The Importance of Shear Strain in CNC Machining
Understanding shear strain is essential not only for selecting the right materials but also for optimizing machining processes in CNC applications.but also for optimizing machining processes. Early in my career, I discovered that each material responds uniquely to stress, especially under shear forces, which are common in CNC applications. The concept of shear strain, which describes how materials deform under shear stress, plays a crucial role in determining how materials perform during cutting, shaping, and other CNC operations.
So, why does shear strain matter in CNC machining? At its core, shear strain helps us understand a material’s deformation behavior, allowing us to anticipate and control how it will respond during machining. This insight is invaluable for engineers, machinists, and designers who need to ensure that materials can handle the forces applied during CNC processes without compromising quality or precision. With shear strain data, I can adjust machining parameters like cutting speed, feed rate, and depth of cut to improve tool life, minimize deformation, and achieve high-quality finishes.
In this article, I’ll guide you through the essentials of shear strain, exploring how it impacts CNC machining parameters and material selection. We’ll delve into real-world applications across industries and cover practical strategies to optimize CNC processes based on shear strain data. By the end, I hope you’ll see why understanding shear strain is critical for achieving precise, efficient, and durable results in CNC machining.
Basic Concepts of Shear Strain
To understand the importance of shear strain in CNC machining, it’s essential to start with the basic concepts of stress, strain, and shear forces. Shear strain is a specific type of deformation that occurs when forces act parallel to a material’s surface, causing layers within the material to slide past each other. This type of deformation is critical in CNC machining because it directly impacts how materials behave during cutting, shaping, and finishing processes.
2.1 Introduction to Stress and Strain
Stress and strain are foundational concepts in material mechanics:
Stress (σ) is the force applied to a material per unit area. It’s measured in units such as Pascals (Pa) and is calculated using the formula:
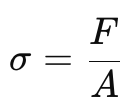
where ( F ) is the applied force, and ( A ) is the cross-sectional area.
Strain (ε) describes how much a material deforms relative to its original shape when stress is applied. Strain is dimensionless and is calculated as:
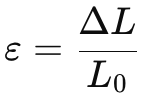
where ( /\L ) is the change in length, and ( L_0 ) is the original length.
2.2 Defining Shear Strain
Shear strain (( \gamma )) specifically measures the deformation caused by shear stress, which occurs when forces act parallel to a material’s surface. The formula for shear strain is:
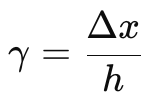
where:
- (/\ x ) is the horizontal displacement caused by the shear force,
- ( h ) is the original height or thickness of the material.
In CNC machining, understanding shear strain helps us determine how a material will respond to shear forces applied by cutting tools. Materials with high shear strain tolerance may deform more easily, allowing smoother shaping and cutting. Conversely, materials with low shear strain tolerance are more brittle, requiring careful control of machining parameters to prevent cracking or breakage.
2.3 The Relationship Between Shear Strain and Shear Modulus
The shear modulus (G) is a material property that describes its rigidity or resistance to shear deformation. It’s calculated by dividing the shear stress (T) by the shear strain (Y):
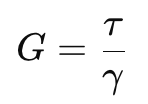
Materials with a high shear modulus are stiffer and resist deformation under shear stress, which is beneficial for parts that need to maintain their shape under heavy loads. In CNC machining, this information guides us in selecting materials that will hold up under the machining forces, enabling us to choose appropriate cutting tools and adjust parameters accordingly.
In my experience, knowing a material’s shear strain characteristics and shear modulus has been invaluable when working with challenging materials like titanium or high-strength alloys. This knowledge helps me adjust machining strategies to suit each material’s behavior, ensuring that parts meet quality standards while maintaining dimensional accuracy.
Effects of Shear Strain on CNC Machining Parameters
In CNC machining, shear strain has a direct impact on key parameters like cutting speed, feed rate, and depth of cut. By understanding how materials respond to shear forces, we can adjust these parameters to optimize machining quality, prevent excessive tool wear, and control deformation. Each of these parameters plays a unique role in how shear strain affects the machining process, so let’s look at them in more detail.
3.1 Cutting Speed
Cutting speed is the rate at which the cutting tool moves across the material’s surface. Shear strain influences cutting speed choices because higher speeds generally increase shear forces, potentially leading to excessive deformation or even material failure in brittle materials. Materials with high shear strain tolerance, such as aluminum, can withstand faster cutting speeds without deformation, whereas more brittle materials like certain ceramics may require lower speeds to prevent cracks and maintain surface quality.
In my experience, using lower cutting speeds for high-strength or low-shear-tolerance materials helps reduce stress and avoids damaging the workpiece. For materials that can handle higher shear strain, increasing cutting speed can improve efficiency without compromising accuracy.
3.2 Feed Rate
Feed rate is the rate at which the material is fed into the cutting tool. Higher feed rates increase the force per pass, which can cause higher shear strain in the material. By controlling the feed rate based on a material’s shear strain capacity, machinists can reduce the likelihood of deformation. For example, for softer materials with high shear strain capacity like plastic, a higher feed rate can be used without causing much deformation. However, for hard metals with low shear strain tolerance, lower feed rates are often necessary to avoid excessive wear and maintain precision.
Here’s a table that provides general recommendations based on shear strain tolerance:
Material | Shear Strain Tolerance | Recommended Cutting Speed | Recommended Feed Rate |
---|---|---|---|
Aluminum | High | High | Moderate to High |
Stainless Steel | Moderate | Moderate | Moderate |
Titanium | Low | Low | Low to Moderate |
POM (Delrin) | High | Moderate to High | High |
Carbon Fiber | Low | Low | Low |
Brass | Moderate | High | Moderate to High |
This table helps me decide on appropriate cutting speeds and feed rates, balancing efficiency with precision and minimizing risks like cracking or deformation.
3.3 Depth of Cut
The depth of cut is another critical parameter influenced by shear strain. A deeper cut generally means more material is being removed in a single pass, which increases the force exerted on the workpiece. Materials with low shear strain tolerance can fracture or warp under large depths of cut, so it’s important to keep this parameter conservative for those materials. For high shear strain tolerance materials, larger depths of cut can be used, which speeds up the machining process.
For instance, when machining titanium—a material with low shear strain tolerance—I typically keep the depth of cut shallow to avoid fractures. In contrast, when working with aluminum, which has a higher tolerance for shear strain, I can use deeper cuts to improve efficiency without risking material integrity.
Here’s a table summarizing recommended depths of cut for various materials based on their shear strain properties:
Material | Shear Strain Tolerance | Recommended Depth of Cut |
---|---|---|
Aluminum | High | Moderate to Deep |
Stainless Steel | Moderate | Moderate |
Titanium | Low | Shallow |
POM (Delrin) | High | Moderate to Deep |
Carbon Fiber | Low | Shallow |
Brass | Moderate | Moderate |
By carefully adjusting cutting speed, feed rate, and depth of cut based on shear strain, I can improve the efficiency of the machining process while ensuring that each part maintains its dimensional accuracy and quality.
Shear Strain Characteristics of Different Materials and Their Performance in CNC Machining
Different materials exhibit distinct behaviors under shear strain, which impacts their suitability and performance in CNC machining. Knowing each material’s shear strain characteristics allows us to optimize machining parameters and predict the quality and durability of the final product. Below, I’ll outline the shear strain characteristics of several commonly machined materials—steel, aluminum, titanium, and plastics—and discuss how they perform in CNC machining processes.
4.1 Steel
Steel is one of the most commonly used materials in CNC machining due to its high strength and versatility. Steel generally has moderate shear strain tolerance, with variations depending on its specific alloy composition. High-carbon steel, for example, is more brittle and has a lower tolerance for shear strain than stainless steel, which is more ductile.
In terms of machining, steel requires moderate cutting speeds and feed rates. Its moderate shear strain capacity means it can handle a reasonable depth of cut without significant deformation, making it suitable for structural and load-bearing parts.
Property | Value Range | CNC Machining Impact |
---|---|---|
Shear Modulus | 80-120 GPa | Moderate rigidity, allowing for accurate cuts |
Shear Strain Tolerance | Moderate | Balanced cutting speed and depth |
Recommended Applications | Gears, structural frames | Reliable for high-strength parts |
4.2 Aluminum
Aluminum’s high shear strain tolerance and low density make it ideal for lightweight parts. Its ductility allows it to withstand higher cutting speeds and feed rates without fracturing, and it’s resistant to warping during machining. Because of these properties, aluminum is often used in aerospace, automotive, and electronics industries.
For CNC machining, aluminum can handle deeper cuts and faster speeds than many other materials, enabling efficient production. It also tends to produce smoother surfaces due to its high ductility.
Property | Value Range | CNC Machining Impact |
---|---|---|
Shear Modulus | 25-30 GPa | Low modulus, suitable for fast machining |
Shear Strain Tolerance | High | High cutting speed, moderate to deep depth of cut |
Recommended Applications | Frames, casings, heat sinks | Lightweight parts, good for high-speed machining |
4.3 Titanium
Titanium is known for its high strength-to-weight ratio and excellent corrosion resistance, but it has a low tolerance for shear strain and can be prone to work hardening. Due to its low ductility, machining titanium requires lower cutting speeds, lower feed rates, and shallower depths of cut to prevent tool wear and material damage.
Titanium’s low shear strain tolerance makes it challenging to machine, but it’s essential in aerospace and medical applications where strength and durability are critical.
Property | Value Range | CNC Machining Impact |
---|---|---|
Shear Modulus | 40-45 GPa | Moderate rigidity, requires controlled machining |
Shear Strain Tolerance | Low | Low cutting speed, shallow depth of cut |
Recommended Applications | Medical implants, aerospace parts | Ideal for high-strength, corrosion-resistant parts |
4.4 POM (Delrin)
Polyoxymethylene (POM), commonly known as Delrin, is a thermoplastic with high shear strain tolerance. Its flexibility and smooth machinability make it suitable for applications where lightweight and moderate-strength components are required. Delrin is often used in precision parts, gears, and bushings, thanks to its high shear strain tolerance and resistance to warping.
In CNC machining, Delrin can withstand high cutting speeds and feed rates, allowing efficient processing without significant risk of deformation.
Property | Value Range | CNC Machining Impact |
---|---|---|
Shear Modulus | 1.2-1.6 GPa | Low rigidity, enables high feed rates |
Shear Strain Tolerance | High | High cutting speed, moderate to deep depth of cut |
Recommended Applications | Gears, bushings, precision components | Excellent for detailed plastic parts |
4.5 Brass
Brass is a metal alloy with moderate shear strain tolerance, known for its excellent machinability and smooth surface finish. It is commonly used in fittings, valves, and decorative components. Its moderate tolerance allows for faster cutting speeds and feed rates, making it efficient for producing parts that require intricate details.
Property | Value Range | CNC Machining Impact |
---|---|---|
Shear Modulus | 35-45 GPa | Moderate rigidity, smooth machining |
Shear Strain Tolerance | Moderate | High cutting speed, moderate depth of cut |
Recommended Applications | Valves, fittings, decorative parts | Ideal for intricate parts requiring high precision |
This table summarizes the shear strain characteristics and machining performance of these materials:
Material | Shear Modulus | Shear Strain Tolerance | Recommended Cutting Speed | Recommended Depth of Cut | Common Applications |
---|---|---|---|---|---|
Steel | 80-120 GPa | Moderate | Moderate | Moderate | Structural frames, gears |
Aluminum | 25-30 GPa | High | High | Moderate to Deep | Casings, heat sinks, lightweight parts |
Titanium | 40-45 GPa | Low | Low | Shallow | Aerospace, medical implants |
POM (Delrin) | 1.2-1.6 GPa | High | High | Moderate to Deep | Gears, bushings, precision components |
Brass | 35-45 GPa | Moderate | High | Moderate | Valves, decorative parts, fittings |
By understanding each material’s shear strain characteristics, CNC machinists can better match machining parameters to material properties, ensuring optimal performance and minimizing issues like deformation or tool wear.
Application of Shear Strain Analysis in Various CNC Machining Industries
Shear strain analysis has practical applications across several industries that rely on CNC machining. Each industry has unique material requirements, load conditions, and performance expectations, and understanding shear strain helps CNC machinists select appropriate materials and adjust machining parameters to meet these demands. Below, I’ll explore how industries like aerospace, automotive, medical equipment, and research utilize shear strain data in their CNC machining processes.
5.1 Aerospace Industry
In aerospace, materials must be lightweight yet able to withstand extreme stresses. Shear strain analysis is crucial in selecting materials for structural components like fuselage frames, landing gear, and turbine blades. Aerospace engineers often work with materials like titanium, aluminum alloys, and high-strength steels, all of which have distinct shear strain tolerances.
- Application Example: Turbine blades made of titanium require low cutting speeds and shallow cuts due to titanium’s low shear strain tolerance. By carefully controlling machining parameters, machinists ensure that these parts maintain high precision and strength without cracking or deforming under shear stress.
Component | Material | Shear Strain Tolerance | Recommended Machining Parameters |
---|---|---|---|
Fuselage Frame | Aluminum Alloy | High | High cutting speed, moderate depth of cut |
Turbine Blade | Titanium | Low | Low cutting speed, shallow depth of cut |
Landing Gear | High-Strength Steel | Moderate | Moderate speed, moderate depth of cut |
5.2 Automotive Industry
The automotive industry often demands materials that can handle frequent cyclic loading and impact without excessive wear. Shear strain analysis aids in determining if a material can sustain such conditions, particularly for engine components and structural parts. Engineers use materials like steel, aluminum, and brass for different automotive applications based on their shear strain behavior.
- Application Example: Engine blocks, often made from cast iron or aluminum, are subject to high internal stresses. By using shear strain data, CNC machinists can choose the right machining parameters to maintain the structural integrity of the block, ensuring durability under prolonged use.
Component | Material | Shear Strain Tolerance | Recommended Machining Parameters |
---|---|---|---|
Engine Block | Cast Iron | Moderate | Moderate speed, moderate depth of cut |
Transmission Gear | Steel | Moderate | Moderate speed, moderate depth for high precision |
Brake Calipers | Aluminum Alloy | High | High cutting speed, moderate depth for smooth finish |
5.3 Medical Equipment Industry
Medical equipment requires materials that are biocompatible and durable under repeated use. For components like surgical tools and implants, shear strain analysis helps engineers ensure that materials will not fracture or wear out under minor deformations. Common materials include titanium, stainless steel, and PEEK (a high-performance polymer).
- Application Example: Titanium implants require low machining speeds and controlled shear forces due to titanium’s low tolerance for shear strain. This precision ensures implants retain their shape and strength, crucial for patient safety and longevity of the implant.
Component | Material | Shear Strain Tolerance | Recommended Machining Parameters |
---|---|---|---|
Bone Plates | Titanium | Low | Low speed, shallow depth to prevent cracking |
Surgical Tools | Stainless Steel | Moderate | Moderate speed, moderate depth for tool longevity |
Spinal Cages | PEEK | High | High speed, moderate depth for detailed precision |
5.4 Research and Education
In educational and research environments, shear strain analysis is often used to understand material behavior under various machining conditions. Researchers experiment with different materials, machining techniques, and parameters to study how shear strain affects performance, especially for advanced or experimental materials.
- Application Example: Researchers testing new metal alloys can use shear strain analysis to determine if the material can withstand CNC machining processes without significant wear or deformation. By adjusting parameters according to shear strain, they can optimize machining for the unique properties of each alloy.
Research Area | Material Tested | Shear Strain Tolerance | Machining Focus |
---|---|---|---|
New Alloys | Experimental Metals | Varies | Conservative speed, shallow cut for initial testing |
Polymer Research | High-Performance Polymers | High | Moderate to high speed, moderate depth for precision |
Tool Wear Analysis | Steel, Titanium | Moderate to Low | Variable speeds to study tool life under shear stress |
These industry applications demonstrate how shear strain data guides material selection, machining parameter choices, and quality control in CNC processes. By leveraging shear strain analysis, CNC machinists and engineers can make informed decisions to meet specific requirements and achieve precise results.
Strategies for Optimizing CNC Machining Parameters Based on Shear Strain
Shear strain data plays an invaluable role in fine-tuning CNC machining parameters, particularly for materials with varying tolerances to shear stress. Adjusting cutting speed, feed rate, and depth of cut based on shear strain properties allows for efficient machining while maintaining part quality and minimizing tool wear. Here, I’ll share strategies I use to optimize CNC machining processes by leveraging shear strain data.
6.1 Adjusting Cutting Speed Based on Shear Strain Tolerance
Cutting speed influences the rate of material removal and heat generation, both of which impact how shear strain develops in the workpiece. Materials with high shear strain tolerance, like aluminum, can handle higher speeds without excessive deformation. Conversely, materials like titanium, which have low shear strain tolerance, require slower speeds to maintain structural integrity.
For example, I find that reducing the cutting speed by even 10-15% for brittle materials helps prevent cracking and tool wear. In contrast, increasing cutting speed for ductile materials enhances productivity without sacrificing quality.
Material | Shear Strain Tolerance | Recommended Cutting Speed Adjustment |
---|---|---|
Aluminum | High | Increase by 10-20% for faster processing |
Titanium | Low | Reduce by 10-15% to prevent cracking |
Stainless Steel | Moderate | Maintain moderate speeds for balance |
6.2 Optimizing Feed Rate to Control Shear Force
Feed rate, or the speed at which the workpiece moves towards the tool, affects the force applied on the material per cut. A higher feed rate increases shear force, which is beneficial for materials with high shear strain tolerance, as it can improve efficiency. For more brittle materials, a lower feed rate reduces the risk of deformation and maintains precision.
From my experience, reducing the feed rate for materials like brass and titanium allows for a smoother, more controlled cut. This is particularly useful when machining parts with intricate details or tight tolerances.
Material | Shear Strain Tolerance | Recommended Feed Rate Adjustment |
---|---|---|
Brass | Moderate | Lower feed rate for detailed, precision cuts |
Aluminum | High | Increase feed rate to improve efficiency |
Carbon Fiber | Low | Lower feed rate to avoid excessive stress |
6.3 Controlling Depth of Cut to Minimize Shear-Induced Deformation
Depth of cut is a critical factor when machining materials sensitive to shear strain. A deeper cut can increase the strain and risk of cracking in materials with low shear strain tolerance. For high-tolerance materials, deeper cuts are feasible and can speed up machining.
For instance, I often start with shallow cuts on materials like titanium and gradually increase depth if the material’s response allows. This approach prevents sudden stresses and maintains accuracy, especially for critical components.
Material | Shear Strain Tolerance | Recommended Depth of Cut Adjustment |
---|---|---|
Steel | Moderate | Moderate depth of cut for strength applications |
Titanium | Low | Shallow cut to reduce risk of cracking |
POM (Delrin) | High | Moderate to deep cut to maximize productivity |
6.4 Using Shear Strain Data to Extend Tool Life
Tool wear is a significant consideration in CNC machining, particularly for hard materials with low shear strain tolerance. Shear strain data helps me choose cutting tools and adjust parameters to minimize wear. For example, when machining hard metals, I select carbide or diamond-coated tools that can handle the strain without excessive wear. Adjusting parameters based on shear strain also reduces friction, heat, and stress on the tool, prolonging its lifespan.
Material | Shear Strain Tolerance | Tool Material Recommendation | Suggested Adjustment for Tool Longevity |
---|---|---|---|
Stainless Steel | Moderate | Carbide or high-speed steel | Moderate speed and feed rate |
Titanium | Low | Diamond-coated or carbide | Low speed, shallow cut |
Aluminum | High | High-speed steel | Higher speeds, moderate to deep cuts |
By optimizing machining parameters based on shear strain tolerance, I can achieve a balance between efficiency, quality, and tool wear, ensuring that each job is completed to high standards while minimizing resource costs.
Choosing Suitable Materials and Tools Based on Shear Strain
Selecting the right materials and tools is crucial for achieving optimal results in CNC machining, particularly when shear strain characteristics vary widely among materials. By understanding the shear strain tolerance of a material, I can make informed choices about the tool type, tool material, and cutting parameters needed to ensure precise and efficient machining.
7.1 Material Selection Based on Shear Strain Characteristics
Materials with high shear strain tolerance, such as aluminum and POM, allow for greater flexibility in machining, including faster cutting speeds and deeper cuts. For brittle materials or those with low shear strain tolerance, such as titanium and carbon fiber, it’s essential to choose materials that can withstand the required machining forces without excessive deformation.
When choosing materials for CNC projects, I consider not only the end-use requirements of the part but also the machinability, which shear strain data greatly influences. Here’s a table summarizing suitable applications based on shear strain tolerance:
Material | Shear Strain Tolerance | Recommended Applications |
---|---|---|
Aluminum | High | Aerospace parts, automotive components |
Titanium | Low | Medical implants, aerospace structural components |
Brass | Moderate | Valves, fittings, decorative parts |
POM (Delrin) | High | Precision plastic parts, gears, bushings |
Carbon Fiber | Low | Lightweight structural components, sporting goods |
7.2 Tool Material and Geometry Selection
The type and material of the cutting tool play a vital role in how effectively a material can be machined under specific shear strain conditions. For materials with low shear strain tolerance, selecting harder tool materials—such as carbide or diamond-coated tools—helps withstand the higher resistance these materials present. Conversely, for softer or high-tolerance materials, high-speed steel or coated tools are often sufficient.
Tool geometry also impacts the effectiveness of machining based on shear strain. For example, tools with a larger rake angle reduce cutting forces and are suitable for high-shear-strain materials, while smaller angles provide better support for brittle materials.
Material | Shear Strain Tolerance | Recommended Tool Material | Recommended Tool Geometry |
---|---|---|---|
Aluminum | High | High-speed steel | Large rake angle, positive cutting angle |
Titanium | Low | Carbide or diamond-coated | Small rake angle, low cutting angle |
Stainless Steel | Moderate | Carbide | Moderate rake angle |
POM (Delrin) | High | High-speed steel or coated | Large rake angle, positive cutting angle |
Carbon Fiber | Low | Diamond-coated | Small rake angle, low cutting angle |
7.3 Matching Tools and Materials to Control Shear Strain-Induced Deformation
When working with materials that have low shear strain tolerance, I use specialized tooling strategies to prevent excessive deformation and maintain part accuracy. For instance, using tools with coatings that reduce friction helps limit heat generation, which is beneficial for materials like titanium that are prone to thermal deformation.
Here’s a table illustrating recommended tool and material pairings based on shear strain to reduce deformation:
Material | Tool Type | Tool Coating | Recommended Usage |
---|---|---|---|
Aluminum | High-speed steel | TiN-coated | High-speed cuts, moderate depth |
Titanium | Carbide or diamond-coated | Diamond | Slow, shallow cuts to avoid heat buildup |
Stainless Steel | Carbide | Uncoated or TiN-coated | Moderate cuts with emphasis on durability |
POM (Delrin) | High-speed steel | None needed | High-speed cuts with positive cutting angles |
Carbon Fiber | Diamond-coated | Diamond | Low-speed, shallow cuts to maintain structural integrity |
Matching the right tool material and geometry with a material’s shear strain properties enhances the machining process by reducing risks of deformation, improving surface quality, and extending tool life.
FAQ
Shear strain plays a significant role in CNC machining, influencing everything from material selection to parameter optimization. Here are some frequently asked questions about applying shear strain knowledge in CNC processes, with insights to help machinists, engineers, and designers make the most of this information.
Q1: How does knowing a material’s shear strain tolerance affect CNC machining?
Understanding a material’s shear strain tolerance helps you choose the right machining parameters, such as cutting speed, feed rate, and depth of cut. This allows for efficient machining without causing unwanted deformation or compromising material integrity. Materials with high shear strain tolerance can handle more aggressive machining, while low-tolerance materials require controlled, precise parameters.
Q2: Can shear strain data help reduce tool wear?
Yes, shear strain data helps in selecting optimal machining conditions that reduce tool wear. By adjusting parameters like feed rate and cutting depth based on the material’s shear strain tolerance, you can minimize stress on the cutting tool, extend its life, and reduce the need for frequent replacements. For instance, reducing cutting speed when working with hard, brittle materials helps decrease wear.
Q3: How do I determine if a material’s shear strain properties are suitable for a specific CNC machining project?
Assess the end-use requirements of the part—if the part needs to be strong and resist high loads, choose materials with lower shear strain tolerance and high rigidity. For parts that require flexibility or need to handle large deformations, materials with high shear strain tolerance are preferable. Referencing material data sheets or testing shear strain behavior in advance is a good practice.
Q4: How does shear strain affect surface finish in CNC machining?
Materials with low shear strain tolerance, such as brittle metals, may produce a rougher finish if machined with high-speed or deep cuts due to potential cracking or chipping. Controlling shear strain through moderate machining parameters often results in a smoother surface finish, especially for materials sensitive to stress. For smoother finishes, reduce cutting forces by using slower speeds and shallower cuts.
Q5: What challenges arise when machining high-shear-strain materials like aluminum?
High-shear-strain materials, such as aluminum, can handle higher speeds and feed rates, but they are also prone to heat buildup, which may lead to warping or tool coating breakdown. Proper cooling and chip removal are essential to maintain surface integrity. Using coated tools can help manage friction, and chip removal systems keep the workspace clean and prevent tool binding.
Q6: How do I control shear strain-induced deformation in thin-walled parts?
For thin-walled parts, even small levels of shear strain can lead to deformation. To mitigate this, use lower cutting speeds, shallow depths of cut, and conservative feed rates. Stabilizing fixtures can also help reduce vibrations, preventing thin-walled parts from flexing under machining forces.
Q7: What role does tool geometry play in controlling shear strain?
Tool geometry, such as rake and clearance angles, significantly affects shear strain. A larger rake angle reduces cutting forces, which is beneficial for high-shear-strain materials. However, for brittle or low-shear-strain materials, a smaller rake angle provides better support, reducing the risk of chipping or cracking.
Q8: How does temperature affect shear strain in CNC machining?
Higher temperatures can alter shear strain behavior by increasing a material’s ductility, which might be beneficial for machining brittle materials. However, excessive heat can also lead to thermal deformation, particularly in low-shear-strain materials. Managing heat through cooling systems and controlled cutting speeds is essential to maintaining material properties.
Q9: How does shear strain analysis benefit high-precision CNC applications?
For high-precision applications, shear strain analysis allows for exact parameter adjustments to avoid unwanted deformation, ensuring tight tolerances. Materials with low shear strain tolerance are ideal for high-precision parts, as they maintain shape under stress. Adjustments based on shear strain help achieve accurate dimensions and improve overall quality.
Q10: What are some common issues encountered when machining low-shear-strain materials like titanium?
Low-shear-strain materials like titanium are prone to cracking and tool wear if machined with aggressive parameters. To minimize these issues, use carbide or diamond-coated tools, low cutting speeds, shallow cuts, and moderate feed rates. This approach preserves tool life and prevents material damage.
Other Articles You Might Enjoy
- Precision CNC Machining of Steel: High-Volume Production
Precision CNC Machining and High-Volume Production As an integral part of modern manufacturing processes, Precision Computer Numerical Control (CNC) machining brings about unmatched accuracy and consistency in the production of…
- Optimizing CNC Machining with Hybrid Materials: Benefits and Challenges
Introduction: CNC Machining and the Role of Hybrid Materials CNC machining, short for Computer Numerical Control machining, is a manufacturing process where pre-programmed computer software dictates the movement of factory…
- What should be noted about materials when machining parts with CNC?
When machining parts with CNC, not all materials can be precisely processed. Some materials are too hard and may damage the CNC machining tools, making them unsuitable for precision machining…
- Material Versatility in CNC Machining: From Titanium to Thermoplastics
Introduction to CNC Machining CNC machining stands as a cornerstone in the manufacturing sector, enabling the precise creation of parts and components. This process utilizes computer numerical control (CNC) to…
- Eco-Friendly CNC Machining: Sustainable Materials and Practices
Eco-Friendly CNC Machining: An Introduction CNC (Computer Numerical Control) machining is a manufacturing process that commands the movement of factory machinery and tools using pre-programmed computer software, ensuring precise design…
- Precision CNC Machining for High-Performance Industrial Machinery
Precision CNC Machining for High-Performance Industrial Machinery The process of Precision CNC (Computer Numerical Control) machining is at the core of manufacturing high-performance industrial machinery. This technique leverages a computer's…