces on the workpiece and subsequent vibration.
- Cutting Conditions:
- Feed Rate and Depth of Cut: If the feed rate is too high or the depth of cut too deep, the grinding forces can exceed the capacity of the machine, causing vibration. Excessive material removal can lead to uneven distribution of forces, generating oscillations in the system.
- Grinding Speed: Operating the grinding wheel at an inappropriate speed (either too high or too low) can lead to unstable cutting forces. Speed fluctuations or deviations from the optimal speed range for the wheel can increase the likelihood of vibration.
- Environmental Factors:
- External Vibrations: Machines located near other industrial equipment or heavy machinery can be subjected to external vibrations. These vibrations can transfer through the floor or machine supports, affecting the grinding process.
- Temperature Changes: Variations in temperature can cause thermal expansion or contraction of machine components, leading to misalignment or instability in the system. This thermal movement can introduce vibration into the grinding process, particularly if the machine bed or supports are not thermally stable.
Effects of Vibration on Grinding Process
Vibration in the grinding process can have several adverse effects that diminish the quality of the machined part and reduce the efficiency of the operation. Key consequences of vibration include:
- Surface Finish Degradation: Vibration during grinding can result in poor surface finish due to inconsistent cutting forces. Instead of producing a smooth, even surface, vibrations cause irregularities such as ridges, waves, or chatter marks on the workpiece. These surface imperfections can increase friction in mechanical components, leading to accelerated wear and reduced performance.
- Reduced Dimensional Accuracy: Vibrations cause the grinding wheel to oscillate, leading to non-uniform material removal. This fluctuation in material removal results in dimensional errors, making it difficult to achieve the required tolerances. Precision grinding, which often demands tight dimensional control, can be particularly affected by vibration-induced inaccuracies.
- Tool Wear: Grinding wheel wear is accelerated by vibrations. The constant oscillation increases the rate at which abrasive grains wear away or become dull, reducing the wheel’s effective life. Additionally, vibrations can cause the wheel to glaze, losing its cutting ability and increasing the need for frequent dressing.
- Increased Heat Generation: Vibrations disrupt the cutting process, leading to increased friction between the grinding wheel and the workpiece. This friction generates additional heat, which can result in thermal damage to the workpiece (e.g., burns, cracks, or metallurgical changes) and exacerbate wear on the grinding wheel.
- Fatigue of Machine Components: Prolonged exposure to vibration can lead to the fatigue of machine components. Bearings, spindles, and even the frame of the grinding machine can suffer from accumulated stress, leading to breakdowns, decreased machine life, and increased maintenance costs.
Methods to Mitigate and Resolve Vibration in Grinding
Resolving vibration issues in grinding involves a combination of preventive measures, corrective actions, and the use of advanced technologies. Below are the key strategies for mitigating and resolving vibrations during grinding:
- Balancing the Grinding Wheel:
- Dynamic Balancing: One of the most effective ways to reduce vibration is by dynamically balancing the grinding wheel. This involves using specialized balancing machines to adjust the wheel’s mass distribution and ensure even rotation. Dynamic balancing can be performed at different stages of the wheel’s life to maintain balance as the wheel wears down.
- Precision Mounting: Ensuring that the grinding wheel is properly mounted and aligned with the spindle is critical for minimizing imbalance. Even small deviations in mounting can lead to significant vibration issues.
- Regular Dressing of the Grinding Wheel:
- Wheel Dressing: Regular dressing of the grinding wheel helps maintain its cutting efficiency and reduces vibration caused by wheel glazing or wear. Dressing removes debris and clogged abrasive grains, exposing fresh, sharp grains that cut more smoothly and with less vibration.
- Automated Dressing Systems: Many modern grinding machines are equipped with automated dressing systems that continuously or periodically dress the grinding wheel. This reduces manual intervention and ensures consistent wheel performance, minimizing vibration.
- Optimizing Machine Rigidity and Alignment:
- Machine Stiffness: To reduce vibrations caused by machine deflection, it is essential to use grinding machines with high rigidity. A robust machine frame and bed can withstand the forces generated during grinding without flexing or deforming, reducing the likelihood of vibration.
- Component Alignment: Ensuring that all machine components, such as the spindle, workpiece holder, and guides, are properly aligned can prevent many vibration issues. Misalignment should be corrected through precision calibration and regular maintenance checks.
- Proper Clamping and Fixturing:
- Secure Workpiece Clamping: The workpiece must be securely clamped to prevent any movement during grinding. Using appropriate fixtures and clamping systems ensures stability, particularly when working with long, slender, or delicate parts. Flexible clamping systems that can adapt to different workpiece geometries are also beneficial for reducing vibration.
- Vibration Damping Fixtures: For workpieces that are prone to vibration due to their geometry, special vibration-damping fixtures can be used. These fixtures absorb the energy generated by the grinding process, reducing oscillation in the workpiece.
- Optimizing Cutting Parameters:
- Adjusting Feed Rate and Depth of Cut: Reducing the feed rate and depth of cut can help decrease the forces that contribute to vibration. While this may reduce productivity, it ensures better surface finish and dimensional accuracy by minimizing oscillations.
- Optimizing Wheel Speed: Operating the grinding wheel within its recommended speed range is essential for stable cutting. Deviating from the optimal speed can increase vibration, especially if the wheel is spinning too slowly or too quickly.
- Using Damping Technologies:
- Hydraulic or Pneumatic Damping Systems: Advanced grinding machines are equipped with hydraulic or pneumatic damping systems to reduce the transmission of vibrations. These systems absorb and dissipate vibrations, allowing for smoother grinding operations.
- Viscoelastic Damping Materials: Applying viscoelastic damping materials to machine components can further reduce vibration transmission. These materials absorb vibration energy and convert it into heat, which is then dissipated.
- Real-Time Monitoring and Adaptive Control:
- Vibration Sensors: Modern grinding machines often incorporate vibration sensors that monitor oscillations in real time. These sensors provide feedback to the machine’s control system, allowing for automatic adjustments to speed, feed rate, or other parameters to reduce vibration.
- Adaptive Control Systems: Adaptive control systems use feedback from sensors to dynamically adjust the grinding process. By making real-time corrections based on the machine’s vibration levels, these systems ensure smoother operation and reduce the risk of vibration-related defects.
- Isolating the Machine from External Vibrations:
- Vibration Isolators: If the grinding machine is located near other equipment or in a high-vibration environment, it may be necessary to isolate the machine from external vibrations. Vibration isolators, such as rubber pads or springs, can be installed under the machine to absorb vibrations transmitted through the floor.
- Environmental Control: Maintaining a stable environment, particularly in terms of temperature, can reduce the risk of vibration. Thermal expansion and contraction of machine components can be minimized by controlling the ambient temperature and ensuring consistent operating conditions.
Case Study: Vibration Control in Aerospace Component Grinding
In the aerospace industry, the grinding of high-precision components, such as turbine blades and engine parts, requires extremely tight tolerances and flawless surface finishes. Vibration is a significant concern in these applications due to the complex geometries and material properties involved.
In one case study, a manufacturer experienced significant vibration issues while grinding nickel-based superalloy turbine blades. These components are highly susceptible to vibration due to their slender shape and the difficulty of machining superalloys. By implementing the following solutions, the manufacturer was able to reduce vibration and improve product quality:
- Wheel Balancing and Dressing: The grinding wheel was dynamically balanced, and regular dressing was implemented to maintain cutting efficiency. This helped reduce vibration caused by wheel imbalance and glazing.
- Use of Vibration-Damping Fixtures: Custom fixtures with vibration-damping properties were designed to securely hold the turbine blades during grinding. These fixtures absorbed the energy generated during the process, minimizing oscillations in the workpiece.
- Real-Time Monitoring: Vibration sensors were installed on the machine, providing real-time feedback to the control system. When vibration levels exceeded a certain threshold, the machine automatically adjusted the cutting parameters to stabilize the operation.
As a result, the manufacturer was able to achieve a 25% improvement in surface finish and a 30% reduction in cycle time, while also extending the life of the grinding wheel.
How to Optimize the Grinding Process? – From Parameter Settings to Process Improvements
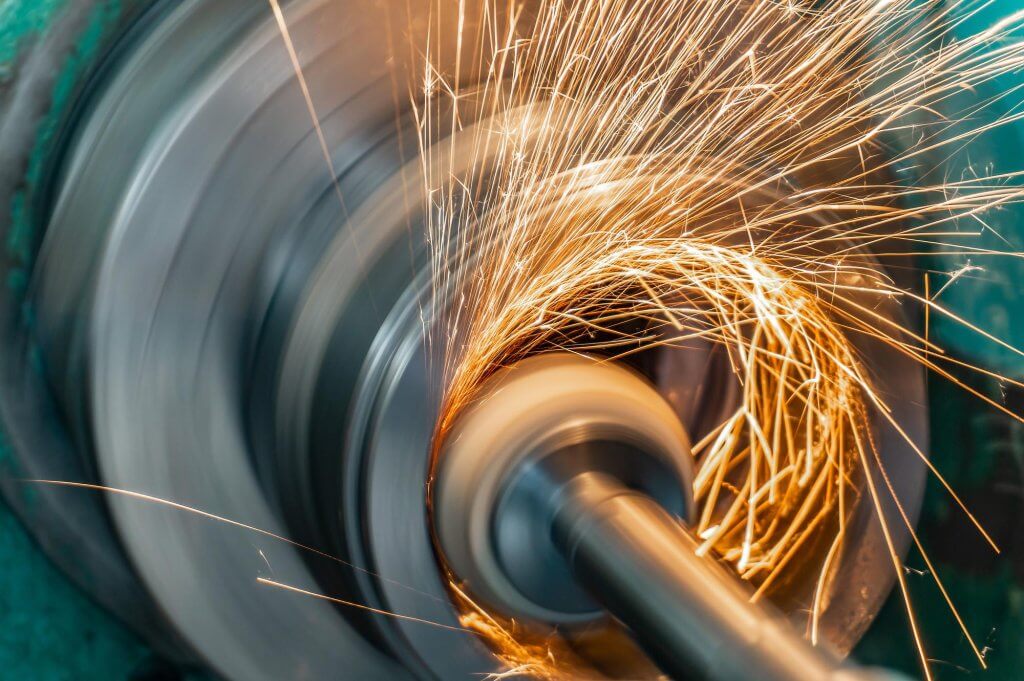
Introduction
Optimizing the grinding process is essential for improving productivity, reducing costs, and achieving better surface finishes. Whether grinding high-precision components for aerospace, automotive parts, or general manufacturing, process optimization involves adjusting a range of variables. These include parameter settings, machine setup, tooling choices, and the use of advanced technologies. By focusing on all aspects of the process, manufacturers can enhance efficiency, reduce waste, and ensure the highest levels of product quality.
In this chapter, we will explore key strategies for optimizing the grinding process, from selecting the right parameters to implementing advanced technologies and monitoring techniques. By understanding and controlling each factor, companies can significantly improve their grinding operations.
Key Grinding Parameters to Adjust
The grinding process is controlled by several key parameters, each of which directly influences the quality, accuracy, and speed of the operation. Here are the critical parameters that can be adjusted to optimize performance:
- Grinding Speed
- Wheel Speed (Surface Speed): The speed at which the grinding wheel rotates, often measured in meters per second (m/s), directly affects the cutting efficiency and heat generation in the process. Too high a wheel speed can cause overheating, burning, or excessive tool wear, while too low a speed can reduce productivity and lead to poor surface finishes.
- Optimal Range: Typically, a surface speed of 20–40 m/s is ideal for most materials, but this range can vary depending on the workpiece material and grinding wheel specifications.
- Feed Rate
- Workpiece Feed Rate: The rate at which the workpiece is fed into the grinding wheel is crucial in determining material removal rates and surface finish quality. A higher feed rate increases material removal but can cause poor surface quality or vibration. Conversely, a low feed rate enhances surface smoothness but reduces throughput.
- Balancing Feed Rate: It’s important to balance the feed rate to optimize both productivity and surface finish. For high-precision applications, slower feed rates are recommended to avoid excessive heat and vibration.
- Depth of Cut
- Initial and Final Depth of Cut: The depth of cut refers to the amount of material removed in each pass of the grinding wheel. Setting the right depth is essential for optimizing material removal efficiency. An aggressive depth of cut (e.g., >0.1 mm per pass) increases productivity but can lead to higher tool wear, while a shallow depth (e.g., <0.01 mm per pass) can produce a better surface finish but lower productivity.
- Incremental Cutting: Optimizing grinding depth involves incremental cutting, where several passes are made with decreasing depth to achieve precision without overloading the machine or grinding wheel.
- Grinding Wheel Selection
- Grain Size, Type, and Bonding: The abrasive grain size and type (e.g., aluminum oxide, silicon carbide, diamond) should be selected based on the material being ground and the desired surface finish. Coarser grains provide faster material removal, while finer grains give smoother finishes. The bonding material (e.g., resin or vitrified) determines the wheel’s rigidity and wear resistance.
- Wheel Dressing: Regular dressing of the grinding wheel maintains its cutting efficiency, prevents glazing, and ensures consistent surface finishes.
- Coolant Flow and Application
- Coolant Type and Flow Rate: Proper cooling is critical to preventing excessive heat buildup that can damage both the workpiece and the grinding wheel. The flow rate, pressure, and type of coolant (e.g., water-soluble or oil-based) must be optimized to ensure effective cooling and lubrication.
- Directed Flow: Ensuring the coolant is directed exactly at the grinding zone improves thermal control and extends tool life.
Advanced Process Improvement Techniques
Beyond parameter adjustments, several advanced techniques can be employed to further optimize the grinding process. These techniques involve leveraging modern technologies and tools to gain real-time insights into the operation and make proactive adjustments.
- In-Process Monitoring and Control Systems
- Vibration and Force Sensors: Incorporating sensors that monitor vibration levels, grinding forces, and spindle speed can provide real-time data on machine performance. These sensors help operators detect and correct any deviations from optimal conditions, such as imbalance in the grinding wheel or excessive heat generation.
- Load Monitoring: Monitoring the power load on the grinding spindle helps prevent overloading, which can cause tool breakage or overheating. By adjusting parameters dynamically based on load data, manufacturers can optimize cutting efficiency while minimizing risk.
- Adaptive Control Technologies
- Real-Time Process Adjustment: Adaptive control systems use real-time feedback to adjust grinding parameters automatically during operation. These systems can modify wheel speed, feed rate, or depth of cut in response to changing workpiece conditions, such as variations in material hardness.
- Benefits of Adaptive Control: By continuously optimizing parameters in real-time, manufacturers can achieve higher precision, reduce tool wear, and prevent damage to the workpiece. Adaptive control is particularly beneficial in high-volume production environments where consistent quality is critical.
- Machine Rigidity and Damping Improvements
- Improving Machine Stiffness: Machines with higher structural rigidity experience less deflection under load, leading to more accurate grinding and less vibration. Reinforcing the machine bed, frame, and spindle housings can improve performance, particularly in precision grinding applications.
- Use of Damping Materials: Integrating damping materials into machine components can help absorb vibrational energy, reducing oscillations that affect surface quality. Many advanced grinding machines now feature built-in damping systems or viscoelastic materials to minimize vibration.
- Tool Life Optimization
- Predictive Maintenance: Monitoring grinding wheel wear and using predictive maintenance software can help determine the optimal time to replace or re-dress the grinding wheel. This prevents downtime due to unexpected wheel failure and maximizes tool life.
- Tool Condition Monitoring: Some advanced systems use acoustic emission or force sensors to detect signs of wear or damage to the grinding wheel. These systems can trigger automatic dressing cycles or alert operators when maintenance is needed, optimizing tool performance.
- Minimizing Heat Generation
- Optimized Cutting Speeds and Coolant Application: Excessive heat generation during grinding can lead to thermal damage (such as burns or cracks) on the workpiece. By selecting appropriate cutting speeds and ensuring effective coolant application, heat buildup can be minimized.
- Coolant Filtration Systems: Coolants must be kept free of contaminants, which can reduce their cooling effectiveness. Implementing filtration systems ensures that coolants maintain their thermal efficiency throughout the process, leading to better control of heat generation.
Practical Case Studies in Grinding Optimization
- Automotive Industry – Cylinder Head Grinding In the automotive industry, grinding cylinder heads is a critical process that requires precision and speed. One manufacturer faced issues with surface roughness and heat-related distortion in the cylinder heads due to high material removal rates. By optimizing the feed rate and introducing real-time vibration monitoring, they achieved a 20% improvement in surface finish and reduced rework by 15%.
- Aerospace Industry – Precision Blade Grinding A precision grinding operation for aerospace turbine blades encountered issues with excessive wheel wear and inconsistent surface finishes. By implementing adaptive control systems that monitored grinding forces in real-time, the company was able to adjust the depth of cut dynamically. This resulted in a 30% increase in tool life and improved dimensional accuracy across the batch.
Best Practices for Parameter Settings in Grinding
Table 1: Example Optimal Grinding Parameters for Common Materials
Material | Grinding Wheel Speed (m/s) | Feed Rate (mm/s) | Depth of Cut (mm) | Coolant Type |
---|---|---|---|---|
Mild Steel | 25-35 | 0.5-1.0 | 0.02-0.05 | Water-soluble |
Hardened Steel (>50 HRC) | 30-40 | 0.2-0.5 | 0.01-0.02 | Oil-based |
Aluminum | 20-30 | 1.0-2.0 | 0.05-0.1 | Water-soluble |
Titanium | 15-25 | 0.2-0.5 | 0.01-0.02 | Water-soluble |
Inconel/Superalloys | 20-30 | 0.2-0.5 | 0.01-0.02 | Oil-based or LN2 |
Table 2: Suggested Dressing Intervals Based on Material and Grinding Wheel Type
Grinding Wheel Type | Material | Recommended Dressing Interval |
---|---|---|
Vitrified Bond (Aluminum Oxide) | Mild Steel | Every 2-3 hours |
Resin Bond (Diamond) | Hardened Steel (>50 HRC) | Every 1-2 hours |
Vitrified Bond (CBN) | Inconel/Superalloys | Every 3-4 hours |
Resin Bond (Silicon Carbide) | Aluminum | Every 4-6 hours |
Implementing Process Improvements
In addition to parameter optimization, manufacturers can implement a range of process improvements to enhance overall grinding efficiency. These include:
- Lean Manufacturing Practices
- Waste Reduction: Identifying and eliminating waste in the grinding process—whether it’s excessive material removal, rework, or inefficient machine setup—can significantly improve productivity.
- Continuous Improvement (Kaizen): Regularly reviewing grinding operations and involving operators in the improvement process helps identify areas for further optimization.
- Automation and Robotics
- Automated Loading and Unloading: By automating the loading and unloading of workpieces, manufacturers can reduce cycle times and improve throughput. Robots or gantry systems can be integrated into grinding cells to streamline the material handling process.
- Automated Wheel Dressing: Advanced grinding machines are equipped with automated dressing systems that maintain optimal wheel performance without manual intervention. This ensures consistent surface finish quality and prolongs tool life.
- Training and Skill Development
- Operator Training: Well-trained operators are key to optimizing the grinding process. Training programs should focus on proper machine setup, parameter adjustment, and troubleshooting techniques. Skilled operators can also make on-the-fly adjustments to optimize performance.
- Data-Driven Decision Making: Providing operators with access to real-time data from sensors and control systems allows for informed decision-making. This empowers them to adjust parameters proactively based on current conditions, leading to better outcomes.
Future Trends in Grinding Optimization
The future of grinding optimization will likely involve even greater integration of digital technologies, machine learning, and artificial intelligence. By leveraging predictive analytics, manufacturers will be able to optimize processes in ways that were previously unimaginable. Key trends to watch include:
- Digital Twins: The creation of digital models of the grinding process allows manufacturers to simulate and optimize grinding operations before actual production. Digital twins can predict potential issues, such as vibration or heat generation, and allow for virtual testing of different parameter settings.
- Artificial Intelligence (AI): AI-driven algorithms can analyze historical grinding data and recommend parameter settings for future jobs. Over time, these systems learn and adapt, continuously improving process efficiency and quality.
- Additive Manufacturing Integration: As additive manufacturing becomes more widespread, hybrid machining processes that combine additive and subtractive techniques (like grinding) will emerge. These processes will require new strategies for optimization to manage both technologies effectively.
Which Industries Use Grinding Technology Most Widely?
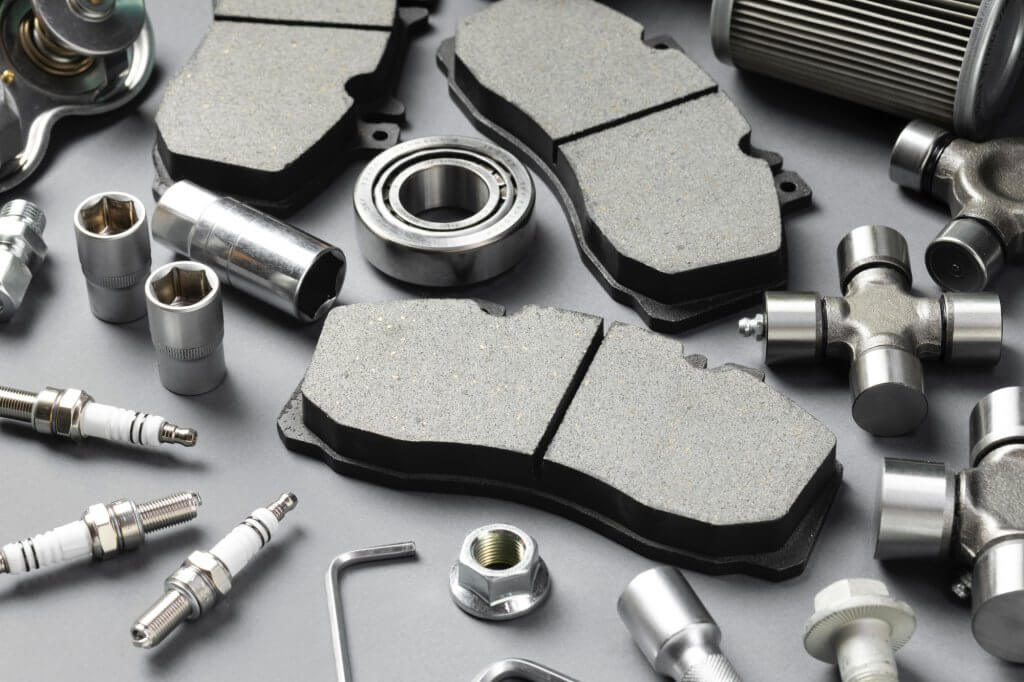
Grinding technology is a vital component in many industries, offering precise material removal and high-quality surface finishes. Its versatility and ability to handle various materials, from soft metals to super-hard alloys, make it indispensable across sectors ranging from automotive and aerospace to medical device manufacturing. As demands for tighter tolerances, superior surface finishes, and complex geometries increase, grinding technology continues to evolve, integrating advanced automation, adaptive controls, and smarter materials.
This chapter explores the most prevalent industries utilizing grinding technology, how they apply it, and why it remains critical for achieving specific industrial goals. We will highlight key applications, common challenges, and future trends within each sector.
1. Automotive Industry
Applications in Automotive Grinding
In the automotive industry, grinding plays a pivotal role in manufacturing critical components such as gears, crankshafts, camshafts, and cylinder heads. These parts require high precision and durability to withstand the harsh operating conditions of modern engines and transmissions. Grinding ensures not only the exact dimensional accuracy but also the surface finish necessary for optimal performance and reduced friction in moving parts.
For example:
- Crankshaft Grinding: Crankshafts must have highly accurate geometries and surface finishes to ensure smooth engine operation. Grinding processes like cylindrical grinding are used to finish crankshaft journals and pins, enhancing wear resistance and longevity.
- Camshaft Grinding: Camshafts, which control the opening and closing of engine valves, require grinding for high precision and surface integrity. The process ensures the correct profile for cam lobes, which impacts engine efficiency and emissions.
- Gear Grinding: Gears in automotive transmissions require precise tooth profiles and surface finishes. Gear grinding, using methods such as form grinding or generating grinding, ensures optimal load distribution and reduces noise, vibration, and harshness (NVH).
Challenges in Automotive Grinding
The primary challenge in automotive grinding is balancing throughput with precision. Automotive manufacturers need to maintain high volumes of production without sacrificing quality. Heat generation and tool wear are also significant concerns, especially when grinding hardened steels used in engine components. To mitigate these issues, the industry increasingly uses advanced coolants and adaptive control systems that optimize cutting parameters in real-time.
Future Trends in Automotive Grinding
The rise of electric vehicles (EVs) is driving the demand for new grinding techniques. For instance, EV motors use magnets and rotor assemblies that require precise grinding to ensure efficiency and minimize energy loss. In addition, lightweight materials like aluminum and composites are becoming more common, requiring adjustments in grinding processes to accommodate different material properties.
2. Aerospace Industry
Precision Grinding in Aerospace
The aerospace industry relies heavily on grinding for manufacturing turbine blades, landing gear, and engine components. These parts often consist of superalloys, titanium, and ceramics—materials that are difficult to machine using traditional methods but can be ground to tight tolerances and superior surface finishes.
- Turbine Blade Grinding: Turbine blades operate in extreme environments, subjected to high temperatures and pressures. Grinding is essential for achieving the precise shape and surface finish required for aerodynamic efficiency and durability. Complex geometries like cooling holes or contours are often ground to within microns of accuracy.
- Landing Gear Grinding: Landing gear components, typically made from high-strength steels and titanium alloys, undergo grinding to achieve the required surface hardness and fatigue resistance. Surface integrity is critical to prevent cracks or failures in such critical applications.
- Engine Component Grinding: Components like turbine disks, combustion chambers, and rotors require grinding to achieve the necessary surface finish and dimensional accuracy. These parts are critical for maintaining the engine’s overall efficiency and safety.
Challenges in Aerospace Grinding
One of the biggest challenges in aerospace grinding is working with difficult-to-machine materials like Inconel, which are extremely heat-resistant and prone to work hardening. Additionally, maintaining high precision while minimizing thermal damage is crucial, as any surface defects or micro-cracks can lead to part failure in operation.
Future Trends in Aerospace Grinding
As jet engines become more fuel-efficient, the demand for advanced grinding technologies will continue to grow. Grinding processes for composite materials and hybrid structures (combining metals and ceramics) are being developed. The use of intelligent grinding systems that can adapt to the material being machined and adjust parameters in real-time will also become more prevalent.
3. Medical Device Manufacturing
Grinding in Medical Devices
In the medical device industry, grinding plays a crucial role in manufacturing surgical tools, orthopedic implants, dental equipment, and stents. The sector demands extremely tight tolerances, especially for parts that will be implanted in the human body or used in precision surgery.
- Orthopedic Implants: Grinding is used to manufacture prosthetic hips, knees, and other implants, ensuring a high degree of precision and smoothness. These components must meet strict biocompatibility and performance standards.
- Surgical Tools: Instruments such as scalpels, forceps, and scissors are ground to achieve sharp edges and precise shapes, improving the surgeon’s ability to perform intricate procedures.
- Dental Tools and Implants: Grinding is employed in the production of dental tools and implants, where accuracy is critical for both functionality and aesthetics.
Challenges in Medical Grinding
The medical industry requires compliance with strict regulations (e.g., FDA standards) and ensuring biocompatibility. Surface finish quality is critical in reducing the risk of infection or material rejection in implants. Additionally, the use of difficult-to-machine materials such as titanium and certain biocompatible alloys makes grinding a key process in ensuring accuracy without compromising material properties.
Future Trends in Medical Grinding
As additive manufacturing becomes more prevalent in medical device production, hybrid processes that combine 3D printing with precision grinding will emerge. This will allow for complex, custom designs that are post-processed through grinding to achieve the required surface finish and dimensional tolerances. Furthermore, miniaturization trends in medical devices are pushing the development of micro-grinding technologies for producing extremely small, yet precise, components.
4. Tool and Die Manufacturing
Grinding in Tool and Die Production
Tool and die manufacturing heavily relies on grinding for creating precise molds, punches, and cutting tools. The ability to grind hardened materials like tool steels and carbide to extremely fine tolerances makes it indispensable in this industry.
- Punch and Die Grinding: The manufacture of punches and dies used in forming operations often requires grinding to ensure that the tools can withstand high wear and maintain sharp edges for cutting or shaping metals.
- Mold and Die Grinding: Precision grinding is used to create molds for injection molding or die casting, where accurate cavities are required to produce parts with tight tolerances.
Challenges in Tool and Die Grinding
Tool and die manufacturers face the challenge of grinding extremely hard materials while maintaining tight tolerances. Heat generation can lead to dimensional distortion or softening of the tool material, affecting tool life. Efficient coolant application and precise control of grinding parameters are essential in this sector.
Future Trends in Tool and Die Grinding
Advances in grinding wheel technology, such as the use of superabrasives like CBN and diamond, are making it easier to grind tough materials with less wear and heat generation. Automated grinding systems are also being increasingly adopted, enabling faster production cycles and consistent quality.
5. Oil and Gas Industry
Applications of Grinding in Oil and Gas
The oil and gas industry uses grinding technology for manufacturing drill bits, valves, and pumps used in exploration and extraction activities. Given the harsh operating conditions, these components need to be extremely durable and resistant to wear and corrosion.
- Drill Bit Grinding: Grinding is used to manufacture hard, wear-resistant drill bits capable of withstanding the extreme forces encountered during drilling.
- Valve and Pump Grinding: Valves and pumps used in the oil and gas industry require precise machining to ensure proper sealing and pressure control. Grinding is essential in creating tight-fitting surfaces that can handle the high-pressure conditions in pipelines and refineries.
Challenges in Oil and Gas Grinding
Components in the oil and gas industry must endure extreme environments, which makes it necessary to grind tough materials such as stainless steel, Inconel, and other corrosion-resistant alloys. Achieving the required surface finishes for sealing purposes while maintaining the integrity of the material is a key challenge.
Future Trends in Oil and Gas Grinding
The push toward more automated and remote-controlled drilling and extraction systems will increase the need for advanced grinding processes that can produce more durable components. Furthermore, as the industry moves toward deeper offshore drilling, the need for high-performance materials and grinding processes will grow.
6. Electronics and Semiconductor Industry
Precision Grinding in Electronics Manufacturing
The semiconductor and electronics industries require ultra-precision grinding for producing wafers, circuit boards, and microelectromechanical systems (MEMS). Grinding is critical in achieving the smoothness and flatness necessary for electronic components, where even minor imperfections can cause performance issues.
- Wafer Grinding: Grinding silicon wafers to precise thicknesses ensures uniformity across the surface, which is critical for subsequent photolithography and etching processes in semiconductor manufacturing.
- MEMS Grinding: Micro-grinding processes are employed to create tiny, precise components used in sensors and actuators found in electronic devices and systems.
Challenges in Electronics Grinding
The biggest challenge in electronics grinding is achieving the high degree of precision required while minimizing surface damage or contamination. The semiconductor industry, in particular, demands ultra-clean processes and surfaces to prevent defects during chip fabrication.
Future Trends in Electronics Grinding
As electronic devices become smaller and more powerful, there will be increased demand for micro-grinding and polishing technologies. Grinding techniques for new materials, such as graphene or advanced ceramics used in semiconductors, will also need to evolve to keep pace with industry demands
FAQ
- Why does grinding sometimes result in surface burns, and how can it be prevented?
Surface burns occur when excessive heat is generated during grinding, leading to oxidation and surface damage. To prevent this, use proper coolant, reduce cutting depth, and optimize wheel speed and feed rate. - How to handle tool wear during the grinding process?
Tool wear can be managed by regularly monitoring and dressing the grinding wheel. Using harder abrasives, optimizing grinding parameters, and applying coolants effectively can also reduce wear. - What safety precautions are essential when working with grinding machines?
Wear personal protective equipment (PPE) such as safety goggles, gloves, and ear protection. Ensure the grinding wheel is properly mounted, regularly inspected, and never exceed the recommended speed. - What types of grinding wheels are suitable for soft materials?
For soft materials, silicon carbide or aluminum oxide wheels with coarser grit are suitable. Softer bond types are also preferred to prevent clogging and to allow the wheel to self-dress. - How can you improve material removal rates in grinding?
Increase material removal rates by optimizing wheel speed, feed rate, and depth of cut. Selecting a more aggressive grinding wheel and applying the correct coolant can also help. - What factors affect the efficiency of grinding in mass production?
Key factors include wheel selection, proper machine maintenance, use of automated systems, consistent coolant application, and optimized grinding parameters like speed and feed rate. - What are the signs that a grinding wheel needs replacement?
A wheel may need replacement if it shows visible cracks, reduced performance, glazing, or requires frequent dressing. Vibrations or noise during operation are also warning signs. - How can grinding be used for complex shapes and profiles?
Complex shapes and profiles can be achieved using CNC grinding machines with precise control of wheel movement. Special form wheels or dressing techniques can also shape the wheel for the desired profile. - What are the key differences between dry and wet grinding?
Wet grinding uses coolant to cool the wheel and workpiece, reducing heat and improving surface finish, while dry grinding generates more heat and may result in higher tool wear and surface damage. - How to ensure uniformity and precision in large batch grinding?
Consistency in large batch grinding is achieved through regular dressing of wheels, maintaining machine calibration, using automated systems for monitoring, and applying coolants uniformly. - What are the specific maintenance requirements for grinding machines?
Grinding machines require regular inspection, lubrication, alignment checks, and timely wheel dressing. Keeping the machine clean and free from debris also extends its service life. - How can grinding be automated for higher consistency and efficiency?
Automation can be integrated through CNC systems, robotic arms for loading and unloading, and sensors for real-time monitoring of wheel wear and cutting parameters, ensuring consistent quality and output. - What environmental regulations apply to grinding operations?
Regulations vary by region but generally cover dust control, waste management, and coolant disposal. Proper ventilation and filtration systems are also required to meet air quality standards. - What role does grit size play in determining grinding performance?
Grit size determines the roughness of the grind. Finer grits produce smoother finishes but remove material more slowly, while coarser grits allow for faster material removal but rougher surfaces. - How to reduce noise levels in industrial grinding settings?
Noise can be reduced by using quieter grinding machines, installing noise barriers, ensuring proper wheel selection, and maintaining machine components to avoid vibrations that increase noise.
.
Other Articles You Might Enjoy
- Grinding Machines: Definition, Uses, Types, and Applications - The Core Tools of Manufacturing
The term "grinding machine" might be unfamiliar to many, but it plays an indispensable role in our daily lives. Whether it’s the car you drive, the electronics you use, or…
- Can Precision CNC Machining Compensate for Material Weaknesses in High-Stress Applications?
The Role of CNC Machining in Material Enhancement In engineering applications where materials are subjected to high stress, the choice and treatment of materials are crucial for the integrity and…
- Grinding Techniques and CNC Machining in Rubber Compression Molding Machine Production
Rubber compression molding machines are essential in various industries that require precise and durable rubber components. One of the key processes in manufacturing these machines is ensuring that all parts,…
- Elevating Surface Finish of CNC Machining Parts with High-Speed Techniques
High-speed cutting techniques have revolutionized CNC machining, offering not only increased production efficiency but also superior surface finishes on machined parts. The appeal of high-speed machining lies in its ability…
- Impact of Surface Roughness on CNC Machined Parts: Material and Process Variables
Introduction to CNC Machining and Surface Roughness CNC machining, abbreviated from Computer Numerical Control machining, is a manufacturing technique that uses pre-written computer software for dictating the movement of factory…
- High-Precision CNC Machining for Military Applications
Introduction to High-Precision CNC Machining in Military Applications The technical realm of high-precision Computer Numeric Control (CNC) machining is fast becoming integral to the military sector. This process, which relies…