Plastics play a crucial role in today’s manufacturing sector since they are widely accessible, generally economical, and suitable for common production techniques like CNC machining, 3D printing, and injection molding.
One factor contributing to this growth is the expanding use of plastic materials in manufacturing. As more industries seek lightweight, durable, and cost-effective solutions, plastic CNC machining provides an efficient way to create custom parts from a wide range of plastic materials.
Moreover, advancements in technology are further fueling industry growth. High-speed machining, advanced software, and automation are improving the speed, accuracy, and quality of plastic CNC machining, making it an increasingly viable option for mass production.
This article describes methods that are accessible, materials that are suitable for the procedure, and other elements that can support your project.
What Is Plastic CNC Machining Used For?
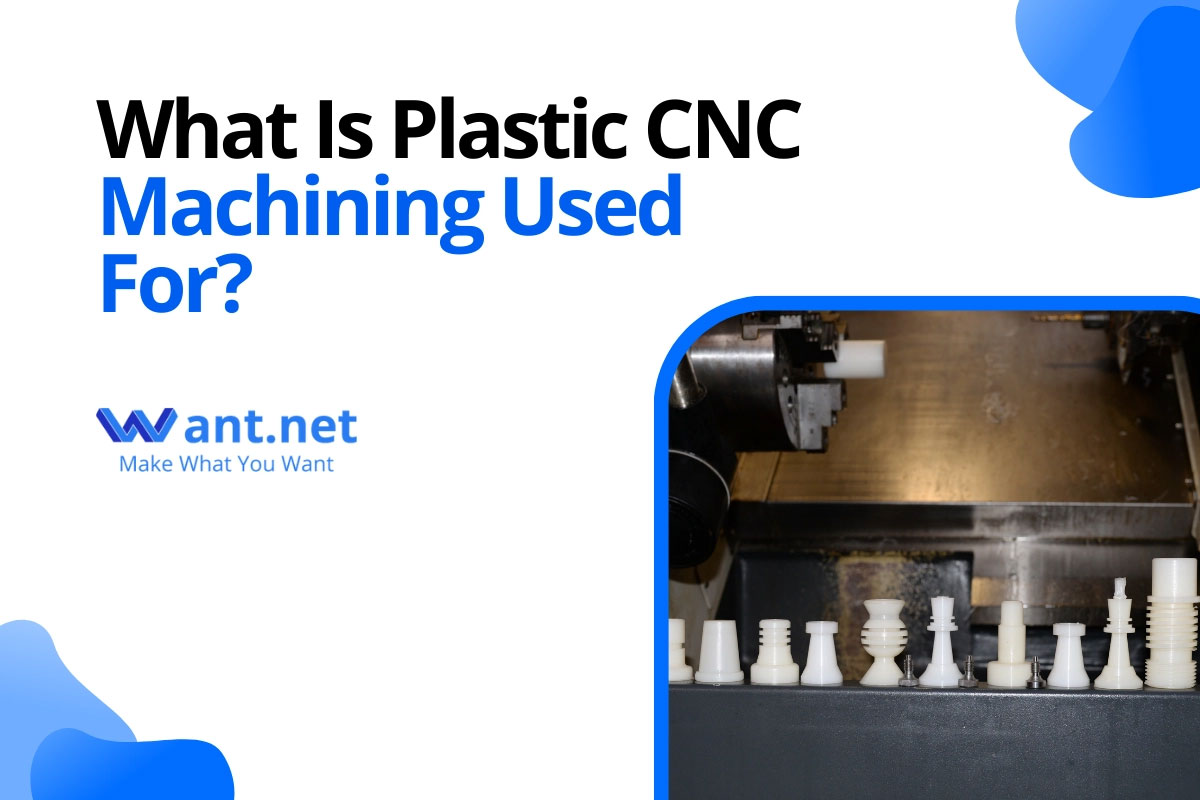
Plastic CNC machining is a method of creating 3D items from plastic material that uses computer-aided design (CAD) and computer-aided manufacturing (CAM).
This plastic machining process is helpful for prototyping, design and development, and manufacturing. In this article, we will discuss the advantages and applications of plastic CNC machining.
What Are the Benefits of Using Plastic CNC Machining?
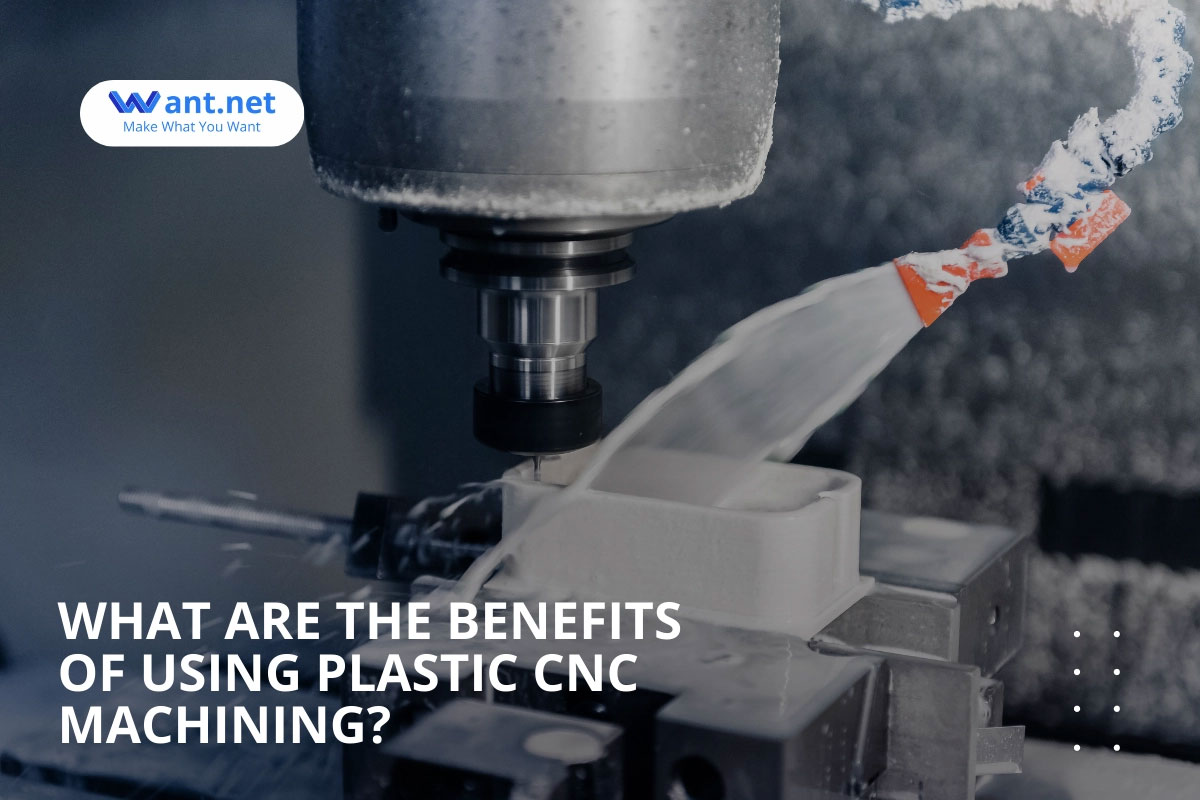
Plastic CNC machining is a method for cutting and forming plastic objects using computer-controlled tools. It also has many advantages:
- Speed: This process is fast and efficient.
- Tight tolerances: Plastic components manufactured by a CNC machine can have very little variance.
- Complex shapes: Moreover, CNC machining makes it possible to produce intricate designs that would be difficult or impossible to make using traditional methods. In CNC machining, a computer directs the movement of the cutting tools, allowing for the manufacture of CNC plastic parts with a high degree of accuracy and precision.
- Cost-effective for small batches: A CNC machine is frequently used to produce low-volume production of plastic prototypes since it is reasonably quick and simple to set up and hence more affordable than conventional milling techniques.
- Accuracy and repeatability: Because of its accuracy, the process may also be used to produce huge quantities of similar parts, making it beneficial for the mass manufacturing of complex parts.
A CNC machine is a flexible and effective tool that can be utilized to produce a wide range of plastic components.
5 Different Types of Plastics and Their Properties
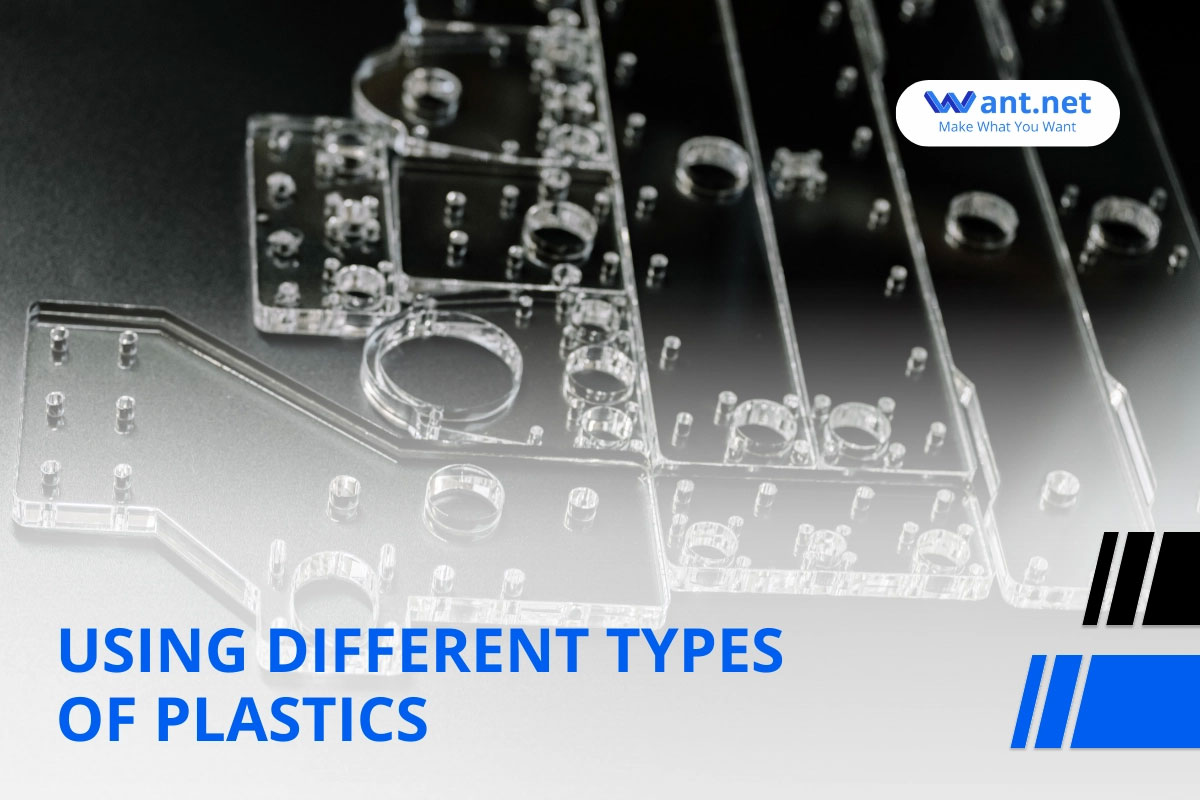
CNC machining uses various types of plastic materials, depending on the application. Here are a few examples:
1. Acrylonitrile Butadiene Styrene (ABS)
ABS is a commonly used engineering thermoplastic that has excellent machinability, strong heat resistance, and impact strength and resistance. This plastic maintains its mechanical stability over time and is a good insulator, making it perfect for electrical applications.
Mechanical specifications:
- Hardness shore D: 100
- Tensile strength: 29.8 – 43 MPa
- Flexural modulus: 1.6 – 2.4 GPa
- Elongation at break: 10 – 50%
ABS Listing
Applications for this material include keyboard covers, electronics enclosures, and auto dashboard parts.
Nylon 66
Nylon, usually referred to as polyamide (PA), is a broad group of low-friction engineering thermoplastics with superior impact strength, abrasion resistance, and chemical resistance.
Nylon 66 is very well-suited for CNC machining since it is durable and long-lasting enough for a variety of uses in manufacturing sectors, including medical and automotive equipment. This material has a high-performance level by nature, can withstand heavy use, and is resistant to damage from gasoline and oil.
Mechanical specifications:
- Hardness: 116, Rockwell R
- Tensile strength: 76 MPa
- Flexural modulus: 2965 MPa
- Elongation at break: 150 – 300%
Polyetheretherketone (PEEK)
PEEK is a strong thermoplastic that stands out for having an unusually wide range of mechanical characteristics. This material can withstand temperatures of up to 260 °C (480 °F), liquids, wear, creep, and fatigue. It is also insoluble in all common solvents, lightweight, and durable enough to withstand adverse climatic conditions.
PEEK is widely used in CNC machining to replace metal, much like nylon. Piston units, essential components of aero plane engines, and dental syringes are examples of common applications.
Mechanical specifications (unfilled PEEK):
- Toughness: 80 – 94 J/m
- Density: 1.26 – 1.32 g/cm3
- Flexural modulus: 3.7 – 4 GPa
- Elongation at break: 30 – 150%
(Polyacetal polyoxymethylene) POM
POM is among the most machinable of all CNC plastics and is most frequently referred to by its trade name, Delrin. POM is a high-strength, high-stiffness plastic with outstanding heat, abrasion, moisture, chemical, and chemical resistance that plastic machinists choose when they need it.
The most popular POM grades for CNC machining are Delrin 570 and 150 because of their outstanding dimensional stability and adaptability for producing precision parts with tight tolerances.
Mechanical specifications (Delrin 570):
- Tensile strength at break: 53 MPa
- Impact strength, notched IZOD: 6 kJ/m²
- Flexural modulus: 4600 MPa
- Tensile modulus: 4900 MPa
5. Polycarbonate (PC)
PC is commonly used and widely used in the industrial sector. It is naturally heat-retardant, strong but lightweight, and has good electrical insulation properties. Also, PC is more effective than other commercial thermoplastics.
Plastic machinists should be aware that PC is naturally transparent, can transmit light as effectively as glass, and readily absorbs color. Safety eyewear, surgical tools, circuit breakers, and CDs/DVDs are a few examples of common applications.
Mechanical specifications:
- Hardness shore D: 90-95
- Tensile strength at break: 55-77MPa
- Flexural modulus: 2.2-2.5GPa
- Elongation at break: 50-120%
What Are the Plastic CNC Machining Methods?
Plastic CNC Turning
Plastic CNC turning includes clamping a plastic part to a lathe, which is subsequently moved or turned opposite to the cutting tool. There are different varieties of CNC turning, each with a set of special goals and results. For example, CNC turning that is straight or cylindrical is appropriate for large cuts, while CNC turning that is tapered results in a unique cone-like shape.
The following are suggestions for producing plastic parts with CNC turning machines:
- Ensure that cutting edges have a negative back rake to minimize friction.
- Making cutting edges with ample relief angles.
- Polishing top surfaces to improve surface finish and help avoid material buildup.
- Making use of C-2 grade fine carbide inserts.
We advise using a feed rate of 0.015 IPR for rough cuts. We suggest a feed rate of 0.005 IPR for final cuts that are more precise. The clearance, rake, and side angles for CNC turning may change according to the material used, so product teams should be aware of this as well.
Plastic CNC milling
Plastic CNC milling is a computer-controlled milling technique that eliminates material from a solid workpiece using only a milling cutter, which is a cylindrical moving tool. Three-axis mills and multi-axis mills are the two subcategories of CNC milling machines.
The best 3-axis mills for producing simpler designs are ones that rotate the cutting tool or the workpiece over three linear axes. The best multi-axis mills for creating plastic components with complicated geometries have four or more axes.
Particular guidelines for using CNC milling to produce plastic parts include the following:
- Employing carbon tooling when milling plastics bonded with glass or carbon fibers
- Increasing spindle speeds using clamps
- Shaping internal edges and pockets with end mills to reduce tensile stress
Plastic CNC drilling
CNC drilling uses a power drill to create holes in a plastic block. The suitable holes are then drilled after a spindle that holds the block and the CNC drill lowers onto the block. A CNC drilling machine can be used with a variety of drill presses, including upright, bench, and radial CNC drill presses.
It’s important to maintain CNC drill bits sharp when using CNC drilling to make plastic components. Dull-shaped drills may put too much stress on the component, causing performance problems and tooling problems. We advise using a 90 to 118-degree drill bit with a 9 to 15-degree lip angle for most thermoplastics. Using a 0° rake is recommended for drilling acrylic.
The CNC drill’s chip ejection is extremely important since ineffective chip ejection can increase heat and friction. Heat reduction is essential to reducing stress and damage since CNC drilling produces more heat compared to any other CNC machining process.
Try to keep the drilling depth to no more than three or four times the drill diameter, and reduce the feed rate when the drill is almost out of the material, in order to properly remove a CNC drill without destroying the item.
Why Should You Use High-Precision CNC Machining Plastics Instead of Molding Plastics?
High tolerance, smaller quantity pieces are ideal for high accuracy, high precision CNC plastic machining. CNC machining removes the need for extremely expensive mold expenses. The price of alterations is likewise significantly lower.
High-accuracy CNC Compared to the molding process, lathe, and high-precision CNC milling machines may keep tighter tolerances. Moreover, high-precision CNC plastic part machining enables the addition of threads, undercuts, and other angles.
Why Not Use 3D Printing Instead of CNC Precision Plastic Machining for Units?
High-precision CNC machining is a subtractive process when compared to 3D additive printing. There is currently a small variety of plastic materials available for 3D printing.
The most widely used materials for 3D printing include wood, nylon, polymax PLA, ABS, and PLA. There are numerous materials that can be used for CNC precision plastic machining, including PTFE, polycarbonate, PEEK, acetal, PCTFE, acrylic, Nylon, Delrin®, etc.
Furthermore, compared to 3D printing’s 0.016-inch resolution, CNC milling, and CNC turning provide 15 times more accuracy at 0.001 inches. The process of 3D printing is quieter, cleaner, and uses fewer programming and operational resources.
This makes it a good option for low tolerance, low volume, and unusual prototyping. Particularly when material selection is crucial. However, CNC milling and CNC turning are the best solutions for high-precision, high-tolerance products.
Conclusion
CNC plastic machining is a commonly used industrial method because of its accuracy, speed, and versatility for manufacturing products with tight tolerances. This article discusses the many CNC machining materials that work with the process, the techniques that are accessible, and other elements that can benefit your project.
It might be very difficult to choose the best machining method; thus, you may need to hire a plastic CNC service provider. We at Want.Net provide best CNC machining services. We may help you in creating various prts for prototyping or real application.
Other Articles You Might Enjoy
- Aluminum CNC Machining Service for Custom Parts
Aluminum CNC machining stands at the forefront of modern manufacturing, epitomizing precision, versatility, and efficiency. With its widespread applications across industries ranging from aerospace to automotive and beyond, aluminum CNC…
- Unraveling the World of CNC Machined Plastic Parts(CNC machined plastic parts Mabel)
Modern innovations have taken traditional manufacturing methods to new heights. One such innovation that stands out is Computer Numerical Control (CNC) machining, a process used extensively in various industries from…
- CNC Machined Plastic Parts: An In-depth Overview(CNC machined plastic parts Norman)
Computer Numeric Control (CNC) machining is an advanced manufacturing process where pre-programmed software dictates the movement of factory machinery and tools. These applications can carry out complicated manufacturing tasks with…